How To Get Maximum Benefit From Tyres: Commercial Fleet And Mining Operations
- By Ahmad Hidayat
- September 30, 2024
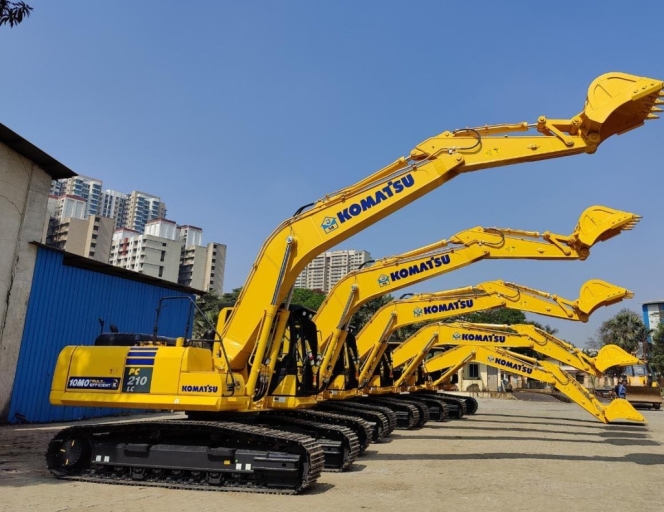
In human mobility, tyres are ‘the only contact between the vehicle and road’, to make people move from one point to another ‘safely’.
In land cargo transportation, they are the ‘work horse’ of the supply chain for any goods, whether industrial (raw material) or finished goods. In special applications such as mining, they are ‘mimicking’ pipelines in the oil and gas industry, such as piping where hydraulic pumps replaced by truck engines.
So tyres play a ‘critical role’ in transporting almost anything: ‘people and goods’ when we must deliver on land transport mode.
The challenges: Too many options
Its vital role is not questionable. But having that critical role doesn’t mean it’s easy to handle for the end user.
Why?
In the case of tyres, we know premium brands, regional brands and sometimes local brands. The classic question is: which one is the best?
For personal purposes (PCR), a decision could be made easily with the risk of losing a small amount of money. Simply fitting a tyre according to OEM standards will not be a big issue. The problem arises with fleet companies (trucking or bus) with tens, hundreds or even thousands of units of equipment.
Even riskier when it comes to OTR tyres, where prices can reach tens of dollars or more. It is not easy to pick which one is the best.
How to choose the most suitable tyre for operations?
In order to get the right choice, we must do the following:
1. Define performance indicators: Productivity or efficiency - Regarding commercial tyres (TB/AG/OTR/IND), performance is defined as productivity and efficiency. These two elements are sometimes aligned and sometimes contradictory.
Which one should be chosen?
It depends on the company’s goal or situation. We must optimise between those two so that it becomes ‘business decision’ and not a solely ‘tyre technical decision’. When productivity takes the lead compared to efficiency
One fleet of 120T giant trucks fitted with 27.00R49 has limitations due to the TKPH caused mainly by long distances, so the real site TKPH is quite high. It limits trucks operating cycles to only 6.5 per shift. It is only transporting coal at 120 T/cycle x 6 cycles = 720 T per shift, while the end user burns fuel without getting tonnage in return for a half cycle.
In this situation, the end user is not sensitive to efficiency; they are more sensitive to how to increase productivity.
When efficiency becomes the driver instead of productivity
The other situation is that coal transporters have problems with tyre costs due to inefficient tyre usage. The end user thinks they made a good choice using the 12.00R24 *** (three-star) rating. They expect a long life, but the outcome is the opposite. Testing was done with bias tyres (12.00-24), 18PR and 20PR. Comparison testing was done for six months, and in the end, we concluded bias tyres were more efficient than radial tyres.
The explanation for why bias tyres perform better than radial tyres comes from a pressure check done with 1,500 points of data show ‘intentional’ pressure reduction.
When it was discussed with site management and the driver, the driver told management that the hauling road was undulating, forcing them to reduce pressure. If they don’t reduce pressure, they will suffer from back pain.
So in terms of truck load, it is not overload, but in terms of tyres, it becomes overload due to low pressure. As bias tyres use nylon as the carcass, they have more resistance to fatigue, whereas radial tyres using steel cord have less resistance to fatigue and are more prone to premature failure.
The common sayings that radial is better than bias, premium is better than normal brand and thicker tread is better than shallow tread are more myths than realities. It all depends on the requirements coming from the field/ operations.
2. Optimise tyre life
The only way to do this is the end user doing an assessment of their requirements for each application, operating condition and site/road condition. This way, they could be able to build up the tyre requirements and externalise their requirement to get the most suitable tyre specification from whichever brand and whichever type of tyres.
With tyre OEMs mostly developing products for the most common applications, the potential performance is not necessarily the best performance on every site, independent of the brand, tyre type etc.
The best suggestion for the end user and OEMs
OEMs should start Co-Creation Value by having close communication from the beginning about actual customer requirements and focusing on creating the most suitable solution rather than the most common approach.
