Lowering Costs And Changing Testing Parameters With Advanced Systems
- By Sharad Matade
- April 17, 2025
The tyre industry is navigating a complex landscape of rising material costs, geopolitical uncertainties and fierce competition. In response, manufacturers are turning to automation, Industry 4.0 and AI-driven solutions to enhance efficiency and reduce operational expenses. Advanced testing and measurement systems are pivotal in this transition, offering cost-effective quality control, streamlined production and improved consistency. However, integrating these innovations poses challenges, including adapting to evolving tyre designs and meeting stricter OEM requirements. This article explores how technological advancements in tyre testing are reshaping the industry, ensuring performance precision and economic viability in an increasingly competitive market.
Increasing raw material prices, geopolitical crises, rising freight costs and stronger competition have led tyre companies to find ways to lower operational costs. Technological breakthroughs like automation, Industry 4.0, etc. are a boon in disguise in this hour of need. While automation is not a new concept, its usage gradually increases within the tyre industry, riding on the back of other advancements.
Micro-Poise Measurement Systems Division Vice President & Chief Technology Officer Dr Shaun M Immel believes that the ever-increasing need for automation and data connectivity to support Industry 4.0 is driving tyre manufacturers to adopt advanced measurement systems that lower inspection costs, enhance consistency and provide critical data for analytics.
“Simultaneously, manufacturers seek improved equipment throughput while maintaining high measurement quality to meet tightening tyre screening requirements. The growing variety of electric vehicle (EV) tyre designs necessitates greater measurement system flexibility to support a larger number of stock-keeping units (SKUs). Additionally, customers increasingly require user-friendly systems that accommodate inexperienced personnel by presenting simple-to-use and highly automated products,” he added while speaking exclusively to Tyre Trends.
The tyre testing industry has significantly transformed over the past five years. Automation cuts measurement and inspection costs while improving consistency and predictability, allowing manufacturers to redeploy labour to higher-value tasks. It also enables precise, data-driven decision-making by replacing subjective human evaluations with quantifiable metrics, ensuring better process control and continuous improvement.
As tyres grow larger and heavier, automation presents new challenges, but advancements in artificial intelligence (AI), faster processing power and GPU technology are making implementation more feasible and cost-effective. These innovations are fuelling a resurgence in automation, enhancing efficiency and providing manufacturers with deeper insights into production quality and performance.
However, he noted that while including sustainable materials within tyre compounds is strong founded within tyre makers, it is not likely to affect testing strongly. “The shift towards sustainable materials in tyre manufacturing is reshaping the industry. While this evolution may impact tyre design materials and manufacturing processes, it will not significantly alter the core processes of final finish testing. Testing equipment focuses on force variation, dynamic balance, X-ray analysis and geometry measurement, and it remains largely unaffected as long as tyre sizes stay within standard categories. However, as manufacturers integrate new compounds and materials, potential changes in tyre behaviour may lead to adjustments in testing methodologies to address emerging manufacturing challenges,” said Dr Immel.
PARADIGM EVOLUTION
The tyre industry is undergoing a strategic shift. Top-tier manufacturers are moving away from mass production to focus on high-performance and premium tyres, consolidating production into specialised plants for passenger, truck and OTR tyres. This shift is driven by increasing competition from Asian manufacturers dominating the mass-market segment. At the same time, some Asian players are pushing into the premium space, intensifying competition at the high end.
This evolving landscape reinforces the demand for precision testing, high measurement quality and faster throughput. “Our longstanding partnerships with tier-one manufacturers position us well in this premium market, particularly in the 18-inch-and-above segment, where measurement accuracy and reliability are critical and where Micro-Poise’s measurement systems excel. As the industry diversifies, we continue to enhance our equipment’s flexibility and feature set to meet the evolving needs of both established premium brands and emerging challengers,” said Dr Immel.
