How To Use Virtual Modelling Technologies For Smart Tyres
- By TT News
- March 04, 2025
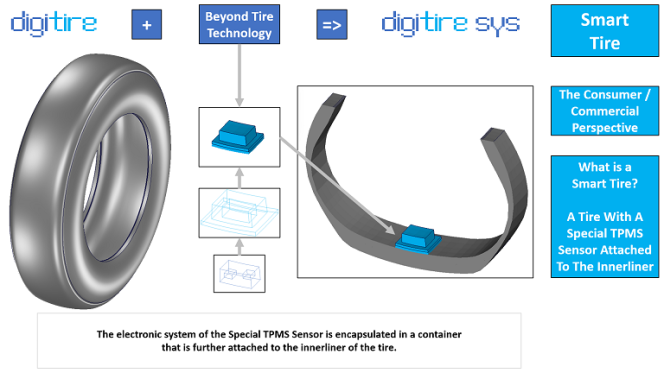
For more than 30 years, Haluk Kizilay has built an impressive career that spans everything from tyre design and development to strategic planning, marketing and business development, both in Turkey and overseas.
He received BSc in mechanical engineering as well as another degree in Business Management (BBA) in Turkey.
At Brisa, Bridgestone Turkey, Haluk supported executive and functional level of tyre design, material development, production, field evaluation and management. He also engaged in strategic plan development, competitive intelligence, OEM programmes and benchmarking.
In 2011, Haluk moved on to become an ‘R&D Engineering Manager’ in Cooper Tire & Rubber. He took wide-range responsibility for Truck & Bus product development as well as Field Engineering & Business Development.
In addition to design direction at Cooper, he also participated in Product Planning and Global Technology Development and Merger and Acquisition activities in China and Europe.
Haluk is one of the registered researchers of TUBITAK – The Scientific & Technological Research Council of Turkey – and he is also one of the authorised judges of EU Horizon work programme.
In 2019, he established his own consulting firm called ‘TICTire Industry Consulting’ to serve the tyre industry globally.
The global tyre market has been expanding annually at a rate of 2 to 10 percent, depending on the region. This growth is driven by global economic expansion, increased mobility demands and diversification, new business models and other factors. At the same time, the performance requirements for tyres have become more stringent than ever. As a result, the tyre industry is increasingly focused on advanced technologies, including innovative, light and green materials, enhanced modelling and testing methods, embedded systems, environmental sustainability and the development of smart tyres.
To meet these demands, the tyre industry must elevate its New Product Development (NPD) processes by intensifying research and development efforts. In the highly competitive market of the future, and in the new CASE mobility context (which stands for Connected Autonomous Shared and Electric vehicles), the new tyre technology and knowledge will be more critical than ever before.
One significant trend in NPD is the drive to reduce development time through the use of modern simulation and modelling techniques. At TIC-Tyre Industry Consulting, in partnership with Autoadmin Consulting, we emphasise the philosophy of ‘speed to market with the right modelling solutions and innovation’. Virtual modelling technologies are central to this approach, enabling companies to launch world-class products faster and more cost-effectively by eliminating the trial-and-error physical development approaches.
The role of virtual modelling technologies in smart tyre development
Virtual modelling technologies are indispensable for understanding how the various components of a tyre interact. By leveraging modelling and simulation, tyre manufacturers can predict the full range of potential outcomes, including complex and novel testing scenarios beyond what traditional mental models can anticipate.
As a critical vehicle safety component, the tyre significantly impacts overall vehicle performance and has now new ‘attributes’ like providing various data about the tyre status in real time. Therefore, designing high-quality, high-performance tyres require not only an understanding of their intrinsic properties – such as tread pattern, carcass structure, materials characteristics – but also the external running conditions like vehicle load and speed, wheel torque and road surface. Virtual tyre models, built with the FEA (finite element analysis) method, provide a comprehensive framework for evaluating and understanding the impact of these variables, particularly in the case of smart tyres applications.
Here are some examples of how tyre FEA simulation and tools can unlock the potential of virtual modelling technology:
• Component and system development: Creating models for tyre carcasses, plies, belts, reinforcements and tread patterns, including beyond tyre components (such as RFID or TMS sensors) for structural analysis.