How it becomes practical If fleet truck customers have more than 1,000 trucks and mining customers have at least 100 giant trucks, they would like to have the most suitable product rather than the most common product for their application, as their tyre cost will be significant to gain their attention.
Meanwhile, for OEMs, it is worth to develop tyres with the most suitable solution and treat the customer as Key Account.
How to measure the benefits for each party
For the end user, the more suitable the tyre, the more optimum tyre performance they will have. For OEMs, the measurement is quite simple: calculating the potential life-time value (LTV) of a customer (estimate revenue generated from this customer) compared to the cost-time value (CTV) of the customer (the spending on developing products and maintaining relationship with the customer).
And if LTV/CTV > 1, it is an Attractive Customer. If the estimated LTV/CTV is not attractive enough to be handled, the OEM could focus on another customer.
Summary
- Tyre optimisation for end-user applications is a fair measure, and the actual performance indicator aligns with the temporary business objectives of the end-user that could change over time; one time it will be more productivity focused, the other time it may be efficiency focus.
- Democratisation and an open field for the whole OEM player that is not dogmatised as premium always being better, radial always being better or star rating always being better. It is merely how end-users could define their operational requirements and work together as cocreators with certain OEMs.
- It is not necessary for OEMs to chase all market segments; each OEM could choose where they will be more competitive than others. Meanwhile, for the end-user, they will get high-quality and reliable service from certain OEMs on their tyre usage.
Representational image courtesy: cebmumbai/Facebook
The author is an engineering expert in the mining and truck tyres field.
The column was first published in August-September 2023 issue of Tyre Trends.
Degrees In Sustainability
- By Adam Gosling
- July 08, 2025
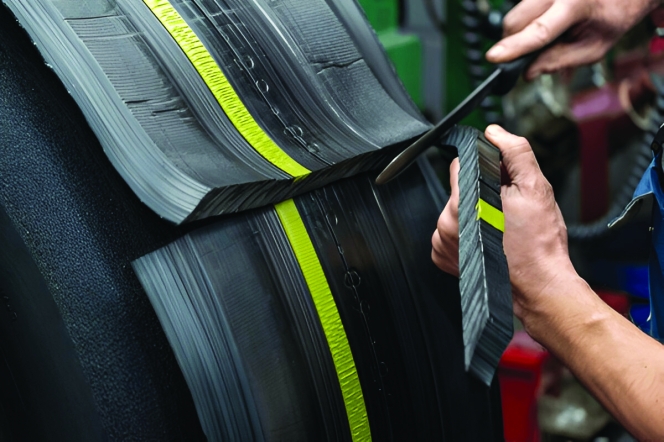
Raw materials and sustainability are symptomatic of a tyre when you think about it.
As a society very dependent upon mobility, our drivers and passengers need to be able to enjoy sustainable service from the tyres our industry produces. To date, primarily raw materials have been used in manufacturing, but there is a paradigm shift underway. The recyclability of tyres is as yet still a question more than a solution, from an economic perspective as well as an environmental approach.
As we are all observing, global economics is entering an interesting phase and hands are being outstretched looking for payment or retribution, or both.
The tiresome question in front of everyone is ‘what is the cost’?
a) Of not doing ‘it’
b) Of attempting to do ‘it’
c) Of being able to enjoy economic success to do ‘it’
d) Having positive outcomes for the environment or at least neutral
e) Option C as well as D, very hard to achieve this balance in my opinion, but nevertheless, is the most desired
The ‘it’ in this case is producing a tyre with no adverse effects or outcomes.
Tyre OEMs are progressing through the issue of designing tyre tread patterns as well as structural casing considerations (even down to acoustic considerations from inside the tyre’s air chamber) as the tyre in motion is now the largest noise generator (no engine or exhaust noise) on a current generation electric vehicle (EV). Having high levels of noise is part of modern life; however, as people, we don’t accept noise intrusion, especially inside the modern auto cocoon, sorry, car. How far do we push sustainability?
A tyre admirably demonstrates there can be reciprocity and sustainability between unlikely companions. Nominally, inflexible steel lives happily with totally flexible rubber whilst the road pavement (bound stone, cement or unsealed) abrades the tread rubber. From an unsustainable perspective, there are the tread road wear particulates (TRWP) that are generated at the tread pavement interface; huge questions here as the yet to be determined answers need to be found.
With more fuel-efficient propulsion systems, greater demands are placed on the humble tyre. Rolling resistance (of the tyre) is a major consumer of energy and now, not forgetting, aerodynamics too.
The global program of ‘safer vehicles’ also has impact on tyre performance not only on the overall life but also the traction / grip aspects. Vehicles that are heavier, faster and more responsive place increased demands on tyre performance.
WANTED: lighter, quieter, more grip in all conditions, longer life, greener, cheaper ... the holy grail.
