Changing Compounds Open Vistas For Smart Mixing, Upgraded Technologies
- By Sharad Matade
- April 17, 2025

The tyre industry is undergoing a profound transformation, driven by sustainability, digitalisation and material innovations. As manufacturers push the boundaries with high-silica compounds, recycled rubber and alternative materials like dandelion rubber, the mixing process faces increasing complexity. Traditional methods struggle to maintain efficiency, necessitating advanced technologies like HF Mixing Group’s Tandem mixing and smart solutions. With automation, and precision engineering, the industry is redefining efficiency and sustainability.
Tyres are a sheer example of impeccable chemical engineering. From passenger car radials (PCR) to off-the-road (OTR), these technical marvels can carry loads weighing tonnes even in the deadliest of roads. For centuries, they have been the backbone of logistics, transportation and more.
But making a tyre is not an easy task. It involves a tremendously meticulous process ranging from raw material selection to mixing compounds for deriving the exact formula that gives these rubber casings durability, elasticity and more.
As the global tyre industry undergoes a transition in every critical aspect, it also sees a change in compounds that go into mixtures. This in turn paves the way for upgradation in technologies.
According to HF Mixing Director of Product and Services, Nils Spier, “The growing use of silica in passenger tyres is reshaping the industry with specifications now reaching 100, 130 and even 180 parts per hundred rubber (PHR). Levels above 150 PHR have recently gained traction, particularly in the premium segment, where high-performance tyres demand lower rolling resistance and improved wet grip.”
On the other hand, he revealed to Tyre Trends that increasing silica content presents technical challenges. Standard single-mixer setups face limitations due to the need for adequate silanisation time. When more silica is added, the process becomes more complex and time-consuming. HF Mixing Group’s Tandem mixing technology addresses this by transferring the process from an upper to a lower mixer, preventing capacity losses and optimising mixing efficiency.
“Dispersion is another critical factor as silica’s inherent stickiness complicates processing. The upper mixer completes the dispersing task, utilising a geometry established in the industry for over 20 years. The latest-generation PES7 mixer builds on this, ensuring the same high-quality results. Once the compound moves to the lower mixer, further refinements occur. A specialised bottom mixer rotor TRC, developed to enhance cohesion and compacting, helps mitigate issues where certain components tend to crumble. Without this step, batches risk fragmenting into plates and uneven portions, complicating further processing. The Tandem mixer’s rotor system ensures that the full batch remains intact, facilitating smooth transfer onto a mill or twin-screw extruder,” he added.
In a nutshell, the Tandem mixing technology allows tyre manufacturers to accommodate higher silica content without compromising processing efficiency or final product quality.
HF’s latest advancements in mixing technology are delivering notable efficiency improvements, particularly in intermeshing rotor systems. The PES7 rotor, introduced around two years ago, has now been successfully deployed at multiple customer sites, showing strong results in both new and retrofit applications. The rotor upgrade offers an increased mixer empty volume plus higher possible fill factors, resulting in a 10–15 percent increase in throughput without compromising cycle time or product quality.
UPGRADING MIXING TECHNOLOGY THROUGH SMART DIGITAL SOLUTIONS
According to Spier, “Tandem and the smart digital mixing solutions represent a holistic approach to optimising the mixing process. The smart final mixing solution is a software and service concept developed by HF, designed to work in close collaboration with customers. The process begins with defining the customer’s target recipe and process parameters, followed by calibration tests conducted on-site.”
Calibration tests involve capturing the fingerprint of the mix including rotor speed, drive data, temperature control unit settings and ram seating time. This data is then processed through the company’s proprietary algorithms and material models, which simulate various mixing scenarios to identify optimal process parameters.
The simulation models predict key variables such as batch temperature development at different rotor speeds and the impact of ram lift adjustments to improve compound aeration. This approach eliminates the need for extensive design of experiment, accelerating the optimisation process without compromising on productivity of the production equipment.
The smart mixing solution is specifically designed for HF mixers as the company has precise knowledge of the machine parameters, cooling surfaces and other mixer-specific properties. The validation trials conducted post-simulation have demonstrated cycle time reductions up to 20 percent, translating into significant efficiency gains for manufacturers.
