- Rubber
- Chemical & Petrochemical Skill Development Council
- RCPSDC
- Ministry of Skill Development and Entrepreneurship
- National Skill Development Corporation
- NSDC
- Saif Mohammad
- skill training
- rubber
- natural rubber
- farmer
- synthetic rubber
RCPSDC Aims To Be A Bridge Between The Government And The Industry
- By Nilesh Wadhwa
- February 26, 2025
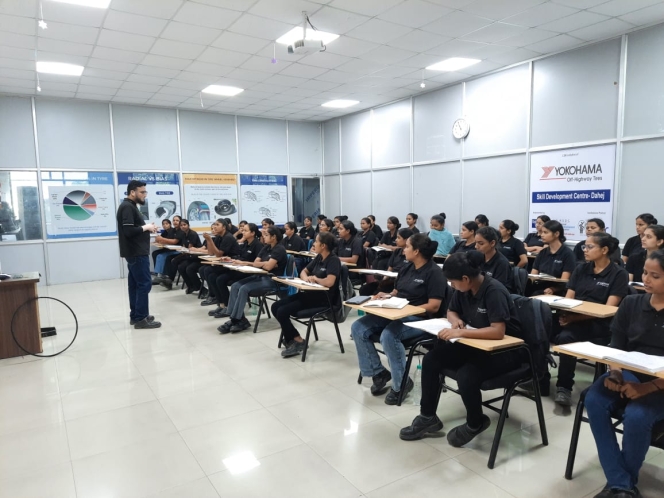
The Rubber, Chemical & Petrochemical Skill Development Council (RCPSDC), under the aegis of the Ministry of Skill Development and Entrepreneurship, set up by the National Skill Development Corporation (NSDC), aims to nurture young talent in the country to improve livelihood opportunities.
The rubber industry in India is facing huge challenges and disruptions, not least due to the shortage of rubber, skilled workforce or the lack of interest among the younger generation in following the footsteps of their predecessors in the natural rubber tapping profession.
But as the proverb goes, ‘every opportunity is a blessing in disguise’, there are stakeholders who are working tirelessly to improve the situation. Among them, Saif Mohammad, CEO of the Rubber, Chemical & Petrochemical Skill Development Council, is optimistic about his organisation’s role in acting as a bridge between the government and the industry.
“A lot of efforts have already been made, and a lot more are ongoing as we speak. We engage with the industry to educate them and actively, proactively seek their feedback on how and what they need, which can be incorporated into our training programmes,” he shared.
As the head of RCPSDC, Mohammad is tasked with driving skill training in the rubber sector by largely complementing the development of qualifications spanning rubber (natural and synthetic) production, rubber product/tyre manufacturing and tyre services and maintenance.
LABOUR SHORTAGE
The development of tyres and other rubber materials is predominantly dependent on rubber tapping, wherein workers make an incision on the tree with a sharp knife, place the collecting cup and repeat the process with subsequent trees. It is estimated that workers carry out this process for hundreds of trees and wait for the cups to be filled with latex. Tapping requires efficient skills to ensure proper incision, so that it does not damage the tree and enables higher extraction of latex.
It may not seem like a very exciting job, given the slow process and subsequently dwindling earnings, which have made it a less lucrative career.
Kerala, once home to the largest rubber tappers in the country, is now facing an acute shortage of skilled workers to continue the profession. Farmers who were earlier involved in the trade are finding it difficult to convince the younger generation to follow in their footsteps.
“A good percentage of the current workforce working as rubber tappers are trained by their predecessors and have no formal training. I believe formal technical training is required alongside training on new technologies, which not only helps them increase their yield but also enables alternative revenue streams,” explained Mohammad.
He elaborated that it is not just about rubber tapping; farmers also need to see the business potential in their profession. They could look at intercropping, beekeeping and other revenue streams.
“India is facing a significant crunch in terms of feed on plantations. Workers are migrating for better opportunities and leaving the rubber industry. Many of them, for example in Kerala, are going abroad for better earning prospects,” added Mohammad.
On one hand, there is labour shortage and drop in yield of natural rubber, but on the other hand, the demand for natural rubber globally, including in India, is scaling new heights. This raises the question: if there is high demand, why are rubber tappers not reaping the benefits?