There is a price to pay; as Isaac Newton stated, ‘to every action, there is always opposite and equal reaction’. This is a basic law of physics, the third law of motion. There is no free lunch; we usually pay in many ways, either in the short term, the medium or the long term, or in all terms.
Retreading is very much a partial solution using the casing of the tyre to yield second, third and more lives. Tyre OEMs have not favoured retreading in past times as for every tyre retreaded, a new virgin tyre was not required. Tyre manufacturing facilities operate on volume; the more they can produce, the lower the cost of each item. Selling more tyres was the only answer. Retreading has many benefits, and with modern electronics, the quality of the product can be as assured as a virgin tyre. In some cases, the performance of the retread can be superior to that of the original tyre. Retreading is a sustainable practise to a point. Eventually, the tyre’s structural casing will fatigue and fail. Commercial aviation tyres are retreaded numerous times as a matter of practise. An aircraft tyre will experience loads well in excess of that your daily drive tyre experiences. When the tread is worn down, it is replaced with a new tread package. The other very important consideration in regards tyre retreading is the reduction in the consumption of raw materials. A tyre is assembled using upwards of 40 percent carbon black. There is about 20 percent steel and fibre product whilst the rubber that converts to a petroleum oil during the pyrolysis process is the remainder. Every casing reused reduces the requirement for fresh raw materials and associated manufacturing.
Whilst recycling offers sustainability in a circular economy scheme, there is a long way to go before sustainability is actually sustainable. With increased recycling and the rise of the circular economy, past attitudes are being revised, modified, changed or rewritten. The prime hurdle to jump for this potentially emerging (recycling) industry is the refining of the end products tyre pyrolysis systems generate. The carbon black has many challenges before re-use for tyres. The oil also requires refining prior to replacing petroleum. What about the byproducts from the refining process? If the pyrolysis product is more expensive than the original raw material, will you as the consumer still buy cheap? If so, why are we, the tyre OEM s, investing in our ESG programme of sustainability?
Repurposing end-of-life tyres has great potential, but there are concerns around the outcomes if such products are used. Ground rubber used in uncaptured soft fall has been outlawed in some jurisdictions; even captured rubber such as in hot mix bitumen has outfalls (TRWP). Geological uses as ground support and river stream bank erosion mitigation are another limited use. The re-use of the raw materials is the ideal outcome, but sustainability is still a process in progress.
All processes are required to extract the highest outcomes from our raw materials as well now (with landfill diminishing capacity), thinking about end-of-life products (not just tyres, think about electronics, for instance, and the list grows), so there is a requirement to promote the recycling, re-purposing and retreading of tyres. The retreading facilities can be localised geographically to reduce the sea transport for virgin tyres from manufacturing facilities to the end destination. Pyrolysis and re-purposing facilities are best locally located, but there has to be a market for the downstream products; this is a crunch point. However, there are advantages that we are currently not availing ourselves of with the many economic benefits seemingly available. With export/import tariffs introduced or even if sea lanes are unable to be used to import/export tyres, then retreading capacity will be a license to print. There must be a strategic deliberation to include tyre retreading in national planning as well. Our mobile society requires tyres; from farm to plate, our food is supported by tyres for much of the journey, then there is the rest of life.
We should not underestimate the critical role tyres play in our global supply chains and mobility; however, the price we pay has to be sustainable in the long term. That means easing our demands on raw materials including the use of recycled products, but we also need to extract better performance not just from the tyres so much but also from the maintenance of the vehicles. In my overviewing large data sets of tyre life performance, it has been noted that ‘we’ use only about 65 to 70 percent of the available tread; many tyres are scrapped earlier than they should be as a result of irregular wear and/or poor maintenance. Considering the aids available today (namely drive over alignment pads, tyre pressure monitoring systems TPMS), there is little excuse for such dubious maintenance decisions stemming from sub-standard economic directions.
The old model of ‘produce more sell more’ has a large price to pay. Sustainability is now becoming a serious issue in our supply chains. We (businesses) have to be able to open the shop doors tomorrow, and that means generating capital reserves that enable us to pay the bills and put food on the table.
What price is sustainability? Are you prepared to pay today for tomorrow’s sake?
