Goodyear Names Grégory Boucharlat as Sr VP of Global Commercial Division
- By TT News
- May 16, 2025
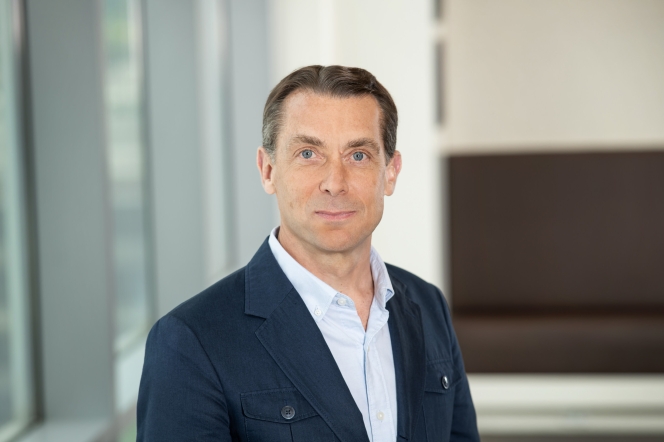
Goodyear Tire & Rubber Company has appointed Grégory Boucharlat as senior vice president of Global Commercial, the company announced today. In this newly created position, Boucharlat will join Goodyear’s senior leadership team, which will strategically coordinate the company’s worldwide commercial tyre business.
Boucharlat, who will report directly to Chief Executive Officer and President Mark Stewart, will continue to lead Goodyear’s Tires-as-a-Service (TaaS) organisation as part of his expanded responsibilities.
The appointment comes as part of the American tyre manufacturer’s efforts to create what it describes as “a unified and aligned global company” following its recent streamlining of operations, which included the sale of its off-the-road tyre business to Japan’s Yokohama Rubber earlier this year.
With more than thirty years at Goodyear, Boucharlat has built extensive experience in the company’s commercial tyre operations. He started in truck tyre sales before progressing through various leadership positions in Europe, including vice president of Commercial EU. His most recent role was vice president of TaaS, where he gained broader global commercial experience beyond the European market.
“Grégory brings to this new role proven abilities to drive innovation in our business and expand his leadership responsibility. He is well-positioned to have a fast start and ensure a seamless transition for our Commercial business,” said Stewart. “I have enormous confidence in his ability to lead our Commercial business on a global scale as our next step in creating a unified and aligned global company.”
The appointment takes effect immediately, with Boucharlat continuing to be based in Brussels, Belgium.
The move comes as Goodyear focuses on strengthening its commercial vehicle operations after divesting its mining and construction tyre division to Yokohama in a $919 million deal that closed in February 2025.
Apollo Tyres Hungary Plant Gets ISCC+ Certification
- By TT News
- July 01, 2025
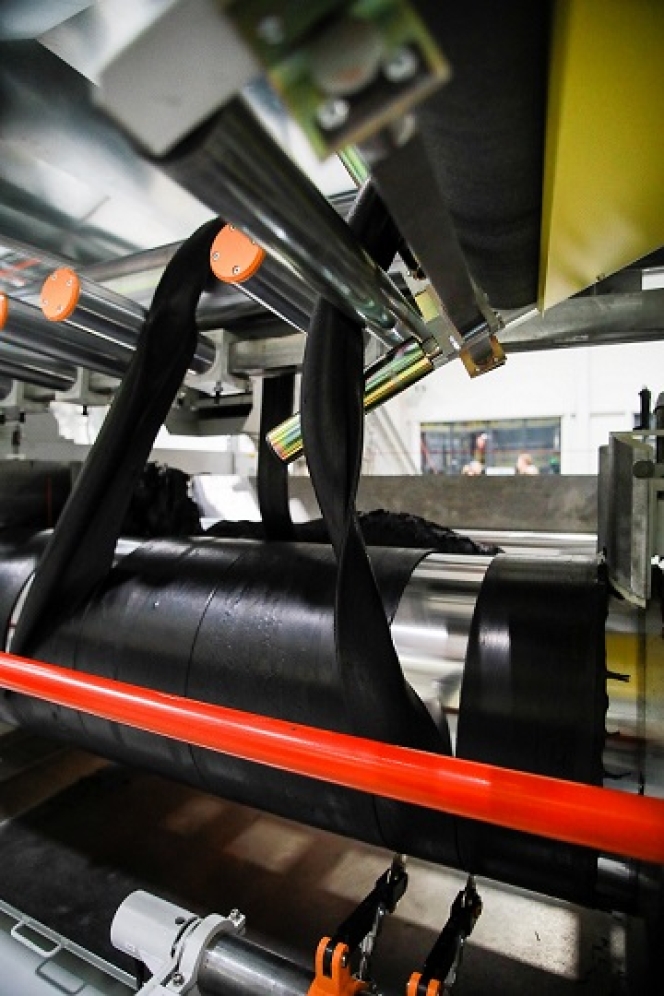
Apollo Tyres, one of the leading tyre manufacturers in the world, has added another feather to its cap, with its Hungary production plant bagging the International Sustainability and Carbon Certification Plus (ISCC+) certification.
