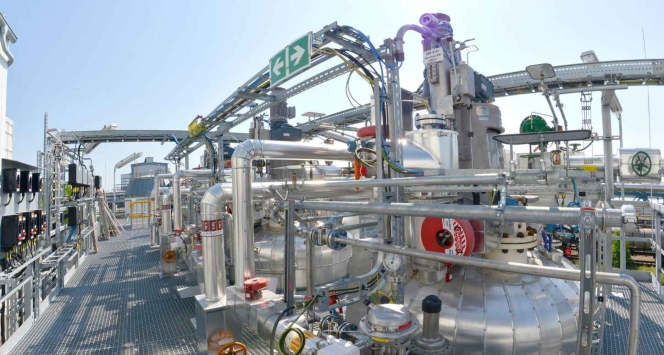
Reflecting on current and future trends in the tyre industry, Andre Lanning, Global Business Director, Synthetic Rubber, Trinseo Europe GmbH, sees the need for much closer collaborations - not only between tyre companies and suppliers but among suppliers themselves. “If we really want to address the big issues in the industry, reduce rolling resistance, improve fuel efficiency, and get better at recycling and re-using materials and chemicals, we need to have a paradigm shift in how we approach innovation.”
According to Dr. Sandra Hofmann, Director, Technology & Innovation, Synthetic Rubber, Trinseo Deutschland GmbH, speed (response time to market) and sustainability are the main trends that will dominate the global tyre industry compared to other industries.
“The tyre industry, traditionally, has been conservative on knowledge-sharing and collaborating on innovation. Going forward, collaborations are key to moving forward as the complexity in the segment we are focusing on is very high. Every stakeholder in the tyre industry is driving hard for innovations, and, on the co-suppliers’ side, we are keen on collaborations. And, of course, working together with customers is always part of the development,” said Dr. Hofmann.
In recent times, Trinseo has been focusing on close relationships with other stakeholders for developing new products. Trinseo fosters deep engagement with partners through its centralised synthetic rubber site located in Schkopau, Germany, where technology & innovation, mini-plant, pilot plant, and expanded production assets are located. To reduce product development time from lab sample to commercialisation, Trinseo started a state-of-the-art S-SBR pilot plant in Schkopau, for its synthetic rubber business, which makes it more agile and flexible than ever before in its ability to turn around S-SBR product testing. The company says the S-SBR pilot plant allows for more efficient use of Trinseo’s production facilities and helps speed up innovation in the performance tyres market. As part of its efforts, the company introduces the early development process to its customers. “We have invested substantially in R&D. In 2018, we started the pilot plant where we can make several hundred kilograms of materials, and that is enough for our development partners and customers to build a tyre already in the product development process,” said Dr. Hofmann.
Dr. Hofmann added, “The capabilities we are bringing to the table, in combination with our openness and willingness for collaborations, are major enablers towards shortening of the product development process.”
Major tyre companies are betting high on recycled and bio-mass materials, aiming to eliminate materials derived from fossil fuels, to make tyres in the future. However, the ‘industrialisation’ of recycled and bio-mass materials to obtain synthetic rubber will be a more significant threshold. “It is nice to have targets, but the main challenge is to implement these targets through technology. Making synthetic rubber from recycled and bio-mass materials will be a gradual process, and we see it as an opportunity and want to be a front runner for sustainability”, said Lanning.
Sustainability
Trinseo, according to the executive, is already contributing to tyre companies’ sustainability efforts by supplying solutions that reduce rolling resistance, CO2 emissions and improve fuel efficiency.
“Sustainability has many dimensions. It could be recycled and bio-based materials. As a company, we are very much active in the recycling of polystyrene back into styrene monomer which can be introduced as recycled feedstock for packaging applications. As for butadiene, for a long time, it has been made of biomass like sugar and others. As a company, we are exploring sources of sustainable feedstocks, not only looking at how we can contribute to our customers’ sustainability efforts, but to the raw materials that go into our own products,” explained Dr Hofmann.
When asked about having a common platform for all stakeholders to develop products, Lanning, said “if tyre manufacturers are serious about sustainability, there needs to be closer and more open collaboration around innovation between tyre and rubber producers. And that is not the case today. Working together we can tackle the challenges, whereas pursuing innovation completely separately will make it harder to reach the sustainability targets”.
Trinseo has an excellent technical community, called Technical Service & Development Group, that works with its customers around the world. This way, the company educates them on its products and their usages. “Irrespective of where we operate, Trinseo focuses on high-end technologies in functionalised S-SBR,” said Lanning. Dr Hofmann added “We are investing heavily in local markets to provide our products and services more efficiently and improve communications between our customers and the company”.
Synthetic rubber is now being used for passenger car tyres, owing to properties that make it suitable for high-end tyres. Trinseo is expanding its portfolio by also focusing on truck and bus tyres (the company’s low Tg polymers like SPRINTAN SLR 3402 are already used in truck and bus tyres as a partial replacement for natural rubber; they improve energy efficiency and performance, predominantly balancing rolling resistance and wear).
“We need to increase the use of synthetic rubber in truck and bus tyres to further impact global sustainability goals. To achieve these goals, we are looking for customers that plan to have SR in tyres for heavy commercial vehicles as well, but we are also using this opportunity to educate the end customers about the advantage of using functionalised S-SBR” said Lanning.
Another challenge for material suppliers is to keep its product development strategies aligned with the fast-changing trends in the automotive industry. Fundamental requirements of low rolling resistance in tyres are not changing in any types of new mobility, believes the company executive. “We also see a shift of focus on wear improvement,” added Dr Hofmann.