• Predictions of footprint and stiffness characteristics: Simulating static or quasi-static footprint behaviour under normal, lateral and torsional forces.
• Predictions of force and moments: Simulating steady state rolling during braking, acceleration and cornering.
• NVH applications: Evaluating tyre cavity profile, tread block design, void areas, non-skid depth, groove angles and pitch sequencing.
• Emerging technologies applications: Addressing new tyre engineering challenges like traceable, silent, studded tyres with the integration of TMS or RFID sensors, innerliner foams or tread studs and EV-specific reinforcements requirements for high load capacity tyres.
The game changer: Adopting a 3D modelling approach first to tyre design
The tyre industry must fully transition to a 3D first mindset when designing products, just as other industries – such as automotive and aerospace – have done for parts and assemblies. Today, every component of a vehicle, whether for ICE vehicles or EVs, is first modelled in 3D space. From these models, 2D sketches, assembly and execution drawings are derived using cutting, cross-sectioning and projection techniques for manufacturing plans.
By adopting this approach, tyre designers can address the complexities of designing emerging technologies for smart tyre development, such as various sensors embedded in or glued to the tyre. Likewise for foam in tyre (FIT) and non-pneumatic tyres (NPT) technologies. This shift from traditional 2D design thinking to a comprehensive 3D space representation will enable the industry to better meet the challenges of smart tyre innovation.
Advancing FEA for proactive tyre development
To achieve higher levels of ROI in FEA simulations and tools, the industry must integrate the latest advancements in FEA technology. These efforts should be proactive, conducted well before manufacturing begins. The outdated 2D to 3D model creation approaches, involving the solver in the model creation stage, no longer suffices, besides having many limitations. Given the increasing complexity of tyre design and the massive data exploration required for simulations and testing various load cases, automations in post-processing should also be considered.
To succeed in this environment, manufacturers must rely on expert knowledge. Virtual modelling technologies provide the tools needed to address these challenges and seize new opportunities, empowering the tyre industry to lead in innovation and performance.
Support from TIC-Tyre Industry Consulting and Autoadmin Consulting
At TIC-Tyre Industry Consulting and Autoadmin Consulting, our Subject Matter Experts (SMEs) bring extensive hands-on experience in the topics discussed above. We are ready to support R&D activities with tailored technical solutions designed to address unique challenges. We pride ourselves on adhering to the highest professional and ethical standards, a hallmark of our work for many years.
In addition to our consulting services, we offer Simulation and Modelling Technical Courses. These programmes are designed to equip your workforce with the skills, mindset and competencies needed to thrive in today’s competitive environment. Our expert trainers guide participants through an engaging learning journey, incorporating workshops, real-world case studies and cutting-edge educational technologies.
Anshuman Singhania Honoured As CEO of the Year At National Management Summit
- By TT News
- August 25, 2025
Anshuman Singhania, Managing Director of JK Tyre & Industries, has been awarded the 'CEO of the Year' by the Top Rankers Management Club. The accolade was presented at the 25th National Management Summit, held in New Delhi on 23 August 2025.
The award recognises Singhania’s exceptional leadership and strategic vision, which have been pivotal in steering the company toward sustained growth and innovation. Under his guidance, JK Tyre has reinforced its position as a leader in radial tyre technology, expanded its global presence and strengthened its dedication to sustainability and customer focus.
In his acceptance speech, Singhania expressed his gratitude, stating, “I am honoured to receive this recognition from the Top Rankers Management Club. This award reflects the collective commitment of the entire JK Tyre team, whose efforts continue to drive our progress. I would like to thank my colleagues, industry partners and stakeholders for their unwavering support in our journey of growth and transformation.”
He has been a key figure in modernising the company, leveraging new technologies and expanding its presence in both domestic and international markets. The 'CEO of the Year' award, presented by the Top Rankers Management Club, celebrates leaders who demonstrate a clear vision for organisational excellence and industry transformation.