Climate change, natural disasters and the average price of natural rubber being below expectations have been hurting farmers. For instance, the peak price of natural rubber was INR 20,805 per 100 kg in 2011-12; at present, it is INR 18,800 per 100 kg (as of 26 December 2024). This means that farmers’ incomes have not kept up with inflation, pushing them to explore other revenue streams.
Mechanised solutions do exist, but the high acquisition costs, as well as an ageing population hesitant to continue the profession, have resulted in rubber tapping remaining heavily dependent on skilled workers.
RCPSDC’S ROLE
“The Government of India is doing its part. The Rubber Board, for instance, is working in tappable areas, and several programmes are run with RCPSDC for training people who can work on plantations. However, there is also a transition towards synthetic rubber in India,” he shared.
Mohammad explained that the import of synthetic rubber is increasing. Manufacturers in the MSME space are actively forging or finding new technologies to switch from natural rubber to synthetic rubber.
“The government is working to protect and enrich the workforce and natural rubber in the country and would definitely want India to continue with it and ensure it does not fall below a certain threshold. However, a significant influx of synthetic rubber is also happening. There has to be a balance, and there’s no immediate answer or figure to it. In the last five years alone, we might have trained more than 25,000 to 30,000 workers in Tamil Nadu alone,” he elaborated.
Regional training is also being conducted across the country by the association based on curricula aligned with the National Occupational Standards (NOS). The curricula ensure that students acquire specific skills required for a particular job role as per the guidelines laid down by the industry; in this case, rubber.
He believes that in addition to skilling/upskilling talents, a lot of vocational training is being conducted through educational institutions such as polytechnics.
“Skill councils like RCPSDC also have courses targeted at people who have not even cleared their secondary education. I think one area we should strengthen our focus on is counselling. It is very important for parents as well as students. Candidates and students are under pressure; they are young and usually opt for things that their parents suggest or that they see happening around them (peer pressure),” said Mohammad.
According to him, while there is a lot of glamour around electronics and engineering, proper education and awareness about career progression opportunities in the rubber, polymer or chemical industries should be prioritised.
“Counselling is very important. This is what needs to be addressed by everyone, including industry mentorship programmes. We need to have alumni from these training programmes who can share success stories with newcomers,” Mohammad added.
The executive believes that people are not recognising the immense opportunity to upscale, increase productivity and enhance efficiency because, in the end, everything boils down to the workforce.
An organisation is only as strong as its weakest link. For instance, on the shop floor, if a person is not trained, that is how strong a company is, he stated. And in the global competitive environment, it is very important to acknowledge that people need training and upskilling to ensure they can contribute not only efficiently but also improve their productivity over time.
“If you are planning to take on these futuristic or emerging roles around sustainability and security, then you need to have trained people, right from the ground level upwards,” concluded Mohammad.
Anshuman Singhania Honoured As CEO of the Year At National Management Summit
- By TT News
- August 25, 2025
Anshuman Singhania, Managing Director of JK Tyre & Industries, has been awarded the 'CEO of the Year' by the Top Rankers Management Club. The accolade was presented at the 25th National Management Summit, held in New Delhi on 23 August 2025.
The award recognises Singhania’s exceptional leadership and strategic vision, which have been pivotal in steering the company toward sustained growth and innovation. Under his guidance, JK Tyre has reinforced its position as a leader in radial tyre technology, expanded its global presence and strengthened its dedication to sustainability and customer focus.
In his acceptance speech, Singhania expressed his gratitude, stating, “I am honoured to receive this recognition from the Top Rankers Management Club. This award reflects the collective commitment of the entire JK Tyre team, whose efforts continue to drive our progress. I would like to thank my colleagues, industry partners and stakeholders for their unwavering support in our journey of growth and transformation.”
He has been a key figure in modernising the company, leveraging new technologies and expanding its presence in both domestic and international markets. The 'CEO of the Year' award, presented by the Top Rankers Management Club, celebrates leaders who demonstrate a clear vision for organisational excellence and industry transformation.