Optimising all three aspects of the magic triangle has always been a challenge. The latest functionalised SPRINTAN™ S-SBR grades are proven to reduce lab indicators for rolling resistance by 30 percent compared to nonfunctionalised synthetic rubber grades. This allows for at least three to five percent less fuel consumption in passenger cars. Trinseo’s recently launched SPRINTAN 918S displaying multi-functionalisation technology to reduce rolling resistance and improve wet grip for ultra-high-performance tyres used on premium cars and SUVs.
Retreading’s Stubborn Struggle
- By Gaurav Nandi
- August 29, 2025
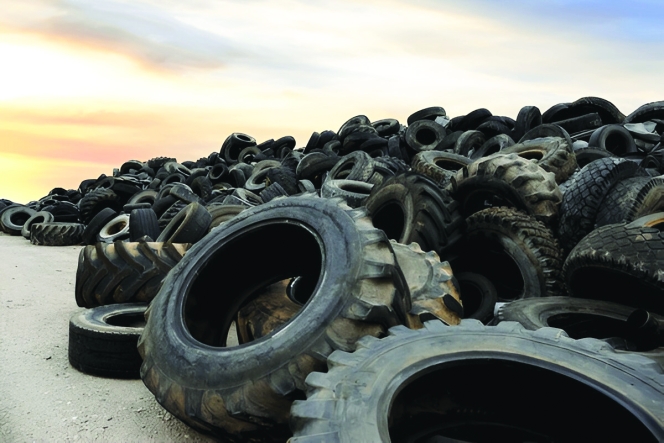
Despite decades of presence and proven sustainability benefits, the global truck tyre retreading industry remains mired in perception problems and systemic inertia. As raw material costs rise and environmental pressures mount, retreading should be a no-brainer. Yet, it continues to be sidelined by outdated mindsets, customer ignorance and a lack of cohesive industry messaging. Tirecore CEO Garry Drisdelle, in a candid interview with Tyre Trends, paints a picture of a sector at risk – not because it lacks value, but because it has failed to communicate it. The stakes, he warns, are too high for complacency.
Despite decades of existence, the retreading industry still wrestles with fundamental challenges across the world – not least the stubborn perception among customers and stakeholders about the true value of retreaded truck tyres. Tirecore Chief Executive Officer Garry Drisdelle pulls no punches in diagnosing the sector’s issues and outlining the uphill battle ahead.
Speaking to Tyre Trends, he said, “Tirecore is primarily a supplier of quality truck tyre casings to the retread industry. But while retreading should logically form the cornerstone of sustainable tyre use, the industry remains far from mainstream acceptance.”
“Educating the customers really as to how much upcycling, how much can we save – it’s beyond the pennies or pounds you save on the initial purchase,” Drisdelle said. Yet, frustratingly, many customers remain fixated on upfront costs instead of the total lifecycle value of a tyre.
This fixation, he implies, represents a systemic failure within the industry. “The industry has to do a better job towards educating the consumers, which primarily are fleet owners, beyond the initial purchase,” said Drisdelle. The inability to shift consumer mindset threatens to leave retreading as a niche rather than a necessity.
Tirecore positions itself primarily as a global supplier of high-quality truck tyre casings to the retread industry, operating across markets that include the United States, Canada and India. Rather than manufacturing or retreading tyres directly, the company serves as a critical node in the circular economy of commercial tyres, ensuring that valuable casings find extended life through retreading.
“We are in the business of preserving 85 percent of the tyre components existing material’s value saving valuable resources,” said Drisdelle.
The company’s operational model is rooted in the principle of upcycling over replacement, focusing on longevity and material reuse rather than disposability. While Tirecore’s precise logistical affiliations remain unspecified, its strategic direction is clearly aimed at aligning with sustainability mandates and evolving global market demands.
DISPOSABLE TREATMENT
Drisdelle highlights a critical contradiction. Tyres are one of the most safety-critical components on the road, yet they are taken for granted at a staggering scale. “Picture a truck is rolling down the highway at 100km/h pulling 20,000 kilogrammes of freight, riding on just 6-8-10 rolling rubber contact points. Tyres are one of the most critical transportation components, yet we treat them like disposable goods. How taken for granted is that product?”
Even as raw material prices surge and truck tyre costs climb, the entrenched perception treats tyres as disposable consumables. “We need to reframe the conversation – a tyre should be seen as an asset and not a consumable,” Drisdelle emphasises.
This disconnect reveals deeper issues prevalent within the industry. Retreading has not been effectively communicated as a financial and environmental beneficial in the long tome. Moreover, legislative inconsistency and lack of incentives for the industry as a whole is a deterrent that needs to be addressed immediately.
Drisdelle insists that retreading should be the environmental rallying point for the sector. “We have 85 percent of the material in the original product that is quite capable of being reprocessed and upcycled many times,” he said.
He contrasts upcycling favourably with recycling, which he argues requires more energy and effort than the original production process, especially in plastics and other materials: “By the time you just recycle something, the energy to recycle it is more than the process.”
Yet these arguments come with an implicit critique that the industry has failed to effectively translate this environmental rationale into a compelling value proposition for customers and regulators alike.
LEGISLATIVE MOMENTUM
Drisdelle points to potential legislation requiring truck tyres to be recyclable or retreadable as a possible catalyst for change. “Picture if legislation comes out that you’re not allowed to sell truck tyres unless they’re recyclable from their ingredients unless they’re retreadable,” he noted.
However, he quickly tempers this with realism stating, “We can never get to zero. That’s a cool little marketing thing but it’s an impossibility in the world of physics and science.”