Furthermore, Dr Immel noted that the testing industry is undergoing significant advancements with a strong focus on increasing throughput while meeting increasingly stringent quality requirements. “Tyre manufacturers face tightening OEM screening limits, necessitating greater accuracy and repeatability in measurement systems to ensure precise and proper classification of tyres for various markets. Traditionally, higher throughput and improved measurement repeatability are a trade-off, but the industry is now working to improve both simultaneously, requiring innovative approaches,” he said.
“A notable shift, particularly influenced by EVs, is the growing demand for higher frequency content in geometry and uniformity measurements. As EVs eliminate engine noise, tyres have become the dominant source of road noise, prompting manufacturers to analyse higher-frequency variations that could contribute to unwanted sound. These variations, often linked to tread design and tyre construction, are now being examined more closely for tyre-to-tyre variation to mitigate its impact,” he added.
He also contended that regulatory trends and market dynamics are driving further changes beyond noise control. The rise of EVs has significantly expanded the number of SKUs manufacturers must manage, pushing the need for greater equipment flexibility and quicker changeover.
“With tyre designs evolving rapidly, testing systems must adapt through quick-change tooling and advanced marking capabilities to accommodate frequent model shifts. At the same time, manufacturers continue to push for higher throughput without compromising measurement and inspection performance, reinforcing the need for cutting-edge solutions that balance speed, accuracy and adaptability in an increasingly complex landscape,” he added.
MEASURING PARAMETERS
According to Dr Immel, the time required to measure and assess a single tyre depends on the type of test(s) being conducted. A typical measurement cycle may range between 15 and 30 seconds, depending on the tyre size, the required tyre ‘warmup’ time, and the measurements being performed. The key to high-quality final finish equipment is to ensure high throughput while maintaining the measurement performance necessary for accurate quality assessments.
Explaining the quality measurement process, he said, “Quality measurement in tyre testing hinges on two fundamental aspects, accuracy and repeatability. Accuracy refers to each measurement’s ability to reflect the tyre’s true assessment value and characteristics, a non-trivial task given the inherent variability in production tyre measurement. Manufacturers rely on these values to determine whether a tyre meets quality standards or should be scrapped.”
Repeatability, on the other hand, measures measurement consistency. Sophisticated technology minimises measurement variations of production tyres, ensuring that the system can effectively differentiate between acceptable and defective products. The financial impact of incorrect classifications, whether approving a faulty tyre or rejecting a good one, is substantial, making excellent system measurement performance a critical factor in reducing long-term operational costs.
Answering what tyre screening limits are acceptable to the market, he said, “The acceptable limits are proprietary to each tyre manufacturer. Each manufacturer receives screening limits from original equipment (OE) manufacturers and select replacement market dealers. These OE and replacement screening limits vary across players. Beyond that, tyre companies often impose stricter internal limits to enhance quality, improve customer perception or differentiate products.”
Alluding to whether the industry is more concerned about variation in passenger car tyres than in TBR or OTR tyres, he explained, “The industry is indeed more focused on variations in PCR, but I believe that’s largely due to volume. Passenger car tyres are produced in significantly higher numbers, and since they are consumer-facing products, expectations are much higher. People notice and care about ride quality, so manufacturers focus heavily on minimising tyre-to-tyre variations.”
“However, even in the TBR segment, certain types like steer and drive tyres undergo strict testing and must meet high standards. Steer tyres, in particular, incorporate advanced technology because they directly impact vehicle handling and safety. Trailer tyres, on the other hand, face less scrutiny since they directly affect ride comfort. That said, manufacturers across all segments are under continuous pressure to tighten tolerances. OEMs and fleet operators are always pushing for lower limits, forcing tyre makers to improve,” he added.
The company is advancing tyre grading technology with a data-driven approach that moves beyond traditional tyre metrics. Developing and integrating alternative measurements aims to refine performance assessments, ensuring a closer correlation between lab results and real-world ride quality. This shift could boost product yields while maintaining more stringent standards, enabling a ‘smarter’ assessment of tyre quality.
When asked about the causes of early tyre failure and how geometry plays a role in identifying defects, he explained that issues in ply splicing during manufacturing can lead to structural weaknesses. If the ply material splice is left open, missing ply cords create a bulge defect when the tyre is inflated under high pressure.
