Capital Carbon Expands rCB Capacity To Tackle Supply Chain Issues
- By Gaurav Nandi
- January 14, 2025
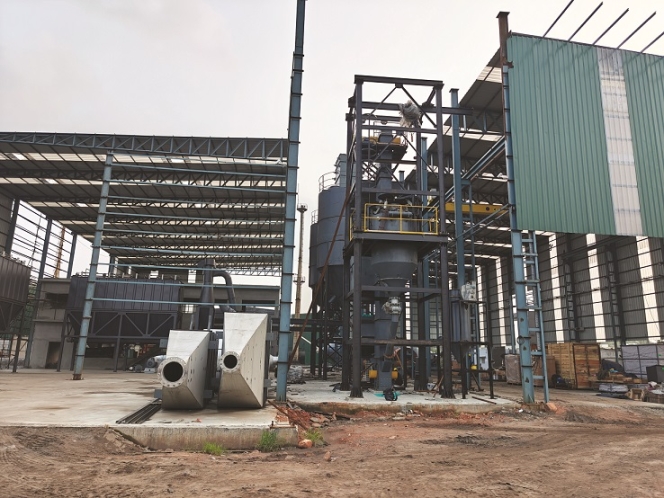
The Tamil Nadu-based company’s greenfield expansion will propel its rCB capacity from 5,000-20,000 metric tonnes. Director Ravi Rathi explained that there has been a change in attitude towards rCB within tyre companies, leading to heightened demand.
Tamil Nadu-based Capital Carbon is expanding its recovered carbon black (rCB) capacity by 15,000 metric tonnes with a new greenfield project at Gummidipoondi. The plant is slated to become operational by January 2025 and boost the capacity from 5,000 metric tonnes to 20,000 metric tonnes, annually.
Speaking to Tyre Trends, Director Ravi Rathi explained, “The decision to pursue a greenfield expansion in the rCB sector stemmed from the rapid development of this innovative product over the past four to five years. Given our background in the pyrolysis business, expanding into rCB felt like a natural progression. rCB is still a relatively new product and both manufacturers and users are in the process of learning about its applications. When we first began exploring this market, around four years ago, it was challenging. Many tyre manufacturers would dismiss our proposals even before we could present our case as they were hesitant to incorporate recycled materials into their mainstream formulations.”
“However, in recent years, attitudes have shifted significantly due to increasing emphasis on sustainability and circular economy principles. The industry is now more open to integrating green products. We started with a modest capacity of 5,000 metric tonnes per annum, which allowed us to gain insights into customer needs. Gradually, we scaled our operations from small quantities to commercial sales. The key driver for our recent expansion is customer demand. We have obtained product approval, and customers are eager to purchase rCB,” he added.
He also noted that companies wanted assurance that the demands could be met consistently, which was also a factor behind the expansion. Furthermore, having multiple units also allows the company to manage any potential supply chain issues, effectively. “If a minor problem arises in one unit, we can still supply material from another, minimising disruptions for our customers,” said Rathi.
The entire CAPEX for the greenfield plant is set at INR 20 crore.
Pyrolysis to rCB
Capital Carbon commenced operations in 2012 with a modest pyrolysis capacity of 10 tonnes per day. Over the years, it has consistently expanded its capacity, increasing to 150 metric tonnes per day. The company has also bolstered its backend operations, enhancing sourcing capabilities and adding substantial shredding and crumbing capacity.
Additionally, Capital Carbon has focused on value-added products including pyrolysis oil distillation and rCB. As of now, it operates a shredding capacity of 120,000 metric tonnes per annum for captive consumption. This capacity is supplemented by sourcing contaminated tyre bales, which typically have 20-30 percent rubber contamination. This material is cleaned to yield 98 percent pure steel, with the remaining rubber used for pyrolysis, creating a separate business vertical.
Currently, the company processes approximately 50,000 to 52,000 metric tonnes of tyres per annum through its pyrolysis operations. In terms of value addition, Capital Carbon produces between 20,000 to 24,000 tonnes of pyrolysis oil, annually.
When asked about the motivation behind establishing a pyrolysis plant, Rathi noted, “My father worked at Birla Carbon and retired in 2019. Although we lacked prior business experience, we were inspired by the industrial upbringing and the promising potential of the pyrolysis sector. Following the completion of my chartered accountancy studies, I decided to pursue this opportunity.”
He acknowledged that pyrolysis often has a negative reputation in India, where it is sometimes viewed as a ‘dirty business’. To combat this perception, Capital Carbon prioritises quality management and environmental responsibility in its operations. IT employs fuel-based heating methods in its pyrolysis process as electric heating is generally not feasible due to the high volumes involved in tyre pyrolysis. The initial heating requires some fuel, which can include biomass or pyrolysis oil, but the system becomes self-sufficient once it reaches a certain temperature.