The globally recognised ISCC certification is a voluntary programme that recognises companies for their sustainability and carbon reduction initiatives. Apollo Tyres, by achieving ISCC+ certification, has been recognised for not only meeting the stringent sustainability standards but also for its responsible production in the industry.
Apollo Tyres Secures Gold Medal In 2025 EcoVadis Sustainability Rating
As part of its commitment, the tyre maker continues to focus on monitoring and verifying sustainability practices across its processes and supply chain.
Rajeev Kumar Sinha, Chief Manufacturing Officer, Apollo Tyres, said, “This certification is an important step forward as we continue to integrate sustainability deeply into our operations. It aligns perfectly with our ambitious goal of incorporating 40 percent sustainable raw materials – including renewable and recycled input materials – into our products by 2030.”
- Kraton Corporation
- Kraton Sustainability Report
- Sustainability
- EcoVadis Platinum
- 2024 Nitto Supplier Sustainability Award
Kraton Corporation Publishes 2024 Sustainability Report
- By TT News
- July 01, 2025
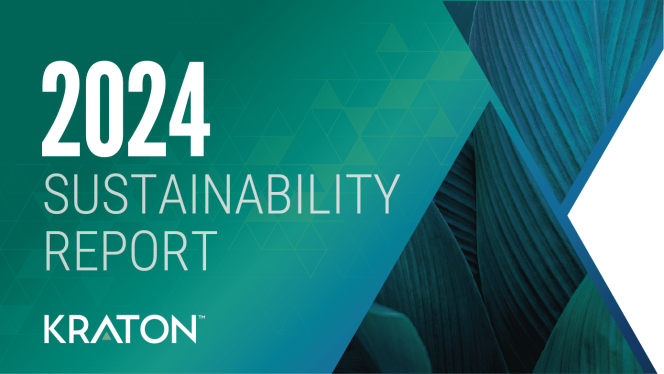
Kraton Corporation, a global leader in speciality polymers and biobased solutions derived from pine wood pulping co-products, has published its 2024 Sustainability Report, ‘Innovating with Purpose’. The report showcases the company’s advancements in climate action, circular product innovation and value chain partnerships, reinforcing its commitment to sustainable solutions.
Key achievements include a 41 percent reduction in Scope 1 & 2 greenhouse gas emissions since 2014 and a 35 percent decline in emissions intensity. Kraton also maintained its EcoVadis Platinum rating for the fourth consecutive year and received the 2024 Nitto Supplier Sustainability Award. Strategic initiatives such as a Double Materiality Assessment and a USD 35 million investment in biorefinery upgrades at its Panama City facility further demonstrate Kraton’s sustainability leadership.
The company enhanced transparency by expanding life cycle assessment (LCA) data to cover nearly 90 percent of its product portfolio, helping customers evaluate environmental impacts. Additionally, Kraton launched a data excellence program to streamline ESG reporting and refine decarbonisation goals.
Aligned with GRI, SASB, UN Global Compact and TCFD frameworks, the report reflects Kraton’s sustainability pillars: Being Reliable Partners, Preserving Planet and Empowering People. These efforts underscore Kraton’s dedication to driving meaningful progress across its operations and industries.