This admission highlights the gap between aspirational sustainability goals and practical realities, a gap that leaves retreading vulnerable to accusations of greenwashing or insufficient progress.
ADAPT OR STAGNATE
Looking to the future, Drisdelle’s plan is pragmatic but cautious. “Our future plans are to keep up with the market demand, to evolve as the market evolves. Pivot and prosper,” he said.
Such a measured approach reflects the uncertainty and fragmentation within the industry. The promise of retreading remains strong, but without decisive action on education, regulation and innovation, the sector risks losing ground to cheaper, new tyres or alternative technologies.
The recurring theme throughout Drisdelle’s commentary is education, or rather, the lack of it. “The education of the fleet owners is primary to everything. The education of the industry to build a better tyre is somewhat secondary,” he stated.
This stark admission speaks volumes. Despite retreading’s environmental and economic advantages, a fundamental communication failure continues to hobble the industry.
Drisdelle points out the irony stating, “Without a widespread cultural shift in perception, retreading will struggle to move beyond a cost-saving niche for price-sensitive fleets to a mainstream standard.”
Drisdelle’s blunt assessment of the retread industry reveals a sector caught between its potential and its persistent shortcomings. Tirecore’s role as a global supplier to retreaders is clear but the wider challenge remains.
Without significant progress on education and regulatory backing, the retread industry risks remaining on the margins, overshadowed by the convenience of new tyres and the pressures of market inertia.
Retreading’s promise is substantial. But, as Drisdelle’s comments underscore, fulfilling that promise demands a candid reckoning with the industry’s educational failures and a relentless push for change or face stagnation in a rapidly evolving tyre market. n
India’s Tyre Recycling Industry Enters New Era With Gujarat’s Green Light To Continuous Pyrolysis
- By Gaurav Nandi
- August 28, 2025
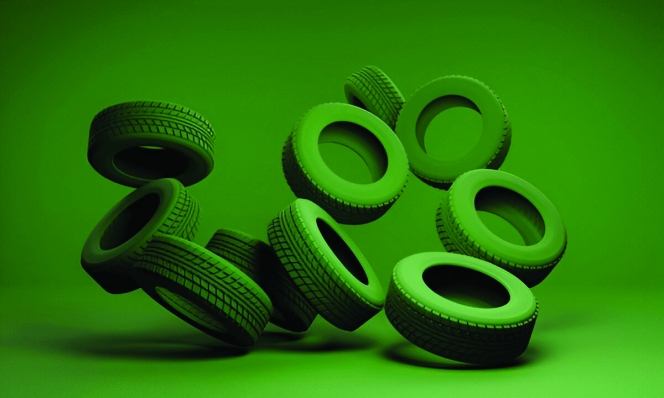
India’s tyre recycling sector, long plagued by fragmented operations and lax compliance, is undergoing a critical overhaul. With Gujarat’s recent approval for continuous pyrolysis plants, the industry is moving decisively towards cleaner, scalable and regulation-driven solutions. This shift signals more than a technological upgrade and it’s a rebuke of outdated batch systems and a call for formalisation, traceability and environmental accountability. As global demand for sustainable materials rises, India’s pivot positions it as a potential leader in circular economy practices. In conversation with TRRAI President Chetan Joshi, we explore how this development could redefine the future of tyre waste management at home and abroad.
India’s tyre recycling sector is on the cusp of a transformational shift with the Gujarat Pollution Control Board (GPCB) approving the establishment of continuous pyrolysis plants in the state. The move marks a significant departure from traditional batch-based tyre processing systems, promising to boost efficiency, environmental compliance and resource recovery at an industrial scale.
“This shift is nothing short of revolutionary,” said President of the Tyre and Rubber Recyclers Association of India (TRRAI) Chetan Joshi. “We’re moving from outdated, fragmented batch operations to streamlined, automated continuous pyrolysis systems. This is going to uplift the entire industry, from cleaner emissions to higher resource recovery, better traceability and serious investor interest. It sets a new national standard and will accelerate formalisation, industrial-scale operations and a far more sustainable approach across India.”
The approval has been met with optimism by recyclers and environmental advocates alike as it signifies a structural change in how end-of-life tyres will be handled in India, which is home to more than 1.8 million tonnes of tyre waste annually.
The Gujarat model mandates stringent adherence to environmental standards, particularly concerning air quality and emissions. Continuous pyrolysis plants approved under the new framework are required to incorporate top-tier pollution control mechanisms.
“We see compliance not as an obligation but as a core design principle. Our plants are being built with advanced air pollution control devices (APCDs), real-time emissions monitoring and automation that ensures consistent performance. We’re aligning with both GPCB and CPCB regulations through pro-active design, third-party audits and integrating global best practices. It’s not just about meeting today’s standards but staying ahead of tomorrow’s,” said Joshi.
The approach reflects a broader shift in the recycling sector, where regulatory compliance is no longer viewed as a hurdle but as a strategic advantage and market differentiator.
Industrial scale
Under the new directive, each continuous pyrolysis facility must operate at a minimum capacity of 60 tonnes per day (TPD). This scale reflects the government’s push to industrialise tyre recycling and eliminate inefficient, informal practices.
“Scaling to 60 TPD is a serious industrial commitment and it means heavy investment in automation, utilities, safety systems and logistics. But it’s also the only way forward. India generates over 1.8 million tonnes of end-of-life tyres annually. This scale allows us to handle the problem responsibly while creating traceable and economically viable recycling ecosystems,” Joshi said.
With India’s growing automotive base, the urgency to develop sustainable, high-capacity recycling infrastructure has never been higher.