The primary outputs from the pyrolysis process include fuel oil, carbon char (used as raw material for rCB or as an alternative energy source for cement plants), steel wires and pyrolysis gases, which are utilised for heating purposes.
He highlighted that the pyrolysis oil produced is of high quality with low sulfur and carbon content, making it cleaner than many conventional heating fuels used in India.
Quality control
The company’s sourcing strategy primarily focuses on domestic suppliers. It procures rejected tyres and dealer returns from various companies, which constitute a substantial portion of the feedstock. This local sourcing approach ensures that it maintains a steady supply of raw materials
Following sourcing, the production of recovered carbon black involves several critical steps. Initially, tyres are shredded to extract carbon black, steel and other components. The distinction in product application necessitates tailored processing methods.
For instance, producing carbon char for energy requires less stringent technical specifications compared to producing carbon black intended for high-performance applications, such as tyre manufacturing or footwear.
“The quality of the final product begins with meticulous sorting of tyres to determine suitability for pyrolysis. This initial step is vital for ensuring consistent output quality. Following sorting, the tyres are shredded into steel-free rubber chips of 15-20 millimetres. During pyrolysis, we focus on maintaining specific quality parameters for the pyrochar produced. This includes stringent controls to limit ash content, which must remain below 20-22 percent to ensure product consistency. The handling of impurities such as wires and stones in the pyrochar is essential. Post-processing, the pyrochar is milled to fine particle sizes (10-15 microns), enhancing its surface area for better compatibility with rubber compounds,” explained Rathi.
Once the recovered carbon black is processed, palletisation becomes the next step. This method streamlines handling and ensures that the product meets industry standards. While the equipment resembles that used for traditional carbon black, adaptations are necessary to accommodate the unique characteristics of recovered carbon black.
“To facilitate customer adoption, we offer tailored packaging solutions including 25kg paper bags, EVA / LDPE bags and FIBC bags, allowing clients to integrate our products seamlessly into their existing production processes,” he added.
As the industry evolves, the need for standardised quality benchmarks for recovered carbon black has become increasingly clear. Major corporations have driven this change, leading ASTM to establish a dedicated committee (D36) focused on developing specific standards for recovered carbon black. Unlike conventional carbon black, which adheres to existing standards, recovered carbon black requires new metrics to account for its varied origins and compositions.
The committee is currently validating a series of standards including moisture content, pallet hardness and particle size analysis, specifically for rCB. This ongoing development is slated to enhance product credibility and facilitate broader market acceptance.
Commenting on the same lines, Rathi mentioned, “We maintain a dedicated quality lab to refine our production processes continually. Our focus on evolving our offerings has resulted in the introduction of two new grades of recovered carbon black, aimed at meeting diverse market needs. Our commitment to leveraging advanced machinery and improved grinding techniques reflects our proactive approach to quality enhancement and capacity expansion.”
Optimistic market outlook
The demand for recovered carbon black in India is poised for significant growth, driven by a strong shift toward sustainability. Customers are increasingly seeking high-quality suppliers, indicating a burgeoning market for rCB.
“Globally, rCB production currently accounts for less than one percent of total carbon black production, underscoring a substantial opportunity for expansion. As customer awareness and demand for sustainable products increase, we anticipate a corresponding rise in rCB consumption,” informed Rathi.
He added, “Many major corporations have committed to achieving carbon neutrality by 2050, necessitating immediate action to integrate green and circular products into their supply chains. As these companies strive to meet their net-zero targets, they are turning to recovered materials such as rCB to fulfil sustainability mandates. Our role is crucial in assisting these customers to achieve their goals through the production of eco-friendly and circular products derived from end-of-life tyres.”
Speaking on market opportunities, he said, “India remains our largest market, but we are also making significant inroads into Sri Lanka. The European market is particularly promising, though it presents challenges related to certifications and distribution. We are currently working on obtaining the necessary certifications, including ISCC Plus, to unlock this market potential.”
“Our immediate focus is on completing our current expansion project, after which we will enhance our pyrolysis capacity to align with the growing demand from our customers. As the volumes of recovered carbon black usage increase, we aim to be ready with sufficient supply,” he added.
He expects to penetrate the European market by the first half of FY26, following the completion of the current plant expansion.