Moreover, the company’s smart mixing approach optimises key parameters to enhance energy efficiency and quality in the mixing process. Cycle time is a primary focus with proprietary algorithms minimising unnecessary processing steps while ensuring uniform distribution and dispersion of the curative package.
Rotor speed plays a crucial role as it must be adjusted at different phases of mixing. A higher speed may be beneficial in the initial dispersion stage, but excessive speed leads to rapid temperature increases, negatively affecting compound properties. The company’s models balance rotor speed, energy efficiency and temperature for optimal results.
Lastly, fill factor is essential for both quality and efficiency. Overfilling can result in uneven mixing and longer processing times, while underfilling reduces throughput and jeopardises batch quality. The company’s Smart Final Solution ensures that the fill factor is set to an ideal level for maximum quality and throughput.
TECHNOLOGICAL INCLUSIVITY
The company’s approach to smart mixing is currently data-driven and reliant on process specialists, but the role of artificial intelligence (AI) in this field is expected to grow. “While AI has the potential to make autonomous decisions and process adjustments in the future, we still integrate human expertise alongside digital tools to ensure process reliability. Factors such as installed downstream equipment, mixer conditions and on-site variations must be considered, which currently require operator input. However, we are already exploring AI-driven solutions such as predicting batch temperature, optimising carbon black incorporation and refining oil dispersion, which could eventually enhance process automation,” informed Spier.
While digitalisation is a key part of the company’s transformative roadmap, AI’s role is still in development. Instead of full AI automation, it employs advanced models and algorithms that run extensive simulations to optimise mixing conditions without compromising quality. These models provide real-time feedback on the best possible process adjustments, delivering improvements in efficiency, quality and consistency.
Alluding to whether older mixers installed 5 to 10 years ago can be retrofitted with recent upgrades, he noted, “There is a possibility of retrofitting smart solutions to enhance its capabilities. Rather than relying solely on AI, we offer in-line process monitoring, where historical mix data is used to establish a reference baseline with tolerance bands. This allows for real-time adjustments.”
The mixing process is fully automated with step-related control systems defining key parameters such as mixing time, specific energy input and rotor speed per step, batch temperature to ensure precision and consistency. Every mixing step can be supported by HF’s unique intelligent controller technology such as intelligent Ram control iRam, the HF constant temperature controller or iXSeal Dust Stop Lubrication Controller.
PROCESS ADAPTATION
Tyre makers are increasingly experimenting with alternative materials, such as recycled rubber and dandelion-derived compounds, which significantly impact the mixing process. Adjustments are necessary to maintain efficiency and quality, as non-traditional materials alter torque curves and require parameter modifications.
Moreover, different category of tyres requires different mixing processes due to variations in tread compound formulations. Passenger car tread compounds typically differ from OTR formulations, necessitating specific dispersion techniques to achieve the desired performance characteristics.
With that said, it is prudent that companies adapt to changing processes fuelled by market demand. “The company provides a range of rotor solutions to optimise these mixing processes. Tangential rotors are designed to enhance master batch dispersion, especially the NST rotor, ensuring uniformity in the compound. ZZ rotors are mainly used for final batch production, offering precision in mixing the final formulation. In addition, the ZZ rotor geometry has proven strong performance in Master Batch Silica Processing. Additionally, intermeshing rotors are employed to manage specialised compounds, providing better control over the mixing process for unique material requirements,” revealed Spier.
Furthermore, material innovations are significantly impacting the mixing process, requiring process adaptations to maintain efficiency and achieve consistent final results. The use of alternative materials such as recycled rubber or non-traditional sources like dandelion rubber, rCB and other recycled materials alters the torque curves during mixing. These changes necessitate adjustments to mixer parameters, ensuring optimal dispersion and processing without compromising product quality.
To support customers in navigating these challenges, HF’s process experts collaborate closely with them through the technical centre in Germany and worldwide operating process engineers. By testing new processes before full-scale industrialisation, the company helps identify and resolve potential issues in advance.
INDUSTRY SHIFTS
The shift towards premium tyres is shaping the European, Asian and North American markets differently. In Europe, manufacturers are increasingly focusing on premium and OTR tyres while scaling back production of 15–17-inch models and consolidating operations.