This bulge, a critical measurement in quality control, appears radially along the sidewall and is a standard defect monitored by tyre manufacturers. If the bulge exceeds acceptable limits, it can cause the inner liner to become voided, leading to slow air loss and deflation – an irreparable but not necessarily catastrophic failure mode.
Dr Immel also noted that the company has developed several features to enhance flexibility. “We have an automatic rim change feature with adaptable tooling that streamlines adjustments. We’re also exploring innovations to improve changeover efficiency further. One of our key advantages is that when a tyre enters the system – even if it’s a single unit – we can immediately identify it, load the correct parameters and process it without any cycle time penalty. Unlike other machines requiring manual adjustments and extra cycle time, ours can handle small lot sizes and frequent model changes seamlessly,” informed Dr Immel.
When asked whether every tyre produced on the line is measured, Dr Immel explained that almost all OE tyres undergo screening to meet strict screening limits. For the replacement market, tyre manufacturers screen a varying percentage of products, depending on customer requirements and market strategy. While nearly 100 percent of OE tyres is tested, the extent of screening for replacement tyres varies across manufacturers and customers.
PRODUCT CATALOGUE
Micro-Poise Measuring Systems’ ASTEC FX system evaluates critical parameters such as force variation, while Micro-Poise’s TGIS FS system evaluates tyre runout and sidewall appearance. While these factors primarily influence ride comfort rather than direct safety, they play a role in detecting defects that could lead to premature tyre failure. “Some of these defects have been monitored for decades, forming an industry benchmark,” noted Dr Immel.
When discussing the process of force variation measurement, the executive compared a tyre to a system of parallel springs, where each section should ideally have the same spring constant or stiffness around the tyre. However, variations in manufacturing such as splices, component alignments and positioning errors can create inconsistencies, making certain areas stiffer or softer than others, resulting in a variation of the force the tyre induces into a vehicle while driving.
A load wheel presses into the tyres while it rotates to detect these variations, measuring force fluctuations. Higher force readings indicate stiffer areas, while lower ones suggest softer regions. This data is analysed using Fourier analysis, breaking it down into harmonics to help manufacturers ensure that force variation at certain frequencies remains within acceptable limits.
The US-headquartered company’s ITMS FX (Integrated Tire Measurement System) minimises testing cycle times while integrating and maintaining excellent measurement quality across force variation, dynamic balance and geometry measurements. In high-volume manufacturing, any cycle time advantage can significantly impact overall throughput, driving up the overall equipment value for the customer. “It’s always about how fast you can get the process done – get one tyre out, bring the next in and repeat,” Dr Immel explained.
Beyond speed, system reliability is equally important. Fully automated testing systems need to run continuously with minimal stoppages. “If a fault occurs, recovery must be instant,” he added. However, increasing speed without sacrificing measurement quality presents an inherent challenge.
The company’s Tire Geometry Inspection System (TGIS FS) integrates proprietary tyre-optimised 3D sensors to inspect sidewall geometry accurately. The system employs three strategically placed sensors in fixed locations – one each on the top lateral, radial and bottom lateral surfaces – to complete a full geometric scan in a single tyre revolution. The result is a micron-resolution contour of the entire tyre. This data supports defect detection, dimensional measurements and process optimisation. The system is adaptable across Micro-Poise’s force variation (uniformity), dynamic balance machines and various competitive equipment.
The company is reinforcing its position as the ‘automation partner of choice’ for tyre manufacturers, supported by the fact that it has always focused exclusively on final finish solutions. The company is driving towards fully automated ‘Lights Out’ operations, ensuring maximum efficiency and cost-effectiveness across all its products.
Key advancements include revolutionary throughput enhancements that significantly improve final finish processes without adding costs, ease-of-use innovations that simplify complex systems for less experienced operators and increased flexibility through automated changeovers to address the growing number of SKUs in tyre production.
Additionally, it is advancing automated inspection and defect detection by helping its customers shift from manual to autonomous inspection, which encompasses more precise numerical measurements, reduced errors and a reduction in overall inspection costs.