Challenges in scaling production
“One of the primary challenges in scaling rCB production is the scarcity of raw materials. The supply of suitable feedstock is diverse and scattered, making it difficult to source consistently. In the past, customers struggled to understand the differences between recovered carbon black and virgin carbon black grades, often asking if we could produce specific grades like L550 or L660. However, as knowledge in the market has matured, customers are increasingly recognising that rCB is a distinct material requiring tailored processing approaches,” informed Rathi.
- Kuraray
- Kuraray Asia Pacific
- Kuraray Asia Pacific Centre
- Activated Carbon
- Singapore Economic Development Board
Kuraray Opens Asian Technical Support Hub
- By TT News
- September 06, 2025
Kuraray Asia Pacific Pte. Ltd., a subsidiary of Kuraray Co., Ltd., has inaugurated the Kuraray Asia Pacific Centre in Singapore's Science Park. This new facility will function as a dedicated technical support hub for the Asian market. Its primary focus will be on providing specialised expertise for growing regional demand in PVOH resin, EVAL EVOH resin and activated carbon products.
Equipped with advanced material evaluation and analysis laboratories, the centre is designed to deliver prompt and tailored solutions to meet specific local customer requirements. It will also act as a platform for open innovation, fostering collaborative development and product demonstrations to generate new value.
By establishing itself within the concentrated research environment of the Singapore Science Park, the centre aims to accelerate market development and attract global talent through strategic partnerships. This initiative is a key part of the Kuraray Group's strategy to address emerging customer needs, explore new applications and strengthen its overall business expansion throughout the region.
Lim Wey-Len, Executive Vice President, Singapore Economic Development Board, said during the opening ceremony on 1 September: “We welcome Kuraray and other like-minded companies to leverage Singapore’s innovation ecosystem, talent pool, and regional connectivity to scale impactful and sustainable solutions from here.”
Tomoyuki Watanabe, Director and Managing Executive Officer, and President of the Vinyl Acetate Resin Company at Kuraray, said, “By offering a place for co-creation with our customers, we hope to drive the rapid market growth in the region.”
- Association of Natural Rubber Producing Countries
- ANRPC
- Monthly NR Statistical Report
- Natural Rubber
ANRPC Publishes Monthly NR Statistical Report For July 2025
- By TT News
- September 05, 2025
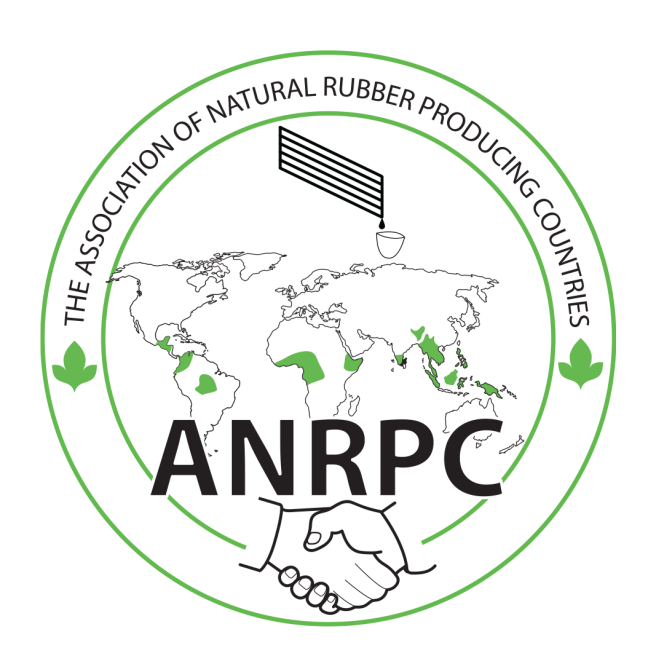
The Association of Natural Rubber Producing Countries (ANRPC) has released its Monthly NR Statistical Report for July 2025, providing an overview of key developments in the global natural rubber sector.
According to the report, natural rubber prices exhibited significant volatility in July. This instability was driven by a combination of adverse weather conditions impacting production, ongoing geopolitical tensions and international trade tariffs. After an initial phase of ample supply and muted demand, market sentiment shifted as concerns over potential supply disruptions prompted a notable increase in purchasing activity.
The report further projects a modest global production increase of 0.5 percent for 2025, while demand is anticipated to grow by a slightly higher 1.3 percent. However, this growth is expected against a challenging backdrop of a potential global economic slowdown. Complex US tariff policies and their widespread ripple effects are primary factors contributing to what may become one of the most subdued years for economic expansion since the pandemic.