This shift is driving higher demand for advanced compounds and increased silica usage. However, capacity expansions remain limited with most investments directed towards equipment upgrades rather than new production facilities.
In Asia, particularly in India and China, greenfield projects are on the rise due to strong automotive demand. This expansion reflects the region’s growing role in the global tyre industry as manufacturers invest in new facilities to meet both domestic and export needs. North America, on the other hand, is seeing a mix of replacement investments and selective large-scale expansions with companies balancing modernisation efforts and strategic growth.
Beyond these key regions, North Africa, specifically Algeria, Morocco and Egypt, is emerging as a new manufacturing hub. This region is gaining traction in the global tyre industry, an area where it previously had little presence. With increasing investment and infrastructure development, North Africa is positioning itself as a competitive player in tyre production.
With many manufacturers shifting to smaller campaign to accommodate different tyre recipe, flexibility in the mixing process has become essential. HF’s automation system is designed to handle these challenges by allowing quick modifications to production plans.
Manufacturers can adjust torque, batch sizes and compound quantities without causing disruptions. Additionally, the manufacturing execution system ensures seamless execution, making even short production runs of 5 to 10 batches efficient and cost-effective.
MARKET EXPANSION
Besides Europe, Asian markets such as China and India remain key growth locations for the company. As manufacturers in these regions adopt new technologies to meet evolving industry standards, the demand for efficient and adaptable mixing solutions continues to rise.
“We continue to invest heavily in innovation and research and development to grow in the Asian market. Allocating three percent of our revenue to innovation and 4.5 percent to development, the company ensures that 35 percent of its projects focus on sustainability. By maintaining technology leadership, we deliver high-quality, high-functionality equipment that supports the growth of new and established manufacturers in the region,” informed Spier.
While HF is known for its high-precision machines used by top-tier tyre manufacturers, it also caters to tier 2 and tier 3 players. The company supplies to many smaller manufacturers.
On the context of sustainability, Spiers noted, “Sustainability is a core focus of our research and development strategy, aligning with the ambitious environmental targets set by tyre manufacturers worldwide. We integrate sustainability by developing energy-optimised mixers with efficient drive setups, introducing new hydraulic power units that significantly reduce power consumption and implementing incremental efficiency improvements such as enhanced heat management to extend machine longevity.”
Lastly, the company provides comprehensive service beyond commissioning, including operator training, process optimisation and trouble-shooting, round-the-clock support via ticket and hotline systems and fast-response local service teams across China, South-East Asia, India, North America, North Africa and Europe.
Anshuman Singhania Honoured As CEO of the Year At National Management Summit
- By TT News
- August 25, 2025
Anshuman Singhania, Managing Director of JK Tyre & Industries, has been awarded the 'CEO of the Year' by the Top Rankers Management Club. The accolade was presented at the 25th National Management Summit, held in New Delhi on 23 August 2025.
The award recognises Singhania’s exceptional leadership and strategic vision, which have been pivotal in steering the company toward sustained growth and innovation. Under his guidance, JK Tyre has reinforced its position as a leader in radial tyre technology, expanded its global presence and strengthened its dedication to sustainability and customer focus.
In his acceptance speech, Singhania expressed his gratitude, stating, “I am honoured to receive this recognition from the Top Rankers Management Club. This award reflects the collective commitment of the entire JK Tyre team, whose efforts continue to drive our progress. I would like to thank my colleagues, industry partners and stakeholders for their unwavering support in our journey of growth and transformation.”
He has been a key figure in modernising the company, leveraging new technologies and expanding its presence in both domestic and international markets. The 'CEO of the Year' award, presented by the Top Rankers Management Club, celebrates leaders who demonstrate a clear vision for organisational excellence and industry transformation.