One of the key advantages of continuous pyrolysis lies in its outputs that include valuable petrochemical byproducts like pyrolysis oil, sustainable fuels and recovered carbon black (rCB). These materials are increasingly in demand across a range of industries, from rubber manufacturing to renewable energy.
“These by-products are entering a new phase of global relevance. Recovered carbon black is being adopted in rubber, plastics and even pigments. Pyro oil, when upgraded, is a viable alternative fuel. We’re actively engaging with global buyers and certifiers to standardise and integrate these outputs into international supply chains. The world is ready for sustainable alternatives and it’s up to us to deliver with consistency and quality,” averred Joshi.
India’s entry into this global supply chain positions it not just as a recycler of waste but as a producer of sustainable industrial materials.
Circular economy
TRRAI views this milestone as more than an environmental success. It’s a step towards realising India’s vision of a circular economy, where tyre waste is fully reintegrated into the production cycle.
“We aim to be more than recyclers. We want to be circular economy enablers. That means building systems where tyre waste is traceable from collection to output, where value is recovered and re-injected into the economy. We’re developing collection infrastructure, digital traceability and offtake agreements with industries globally. This is not just about waste; it’s about resource optimisation and environmental stewardship,” Joshi explained.
Such a shift could significantly reduce the country’s carbon footprint while fostering job creation and industrial growth.
Despite the enthusiasm, industry leaders acknowledge that challenges remain, particularly in terms of adoption among legacy operators and infrastructure gaps.
“The biggest challenge is inertia as many operators are still working in the unorganised sector with outdated setups. Then there’s infrastructure as a hurdle as tyre collection networks are underdeveloped in many parts of India. To overcome this, we’re advocating policy changes, investing in reverse logistics and training the workforce. Regulatory clarity and enforcement will be key and we’re working closely with industry associations and government bodies to drive this,” said Joshi.
Stakeholders believe that education, investment and enforcement will be pivotal to ensuring widespread transition to continuous pyrolysis systems.
Global trends
Globally, countries like those in Europe and North America have already adopted advanced tyre recycling technologies. But Joshi believes India has a unique opportunity to leapfrog older systems and build world-class facilities from scratch.
“Europe and North America have a head start, especially in policy frameworks and end-use applications. But India’s opportunity lies in scale and adaptability. We can leapfrog legacy systems and build efficient, tech-driven plants from the ground up. If we get the ecosystem right – collection, compliance and capital – we can set new benchmarks, not just catch up. India could become a global hub for tyre recycling technology,” he said.
The industry’s fast pace of development combined with India’s manufacturing and engineering capabilities could make the country a case study in sustainable industrial transformation.
Innovations in emission reduction
In line with global best practices, TRRAI and its partners are integrating innovations to ensure safety and minimal environmental impact.
“We’re integrating closed-loop systems, AI-driven control logic and multi-stage gas cleaning technology. Real-time emissions data will be available both internally and to regulators. Safety protocols are built into every operational layer, from material feeding to shutdown procedures. We’ve also prioritised workforce training and regular third-party safety audits. The goal is to operate with zero compromise on health or the environment,” Joshi explained.
Such innovations are crucial not only to maintaining regulatory compliance but also to building public and investor confidence.
The entry of advanced technologies is expected to catalyse foreign investment and technical collaboration.
“Our approach is partnership-driven. We’re already working with European and Australian technology providers and are in discussions with institutional investors. We see India as a platform for co-creation, where global IP meets local scale and agility. Through industry associations like TRRAI, we’re building collaborative networks to ensure knowledge sharing, investment facilitation and joint innovation,” Joshi noted.
This strategy could help India become a global innovation hub for recycling technologies applicable across other emerging markets.
The vision
Looking to the long term, the industry’s goals extend far beyond domestic waste management. TRRAI envisions exporting its model to developing nations facing similar challenges.
“Our vision is bold but simple. It is to create a fully circular, scalable and replicable tyre recycling ecosystem. India should not only solve its own tyre waste crisis but become a global model for how emerging markets can tackle resource recovery. We see this model being exported to Southeast Asia, Africa and Latin America. With continuous pyrolysis, India can move from reactive recycling to proactive resource management on a global stage,” Joshi concluded.
As Gujarat lights the way with its approval of continuous pyrolysis plants, India’s tyre recycling sector is poised to become a beacon of innovation and sustainability – one that could shape the future of global recycling practices. n
Selling To Sellers
- By Gaurav Nandi
- August 27, 2025
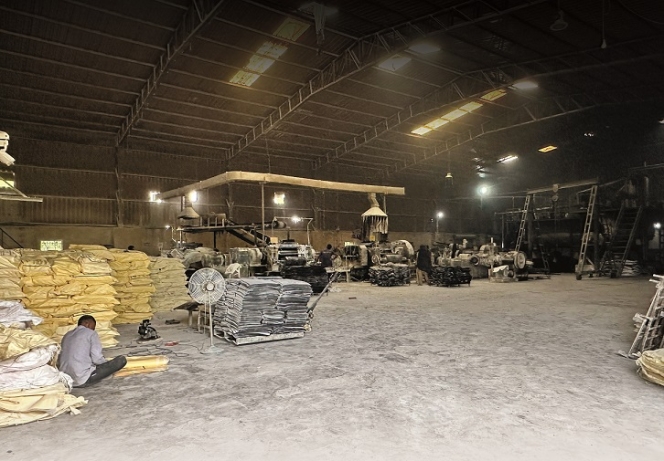
For decades, China has stood as the world’s dominant supplier of raw materials across industries, making it a significant player in the global supply chain. However, Gujarat-based Lead Reclaimed Rubber, an Indian MSME, has achieved a remarkable feat by exporting reclaimed rubber crumb to Chinese manufacturers. The company capitalised on India’s abundant scrap tyre supply and favourable policies, tapping into China’s massive demand for reclaimed rubber. As Lead Reclaimed Rubber continues to expand its production capacity and export markets, the company also faces challenges such as labour shortages, supply delays and regulatory concerns. Despite these obstacles, it remains optimistic about its growth prospects.