Marcello Boldrini, Kraton Chief Executive Officer, said, “2024 marked a pivotal year in Kraton’s sustainability journey. We turned ambition into action, significantly reducing our Scope 1 and 2 emissions by 41 percent from our 2014 baseline and earned an EcoVadis Platinum rating for the fourth consecutive year. We accelerated our decarbonisation strategy, advanced biobased innovation and partnered with customers such as WJ Group and Henkel to help address global sustainability challenges. As demand for sustainable chemicals grows, our focus remains on developing the right solutions, fostering strong partnerships and cultivating the culture necessary to lead this transformation responsibly and competitively.”
Rogier Roelen, Kraton Chief Sustainability Officer, said, “We have established new processes to scale credible, data-driven sustainability across our business. In 2024, we enhanced our ESG reporting through a data harmonisation programme and completed a Double Materiality Assessment to better align with the Corporate Sustainability Reporting Directive (CSRD). We also expanded our Life Cycle Assessment (LCA) data to cover almost 90 percent of our product portfolio, providing customers with greater transparency into the environmental impact of our products. These efforts reinforce our ability to identify where we can make the most impact and support more informed, strategic decision-making.”
Michelin Collaborates With Murfitts For Tyre Pyrolysis Plant
- By TT News
- July 01, 2025
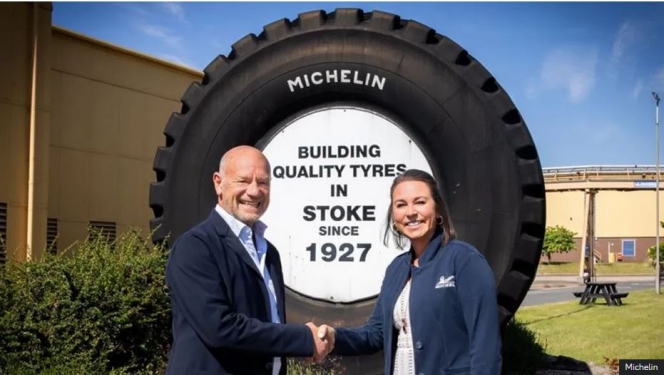
Murfitts Industries, the UK’s largest tyre recycling company, has unveiled plans for a state-of-the-art materials recovery facility at Michelin’s Stoke-on-Trent tyre plant. This groundbreaking initiative will transform end-of-life tyres into valuable resources while significantly reducing the site’s environmental footprint. The advanced recycling process will recover energy to power Michelin’s manufacturing operations, cutting annual CO₂ emissions by 1,500 tonnes. Additionally, the facility will produce high-quality recovered carbon black (rCB) and tyre pyrolysis oil (TPO), supporting sustainable material production.
Under the agreement, Michelin will supply Murfitts with 12,500 tonnes of discarded tyres annually – equivalent to 1.35 million car tyres. This capacity far exceeds local demand, with the plant able to process the equivalent of two tyres from every car registered in Stoke-on-Trent and Staffordshire. Slated for completion by late 2026, the facility will apply Murfitts’ proprietary pyrolysis technology at commercial scale, extracting reusable raw materials from tyres. The rCB will serve as a sustainable alternative in tyre manufacturing and other industrial applications, while TPO will be used in material production and alternative fuels, displacing virgin petroleum feedstocks.
Beyond material recovery, the process generates steam that will directly supply Michelin’s tyre-curing operations, replacing natural gas and further reducing fossil fuel reliance. Murfitts, which already recycles 20 million tyres yearly for applications like sports surfaces and road asphalt, continues to pioneer circular economy solutions – ensuring tyre-derived materials re-enter production cycles, closing the loop on waste. This collaboration marks a major step toward greener tyre manufacturing and resource-efficient industrial practices.
Mark Murfitt, Founder, Murfitts Industries, said, “We believe this plant could be a breakthrough in the life cycle of a tyre. It moves tyre recycling on from recovering energy and material for other uses to being able to feed it directly back into factories for new tyre production. Our core ethos at Murfitts has always been that end-of-life tyres are a valuable resource and we need to do all we can to maximise the use of the energy and materials within them. We have been developing our pyrolysis process for a number of years and our results now show we can produce material from end-of-life tyres which can perform better than the virgin equivalent for some applications. This plant will be a win-win for the tyre industry, the local and national economy and the environment.”