Hana RFID Appoints Jason Chang As New Asia Sales Director
- By TT News
- August 21, 2025
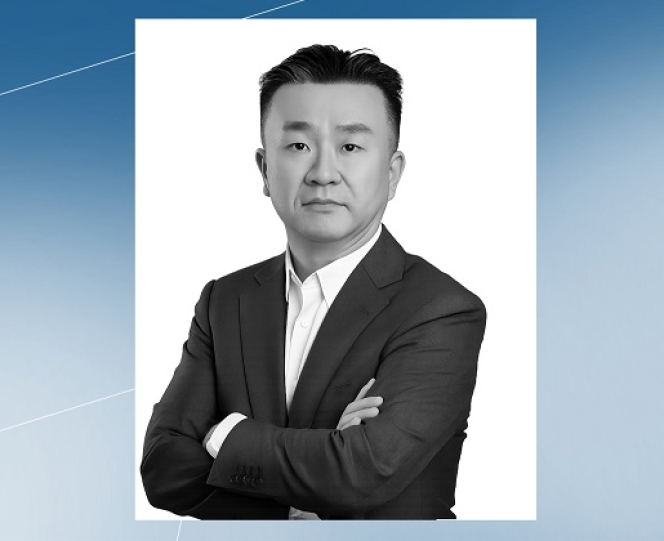
Hana Technologies, Inc. (Hana RFID) has strengthened its leadership in the Asian market with the appointment of industry veteran Jason Chang as Sales Director for Asia. Based in Shanghai, he will be responsible for managing key customer relationships and driving strategic growth throughout the region.
Chang brings a wealth of relevant experience to the role, with over 15 years in the RFID sector following a successful career in IT. His proven track record includes significant tenures at leading firms like Xerafy, Stora Enso and Beontag. His accomplishments range from pioneering the development of innovative flexible anti-metal tags to launching groundbreaking RFID-based retail solutions that gained widespread adoption in China and Europe. He has also demonstrated a strong capacity for growth, most recently achieving remarkable business expansion in the APAC market.
This appointment is a strategic milestone for Hana RFID, underscoring its commitment to supporting global customers with high-performance technology and expert, on-the-ground leadership. This move highlights Hana RFID's focused strategy on deepening its regional support and providing partners with sophisticated RAIN RFID inlay and embeddable tag solutions, backed by local expertise.
Mike Hetric, Senior Vice President – Sales & Marketing, Hana RFID, said, “The appointment of Jason Chang is a significant step forward in improving local availability and supporting our key partners in Asia. Jason’s track record in driving innovation, his deep market knowledge and his commitment to customer success will be invaluable as we expand our footprint in this dynamic region.”
Chang said, “I’m excited to be part of the Hana RFID team, which is recognised in the market as both a key player and a trusted partner for an ever-growing network of label converters, service bureaus and system integrators. I look forward to working alongside our partners in Asia to deliver innovative solutions and exceptional service.”
Ralson Tire North America Expands Leadership Team
- By TT News
- August 21, 2025
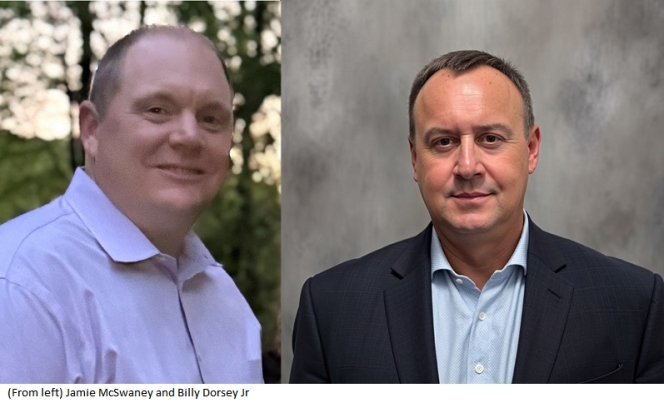
Ralson Tire North America (RTNA) has expanded its leadership team with the appointment of two seasoned tyre industry professionals.
As per the new development, Billy Dorsey Jr has been appointed as Vice President of Sales – South and Jamie McSwaney has been appointed as Vice President of Sales – North. Both the new appointments bring a combined 45 years of tyre industry experience to the company.
Brian Sheehey, President, RTNA, said, “These additions signal our unwavering commitment to accelerating Ralson’s growth in the US and Canada. We’re building a leadership team that knows how to compete, win and deliver results. Their deep industry relationships and ability to execute will be instrumental as we continue to grow our footprint in the North American trucking industry.”