Hana RFID Appoints Jason Chang As New Asia Sales Director
- By TT News
- August 21, 2025
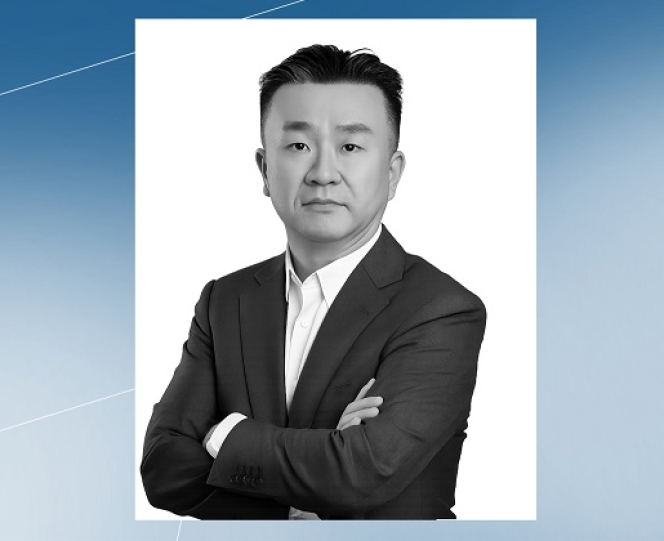
Hana Technologies, Inc. (Hana RFID) has strengthened its leadership in the Asian market with the appointment of industry veteran Jason Chang as Sales Director for Asia. Based in Shanghai, he will be responsible for managing key customer relationships and driving strategic growth throughout the region.
Chang brings a wealth of relevant experience to the role, with over 15 years in the RFID sector following a successful career in IT. His proven track record includes significant tenures at leading firms like Xerafy, Stora Enso and Beontag. His accomplishments range from pioneering the development of innovative flexible anti-metal tags to launching groundbreaking RFID-based retail solutions that gained widespread adoption in China and Europe. He has also demonstrated a strong capacity for growth, most recently achieving remarkable business expansion in the APAC market.
This appointment is a strategic milestone for Hana RFID, underscoring its commitment to supporting global customers with high-performance technology and expert, on-the-ground leadership. This move highlights Hana RFID's focused strategy on deepening its regional support and providing partners with sophisticated RAIN RFID inlay and embeddable tag solutions, backed by local expertise.
Mike Hetric, Senior Vice President – Sales & Marketing, Hana RFID, said, “The appointment of Jason Chang is a significant step forward in improving local availability and supporting our key partners in Asia. Jason’s track record in driving innovation, his deep market knowledge and his commitment to customer success will be invaluable as we expand our footprint in this dynamic region.”
Chang said, “I’m excited to be part of the Hana RFID team, which is recognised in the market as both a key player and a trusted partner for an ever-growing network of label converters, service bureaus and system integrators. I look forward to working alongside our partners in Asia to deliver innovative solutions and exceptional service.”
Ralson Tire North America Expands Leadership Team
- By TT News
- August 21, 2025
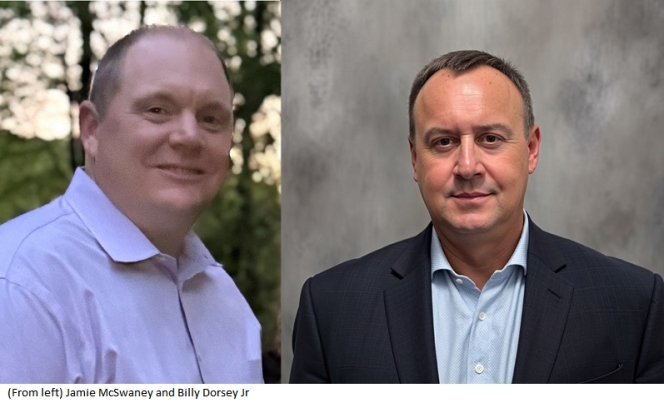
Ralson Tire North America (RTNA) has expanded its leadership team with the appointment of two seasoned tyre industry professionals.
As per the new development, Billy Dorsey Jr has been appointed as Vice President of Sales – South and Jamie McSwaney has been appointed as Vice President of Sales – North. Both the new appointments bring a combined 45 years of tyre industry experience to the company.
Brian Sheehey, President, RTNA, said, “These additions signal our unwavering commitment to accelerating Ralson’s growth in the US and Canada. We’re building a leadership team that knows how to compete, win and deliver results. Their deep industry relationships and ability to execute will be instrumental as we continue to grow our footprint in the North American trucking industry.”
