- CEAT
- 4IR
- Fourth Industrial Revolution
- Digital transformation
- Automation
- AI
- IoT
- Smart Factory
- Manufacturing Execution System
- Predictive Maintenance
- Sustainability
CEAT Cuts Operational Costs By 30% With 4IR, Set To Expand To Nagpur Plant
- By Sharad Matade & Gaurav Nandi
- March 01, 2025
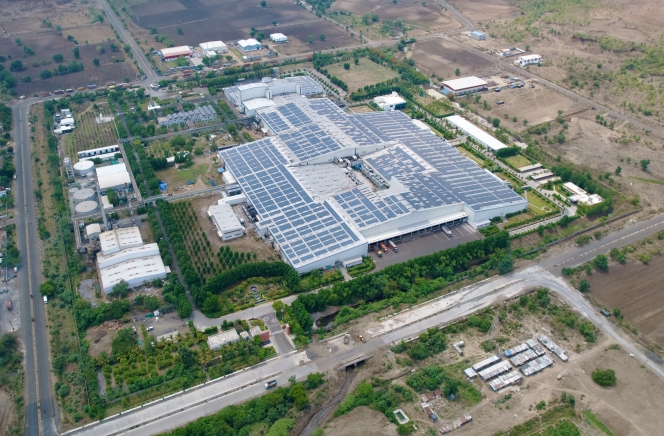
Like many other sectors, India’s tyre industry is undergoing a massive digital transformation. Companies like CEAT have been at the forefront of this shift, adopting state-of-the-art technology.
The company was recently included in the World Economic Forum’s Global Lighthouse Network due to its impactful digital transformation using Fourth Industrial Revolution (4IR) technology.
The leading tyre manufacturer has also planned to extend its technological advancements to its Nagpur plant. “CEAT’s vision for a smart factory dates back to 2015, when it commissioned its Nagpur plant. The groundwork, however, was laid earlier at Halol, where barcode tagging was introduced for traceability and error-proofing. While Nagpur became the first facility to implement a manufacturing execution system (MES), deeper analytics and machine learning capabilities were not yet in focus between 2015 and 2020,” revealed Jayasankar Kuruppal, Sr Vice President –Manufacturing, during an exclusive interview with Tyre Trends.
As Halol expanded and exports to Europe surged by the early 2020s, CEAT had to rethink its manufacturing strategy, shifting from a high-volume, low-variant model to a high-variant, low-volume approach. Once limited to 60-70 stock-keeping units (SKUs), the company's passenger car segment expanded nearly fivefold to meet European demand, requiring a complete overhaul of production workflows.
At the same time, the adoption of silica-based compounds, which is critical for wet grip and rolling resistance, posed new challenges. These materials inherently increased cycle times, impacting capacity utilisation. While Halol was not initially designed for high-silica production, the company’s Chennai plant incorporated necessary corrections. However, tighter OEM specifications and European market requirements led to higher scrap and yield losses.
Recognising the limitations of conventional manufacturing, CEAT turned to 4IR technology to optimise its processes. The 4IR technology refers to the advanced digital and automation-driven technologies transforming industries today. It builds on the Third Industrial Revolution by integrating AI, IoT, big data and robotics to enhance efficiency and decision-making.
“The digital transformation began at the Halol plant, expanded to Chennai and is now planned for Nagpur. Between 2020 and 2022, CEAT developed and deployed over 80 digital use cases, earning its first Lighthouse Factory designation. This data-driven manufacturing approach is now being systematically rolled out across its entire production network,” added Kuruppal.
Intelligent factories
4IR plays a crucial role in tyre manufacturing and recycling by enhancing predictive maintenance through IoT sensors, increasing energy efficiency via AI, production optimisations and advancing smart tyres with real-time monitoring.
On the other hand, an intelligent or smart factory in tyre manufacturing is defined by two core pillars, namely automation and digital intelligence. Traditionally, the tyre industry has been labour-intensive, but the shift towards smart factories is transforming operations through seamless machine-to-machine communication, real-time data sharing and AI-driven decision-making.
The first layer of an intelligent factory is pure automation. This includes automated machines for tyre handling, programmable logic controllers for managing machine operations and automated warehousing systems to ensure smooth flow.
“For a plant to be truly smart, data must move seamlessly across all these systems, creating a connected ecosystem. This integration extends to ERP systems and advanced AI/ML-powered analytics, optimising throughput and efficiency,” said Kuruppal.