Hana RFID Appoints Jason Chang As New Asia Sales Director
- By TT News
- August 21, 2025
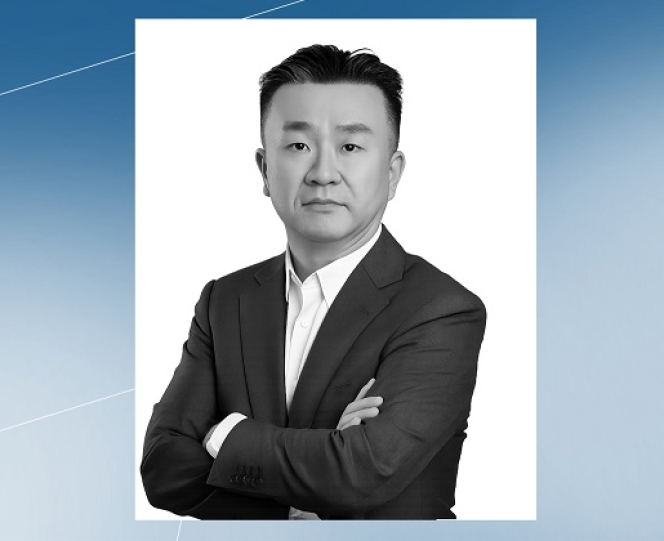
Hana Technologies, Inc. (Hana RFID) has strengthened its leadership in the Asian market with the appointment of industry veteran Jason Chang as Sales Director for Asia. Based in Shanghai, he will be responsible for managing key customer relationships and driving strategic growth throughout the region.
Chang brings a wealth of relevant experience to the role, with over 15 years in the RFID sector following a successful career in IT. His proven track record includes significant tenures at leading firms like Xerafy, Stora Enso and Beontag. His accomplishments range from pioneering the development of innovative flexible anti-metal tags to launching groundbreaking RFID-based retail solutions that gained widespread adoption in China and Europe. He has also demonstrated a strong capacity for growth, most recently achieving remarkable business expansion in the APAC market.
This appointment is a strategic milestone for Hana RFID, underscoring its commitment to supporting global customers with high-performance technology and expert, on-the-ground leadership. This move highlights Hana RFID's focused strategy on deepening its regional support and providing partners with sophisticated RAIN RFID inlay and embeddable tag solutions, backed by local expertise.
Mike Hetric, Senior Vice President – Sales & Marketing, Hana RFID, said, “The appointment of Jason Chang is a significant step forward in improving local availability and supporting our key partners in Asia. Jason’s track record in driving innovation, his deep market knowledge and his commitment to customer success will be invaluable as we expand our footprint in this dynamic region.”
Chang said, “I’m excited to be part of the Hana RFID team, which is recognised in the market as both a key player and a trusted partner for an ever-growing network of label converters, service bureaus and system integrators. I look forward to working alongside our partners in Asia to deliver innovative solutions and exceptional service.”
Ralson Tire North America Expands Leadership Team
- By TT News
- August 21, 2025
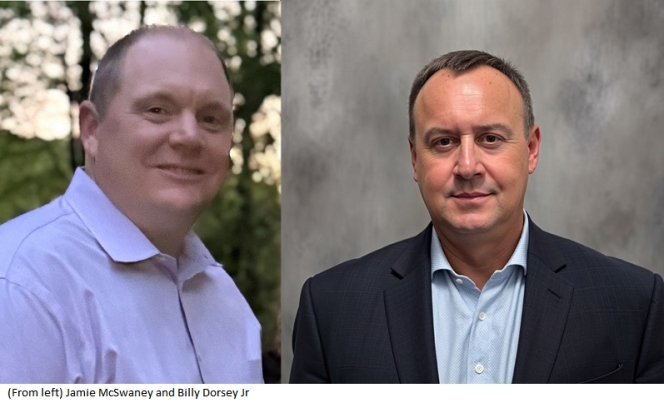
Ralson Tire North America (RTNA) has expanded its leadership team with the appointment of two seasoned tyre industry professionals.
As per the new development, Billy Dorsey Jr has been appointed as Vice President of Sales – South and Jamie McSwaney has been appointed as Vice President of Sales – North. Both the new appointments bring a combined 45 years of tyre industry experience to the company.
Brian Sheehey, President, RTNA, said, “These additions signal our unwavering commitment to accelerating Ralson’s growth in the US and Canada. We’re building a leadership team that knows how to compete, win and deliver results. Their deep industry relationships and ability to execute will be instrumental as we continue to grow our footprint in the North American trucking industry.”