- Tyre
- rating
- sustainability
- RR EU
- natural rubber
- Tire Industry Project
- Global Platform for Sustainable Natural Rubber
- Forest Stewardship Council
- Continental
- Bridgestone
- Nokian Tyres
Sustainability… Innovations And Future Outlook
- By Ertugrul Bahan
- July 08, 2025
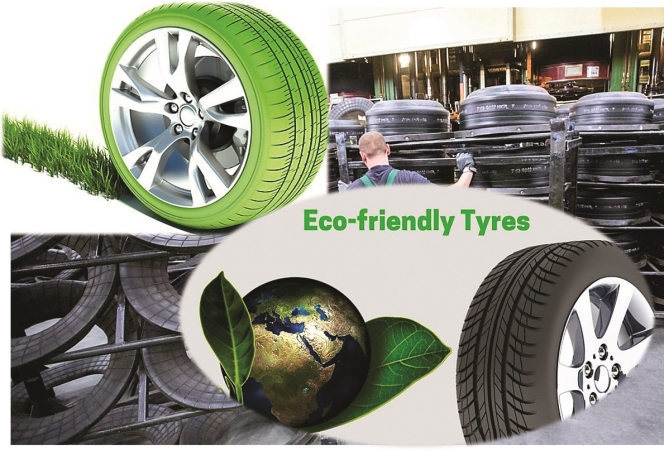
‘Sustainability Rating’ of vehicle tyres will be introduced as the ‘Recyclability Scoring’, i.e. will be more comprehensive than EU RR labelling rating
News, statements and trends from industry players indicate that the ‘Sustainability Rating’ for vehicle tyres will soon become the focus of discussion. This rating will be assessed based on the manufacturer’s carbon footprint, microplastics volume per abrasion percentage and the proportion of sustainable raw materials. In other word, it will be the `Recyclability Scoring` of the tyre itself and its manufacturer. In addition, the mass value of used tyres meanwhile will be assessed based on the sustainability rating of the ELT (end-of-life tyres). So that is why ‘Tire Passport’ label of tyres in the market is currently under regulatory discussion.
Meanwhile, used tyres will become more environmentally friendly in the near future, which will have a significant impact on the improvement of sustainability ratings of ‘end of life tyres’ in the market. The concept of ‘sustainability Rating’ may be a bittersweet experience for most industry players. It is for sure not the same meaning of having `A` grade RR EU labelling rating. However, once sustainability criteria are fully defined on regulatory basis, we should be ready to take a closer look at design, production and disposal requirements.
Tyres with a higher sustainability rating receive the highest rating, meaning they have the best carbon footprint. These tyres contribute more effectively to the carbon neutrality of the entire manufacturing industry due to their near-zero carbon footprint during the production phase.
Regulatory pressures impose tyres industry to radical changes, driven by various dynamics and developments as it traditionally depends heavily on non-renewable petroleum products and natural rubber from rubber trees, which contribute to deforestation.
A significant portion of global CO2 emissions are attributable to the tyre industry as it has long years of weak carbon neutrality and the negative offsetting capability of greenhouse gas emissions released into the atmosphere that should be avoided. Linking to this deficiency, regulatory pressures impose tyres industry to radical changes, driven by various dynamics and developments, including innovations in nanomaterials and the emergence of new environmentally friendly raw materials.
Traditional tyre production relies heavily on non-renewable petroleum products and natural rubber from rubber trees, which contribute to deforestation and resource depletion. The tyre industry has been contributing significantly to environmental pollution, resource depletion and waste accumulation up to now, but sustainable innovations can help reverse these impacts.
Natural rubber, the main material in the tyres industry, is responsible for the deforestation of approximately four million hectares of forest each year in Southeast Asia. Synthetic rubber relies on petroleum and soot emits three tonnes of CO₂ for every tonne of carbon produced. Tyre production releases zinc, lead and sulfur into waterways. New regulations require higher recycled content and stricter emissions standards. Present tyres mostly harm aquatic life and lead to fish mortality.
The tyre industry’s sustainable development momentum is rapidly evolving, driven by regulations, automotive imposements, material innovations and circular economy models.
Manufacturing emissions are significant. However, approximately 70 to 85 percent of a tyre’s total carbon footprint is generated during use but most of this part is unavoidable since tyre itself is a running phenomenon; friction and tractive base drag force is inevitable. So only limited part of it can be regained, but for achieving long-term savings over the tyre’s lifetime, any gain still is important for the total saving. This awareness has led to innovations in tyre design that reduce rolling resistance and improve fuel efficiency, thus delivering significant environmental benefits throughout the product life cycle.
Automakers are also on the line to force all parts manufacturers to compel and demand more environmentally friendly tyres to meet their own sustainability goals. Fleets and transportation companies are seeking fuel-efficient tyres to reduce their operating costs. Sustainable practices often lead to long-term savings through energy efficiency and waste reduction. On the other hand, environmentally conscious retail consumers increasingly prefer sustainable products.
Dandelion rubber is an organic alternative to conventional rubbers. However, some tyre manufacturers use drought-resistant guayule plantations. The attractive point is that some manufacturers already are producing tyres consisting of 50 percent sustainable bio-based raw materials, recycled rubber powder and reclaimed carbon black. Rice husk ash silica is an innovative material that replaces conventional silica, improving sustainability while utilising agricultural waste. Bio-based synthetic rubber is on the way as a source of bio-based material.
What challenges do remain? The transition to bio-based raw materials, recycling and smart tyres is irreversible. Stricter regulations such as bans on tyre wear microplastics and advances in bioengineering are expected to dominate the next decade while sustainability is now a key competitive advantage.
Tyre manufacturers are already working on retreading programmes, devulcanised rubber and pyrolysis outcomes such as rCB, oil and hydrogen – all to improve sustainability. Resource savings through virtual modelling and AI are underway.