The next stage is where operations run end-to-end with minimal human intervention. CEAT has already implemented elements of this, particularly through curing-to-dispatch automation, where tyres move untouched from uniformity testing to segregation, grading, storage, retrieval and final dispatch. It also has AI-driven IoT integrations that enhance energy efficiency, yield optimisation and first-time-right accuracy across all processes.
“The fusion of AI, IoT and automation is enabling tyre manufacturers to move from traditional manual-heavy processes to a digitally orchestrated, high-efficiency production model,” quipped Kuruppal.
CEAT’s production capacity spans multiple plants, each specialising in different tyre categories. The Chennai and Halol plants both produce 20,000 passenger car tyres daily. The Nagpur plant, India’s largest two-wheeler tyre manufacturing facility under one roof, with a capacity of close to 78,000 two-wheeler tyres daily.
Digital implementation
Curing operations in CEAT’s passenger car and truck tyre segments are almost entirely automated. While the curing medium remains unchanged, continuing with a combination of steam and nitrogen across Halol, Chennai and other facilities, the company is also exploring radical new processes, though still in the proof-of-concept stage.
One key digital use case implemented in Chennai focused on reducing steam consumption through real-time process monitoring. Traditionally, mould heating followed fixed time cycles (e.g. 120 or 150 minutes). CEAT optimised heating based on actual temperature data, cutting steam consumption by almost 30 percent by integrating sensors and applying a machine-learning model.
The manufacturer has invested approximately INR 450-500 million in capital expenditure across its three factories to implement automation and digital transformation initiatives. On the operational expenditure side, CEAT spends INR 60-70 million annually on software licenses, infrastructure upgrades, sensors and scanners to sustain these smart factory systems.
Adopting smart manufacturing technologies has led to significant cost reductions for CEAT. Factory conversion costs at Chennai and Halol have decreased by 20-30 percent, driven by lower energy consumption, improved yield, higher manpower productivity and throughput enhancements.
Lead times from order placement to tyre dispatch have been cut by 50-55 percent, significantly improving supply chain efficiency. Additionally, material wastage has been reduced with process scrap, both component-level and finished product waste, dropping by 25-30 percent, resulting in substantial raw material savings.
Alluding to how difficult was it to implement such extensive digital changes, the executive explained, “From an infrastructure standpoint, Chennai had a clear advantage over Halol since the latter was commissioned in 2010 and 2015, when network and digital infrastructure were not as advanced. Unlike Chennai, Halol still does not have a fully integrated MES, making digital transformation more complex.”
“However, the approach to smart manufacturing differed at both plants. At Halol, the primary focus was on efficiency improvements. In contrast, Chennai underwent a more comprehensive transformation, covering the entire manufacturing chain from design and production to dispatch and supply chain optimisation. The goal at Chennai was to reduce overall turnaround time, significantly cutting the cycle from customer order receipt to final dispatch,” he added.
While Chennai benefited from a stronger digital foundation, CEAT did not merely replicate Halol’s use cases but developed new ones tailored to Chennai’s specific needs, further driving end-to-end operational efficiency.
Commenting on the challenges surrounding this paradigm shift, the executive noted, “Integrating legacy systems with Industry 4.0 technologies posed a significant challenge as ensuring compatibility between older manufacturing infrastructure and new automation, IoT and AI-driven solutions required meticulous planning and phased implementation.”
“Another critical hurdle was maintaining data quality and governance, necessitating robust validation processes, data lineage tracking and an accountability framework to enhance data integrity and reliability,” he added.
Answering whether such transformation is possible on OTR production lines, he said, “Unlike passenger or two-wheeler tyres, OTR tyres have a longer cycle time and high levels of customisation, making digital automation less complex but highly specific. While digital transformation is feasible, CEAT plans to prioritise full automation at Nagpur in the next 18–24 months, before shifting focus to digitalisation in OTR production.”
Workforce re-alignment
CEAT is reshaping its workforce strategy to align with its digital transformation, ensuring that shop floor employees are equipped and actively involved in adopting new technologies.
It has digitised over 100 operator touchpoints to secure operator buy-in. The programme simplifies shop floor tasks through digital tools, MES integration and real-time dashboards, allowing operators to make decisions independently and reducing reliance on supervisors. Every operator has undergone basic digital awareness training to facilitate this transition.
A key move was the introduction of business translators, who are frontline supervisors with strong technical acumen. They bridge shop floor pain points with digital solutions. Working alongside data engineers and scientists, these individuals co-develop AI-driven use cases, such as reducing setup time in mixing processes to improve efficiency.