Nordic Market Will Fare Well For Premium Tyres: Citira
- By Gaurav Nandi
- August 21, 2025
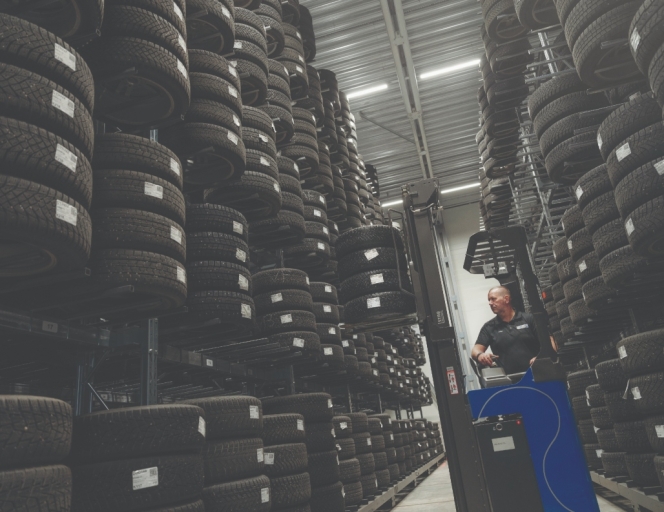
Scandinavian tyre service provider Citira sees robust potential for premium tyres in the Nordic region, driven by seasonal demands and safety priorities. CEO David Boman highlights that premium tyres including Pirelli’s offerings hold a significant share in passenger car, light truck and truck tyre segments supported by harsh winter conditions that emphasise performance and reliability. Despite a slight recent decline amid broader economic pressures and rising price sensitivity, premium brands remain relevant. Citira’s new long-term partnership with Pirelli and acquisition of Dackia AB aims to consolidate and optimise premium tyre distribution across Sweden.
Scandinavian tyre service company Citira recently told Tyre Trends that Nordic countries have excellent potential for premium tyres during a discussion over its partnership with Italian tyre major Pirelli.
Speaking on the market potential, Chief Executive Officer David Boman said, “When it comes to the Nordic markets, Scandinavia in particular has a relatively high share of premium tyres across categories including passenger car, light truck and TBR segments. Compared to other global regions, the demand for premium tyres here is notably strong.
“One of the main reasons for this is the seasonal nature of our market. Winter tyres, in particular, drive a more premium-oriented approach because of the need for high performance and safety under harsh conditions. While we’ve observed a slight decline in the premium tyre share over the past few years, it still holds a significant portion of the market. This demand is closely tied to seasonal safety concerns, especially in winter, autumn and early spring. Drivers here prioritise safety and reliability, which naturally supports the continued relevance of premium brands like Pirelli.”
He noted that the decline is likely tied to broader financial challenges in the market, especially following the Covid period. Both consumers and companies have become more price-sensitive, making cost a bigger factor in purchase decisions.
As a result, there’s been a gradual increase in demand for lower-cost, imported non-European tyre brands, while the market share of European premium tyre brands has slightly decreased.
Pirelli and Citira have entered a long-term strategic partnership aimed at enhancing their market presence in Sweden. As part of the deal, Citira will acquire Dackia AB that has a network of 102 retail outlets from Pirelli.
In return, Pirelli and Dackia have signed a supply agreement extending to 2030, ensuring Pirelli remains the main tyre supplier. The transaction, pending regulatory approval, is expected to close by 2025. The partnership will boost Pirelli’s distribution and market coverage while supporting Citira’s goal of expanding a sustainable, flexible and high-quality customer service network.
THE PACT
Citira currently runs over 50 tyre shops and over five retreading units across Scandinavia and Poland. “Citira is actively working towards creating a more efficient and consolidated tyre market. While our current focus is primarily on the Scandinavian region, it’s not out of the question that we may consider expanding beyond this geographic perimeter in the future. This agreement is part of a broader industry trend where partnerships and acquisitions are used to enhance efficiency, strengthen distribution networks and provide end customers with better service coverage,” revealed Boman.
Nonetheless, the deal specifically pertains to the Swedish market, and as part of the regulatory process, Citira has conducted a market analysis to understand the potential implications on market share. However, the specifics of that study were said to be confidential and could not be disclosed prior to the official closing of the deal.