Nordic Market Will Fare Well For Premium Tyres: Citira
- By Gaurav Nandi
- August 21, 2025
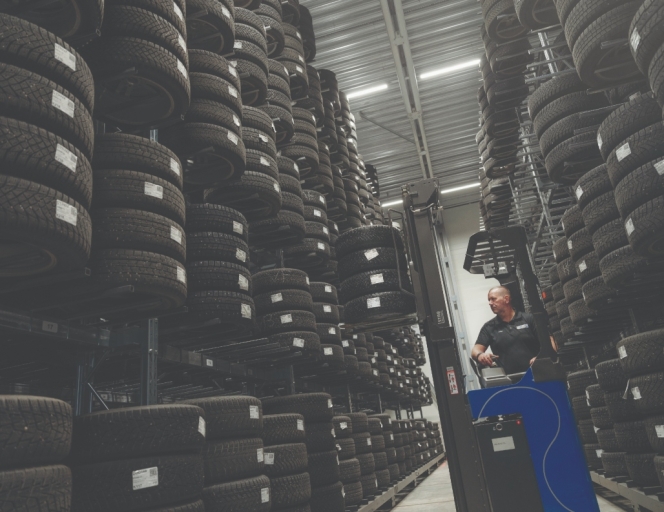
Scandinavian tyre service provider Citira sees robust potential for premium tyres in the Nordic region, driven by seasonal demands and safety priorities. CEO David Boman highlights that premium tyres including Pirelli’s offerings hold a significant share in passenger car, light truck and truck tyre segments supported by harsh winter conditions that emphasise performance and reliability. Despite a slight recent decline amid broader economic pressures and rising price sensitivity, premium brands remain relevant. Citira’s new long-term partnership with Pirelli and acquisition of Dackia AB aims to consolidate and optimise premium tyre distribution across Sweden.
Scandinavian tyre service company Citira recently told Tyre Trends that Nordic countries have excellent potential for premium tyres during a discussion over its partnership with Italian tyre major Pirelli.
Speaking on the market potential, Chief Executive Officer David Boman said, “When it comes to the Nordic markets, Scandinavia in particular has a relatively high share of premium tyres across categories including passenger car, light truck and TBR segments. Compared to other global regions, the demand for premium tyres here is notably strong.
“One of the main reasons for this is the seasonal nature of our market. Winter tyres, in particular, drive a more premium-oriented approach because of the need for high performance and safety under harsh conditions. While we’ve observed a slight decline in the premium tyre share over the past few years, it still holds a significant portion of the market. This demand is closely tied to seasonal safety concerns, especially in winter, autumn and early spring. Drivers here prioritise safety and reliability, which naturally supports the continued relevance of premium brands like Pirelli.”
He noted that the decline is likely tied to broader financial challenges in the market, especially following the Covid period. Both consumers and companies have become more price-sensitive, making cost a bigger factor in purchase decisions.
As a result, there’s been a gradual increase in demand for lower-cost, imported non-European tyre brands, while the market share of European premium tyre brands has slightly decreased.
Pirelli and Citira have entered a long-term strategic partnership aimed at enhancing their market presence in Sweden. As part of the deal, Citira will acquire Dackia AB that has a network of 102 retail outlets from Pirelli.
In return, Pirelli and Dackia have signed a supply agreement extending to 2030, ensuring Pirelli remains the main tyre supplier. The transaction, pending regulatory approval, is expected to close by 2025. The partnership will boost Pirelli’s distribution and market coverage while supporting Citira’s goal of expanding a sustainable, flexible and high-quality customer service network.
THE PACT
Citira currently runs over 50 tyre shops and over five retreading units across Scandinavia and Poland. “Citira is actively working towards creating a more efficient and consolidated tyre market. While our current focus is primarily on the Scandinavian region, it’s not out of the question that we may consider expanding beyond this geographic perimeter in the future. This agreement is part of a broader industry trend where partnerships and acquisitions are used to enhance efficiency, strengthen distribution networks and provide end customers with better service coverage,” revealed Boman.
Nonetheless, the deal specifically pertains to the Swedish market, and as part of the regulatory process, Citira has conducted a market analysis to understand the potential implications on market share. However, the specifics of that study were said to be confidential and could not be disclosed prior to the official closing of the deal.