Christina Peloquin, Site Director, Michelin UK, said, “This is a really exciting project which reduces our environmental impact at the same time as helping us stay competitive by lowering our energy costs. The team has worked exceptionally hard on this project, and we’re looking forward to welcoming Murfitts to our Stoke-on-Trent site.”
Maria Röttger, CEO and President, Michelin Europe North, said, “At Michelin, we see every challenge as a chance to lead positive change – and end-of-life tyres are no exception. As shapers, innovators and pioneers of sustainable mobility, Michelin is committed to transforming the way tyres are handled at every stage of their life cycle. Through our deep expertise and forward-thinking approach, we are co-building a robust recycling ecosystem that redefines what has previously been possible. This project with Murfitts Industries is a powerful reflection of Michelin’s enduring commitment to sustainability and responsible leadership in the tyre and rubber industry.”
Evonik to Boost Asia Supply Chain with Shanghai Production Expansion
- By TT News
- June 30, 2025
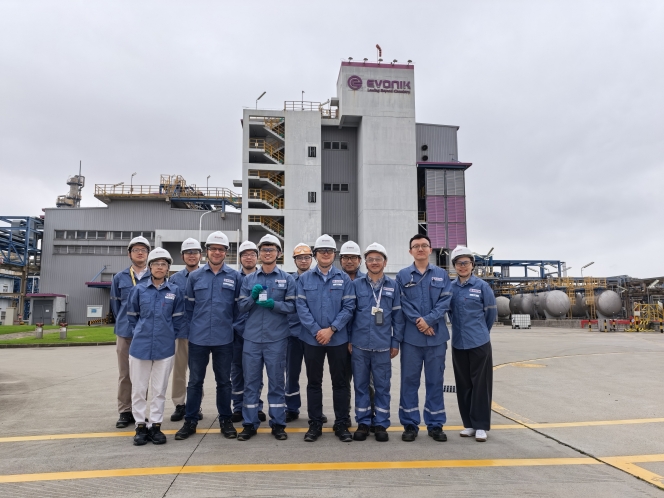
Evonik Industries will localise production of a key tyre additive in Shanghai, marking a strategic shift to enhance supply security across Asia amid growing regional demand.
The Essen-based company announced plans to establish the final production step of its POLYVEST ST-E 60 product at its Shanghai facility, with operations expected to commence by the third quarter of 2025. The expansion will significantly increase the global production capacity of silane-functionalised polybutadienes.
The move represents Evonik’s latest effort to strengthen supply chains and reduce dependency on European manufacturing for Asian markets. POLYVEST serves as a reactive plasticiser in tyre formulations and is also used in rubber compounds, adhesives, tyres, coatings, and sealants.
“This strategic investment will enhance our production capabilities and ensure that our customers in Asia benefit from improved supply security and shorter lead times,” said Dr Anna Maria Ickert, Head of Evonik Coating & Adhesive Resins. “In today’s environment, fostering independent supply chains and bringing our products closer to our customers is essential, enabling us to respond more effectively to their needs.”
The Shanghai expansion comes as global chemical companies reassess manufacturing footprints following supply chain disruptions experienced during the pandemic and ongoing geopolitical tensions. China remains a crucial market for speciality chemicals, particularly in the automotive and construction sectors.
Evonik’s decision reflects broader industry trends towards regionalisation of production, with companies seeking to reduce logistics costs whilst improving responsiveness to local market demands. The tyre industry, a key end-market for POLYVEST, has experienced robust growth in Asia driven by expanding automotive production.
Dr Jürgen Herwig, Head of Evonik’s polybutadienes and speciality acrylics business, emphasised the expansion’s strategic importance. “This expansion aligns with our long-term strategy to strengthen our global footprint while maintaining a strong focus on sustainability and operational excellence,” he said. “The new capacity will enable Evonik’s customers to achieve their business goals while participating in the region’s growth.”
POLYVEST products utilise rubber-based chemistry to ensure compatibility with tyre tread compounds, thereby addressing performance requirements in an increasingly demanding automotive market. The localisation strategy aims to reduce lead times whilst maintaining product quality standards.
Comments (0)
ADD COMMENT