Tyre manufacturers are already working on retreading programmes, devulcanised rubber and pyrolysis outcomes such as rCB, oil and hydrogen – all to improve sustainability. Resource savings through virtual modelling and AI are underway.
Real-time data synchronisation, simulation and prediction, known as ‘digital twins’, allow scenarios to be tested before implementing concrete changes. The integration of AI and machine learning improves predictions and eliminates multiple testing steps, resulting in significant resource savings. These advanced technologies promote more sustainable design, production and use.
Sustainability challenges require joint actions. Tyre manufacturers are working together through various initiatives. For example, the Tire Industry Project (TIP) brings together major companies to advance sustainability research programmes. The Global Platform for Sustainable Natural Rubber (GPSNR) promotes responsible rubber sourcing. Other joint technical standardisation efforts include the Carbon Black Recovery Guidelines. This collaboration helps establish common standards, share best practices and accelerate progress across the industry.
Retreading programmes are highly sophisticated and can extend the service life of the original tyres by up to 80 percent. Possible options include 100 percent recycling of used tyres through pyrolysis and devulcanisation. Pyrolysis converts them into recovered carbon black (rCB), which reduces CO₂ emissions by 30 percent. Pyrolysis oil is to be used as synthetic rubber oil or hydrogen (H₂) can be used or stored as a clean fuel for tyres factories after its gasification and purification. Devulcanization of recycled rubber, on the other hand, breaks the sulfur bonds in the rubber so it can be reused in new tyres.
Sustainable practices often lead to long-term savings through energy efficiency, waste reduction and new and futuristic technologies.
While challenges remain, the tyres manufacturers’ shared commitment to ambitious sustainability goals demonstrates that the industry recognises its environmental responsibility and is determined to contribute to the fight against climate change. Thanks to technological advances and the increasing adoption of sustainable practices, the vision of a truly green tyre industry is becoming increasingly clear.
Recently, some tyre manufacturers have begun placing the ‘Forest Stewardship Council (FSC)’ logo and a tree-shaped label on the sidewall and packaging. This globally recognised sustainability logo can influence tyre-purchasing decisions. Some criticise the FSC for its lack of commitment, but an average quarter of the total mass of these tyres is made from sustainable materials to make it less harmful to the planet. This voluntary system encourages companies to go beyond government regulations.
Michelin, Continental and Bridgestone aim to use 100 percent sustainable materials in their tyres by 2050. Nokian Tyres aims for 50 percent renewable or recycled materials by 2030. Continental plans to use more than 40 percent sustainable materials by 2030. Stricter regulatory changes could expedite the fulfilment of these commitments.
Sustainable practices often lead to long-term savings through energy efficiency, waste reduction and new and futuristic technologies. Environmentally friendly production can help tyre manufacturers from the competition and enhance their brand images.
Investments in sustainable development secure the future of companies in the face of stricter regulations. Sustainable materials are now profit drivers and not just only compliance tools. Companies lagging in adoption risk market irrelevance by 2030.
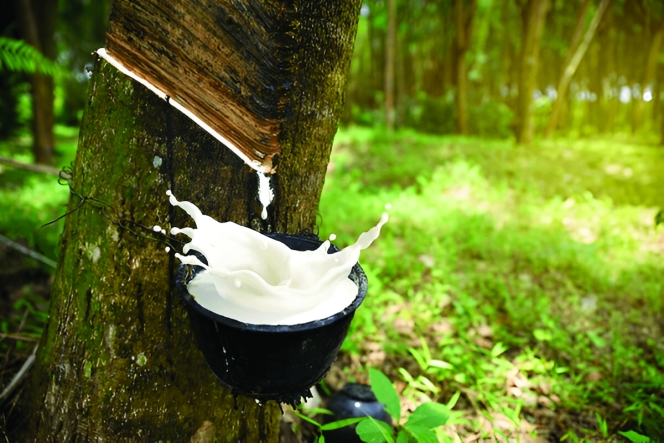
In light of evolving geopolitical developments – most recently the imposition of reciprocal tariffs by the US – raw material security and self-reliance have emerged as critical priorities for nations worldwide. For a country like India, with a population of 1.4 billion and a burgeoning youth demographic, ensuring economic resilience and safeguarding employment are imperative. India’s heavy reliance on imported raw materials exposes it to external shocks and supply chain disruptions, making the case for domestic capability building even stronger. In this context, self-reliance is increasingly seen as a strategic necessity rather than a choice.
Natural rubber is a strategic raw material that supports not just a million farmers growing rubber in India but the entire mobility ecosystem. Yet, for all its importance, natural rubber has long faced a silent crisis. Demand keeps growing. Domestic supply often stumbles. Quality variations persist. And most importantly, the knowledge gap in rubber cultivation continues to be wide, especially in non-traditional regions.
Last week, a quiet but powerful step was taken to bridge that gap. It came not through grand declarations but through an initiative designed to deliver change – patiently, persistently and at the grassroots. It’s called iSPEED.