A major breakthrough in this area is the integration of AI and deep learning (DL) into its Coll-Tech Automatic Defect Recognition (ADR) software for tyre X-ray image analysis. Showcased at the 2024 Tire Tech Expo, the latest advancements have dramatically improved defect detection accuracy and responsiveness to customer configuration and customisation requests.
“Previously, algorithmic versions required extended response times for adaptation and modification, but the AI-driven enhancements have eliminated this delay. Multiple manufacturing facilities are now operating their ADR-equipped X-ray systems without human inspectors, allowing personnel to be redeployed elsewhere while significantly reducing inspection expenses. The transition to full autonomous inspection is a learning process that requires adaptation, but the investment yields substantial positive financial returns. Micro-Poise’s ADR system allows our customers to control the pace and number of steps in the journey to full autonomous inspection. To facilitate adoption, we offer image evaluations, follow-up consultations and in-plant demonstrations,” said Dr Immel.
Beyond inspection advancements, Micro-Poise has also improved tyre grinding systems, enhancing both functional system performance and the visual appearance of ground tyres.
Historically, tyre grinding – used for force variation and geometry optimisation – has been instrumental in converting rejected tyres into OE-grade products. However, some manufacturers hesitate to adopt grinding due to concerns about visible grind marks. Micro-Poise has addressed these concerns by refining the grind appearance and adding new functionalities that turn tyre grinding from an art into a precise science. These innovations increase product yield, improve tyre grading and deliver a strong return on investment for manufacturers. With AI-driven defect detection, automation advancements and improved tyre yield solutions, Micro-Poise is setting new standards for efficiency, accuracy and cost savings in the final finish stage of tyre manufacturing.
The company continuously refines its technology, balancing cost efficiency with high performance. “Customers request additional features based on unique measurement methodologies and defect detection requirements,” Dr Immel said.
Customers expect the machines to operate for decades. Mechanically, the company’s systems are built for longevity, but electronics and software evolve much faster. To address obsolescence, the company offers modular control system upgrades bundled with new features, ensuring customers gain added value while modernising their equipment and extending its lifecycle.
In the context of retrofitting, Dr Immel said, “We design machines to accommodate sensor and measurement upgrades, enabling customers to integrate new parameters without replacing entire systems. The balance lies in designing robust mechanical structures while allowing flexibility in electronics and software.”
ADDRESSING CHALLENGES
Developing intuitive, easy-to-use machines is an ongoing challenge. “Simplifying a machine while maintaining its capabilities is often harder than designing a complex system,” Dr Immel noted.
The company has invested in UX/UI enhancements to improve operator efficiency and ease of use.
Furthermore, the tyre industry is currently facing one of its most dynamic and challenging periods, driven by rapid technological advancements, shifting regulations, sustainability initiatives and the rise of EVs.
One of the biggest challenges is aligning new technologies with practical applications that benefit customers while ensuring their confidence in these innovations. AI and automation, for example, are transforming manufacturing processes, but their complexity can be daunting for tyre producers who must navigate ever-changing market demands.
Additionally, external factors such as tariffs, trade wars and regulatory changes add another layer of uncertainty, making it critical to choose the right technologies that will bring long-term value.
Sustainability is another key concern as tyre manufacturers work to reduce environmental impact through raw material innovations, renewable energy adoption and energy-efficient manufacturing processes.
While the company does not directly influence the chemical composition of tyres, it contributes to sustainability by designing testing and measurement equipment that uses less energy and air.
With AI-driven automation, faster cycle times and a strong focus on usability and upgradeability, it continues to push the boundaries of tyre testing technology. As the industry embraces data-driven solutions, the company remains at the forefront of precision measurement and defect detection.
FUTURE FOCUS
The industry is undoubtedly shifting towards fundamental measurement improvements and enhanced features like predictive maintenance, retrofitment and software upgrades.