The company also strengthened its talent pipeline, hiring computer science graduates, a rarity in the tyre sector just a few years ago. It has pioneered hiring female operators in the tyre industry, beginning in Halol in 2009.
“Today, 24–30 percent of shop floor employees in Chennai and Nagpur are women. While digitalisation isn’t the primary driver of this shift, automation has made traditionally labour-intensive jobs more accessible. The company also enforces pro-women policies, including home pick-ups and drop-offs, designated rest areas, female security and an internal support forum (V Power) to address workplace concerns,” informed Kuruppal.
When asked whether digitisation will lead to a cut in vacancies, Kuruppal stated, “Contrary to fears that digitalisation reduces shop floor jobs, we find ourselves grappling with the bigger challenge of talent attraction. Post-pandemic, fewer young workers are willing to pursue manufacturing roles, with many opting for finance, retail and IT-driven careers instead. This trend is evident across major tyre-producing states like Tamil Nadu, Maharashtra and Gujarat.”
“While automation and AI reduce physical strain and deskill certain operations, a fully manless tyre plant remains economically impractical in the near term. However, with rising labour costs and shrinking workforce interest, a fully automated future – perhaps within 15–20 years – isn’t off the table,” he added.
Sustainability through digitisation
CEAT is driving sustainability through digital transformation, reducing energy and water consumption while lowering its carbon footprint. Energy efficiency measures have led to a 15 percent reduction in power consumption at Halol and 25 percent at Chennai.
Renewable energy accounts for 40 percent of the company’s power mix, cutting Scope 1 and Scope 2 carbon emissions by nearly 30 percent. Water usage has been reduced by 30-35 percent over the past three years through steam optimisation, with future plans to eliminate steam in curing.
In green material adoption, integrating silica-based compounds in tyre manufacturing has required process adjustments as it increases cycle time. CEAT collaborates with equipment manufacturers to enhance efficiency. It has upgraded mixers to improve silica processing and support its shift towards sustainable materials.
Commenting on future plans to implement digital solutions, Kuruppal said, “We plan to integrate virtual and mixed reality into the manufacturing processes to enhance equipment maintenance and reduce mean time to service. We are also exploring AI-driven process optimisation, as these models will auto-correct processes in real-time, enhancing product consistency and accelerating decision-making. These technologies will also help identify and eliminate bottlenecks in manufacturing and planning, ensuring a more agile and efficient production flow.”
“The company is looking into GenAI to address complex operational challenges. AI-driven predictive maintenance will improve equipment reliability by forecasting potential failures before they occur. Additionally, GenAI will optimise supply chain and production planning, ensuring better resource allocation and efficiency,” he added.
Pirelli Launches New Scorpion All Season SF3 Tyre For SUVs
- By TT News
- July 01, 2025
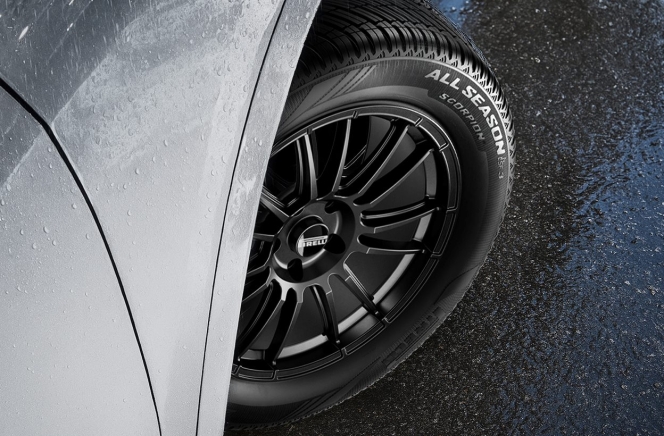
Pirelli has introduced the Scorpion All Season SF3, a new all-season tyre specifically engineered for SUVs, building upon the award-winning technology of the Cinturato All Season SF3 while tailoring performance to the demands of larger, heavier vehicles.
Designed for safety and versatility across diverse weather conditions, the tyre has already earned top ratings in independent Dekra tests, excelling in cumulative braking performance. It carries an ‘A’ rating for wet grip on the European tyre label and meets the 3PMSF standard for certified snow traction. Additionally, the Scorpion All Season SF3 prioritises driving comfort, with a ‘B’ rating for external noise and class A/B efficiency in rolling resistance, ensuring long-lasting performance and lower emissions. The compound is engineered for stiffness and high-temperature stability, while new polymer blends and natural-origin resins enhance cold-weather grip without sacrificing wet traction. Pirelli leveraged AI-driven Virtual Compounder technology to refine the material composition, alongside 3D modelling to synchronise tread and compound design for optimal performance.