China has been the largest supplier of raw material for every industry known to man since decades. While there are many companies in different markets trying to sell back to China, an Indian MSME has unachieved the feat of selling to the ‘seller’.
Gujarat-based end-of-life tyre (ELT) recycler Lead Reclaimed Rubber has been exporting its reclaimed rubber crumb to Chinese manufactures. Commenting on how the company achieved this feat, Chief Executive Officer Jayeshh Patel told Tyre Trends in an exclusive interview, “China is the largest importer of reclaimed rubber, sourcing the material not only from India but also from countries like Vietnam and Sri Lanka. This demand is driven by a vast domestic market for tyres and inner tubes, with numerous brands operating in the aftermarket segment as well as in OEM manufacturing. As a result, the growth potential is significant.”
“While China has its own reclaim rubber plants, it faces limitations due to inadequate scrap tyre availability. In contrast, India has an abundant supply of scrap tyres supported by both domestic generation and strong import volumes. Additionally, India’s favourable government policies and the availability of skilled labour further enhance its position as a competitive and reliable supplier of reclaimed rubber to China. Hence, our company capitalised on the situation and started exporting,” he added.
Lead Reclaim Rubber was established in 2012 and is an NSE-listed company. It operates both in domestic and export markets with plans to grow its current production capacity as the reclaimed rubber market unfolds its potential.
Moreover, Patel noted that the Extended Producer Responsibility (EPR) framework by the Indian Government is playing a crucial role for the recycling industry for reaching greater heights.
EPR IMPACT
According to Patel, EPR has emerged as a transformative force in the recycling industry. Given the industry’s dynamic nature and its drive to adopt advanced technologies, EPR presents a timely and impactful mechanism to support growth particularly for micro, small and medium enterprises (MSMEs).
“While the recycling sector is evolving, recyclers often operate on thin profit margins, which limits investment in new technologies and process upgrades. EPR has helped bridge this gap. Under the scheme, we are awarded green credits for every kilogramme of end-of-life tyres we recycle. These credits are a compliance requirement for tyre manufacturers, who purchase them from registered recyclers like us. For every 100 kilogrammes of tyre recycled, we receive approximately 130 green credits, each valued at INR 2.5, resulting in a direct financial incentive. This additional income strengthens our balance sheet and can be reinvested in research and development, capacity expansion and technology upgrades. In this way, EPR indirectly fosters innovation and scaling in the recycling ecosystem,” said Patel.
To maintain accountability and transparency, the Central Pollution Control Board (CPCB) has developed a digital portal where all stakeholders must report data.
“We record our incoming feedstock (purchase data) and outgoing materials (sales invoices) on the CPCB portal. This data forms the basis for calculating green credit eligibility. Our operations are routinely audited by both government agencies and the tyre industry. These audits verify that we meet all technical and environmental standards before credits are approved. The government has also established baseline electricity usage norms for tyre recycling. We are required to submit our electricity bills to demonstrate compliance. If our energy consumption does not meet the defined threshold, we are ineligible for green credits, preventing fraudulent claims,” he Patel.
He optimistically contented that EPR is rapidly becoming the backbone of the tyre recycling industry. For over a decade, recyclers have struggled with limited access to capital. EPR is now enabling financial stability, paving the way for recyclers to professionalise operations, scale sustainably and drive forward-looking initiatives. This policy is not just a support mechanism but a growth enabler.
AN OVERVIEW
The recycling company focuses on sustainable practices and high-quality output. “Our core operation involves sourcing EOL tyres and tubes from various states across India for recycling into value-added rubber products. Our recycling process begins with a proprietary feedstock checking system to ensure quality. The tyres are then sorted, cut and processed into crumb rubber powder. Currently, we produce crumb in 30–40 mesh sizes with plans to expand into finer 80 and 120 mesh grades in the near future,” explained Patel.
For the domestic industry, crumb rubber serves a wide range of applications. Finer meshes (80 and 120) are used in various rubber and dye industries, while 30–40 mesh is commonly used in bitumen modification for road construction, in line with the Central Government’s CRMB 30 guidelines.
Furthermore, the company employs a green devulcanisation system that utilises steam, oil and pressure to break down and re-bond the rubber polymers from EOL tyres. This method is 100 percent sustainable, producing zero discharge and zero wastage. Even the steam generated during the process is condensed and reused. “We are in the process of acquiring a Z-Certificate for our zero-waste operations,” divulged Patel.
Post-devulcanisation, the rubber material becomes soft and slightly sticky due to the restructured cross-linking. It then undergoes further processing in the reclaim section, which includes refiners, mixing mills and a cleaning stage.
During cleaning, all metallic and non-rubber impurities are extracted using strainers with 60-millimetre wire mesh. The purified compound is extruded into noodle form and sent to the refiners to produce the final reclaimed rubber product, typically in seed form.
“We tailor our reclaimed rubber to meet the specific requirements of our customers including thickness, size and performance properties. Each product is made to specification. The reclaimed rubber is used across various industries including tyre and tube manufacturing, conveyor belts, packaging and other rubber-based products. As industries increasingly shift from virgin to reclaimed rubber, we position ourselves as a reliable and environmentally responsible supplier,” noted Patel.