“While reducing testing time and improving efficiency remain core priorities, there is an increasing demand for smart, automated solutions that can provide deeper insights into machine performance. Predictive maintenance is an exciting development area, but it is still in its early stages. The ultimate vision is to have intelligent software capable of real-time monitoring systems and predicting failures with precision. However, before reaching that stage, the focus is on establishing a solid data foundation and ensuring rapid recovery when issues arise,” averred Dr Immel.
To address these challenges, the industry is exploring soft sensor technology as a potential alternative to expensive hardware-based monitoring systems. These advancements could reduce reliance on physical sensors while still enabling predictive maintenance capabilities. As the industry moves forward, manufacturers must balance cost, efficiency and long-term viability to maximise the benefits of these innovations.
“The integration of AI and DL technologies is poised to continue, though adoption will likely be measured as manufacturers proceed with caution. While some advancements will prove transformative, others may fade over time. AI-driven systems can significantly improve productivity by shortening design and improvement cycles, making processes more efficient. Additionally, AI models can refine their accuracy over time through continuous feedback and training, leading to smarter and more effective applications in manufacturing,” he added.
He also noted that one key concern is the potential burden on customers. Some AI implementations risk shifting performance optimisation responsibilities such as defect evaluation, labelling and training onto end users. While this may be expected in later stages of adoption, it presents a significant challenge in the early phases, making seamless integration into existing workflows critical.
Another significant area of advancement is tyre grinding technology. While some manufacturers hesitate to use grinding due to concerns over visual imperfections, it remains a valuable and financially beneficial process for refining tyres that exceed variation limits.
Recent innovations aim to standardise and automate grinding, transforming it from an art into a precise, science-driven method. These advancements make the process more efficient and user-friendly, ensuring higher-quality output without compromising visual appearance. n
Micro-Poise TGIS FS Geometry Sensor
Anshuman Singhania Honoured As CEO of the Year At National Management Summit
- By TT News
- August 25, 2025
Anshuman Singhania, Managing Director of JK Tyre & Industries, has been awarded the 'CEO of the Year' by the Top Rankers Management Club. The accolade was presented at the 25th National Management Summit, held in New Delhi on 23 August 2025.
The award recognises Singhania’s exceptional leadership and strategic vision, which have been pivotal in steering the company toward sustained growth and innovation. Under his guidance, JK Tyre has reinforced its position as a leader in radial tyre technology, expanded its global presence and strengthened its dedication to sustainability and customer focus.
In his acceptance speech, Singhania expressed his gratitude, stating, “I am honoured to receive this recognition from the Top Rankers Management Club. This award reflects the collective commitment of the entire JK Tyre team, whose efforts continue to drive our progress. I would like to thank my colleagues, industry partners and stakeholders for their unwavering support in our journey of growth and transformation.”
He has been a key figure in modernising the company, leveraging new technologies and expanding its presence in both domestic and international markets. The 'CEO of the Year' award, presented by the Top Rankers Management Club, celebrates leaders who demonstrate a clear vision for organisational excellence and industry transformation.
Hana RFID Appoints Jason Chang As New Asia Sales Director
- By TT News
- August 21, 2025
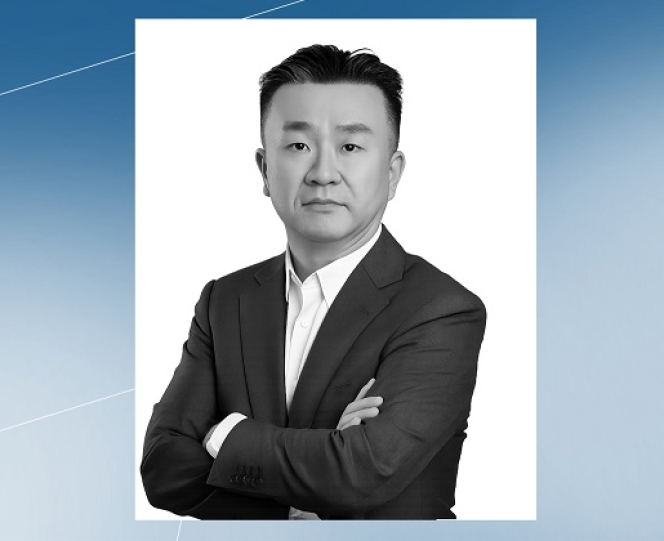
Hana Technologies, Inc. (Hana RFID) has strengthened its leadership in the Asian market with the appointment of industry veteran Jason Chang as Sales Director for Asia. Based in Shanghai, he will be responsible for managing key customer relationships and driving strategic growth throughout the region.