Nordic Market Will Fare Well For Premium Tyres: Citira
- By Gaurav Nandi
- August 21, 2025
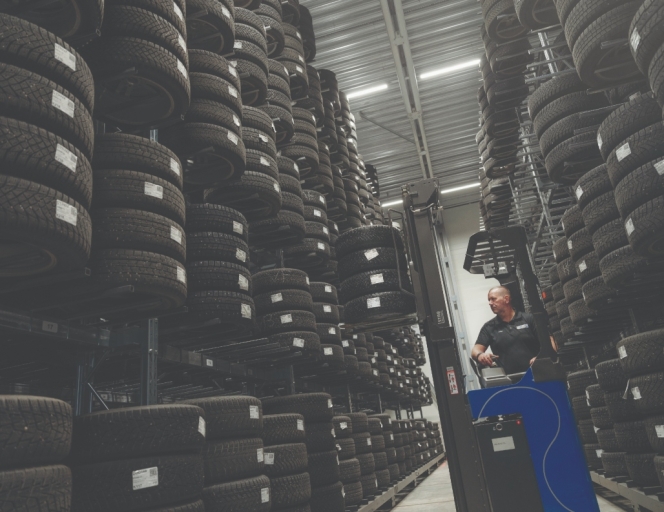
Scandinavian tyre service provider Citira sees robust potential for premium tyres in the Nordic region, driven by seasonal demands and safety priorities. CEO David Boman highlights that premium tyres including Pirelli’s offerings hold a significant share in passenger car, light truck and truck tyre segments supported by harsh winter conditions that emphasise performance and reliability. Despite a slight recent decline amid broader economic pressures and rising price sensitivity, premium brands remain relevant. Citira’s new long-term partnership with Pirelli and acquisition of Dackia AB aims to consolidate and optimise premium tyre distribution across Sweden.
Scandinavian tyre service company Citira recently told Tyre Trends that Nordic countries have excellent potential for premium tyres during a discussion over its partnership with Italian tyre major Pirelli.
Speaking on the market potential, Chief Executive Officer David Boman said, “When it comes to the Nordic markets, Scandinavia in particular has a relatively high share of premium tyres across categories including passenger car, light truck and TBR segments. Compared to other global regions, the demand for premium tyres here is notably strong.
“One of the main reasons for this is the seasonal nature of our market. Winter tyres, in particular, drive a more premium-oriented approach because of the need for high performance and safety under harsh conditions. While we’ve observed a slight decline in the premium tyre share over the past few years, it still holds a significant portion of the market. This demand is closely tied to seasonal safety concerns, especially in winter, autumn and early spring. Drivers here prioritise safety and reliability, which naturally supports the continued relevance of premium brands like Pirelli.”
He noted that the decline is likely tied to broader financial challenges in the market, especially following the Covid period. Both consumers and companies have become more price-sensitive, making cost a bigger factor in purchase decisions.
As a result, there’s been a gradual increase in demand for lower-cost, imported non-European tyre brands, while the market share of European premium tyre brands has slightly decreased.
Pirelli and Citira have entered a long-term strategic partnership aimed at enhancing their market presence in Sweden. As part of the deal, Citira will acquire Dackia AB that has a network of 102 retail outlets from Pirelli.
In return, Pirelli and Dackia have signed a supply agreement extending to 2030, ensuring Pirelli remains the main tyre supplier. The transaction, pending regulatory approval, is expected to close by 2025. The partnership will boost Pirelli’s distribution and market coverage while supporting Citira’s goal of expanding a sustainable, flexible and high-quality customer service network.
THE PACT
Citira currently runs over 50 tyre shops and over five retreading units across Scandinavia and Poland. “Citira is actively working towards creating a more efficient and consolidated tyre market. While our current focus is primarily on the Scandinavian region, it’s not out of the question that we may consider expanding beyond this geographic perimeter in the future. This agreement is part of a broader industry trend where partnerships and acquisitions are used to enhance efficiency, strengthen distribution networks and provide end customers with better service coverage,” revealed Boman.
Nonetheless, the deal specifically pertains to the Swedish market, and as part of the regulatory process, Citira has conducted a market analysis to understand the potential implications on market share. However, the specifics of that study were said to be confidential and could not be disclosed prior to the official closing of the deal.