PRODUCTION AND SUPPLY
According to Patel, virgin rubber contains about 90–100 percent RSPL, while reclaimed rubber has around 50–52 percent. It’s more affordable than virgin rubber, but the use of 100 percent reclaimed rubber in tyre manufacturing is still a distant thought.
However, it’s widely used in rubber mats. Tyre manufacturers are gradually increasing reclaimed rubber usage, encouraged by government directives to reduce dependence on natural resources and imports. Since local virgin rubber production is insufficient, it’s being imported from countries like Vietnam.
Currently, large tyre manufacturers in India use only a small percentage of reclaimed rubber, around two to three parts per hundred
rubber (PHR). For cycle and three-wheeler tyres, it goes up to 20 PHR. Conveyor belts use up to 30 percent, and in non-critical applications with almost no performance impact, reclaimed rubber can be used up to 95 percent.
The company’s plant is located in Katlal, Kheda, near Ahmedabad, and it uses Indian machinery sourced from Punjab. “We started production at 250 metric tonnes per month. After Covid, we scaled up to 490 metric tonnes and recently reached 960 metric tonnes per month. Within the next year, we plan to expand further to 2,000 metric tonnes per month,” said Patel.
He added, “We run our plant with TBR tyres both nylon and radial. We’re centrally located in Ahmedabad and as Gujarat shares borders with Rajasthan, Madhya Pradesh, Maharashtra, and the southern states, it helps us with tyre sourcing. We collect tyres through a three-layer supply chain consisting puncture shops, rag pickers and aggregators. The aggregators sort the tyres as per our requirements.”
For nylon tyres, the company only uses the centre portion, specifically from 1020 tyres and discards the sidewalls. For radial tyres, it recycles the entire tyre. The recycling technology is the same for both, but the processing recipe differs. Radial tyres have cords in the centre, so the devulcanisation process is slightly modified to handle the added strength. Its research and development facility are located inside the plant.
Commenting on what sets the company apart from competitors, Patel explained, “Our focus on consistency and timely delivery sets us apart from competitors. We maintain a 95 percent consistency ratio. From raw material to the final product, everything is monitored and controlled by our control plant, which is also a key differentiator. We also have an in-house development department that not only ensures quality consistency but also works on improving the benefits for our customers. On top of that, we conduct awareness programmes to educate our customers on which materials are best suited for different use cases. That’s something others in the industry usually don’t do.”
MARKET SPREAD
Lead Reclaim Rubber serves both domestic and international markets. Among the industries it caters to, conveyor belts account for 30 percent of its business, tyres for 20 percent and the remainder comes from rubber products and packaging. Although the tyre and tube segments currently represent a smaller share of revenue, Patel anticipates significant growth in these areas. Over the next five years, it expects tyres and tubes to become its largest consumer segment followed by conveyor belts.
The company attributes this projected growth to the government’s strong emphasis on the circular economy and the rapid expansion of the automobile industry, both of which are likely to increase demand for reclaimed rubber.
The company exports to several countries including Sri Lanka, China, Bangladesh, Turkey and Philippines. China is currently the largest consumer in its export portfolio, followed by Sri Lanka. According to the Patel, export markets generally use more reclaimed rubber due to their larger production capacities.
The export market continues to show strong demand and the company currently has pending orders from China.
However, as European nations vie for restricted EOL tyre exports to India, the scenario for indigenous recyclers can be precarious. Commenting on the potential impact of such restriction, Patel highlighted, “India recycles a significant portion of the scrap tyres it generates. However, unregulated and illegal pyrolysis operations remain a critical concern. These units often operate without environmental compliance, posing risks to public health and the environment. Stronger government intervention and regulatory enforcement are urgently needed to eliminate such practices and ensure sustainable recycling.”
“India’s tyre recycling ecosystem is diverse and imbalanced. While there are numerous recyclers, the segment is dominated by pyrolysis players (approximately 70 percent), with reclaim rubber manufacturers constituting only around 30 percent. This heavy skew towards pyrolysis is problematic, especially since many of these players depend on imported scrap tyres for feedstock. If the import of scrap tyres into India is disrupted, it will create a significant supply shortage, driving up the price of ELTs. Currently, the price of scrap tyres ranges between INR 18–21 per kilogramme, but a halt in imports could potentially increase this to INR 40 per kilogramme, a nearly 50 percent spike, which would severely impact the entire recycling value chain,” cautioned Patel.
Besides this looming issue, Patel highlighted several pending challenges for the industry. One of the primary issues is a shortage of skilled labour. Interestingly, even as the industry moves towards greater automation, the demand for labour continues to rise.
Another challenge is supply delays caused by aggregators, who often fall behind on delivery timelines due to their own labour shortages. Additionally, maintaining quality consistency is difficult as scrap tyres vary in composition from batch to batch. As a result, the company must closely monitor and control its processes.
A significant concern affecting future growth is the regulatory environment. The company remains cautious about expanding production because of the current ban on scrap tyres.
Although the business is regulated, there’s an underlying fear that stricter government action could further limit the supply of scrap tyres. Such restrictions could leave newly built expansion units underutilised.
Patel believes that unless government policies become more supportive, major investments and expansions will remain risky.
Looking ahead, Lead Reclaim Rubber is planning both forward and backward integration. On the forward side, the company aims to start manufacturing rubber tiles made entirely from rubber granules, a by-product of its current process. It also plans to enter the cycle tyre industry.
As part of its backward integration strategy, the company intends to set up more tyre collection centres both internationally and within various Indian states to secure a more consistent supply chain.