Explaining how this partnership will influence the supply chain of premium tyre in the Nordics, Boman said, “We do anticipate some changes, particularly within Citira. We operate a number of logistics centres, and this partnership presents an opportunity to optimise our overall supply chain setup. Enhancing logistics will be a key enabler of better service and responsiveness in premium tyre distribution.”
He added, “This particular deal is unlikely to have a direct or immediate impact on independent retailers or smaller distributors. More broadly, the Scandinavian tyre retail sector is undergoing consolidation. Several players are actively reshaping the competitive landscape and that trend could gradually influence the positioning of independents. But again, this specific acquisition is not a disruptive event in that context.”
Alluding to the current demand for replacement tyres, he said, “In general, the tyre market has proven to be quite non-cyclical. Even in challenging economic conditions, it tends to remain stable. That said, I believe we’re entering a phase where circularity and life-extension solutions will gain more momentum. We’re likely to see increased focus on services that extend tyre life, especially for larger fleets. This shift won’t just be driven by cost or fleet uptime concerns but increasingly by environmental responsibilities.”
THE BUSINESS
According to Boman, Pirelli represents a very minimal share of Citira’s overall sales, currently. However, the strategic partnership mainly revolves around Dackia and Pirelli, and the former is intended to become part of the Citira Group. “Moving forward, there is definitely an opportunity to deepen the collaboration with Pirelli and potentially grow their share within our overall brand mix,” added Boman.
Citira currently follows a multi-brand strategy and will continue with it even after closing of the deal. Besides, it is also involved in process and sales of retreaded TBR tyres and wheel rims.
“We operate a facility in Poland where we refurbish truck and bus rims. The process involves media blasting and repainting the rims to restore its appearance and functionality. The logic behind it is quite similar to retreading. In most cases, the structural integrity of the rim is still intact; it’s just the surface or aesthetics that degrade over time. By restoring these rims, we’re able to extend the life and reduce waste,” said Boman.
The company operates five retreading facilities collectively, located in Finland, Sweden and Poland. It uses both hot-cure and cold-cure retreading methods. Hot-cure is used in Poland and cold retreading in Finland and Sweden. Annually, it retreads around 160,000 tyres, averaging about 13,000 per month. While its current focus is on retreading, Citira is actively exploring expansion into tyre recycling as part of a broader push towards sustainability and circularity.
The company also manages tyre distribution for fleets across countries. Its circular tyre distribution approach involves not only delivering new tyres to customers but also collecting used tyre casings from them. These casings are then sent back to its retreading facilities, creating a closed-loop system. Besides, Citira has different suppliers across Europe for sourcing tyres for retreading.
MARKET WATCH
Citira sees a strong willingness in the market for consolidation and it has already engaged in several partnerships. Commenting on market challenges, Boman said, “One key challenge is the need for a player capable of driving consolidation at a larger scale. In the Scandinavian markets, this kind of brand-independent consolidation hasn’t really taken place over the last 10 to 15 years. Previously, consolidation efforts were primarily led by tyre manufacturers or affiliate networks players. However, consolidation has largely been on hold recently, leaving space for an independent actor to step in. We see that opportunity clearly and believe it is well received both by other market participants and customers. The challenge lies in successfully executing this consolidation while maintaining trust and delivering value across a diverse market.”
Commenting on the demand for retreading, he said, “The Scandinavian market has a long tradition of retreading heavy vehicle tyres. Currently, there is a growing shift towards pay-per-kilometre or tyre-as-a-service models, especially among large fleets like bus companies and hauliers. Notably, public tenders increasingly require a certain share of retreaded tyres, reflecting a strong environmental focus. Retreading extends the life of a tyre by reusing about 70 percent of its original material, making it a significant sustainability tool. The market share of retreaded tyres is gradually increasing with expectations that the retread market will grow faster than the new tyre market in the coming years.”
“The main challenges for the retreading industry lie in overcoming the longstanding perception that retreaded tyres are merely a low-cost option rather than an environmentally friendly and sustainable product. This is mostly prevalent is Scandinavia and it is crucial to shift this mindset by educating customers and the broader market about the true benefits of retreading. Moving away from a purely price-driven sales approach to one that highlights quality, durability and positive environmental impact remains a significant hurdle for the industry,” he added.
Comments (0)
ADD COMMENT