Continental Pioneers Industrial-Scale Rubber Recycling With Advanced Pyrolysis
- By TT News
- September 03, 2025
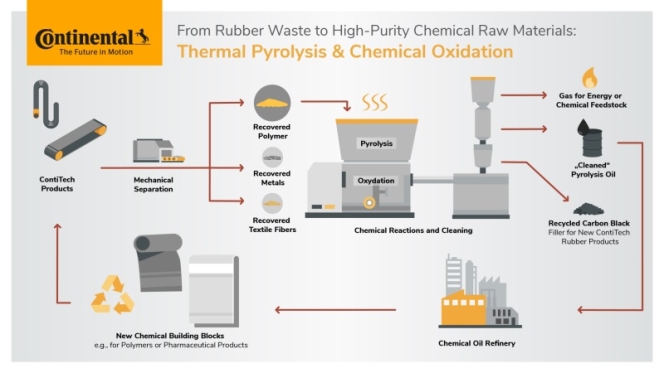
Continental is establishing a groundbreaking industrial process for recycling complex rubber waste through a strategic acquisition of key patents and the launch of a new pilot facility. This initiative, led by its ContiTech division, leverages advanced pyrolysis technology to transform end-of-life rubber products into valuable raw materials, creating a sustainable alternative to fossil resources.
The core of this innovation is a thermal decomposition process where waste rubber is heated in a low-oxygen environment. This breaks the material down into its core chemical constituents, one of which is a high-quality oil with properties mirroring traditional crude oil. This output is particularly significant as it can be directly used in the manufacture of new plastics and rubber goods, effectively closing the material loop.
A major historical obstacle for the industry has been the difficulty of recycling vulcanised rubber, whose altered chemical structure resists conventional separation methods. Pyrolysis successfully circumvents this challenge, cleanly decomposing the material to recover not only oil but also carbon black and other energy sources. The widespread adoption of pyrolysis has been hindered until now by the complexity of purifying its outputs to meet industrial standards. Continental’s new facility, originally developed by British start-up LowSulphurFuels, directly addresses this hurdle with a specialised purification process, making large-scale rubber recycling both technically feasible and economically attractive.
This advancement is especially critical for complex rubber products like composite hoses and specialised seals, which were previously nearly impossible to recycle efficiently. By converting this challenging waste stream into a high-grade resource, Continental is driving progress towards a circular economy. This move also reinforces the company's position as a leader in sustainable innovation, complementing its extensive patent portfolio and ongoing projects focused on material recovery and developing eco-friendly solutions for the automotive and industrial sectors.
Dr Michael Hofmann, Chief Technology Officer, ContiTech, said, “With this technology, we’re closing a crucial gap in the circular materials economy: we’re able to recover high-quality raw materials from rubber waste, which we can then feed back into the chemical material cycle to create new products without relying on crude oil. We’re thus demonstrating how innovation can become the driving force behind sustainable industrial processes – and how a previously untapped raw material cycle can be made economically viable.”
Zeon Board Approves Higher Budget For Cyclo Olefin Polymer Facility
- By TT News
- September 03, 2025
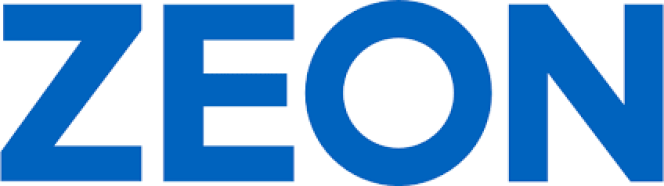
Following a resolution by its Board of Directors on 29 August 2025, Zeon Corporation has formally revised the total investment for its upcoming cyclo olefin polymer (COP) production plant. The new total investment is now projected to be approximately JPY 78.0 billion (approximately USD 525.70 million), a significant increase from the initial estimate of approximately YEN 70.0 billion (approximately USD 471.77 million) announced in June 2024.
This upward revision is attributed to anticipated increases across key construction areas, including rising costs for labour, raw materials and equipment. The updated financial framework incorporates both confirmed and projected cost escalations to ensure accurate budgeting. Zeon Corporation intends to fund the entire investment through a combination of internally generated capital and loans from financial institutions.
The new facility remains on schedule for completion in the first half of fiscal year 2028. Due to this timeline, the substantial investment is not expected to materially affect the company's consolidated financial results for the fiscal year ending 31 March 2026. The project is a central pillar of the company’s medium-term business strategy, identified as a major future growth driver.
The decision to proceed with the plant underscores the strong market outlook for Zeon’s cyclo olefin polymers. These advanced materials are prized for their superior optical clarity, extremely low water absorption and high purity. While already established in applications like optical films and lenses, demand is growing rapidly from the medical and semiconductor industries. By expanding its production capacity, Zeon aims to capitalise on this robust and expanding demand, thereby strengthening its market position and enhancing its corporate value over the medium to long term.
Comments (0)
ADD COMMENT