Challenges That Hinder Progress
- By Gaurav Nandi
- August 26, 2025
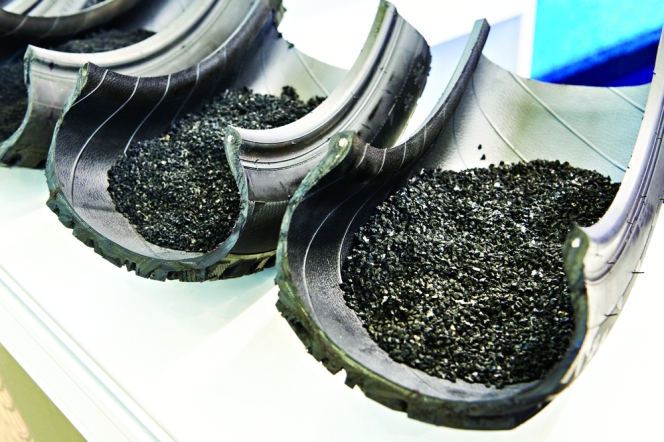
Despite two decades of reform, Europe’s tyre recycling ecosystem remains mired in regulatory inertia and market fragmentation. While the EU successfully curbed tyre landfilling in the early 2000s and achieved high collection rates, true circularity remains elusive. Over half of collected tyres are still incinerated rather than recycled into new products. The lack of mandatory recycled content targets, harmonised end-of-waste criteria and coherent eco-design regulations continue to stall progress. As environmental stakes rise and end-markets like artificial turf face bans, EuRIC’s latest manifesto lays bare the urgent need for systemic reform, spotlighting persistent policy voids, legal ambiguities and missed opportunities across the value chain.
Europe’s tyre recycling challenges have been building for over two decades. Back in 1999, the European Union banned tyre landfilling under Directive 1999/31/EC. This forced a major shift, and by 2003, landfilling tyres was officially prohibited. At that point, Europe still struggled to manage the sheer volume of end-of-life tyres (ELTs), often resorting to incineration or exporting them for disposal elsewhere.
Since then, collection rates improved dramatically, from around 25 percent in the mid-1990s to nearly 95 percent by 2010, but recycling quality remained substandard. Although most ELTs were collected, half were used for energy recovery, not material recycling. True circular solutions like reusing rubber in new tyres have lagged due to technological and regulatory hurdles
Complex EU regulations, limited mandates on recycled content and ecological concerns slow innovation. Over the past few years, initiatives like Life Green Vulcan, BlackCycle and policy push from the European Recycling Industries’ Confederation (EuRIC) show growing momentum, but real impact is yet to be seen.
EuRIC has been constantly advocating reforms that would change the course of the continent’s tyre recycling space with its recent manifesto delving into the immediate steps that ought to be undertaken to strengthen the tyre recycling industry.
EuRIC, through its Mechanical Tyres Recycling Branch (MTR), outlined a comprehensive vision for strengthening Europe’s tyre recycling sector. With over five million tonnes of tyres produced annually in the EU and around three million tonnes becoming ELTs, only about half are recycled – the rest are incinerated. EuRIC underscores the environmental advantages of mechanical tyre recycling and advocates for prioritising it over energy recovery to align with circular economy goals.
Speaking to Tyre Trends on the biggest obstacles to implementing mandatory recycled rubber content targets in new tyres and how industry collaboration can help overcome them, EuRIC’s Technical Advisor for tyres, Gabriel Gomez, mentioned, “Currently, the main regulatory challenge is the lack of a mandate from the authorities to define how and when the mandatory recycled content targets are to be implemented. We have received good feedback from the manufacturers in Europe regarding their willingness to include these targets. However, there is a need for a solidly defined regulatory framework that guarantees a level playing field in the tyre value chain and promotes innovation in this area.”
“The main risk of failing to implement harmonised end-of-waste criteria lies in the growing, practical need for a defined set of criteria to determine end-of-waste status. If the EU delays further in the creation of harmonised end-of-waste criteria, this will push member states to create their own national criteria, which could vary significantly and prove incompatible. This fragmentation would lead to market disruption, create confusion across the value chain and introduce legal uncertainty – all of which would ultimately weaken the European recycling industry and its competitiveness,” he added.
He noted that EuRIC strongly supports a complete ban on the export of tyres and tyre shreds for incineration or landfilling. These practices represent a misuse of valuable resources that should be reintegrated into the economy and clearly contradict the waste hierarchy in the European Waste Framework Directive.
“EuRIC, representing Europe’s tyre recyclers would welcome swift implementation of such a ban, especially since existing tools such as the Waste Shipment Regulation are already being used to prevent exports to operators and facilities that do not ensure environmentally sound treatment of these materials,” noted Gomez.
THE MANIFESTO
The recently published manifesto by EuRIC proposes five key policy actions to address systemic barriers and unlock the potential of tyre recycling. First, it calls for mandatory recycled content targets – 10 percent for new tyres and 20 percent for automotive parts – to stimulate demand and reduce reliance on virgin rubber. Public procurement and financial incentives like VAT reductions are also suggested to support this demand shift. Currently, artificial turf accounts for a major share of ELT-derived rubber, but impending bans on micro-plastics threaten this end-market, making policy support more critical.
Second, EuRIC demands a ban on the export of unprocessed and shredded waste tyres outside the EU. ELTs are often exported to regions with weak environmental controls, where they are landfilled or incinerated. Countries like India have become significant importers, raising environmental and regulatory concerns. To counter this, EuRIC stresses the need for strict enforcement of the EU’s Waste Shipment Regulation and advocates for EU-wide end-of-waste (EoW) criteria to facilitate trade within the EU and promote high-value recycling.