Explaining how this partnership will influence the supply chain of premium tyre in the Nordics, Boman said, “We do anticipate some changes, particularly within Citira. We operate a number of logistics centres, and this partnership presents an opportunity to optimise our overall supply chain setup. Enhancing logistics will be a key enabler of better service and responsiveness in premium tyre distribution.”
He added, “This particular deal is unlikely to have a direct or immediate impact on independent retailers or smaller distributors. More broadly, the Scandinavian tyre retail sector is undergoing consolidation. Several players are actively reshaping the competitive landscape and that trend could gradually influence the positioning of independents. But again, this specific acquisition is not a disruptive event in that context.”
Alluding to the current demand for replacement tyres, he said, “In general, the tyre market has proven to be quite non-cyclical. Even in challenging economic conditions, it tends to remain stable. That said, I believe we’re entering a phase where circularity and life-extension solutions will gain more momentum. We’re likely to see increased focus on services that extend tyre life, especially for larger fleets. This shift won’t just be driven by cost or fleet uptime concerns but increasingly by environmental responsibilities.”
THE BUSINESS
According to Boman, Pirelli represents a very minimal share of Citira’s overall sales, currently. However, the strategic partnership mainly revolves around Dackia and Pirelli, and the former is intended to become part of the Citira Group. “Moving forward, there is definitely an opportunity to deepen the collaboration with Pirelli and potentially grow their share within our overall brand mix,” added Boman.
Citira currently follows a multi-brand strategy and will continue with it even after closing of the deal. Besides, it is also involved in process and sales of retreaded TBR tyres and wheel rims.
“We operate a facility in Poland where we refurbish truck and bus rims. The process involves media blasting and repainting the rims to restore its appearance and functionality. The logic behind it is quite similar to retreading. In most cases, the structural integrity of the rim is still intact; it’s just the surface or aesthetics that degrade over time. By restoring these rims, we’re able to extend the life and reduce waste,” said Boman.
The company operates five retreading facilities collectively, located in Finland, Sweden and Poland. It uses both hot-cure and cold-cure retreading methods. Hot-cure is used in Poland and cold retreading in Finland and Sweden. Annually, it retreads around 160,000 tyres, averaging about 13,000 per month. While its current focus is on retreading, Citira is actively exploring expansion into tyre recycling as part of a broader push towards sustainability and circularity.
The company also manages tyre distribution for fleets across countries. Its circular tyre distribution approach involves not only delivering new tyres to customers but also collecting used tyre casings from them. These casings are then sent back to its retreading facilities, creating a closed-loop system. Besides, Citira has different suppliers across Europe for sourcing tyres for retreading.
MARKET WATCH
Citira sees a strong willingness in the market for consolidation and it has already engaged in several partnerships. Commenting on market challenges, Boman said, “One key challenge is the need for a player capable of driving consolidation at a larger scale. In the Scandinavian markets, this kind of brand-independent consolidation hasn’t really taken place over the last 10 to 15 years. Previously, consolidation efforts were primarily led by tyre manufacturers or affiliate networks players. However, consolidation has largely been on hold recently, leaving space for an independent actor to step in. We see that opportunity clearly and believe it is well received both by other market participants and customers. The challenge lies in successfully executing this consolidation while maintaining trust and delivering value across a diverse market.”
Commenting on the demand for retreading, he said, “The Scandinavian market has a long tradition of retreading heavy vehicle tyres. Currently, there is a growing shift towards pay-per-kilometre or tyre-as-a-service models, especially among large fleets like bus companies and hauliers. Notably, public tenders increasingly require a certain share of retreaded tyres, reflecting a strong environmental focus. Retreading extends the life of a tyre by reusing about 70 percent of its original material, making it a significant sustainability tool. The market share of retreaded tyres is gradually increasing with expectations that the retread market will grow faster than the new tyre market in the coming years.”
“The main challenges for the retreading industry lie in overcoming the longstanding perception that retreaded tyres are merely a low-cost option rather than an environmentally friendly and sustainable product. This is mostly prevalent is Scandinavia and it is crucial to shift this mindset by educating customers and the broader market about the true benefits of retreading. Moving away from a purely price-driven sales approach to one that highlights quality, durability and positive environmental impact remains a significant hurdle for the industry,” he added.
Comments (0)
ADD COMMENT