To enhance SUV handling, Pirelli incorporated reinforced tread blocks with a progressive entry geometry, which gradually increases the contact patch with the road. This design minimises pressure peaks, reducing vibrations and noise while improving stability and grip – particularly beneficial for heavier vehicles. The tread also features an adaptive structure with 3D sipes that evolve from straight lines to a zigzag pattern as the tyre wears, maintaining snow traction even with reduced tread depth. These sipes dynamically adjust under pressure, shifting between a winter-optimised and summer-friendly profile for balanced year-round performance.
The Scorpion All Season SF3 expands Pirelli’s all-season lineup, catering to the rising demand for versatile tyres. Available in 17- to 21-inch sizes, select models include Elect technology for compatibility with electric and plug-in hybrid vehicles, as well as the Pirelli Noise Cancelling System (PNCS) to reduce road noise.
Bridgestone Logistics Transfers 66.6% Shares To SBS Holdings
- By TT News
- July 01, 2025
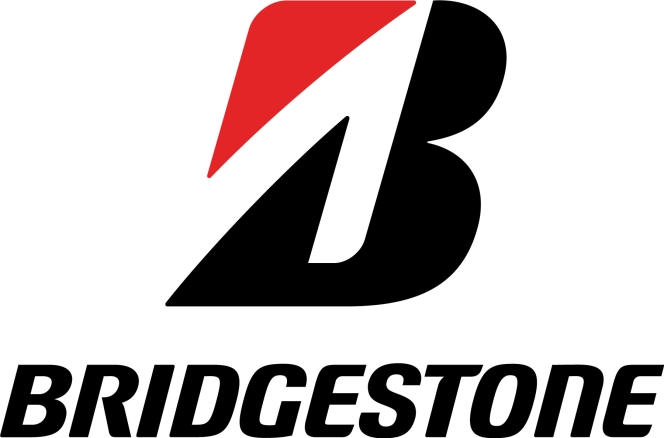
Bridgestone Corporation has agreed to transfer 66.6 percent shares of its wholly owned subsidiary, Bridgestone Logistics Co., LTD, to SBS Holdings, Inc. This move aligns with Bridgestone’s strategy to strengthen its global business by adapting to dynamic market conditions and building a foundation for sustainable growth. In Japan, the company is restructuring operations to enhance productivity and innovation across its value chain, from tire development to logistics and sales. The share transfer is part of these broader efforts to optimise business performance.
The Japanese logistics sector is experiencing major shifts due to carbon neutrality goals, sustainable supply chain demands and labour shortages. SBS Holdings, a key player in the industry, sees these challenges as growth opportunities and is implementing forward-looking strategies. By integrating Bridgestone Logistics into its operations, SBS Holdings aims to bolster the subsidiary’s business and management capabilities, positioning it for future expansion.
Bridgestone Logistics has been advancing sustainable logistics through digital solutions, including next-generation delivery systems, collaborative logistics to improve efficiency and modal shifts toward eco-friendly transport. These initiatives will support SBS Holdings’ mission to ensure safe, secure and sustainable logistics operations. Additionally, SBS Holdings’ adoption of electric vehicles, logistics technology and IT-driven systems will further enhance efficiency. The collaboration will unlock synergies by leveraging SBS Holdings’ expertise, network and resources, enabling Bridgestone Logistics to explore new business opportunities beyond the Bridgestone Group and create greater social and customer value. Moreover, by aligning with SBS Holdings’ workforce development strategies, Bridgestone Logistics will foster talent growth and organisational innovation.
ETRMA Speaks On Automotive Sector Interpretation Guide Of Data Act
- By TT News
- July 01, 2025
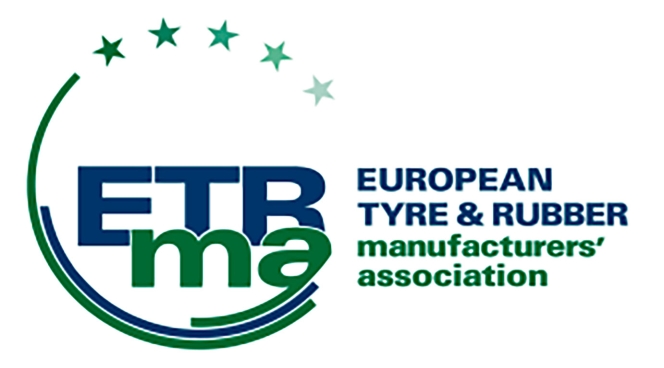
The European Commission’s Industrial Action Plan for the automotive sector included plans to publish Guidance on in-vehicle data alongside the implementation of the Data Act. In response, the European Tyre and Rubber Manufacturers’ Association (ETRMA), alongside other automotive industry groups, has developed an Automotive Sector Interpretation Guide of the Data Act to foster a common understanding ahead of the regulation’s application. This joint effort has helped clarify critical definitions and regulatory interfaces while also incorporating essential tyre-specific considerations – a step ETRMA strongly supports.