Chang brings a wealth of relevant experience to the role, with over 15 years in the RFID sector following a successful career in IT. His proven track record includes significant tenures at leading firms like Xerafy, Stora Enso and Beontag. His accomplishments range from pioneering the development of innovative flexible anti-metal tags to launching groundbreaking RFID-based retail solutions that gained widespread adoption in China and Europe. He has also demonstrated a strong capacity for growth, most recently achieving remarkable business expansion in the APAC market.
This appointment is a strategic milestone for Hana RFID, underscoring its commitment to supporting global customers with high-performance technology and expert, on-the-ground leadership. This move highlights Hana RFID's focused strategy on deepening its regional support and providing partners with sophisticated RAIN RFID inlay and embeddable tag solutions, backed by local expertise.
Mike Hetric, Senior Vice President – Sales & Marketing, Hana RFID, said, “The appointment of Jason Chang is a significant step forward in improving local availability and supporting our key partners in Asia. Jason’s track record in driving innovation, his deep market knowledge and his commitment to customer success will be invaluable as we expand our footprint in this dynamic region.”
Chang said, “I’m excited to be part of the Hana RFID team, which is recognised in the market as both a key player and a trusted partner for an ever-growing network of label converters, service bureaus and system integrators. I look forward to working alongside our partners in Asia to deliver innovative solutions and exceptional service.”
Ralson Tire North America Expands Leadership Team
- By TT News
- August 21, 2025
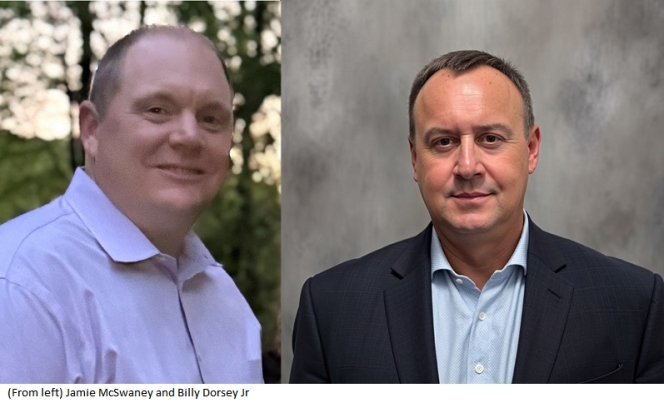
Ralson Tire North America (RTNA) has expanded its leadership team with the appointment of two seasoned tyre industry professionals.
As per the new development, Billy Dorsey Jr has been appointed as Vice President of Sales – South and Jamie McSwaney has been appointed as Vice President of Sales – North. Both the new appointments bring a combined 45 years of tyre industry experience to the company.
Brian Sheehey, President, RTNA, said, “These additions signal our unwavering commitment to accelerating Ralson’s growth in the US and Canada. We’re building a leadership team that knows how to compete, win and deliver results. Their deep industry relationships and ability to execute will be instrumental as we continue to grow our footprint in the North American trucking industry.”