Short for INROAD Skilling and Production Efficiency Enhancement Drive, iSPEED is an industry-led initiative under Project INROAD that was launched in Guwahati by ATMA Chairman Arun Mammen. As someone who has closely tracked the tyre industry for over two decades, I can say with confidence that this is not just another skilling programme. This is a national-level pivot for how India grows, processes and values its natural rubber.
Natural rubber is not optional for tyre manufacturing – it is core. Nearly 40 percent of the raw material in tyres is natural rubber. And yet, even as India is among the largest consumers of NR globally, we are dependent on imports for nearly 40 percent of our requirement.
Enter Project INROAD – a public-private initiative facilitated by ATMA to bring new plantations to non-traditional areas like Northeast India and West Bengal. Since its inception, INROAD has brought over 130,000 new growers into the fold. But plantation alone isn’t enough. What follows next is even more critical: skilling those growers to become long-term contributors to India’s rubber ecosystem.
THAT IS WHERE ISPEED STEPS IN.
What Makes iSPEED different? First, scale. The initiative plans to reach over 200,000 rubber growers over the next five years. But it’s not just about ticking boxes on training sessions. iSPEED focuses on creating capacity at the community level – lead farmers will be trained as experts, who in turn will become local anchors of knowledge.
Second, infrastructure. As any rubber grower will tell you, value is not just created on the tree – it is created in the processing. Poorly processed rubber fetches low prices and discourages further investment. That’s why iSPEED includes deployment of 3,000 smokehouses, 3,000 rolling machines and model nurseries across plantation zones.
Third, integration. The Rubber Board is not just a partner – it’s the lead implementation agency. Academic institutions like Tripura University and local training centres are also involved. Add to this ATMA member companies, and what you have is a true ecosystem approach.
Fourth, accessibility. All training content will be delivered in local languages, supported by WhatsApp groups, short videos, field demos and digital channels. The aim is not to push information but to embed knowledge.
One of the most compelling aspects of iSPEED is its quiet inclusivity. A large percentage of rubber growers in the Northeast are smallholders with less than an acre of land. Many are first-time planters. In regions where migration and underemployment are chronic concerns, rubber provides a steady, multi-year income. iSPEED enhances this by making that income more predictable and the process more dignified.
The iSPEED initiative needs to be viewed not only as an industrial necessity but as agricultural empowerment. It aligns perfectly with the Government of India’s push for Atmanirbhar Bharat and Viksit Bharat @2047. It is rooted in sustainability, driven by productivity and executed through collaboration.
Certainly, the success of iSPEED will not lie in its launch. It will lie in the soil, in the smokehouses, in the WhatsApp groups where farmers ask questions, share pictures and get answers from trainers they trust. It will lie in the numbers – but also in the stories.
As we move forward, the challenge will be to maintain momentum. To ensure that every rupee spent translates into real, visible impact. And to keep the spirit of collaboration alive – between industry, farmers, academia and government.
India doesn’t lack ambition. What it sometimes needs is quiet, steady execution. iSPEED brings that quiet strength. And if nurtured well, it may well become the model for how industry and agriculture can grow stronger – together.
Rajiv Budhraja is Director General of the New Delhi-based tyre industry association, Automotive Tyre Manufacturers’ Association (ATMA).The views expressed here are personal.
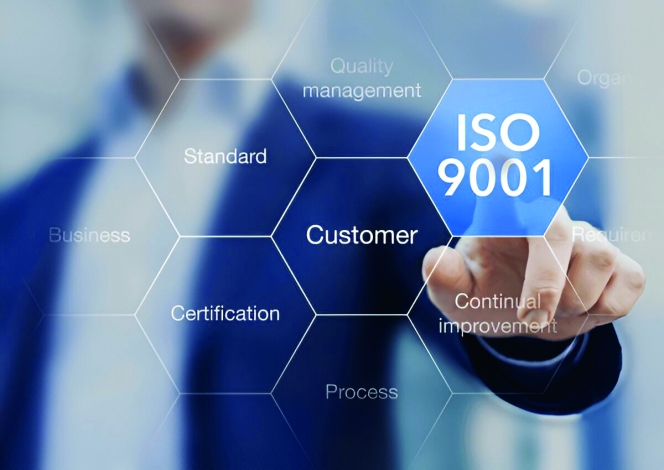
Some exiting insights
I would say that my baptism to ISO 9001 Quality Management Standard (which UpToDate is the most commonly used standard) was in 1999, a little over 25 years ago, at my last work place in Sri Lanka, which at that time was one of the leading tyre retreaders and manufacturers of two/three-wheeler tyres and custom-mixed compounds in our country. Even with my long working association with leading rubber companies, I should say I was amazed, but not in any way bewildered by the vast number of documents and paperwork deployed in establishing and maintaining the Quality Management System (QMS). The 1994 version of ISO 9000 standard used during that period had three versions, namely 9001, 9002 and 9003, adopted for manufacturing industries, service organisations and those engaged in inspection and testing respectively. The 9001-standard recommended 20 mandatory documented procedures, a Quality Manual that was compulsory and the need for work instructions at every conceivable activity. In a way, one cannot be surprised by this apparent proliferation of documentation because the first version of the ISO 9000 QMS standard in 1987 had its origins in the British Military Quality Standard BS 5750, which inherently required a high level of accuracy, precision, consistency and reliability, and hence the necessity for micro detail. Nevertheless, during the gradual evolution of the standard to its current status, one can clearly realise the transformation of the requirements to embrace the changes required for the emerging global needs of the manufacturing and service sectors of the civic society. In this article, I endeavour to bring forth some interesting practical experiences gathered during my working life and consultancy and auditing during the past 25 years with the ISO 9001/14001/and 45001 management systems in the rubber, plastics and other non- related manufacturing and service sector organisations in Sri Lanka.