Explaining how this partnership will influence the supply chain of premium tyre in the Nordics, Boman said, “We do anticipate some changes, particularly within Citira. We operate a number of logistics centres, and this partnership presents an opportunity to optimise our overall supply chain setup. Enhancing logistics will be a key enabler of better service and responsiveness in premium tyre distribution.”
He added, “This particular deal is unlikely to have a direct or immediate impact on independent retailers or smaller distributors. More broadly, the Scandinavian tyre retail sector is undergoing consolidation. Several players are actively reshaping the competitive landscape and that trend could gradually influence the positioning of independents. But again, this specific acquisition is not a disruptive event in that context.”
Alluding to the current demand for replacement tyres, he said, “In general, the tyre market has proven to be quite non-cyclical. Even in challenging economic conditions, it tends to remain stable. That said, I believe we’re entering a phase where circularity and life-extension solutions will gain more momentum. We’re likely to see increased focus on services that extend tyre life, especially for larger fleets. This shift won’t just be driven by cost or fleet uptime concerns but increasingly by environmental responsibilities.”
THE BUSINESS
According to Boman, Pirelli represents a very minimal share of Citira’s overall sales, currently. However, the strategic partnership mainly revolves around Dackia and Pirelli, and the former is intended to become part of the Citira Group. “Moving forward, there is definitely an opportunity to deepen the collaboration with Pirelli and potentially grow their share within our overall brand mix,” added Boman.
Citira currently follows a multi-brand strategy and will continue with it even after closing of the deal. Besides, it is also involved in process and sales of retreaded TBR tyres and wheel rims.
“We operate a facility in Poland where we refurbish truck and bus rims. The process involves media blasting and repainting the rims to restore its appearance and functionality. The logic behind it is quite similar to retreading. In most cases, the structural integrity of the rim is still intact; it’s just the surface or aesthetics that degrade over time. By restoring these rims, we’re able to extend the life and reduce waste,” said Boman.
The company operates five retreading facilities collectively, located in Finland, Sweden and Poland. It uses both hot-cure and cold-cure retreading methods. Hot-cure is used in Poland and cold retreading in Finland and Sweden. Annually, it retreads around 160,000 tyres, averaging about 13,000 per month. While its current focus is on retreading, Citira is actively exploring expansion into tyre recycling as part of a broader push towards sustainability and circularity.
The company also manages tyre distribution for fleets across countries. Its circular tyre distribution approach involves not only delivering new tyres to customers but also collecting used tyre casings from them. These casings are then sent back to its retreading facilities, creating a closed-loop system. Besides, Citira has different suppliers across Europe for sourcing tyres for retreading.
MARKET WATCH
Citira sees a strong willingness in the market for consolidation and it has already engaged in several partnerships. Commenting on market challenges, Boman said, “One key challenge is the need for a player capable of driving consolidation at a larger scale. In the Scandinavian markets, this kind of brand-independent consolidation hasn’t really taken place over the last 10 to 15 years. Previously, consolidation efforts were primarily led by tyre manufacturers or affiliate networks players. However, consolidation has largely been on hold recently, leaving space for an independent actor to step in. We see that opportunity clearly and believe it is well received both by other market participants and customers. The challenge lies in successfully executing this consolidation while maintaining trust and delivering value across a diverse market.”
Commenting on the demand for retreading, he said, “The Scandinavian market has a long tradition of retreading heavy vehicle tyres. Currently, there is a growing shift towards pay-per-kilometre or tyre-as-a-service models, especially among large fleets like bus companies and hauliers. Notably, public tenders increasingly require a certain share of retreaded tyres, reflecting a strong environmental focus. Retreading extends the life of a tyre by reusing about 70 percent of its original material, making it a significant sustainability tool. The market share of retreaded tyres is gradually increasing with expectations that the retread market will grow faster than the new tyre market in the coming years.”
“The main challenges for the retreading industry lie in overcoming the longstanding perception that retreaded tyres are merely a low-cost option rather than an environmentally friendly and sustainable product. This is mostly prevalent is Scandinavia and it is crucial to shift this mindset by educating customers and the broader market about the true benefits of retreading. Moving away from a purely price-driven sales approach to one that highlights quality, durability and positive environmental impact remains a significant hurdle for the industry,” he added.
Comments (0)
ADD COMMENT