Nordic Market Will Fare Well For Premium Tyres: Citira
- By Gaurav Nandi
- August 21, 2025
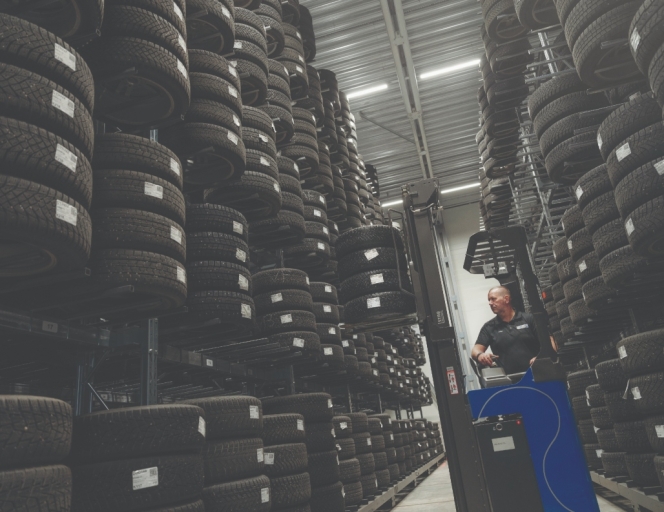
Scandinavian tyre service provider Citira sees robust potential for premium tyres in the Nordic region, driven by seasonal demands and safety priorities. CEO David Boman highlights that premium tyres including Pirelli’s offerings hold a significant share in passenger car, light truck and truck tyre segments supported by harsh winter conditions that emphasise performance and reliability. Despite a slight recent decline amid broader economic pressures and rising price sensitivity, premium brands remain relevant. Citira’s new long-term partnership with Pirelli and acquisition of Dackia AB aims to consolidate and optimise premium tyre distribution across Sweden.
Scandinavian tyre service company Citira recently told Tyre Trends that Nordic countries have excellent potential for premium tyres during a discussion over its partnership with Italian tyre major Pirelli.
Speaking on the market potential, Chief Executive Officer David Boman said, “When it comes to the Nordic markets, Scandinavia in particular has a relatively high share of premium tyres across categories including passenger car, light truck and TBR segments. Compared to other global regions, the demand for premium tyres here is notably strong.
“One of the main reasons for this is the seasonal nature of our market. Winter tyres, in particular, drive a more premium-oriented approach because of the need for high performance and safety under harsh conditions. While we’ve observed a slight decline in the premium tyre share over the past few years, it still holds a significant portion of the market. This demand is closely tied to seasonal safety concerns, especially in winter, autumn and early spring. Drivers here prioritise safety and reliability, which naturally supports the continued relevance of premium brands like Pirelli.”
He noted that the decline is likely tied to broader financial challenges in the market, especially following the Covid period. Both consumers and companies have become more price-sensitive, making cost a bigger factor in purchase decisions.
As a result, there’s been a gradual increase in demand for lower-cost, imported non-European tyre brands, while the market share of European premium tyre brands has slightly decreased.
Pirelli and Citira have entered a long-term strategic partnership aimed at enhancing their market presence in Sweden. As part of the deal, Citira will acquire Dackia AB that has a network of 102 retail outlets from Pirelli.
In return, Pirelli and Dackia have signed a supply agreement extending to 2030, ensuring Pirelli remains the main tyre supplier. The transaction, pending regulatory approval, is expected to close by 2025. The partnership will boost Pirelli’s distribution and market coverage while supporting Citira’s goal of expanding a sustainable, flexible and high-quality customer service network.
THE PACT
Citira currently runs over 50 tyre shops and over five retreading units across Scandinavia and Poland. “Citira is actively working towards creating a more efficient and consolidated tyre market. While our current focus is primarily on the Scandinavian region, it’s not out of the question that we may consider expanding beyond this geographic perimeter in the future. This agreement is part of a broader industry trend where partnerships and acquisitions are used to enhance efficiency, strengthen distribution networks and provide end customers with better service coverage,” revealed Boman.
Nonetheless, the deal specifically pertains to the Swedish market, and as part of the regulatory process, Citira has conducted a market analysis to understand the potential implications on market share. However, the specifics of that study were said to be confidential and could not be disclosed prior to the official closing of the deal.
Explaining how this partnership will influence the supply chain of premium tyre in the Nordics, Boman said, “We do anticipate some changes, particularly within Citira. We operate a number of logistics centres, and this partnership presents an opportunity to optimise our overall supply chain setup. Enhancing logistics will be a key enabler of better service and responsiveness in premium tyre distribution.”