Out of the numerous definitions of a management system, I find the following as a short, simple and concise and practical one:
A Management System is an organised way of defining, implementing, monitoring and improving an organisation’s operations to meet business goals, comply with regulations and enhance overall performance.
When contemplating deeper in to this apparently simple definition, I feel that it has far-reaching implications about management systems, stretching back to our ancient civilisations. One cannot comprehend how the great architectural designs, religious constructions, irrigation and the water management systems, harmonious with the natural eco-systems, were made possible without well-established management systems, although they would have been conceptually different from the contemporary management systems of the modern times. Just to site one example, during the design phase of the Maduru Oya Irrigation Project in Sri Lanka with the assistance of Canadian government in the late 1960s, the modern agro-engineers unexpectedly discovered the ruins of a centuries old anicut (ancient diversion weir). This remarkable find highlighted the advanced hydrological knowledge of our ancient civilisations, demonstrating their ingenuity in water management. Rather than disregarding the historical structure, the engineers decided to incorporate the principles in to their modern designs. Utilising the cutting-edge technology while respecting the traditional engineering wisdom in to their modern design, they constructed a new anicut that blended past innovations with contemporary advancements, enduring sustainable water distribution for agriculture.
Now coming to the more recent times in history, I can recollect that the rudiments of standard operation procedures (SOPs) and documentation, which are some of the salient features of the modern-day management systems, could be seen at the Bata Shoe Company of Ceylon Ltd, which was one of the blue-chip companies in Sri Lanka (the then Ceylon) in the late sixties, when I joined the company as a young Management Trainee. Standardised production control and hourly progress monitoring of the shoe assembly conveyors was used in the one hundred plus Bata companies spread throughout the globe. The rubber formulae cards also were also of a standard format, showing the issue date, revision status and revising date, and very importantly, the review and approval for use, all of which are key aspects of the control of documented information of the ISO Standards, which were first introduced in 1987. Another good practice used, although I realised the importance of it in later life, was the pre-preparation with the arrangements to ensure the 4Ms, namely men/machines/materials and methods to run the next day’s production, before we go home at the end of the working day. This was, in reality, the addressing of the process risks and taking preventive action to avoid the occurrence of problems, which is covered by ‘risk-based thinking’ or ‘what can go wrong’ in simple jargon and is incorporated in all the ISO Management System Standards in use today. Ironically, from my observations, only very few companies are making use of this golden principle in managing their day-to-day affairs, and hence the need for so many ‘meetings’ and firefighting, which has become a typical feature in many companies nowadays.
The crux of the matter is that management systems, in whichever names or forms they were known, have been used historically in all types of organisations, with varying degrees of success and failures, and hence the concept is nothing new. However, the International Organisation for Stadardisation (ISO), over the past 40 years, has endeavoured to bring together the cotemporary practices and thoughts about managing organisations to achieve desired outcomes in the form of all-encompassing requirements, which are universally applicable, especially in ISO 9001/14001 and 45001.
ISO 9001, the most widely deployed management system standard, was first introduced in 1987 by adopting the British military quality standards (BS5750) and aimed to create a universal approach to quality management. Over the years, ISO 9001 has undergone multiple revisions, in line with the changing global business scenarios, to make it more flexible, customer-focused and risk based, and the latest amendment has accommodated climate change issues. As environmental concerns grew in the late 20th century, the need for a systematic approach to environmental management became evident, and ISO 14001 was introduced in 1996 as response to global sustainability challenges, aligning with the Rio Summit objectives. Its revisions in 2004 and 2015 have strengthened its focus on life cycle thinking and integration into corporate strategy. ISO 45001 released in 2018 and replaced the OHSAS 18001, which has served as the primary occupational health and safety standard since 1999. It was developed to provide a structural framework for organisations to adopt a proactive risk management approach, rather than a reactive compliance-based model.
The adoption of these standards is often seen as a necessity for organisations seeking credibility, regulatory compliance and competitive advantage. Moreover, the possibility of integration of these standards allows businesses to create unified management systems, reducing redundancy and administrative burden. The High-level Structure (HLS), unreproduced by the ISO, is aimed to ensure consistency across the different management system standards.