Despite this progress, the Data Act’s objectives may fall short without additional measures. Key solutions – such as human-machine interface (HMI) access for user consent and digital ID federation to enable secure, efficient data sharing within a unified European data space – require further exploration under sector-specific regulation. ETRMA remains dedicated to ensuring the Data Act’s implementation promotes fair, non-discriminatory access to in-vehicle data. The association will continue pushing for enforceable rules that guarantee real-time, secure and efficient access to relevant data, safeguarding innovation and competitiveness in the automotive and tyre industries.
Bridgestone India Strengthens Retail Presence with New Select Store In Nashik
- By TT News
- June 30, 2025
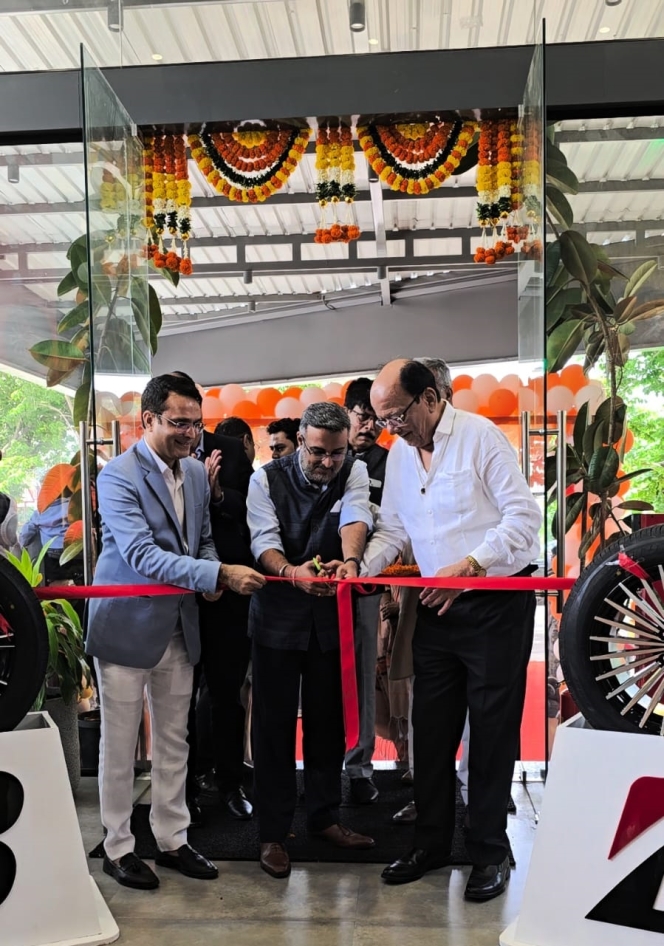
Bridgestone India, a key subsidiary of the global Bridgestone Group and a leader in tyres and mobility solutions, has expanded its premium retail network with the launch of Bridgestone Select Store – M/s Nashik Tyres and Services. The store was inaugurated by Rajarshi Moitra from Bridgestone India, reinforcing the company’s commitment to delivering innovative, customer-centric tyre retail experiences across the country.
Strategically located in Nashik, the store features modern infrastructure and a premium service setup, positioning it as a one-stop destination for tyres and related services in the region. Recognising that tyres are the sole contact point between a vehicle and the road, Bridgestone emphasises safety, performance and driving confidence through its Select stores. These outlets not only help customers choose the right tyres but also enhance their ownership experience with expert guidance and high-quality services.
With over 900 Select stores nationwide, Bridgestone India has established a premium retail network that goes beyond tyre sales to offer a superior, service-driven experience. The expansion of M/s Nashik Tyres and Services further strengthens Bridgestone’s mission to bring world-class tyre solutions closer to customers, reinforcing its pan-India presence with a focus on innovation and customer satisfaction.
Moitra said, “At Bridgestone India, we are committed to redefining the tyre buying experience through our Select stores. As we continue to expand our footprint and enhance manufacturing capabilities our goal is to provide premium products, services and customer experience.”
Comments (0)
ADD COMMENT