Thirdly, the manifesto emphasises the importance of eco-design in tyres, urging that tyres be made retreadable, recyclable and free from hazardous substances. Innovations like self-sealing and noise-reducing foams, while performance-enhancing, impede recycling and can even cause fires during shredding. EuRIC supports the Ecodesign for Sustainable Products Regulation (ESPR) and wants tyre manufacturers to bear the cost of non-recyclable designs.
Fourth, EuRIC promotes the Digital Product Passport (DPP) as a key enabler of recycling efficiency. Current data on tyres is insufficient; hence, they propose leveraging RFID technology to track chemical composition and recyclability through a centralised database. This transparency would help recyclers better handle materials and comply with chemical regulations.
Lastly, the manifesto addresses the need for a science-based chemicals policy that supports recycling rather than undermining it. The current trend towards hazard-based regulation with near-zero thresholds for certain chemicals risks sidelining recycled materials. EuRIC urges a shift towards risk-based assessments, transparent
testing methods and harmonised standards to ensure recycled materials remain viable in the EU’s green transition.
TOWARDS RECYCLABILITY
According to Gomez, mechanical tyre recycling is a recycling method for rubber that has stood the test of time. It remains the most common and best-established route for recycling tyres in Europe with the technology offering high-quality output. It also has the added value that it can serve as a reliable supplier for further processing technologies dealing with vulcanised rubber. Recycled rubber from ELTs offers significant potential for technologies that require a uniform and predictable input to maintain control over industrial processes.
Nonetheless, over three years after rubber from ELTs was prioritised, no regulation has materialised yet. Commenting on what lead to the stalling, Gomez noted, “The past year has brought major changes at EU level with the start of a new Commission mandate, which may explain the shift in priorities. However, at EuRIC we are working closely with manufactures and policymakers to keep the issue high on the agenda. We see harmonised EoW criteria as a key opportunity to align the interests of recyclers and manufacturers. Harmonised EoW criteria would bring significant benefits for the entire value chain, from boosting investment and legal certainty to increasing the uptake of recycled materials.”
Alluding to whether the current EU chemicals legislation, especially restrictions on substances like PAHs, appropriately balances environmental protection with the needs of a circular economy or does it unintentionally favour virgin materials, he stated, “It is not a matter of favouring virgin materials. The main issue is that the current legislation is not designed to consider that the materials in an article may have more than one life. Whenever the legislation targets the content of a substance in a recycled material, sometimes it fails to consider the real exposure to the substance based on the application and the nature of the material.”
Digital Product Passport is another vital tool for the entire industry’s circularity goals. While it is still in its early stages, EuRIC notes that there are projects that target the implementation of the DPP in tyres and it is optimistic about the possibilities this tool offers to the industry. Amongst the information that the DPP should make available for recyclers is the contents of substances of concern and hazardous substances as well as any substances or features that would hinder the recycling of the tyres. With this information in hand, the recyclers will be able to sort the tyres in a manner that allows for safer recycled products and more efficient processing.
PERSISTENT HURDLES
According to Gomez, illegal or poorly regulated exports of tyres create serious problems both economically and environmentally. They drain valuable raw materials from the EU and risk harming the environment and public health in importing countries if ELTs are not treated in an environmentally sound manner.
Furthermore, the loss goes beyond the economic aspect when it comes to the materials used on tyres. Incinerating ELTs destroys a valuable resource like rubber and locks us into a linear economy model that’s no longer fit for purpose. Recycling, on the other hand, and overall circularity of tyres, keeps materials in the loop, boosts resilience and contributes to EU sustainability and competitiveness.
A strong starting point to combat illegal exports would be the rigorous enforcement of the Waste Shipment Regulation, specifically targeting ELT exports. If recyclers can count on a steady, reliable supply of materials, they will invest. Increased availability of material and supply security are essential to encourage investments in recycling.
“An important take-away of the policy related to tyre recycling is that tyres should be treated as strategic resources, not just waste. Tyres are essential to every economy activity and inevitably reach its end-of-life stage. This makes it critical to regulate the full lifecycle, from design to disposal, with circularity in mind. Aligning on principles, like prioritising recycling over landfilling or incineration, would already be a big step forward globally,” averred Gomez.
Commenting whether Europe’s mechanical recycling infrastructure is equipped to handle a sharp increase in ELTs if exports are banned, he mentioned, “The mechanical tyre recyclers in Europe are determined to meet the challenge and tackle the increase in ELTs if an export ban is implemented. However, unlocking further capacity and investments in future development projects depend on regulatory certainty. That means a guaranteed level playing field through harmonised EoW criteria, recycled content targets and eco-design for improved recyclability. With the right framework and tools, uncertainty can be removed and investments will follow.”
While the mandatory recycled content requirements are essential to boost recycling, complementary short-term financial incentives, whether market-based or fiscal, are equally necessary to close the price gap between primary and recycled materials. Fiscal incentives, such as reduced VAT rates for recycled materials and products made from recycled materials, can play a major role in encouraging uptake. Green public procurement also holds substantial potential to stimulate demand for more sustainable and circular products.
Recycled materials from ELTs have real potential in the EV supply chain. Interest is growing, and EuRIC is confident that recycled rubber can be a reliable, high-quality material to support the shift to greener mobility.
Gomez noted that there are many encouraging examples of manufacturers incorporating recycled and sustainable materials into tyre design. A great advantage that recycled materials from ELTs offer is the availability of high-quality recycled raw materials that reliably allow manufacturers to experiment and innovate as they know that the recycling industry is capable and ready to deliver.
Comments (0)
ADD COMMENT