On looking back, with the knowledge and experience I have gained by associating with the ISO-based management systems from the 1990s, I would say that the decade commencing from the mid-nineties was a period of bee-hive of activities for the manufacturing organisations in Sri Lanka. The tendency to embrace and accept any new methodologies, especially when they are successfully used in other parts of the world, is a natural survival instinct, or what has come to be known as benchmarking in the conventional management jargon, or colloquially ‘keeping up with the Joneses’. Similar trends can be seen during the introduction of other productivity improvement methodologies, such as 5S, Quality Circles, Toyota Production System (TPS), Lean and Kaizen concepts, which trickled down to our part of the world around the same period and caught up like wildfire. A notable deviation which I observed in the later methodologies is that they were directly linked to the operations, whether in manufacturing and service industries, and hence baring the initial mind set and attitudinal issues, it was relatively easier to implement and, in most cases, the results and the outcomes were directly and sometimes instantly visible, especially to the floor level personnel.
On the contrary, ISO-based management systems encompassed a more holistic and inclusive systems approach, which most top management and other managerial personnel naturally found somewhat difficult to grasp, and hence I would say that the learning curve progressed on a slow gradient.
The desire and the willingness to adopt the ISO 9001 system on the one hand and the lack of proper knowhow and experience on the other resulted in the complexity perceived by many companies in those early years. The certification bodies and some management consultancy training providers both locally and from overseas began providing the initial training, and these too were on the early stages of the learning curve due to lack of hands-on and practical experience, although the theoretical knowledge was adequately provided. As in the case pf many new waves of management thought, these conditions were ideal for some consultants to levy exorbitant facilitation fees. The mandatory conformity requirements for documentation, while resulting in the proliferation of paperwork, placed excessive burden and stress on the staff who were involved in the establishment and maintenance of the management systems. In the early years, some of the auditors of the certification bodies also focused too much on documentation and document control, document lists and revision numbering, which made the auditing a somewhat sterile exercise.
However, practically all the companies laid high emphasis on preparing for the audits, especially if they happen to be certification or recertification audits. Complete overhauling of the facilities, colour washing and cleaning up were normally carried out in addition to updating all documents and records, some of which have been neglected or not properly maintained throughout the year. Audit days had a sense of austerity and an aura of its own, which I think was good in a way at least once a year, although it could have sent wrong signals to the employees regarding leadership and management commitment as specified in Clause 5.0 of the standards.
The dichotomy between ISO requirements and the other management functions is still seen in some companies, especially the large organisations, which have management system coordination assigned to a septate department. Although the High-Level Structure of the three standards is intended to facilitate to enable an integrated management system, only a very few companies seem to be doing it effectively.
Despite their wide spread adoption, the real-world application of Management Systems like ISO 9001/14001 and 45001 varies significantly. While some organisations genuinely integrate these systems into their operations, others treat them as bureaucratic hurdles for securing certification for external validation and legal compliance rather than for internal improvement. The question is often raised as to whether businesses are blindly embracing these standards, or are they judiciously adopting them for real impact?
The cost and complexity of implementation can be prohibitive, especially for the small and medium scale enterprises (SMEs), and achieving and maintaining certification requires significant resources, which can divert attention from the core business activities. While the standards provide a good framework, their success largely depends on an organisation’s commitment. A poorly implemented system can lead to inefficiencies, resistance from employees and minimum real-world impact. Furthermore, in some industries, rapid technological advancements outpace the evolution of these standards, making them seem rigid or outdated.
These management systems can be powerful tools for improving quality, sustainability and workplace safety if used correctly. However, their effectiveness depends on how they are implemented. Blind adherence to ISO standards very often causes inefficiencies and a waste of resources, and judicious and strategic adoption can drive real improvements.
I vividly remember an awareness programme organised by the Sri Lanka Standards Institution around the year 2000 to introduce the major changes in the ISO 9001: 2000 Standard. In one of the presentations, ISO 9001-based QMS was depieced as an elephant on which the organisation rides to use the system, while what happens in many a case is the organisation carrying the elephant (QMS) as an extra burden.
Margaret Wolff Hungerford, in her 1878 novel Molly Bawan, first mentioned the famous quote ‘beauty is in the eyes of the beholder’, which augments well to the ISO-based Management System Standards.
At this juncture, I cannot resist citing a Buddhist discourse where the doctrine (Dhamma) is depicted as a piece of gold. For a child it will be a play item, and for investor it is a valuable asset whose value keeps on appreciating with time, while for the jeweller it will be the source material that can be turned into a beautiful necklace.
Management System Standards will continue to play a vital role in helping organisations to systematically manage their activities to the foreseeable future with varying degrees of success along with the appropriate amendments and revisions that may come into effect from time to time.
The author is a Management Counsellor from Sri Lanka.
Comments (0)
ADD COMMENT