He added, “This particular deal is unlikely to have a direct or immediate impact on independent retailers or smaller distributors. More broadly, the Scandinavian tyre retail sector is undergoing consolidation. Several players are actively reshaping the competitive landscape and that trend could gradually influence the positioning of independents. But again, this specific acquisition is not a disruptive event in that context.”
Alluding to the current demand for replacement tyres, he said, “In general, the tyre market has proven to be quite non-cyclical. Even in challenging economic conditions, it tends to remain stable. That said, I believe we’re entering a phase where circularity and life-extension solutions will gain more momentum. We’re likely to see increased focus on services that extend tyre life, especially for larger fleets. This shift won’t just be driven by cost or fleet uptime concerns but increasingly by environmental responsibilities.”
THE BUSINESS
According to Boman, Pirelli represents a very minimal share of Citira’s overall sales, currently. However, the strategic partnership mainly revolves around Dackia and Pirelli, and the former is intended to become part of the Citira Group. “Moving forward, there is definitely an opportunity to deepen the collaboration with Pirelli and potentially grow their share within our overall brand mix,” added Boman.
Citira currently follows a multi-brand strategy and will continue with it even after closing of the deal. Besides, it is also involved in process and sales of retreaded TBR tyres and wheel rims.
“We operate a facility in Poland where we refurbish truck and bus rims. The process involves media blasting and repainting the rims to restore its appearance and functionality. The logic behind it is quite similar to retreading. In most cases, the structural integrity of the rim is still intact; it’s just the surface or aesthetics that degrade over time. By restoring these rims, we’re able to extend the life and reduce waste,” said Boman.
The company operates five retreading facilities collectively, located in Finland, Sweden and Poland. It uses both hot-cure and cold-cure retreading methods. Hot-cure is used in Poland and cold retreading in Finland and Sweden. Annually, it retreads around 160,000 tyres, averaging about 13,000 per month. While its current focus is on retreading, Citira is actively exploring expansion into tyre recycling as part of a broader push towards sustainability and circularity.
The company also manages tyre distribution for fleets across countries. Its circular tyre distribution approach involves not only delivering new tyres to customers but also collecting used tyre casings from them. These casings are then sent back to its retreading facilities, creating a closed-loop system. Besides, Citira has different suppliers across Europe for sourcing tyres for retreading.
MARKET WATCH
Citira sees a strong willingness in the market for consolidation and it has already engaged in several partnerships. Commenting on market challenges, Boman said, “One key challenge is the need for a player capable of driving consolidation at a larger scale. In the Scandinavian markets, this kind of brand-independent consolidation hasn’t really taken place over the last 10 to 15 years. Previously, consolidation efforts were primarily led by tyre manufacturers or affiliate networks players. However, consolidation has largely been on hold recently, leaving space for an independent actor to step in. We see that opportunity clearly and believe it is well received both by other market participants and customers. The challenge lies in successfully executing this consolidation while maintaining trust and delivering value across a diverse market.”
Commenting on the demand for retreading, he said, “The Scandinavian market has a long tradition of retreading heavy vehicle tyres. Currently, there is a growing shift towards pay-per-kilometre or tyre-as-a-service models, especially among large fleets like bus companies and hauliers. Notably, public tenders increasingly require a certain share of retreaded tyres, reflecting a strong environmental focus. Retreading extends the life of a tyre by reusing about 70 percent of its original material, making it a significant sustainability tool. The market share of retreaded tyres is gradually increasing with expectations that the retread market will grow faster than the new tyre market in the coming years.”
“The main challenges for the retreading industry lie in overcoming the longstanding perception that retreaded tyres are merely a low-cost option rather than an environmentally friendly and sustainable product. This is mostly prevalent is Scandinavia and it is crucial to shift this mindset by educating customers and the broader market about the true benefits of retreading. Moving away from a purely price-driven sales approach to one that highlights quality, durability and positive environmental impact remains a significant hurdle for the industry,” he added.
Comments (0)
ADD COMMENT