Need for scrap tyre disposal policy
- By Rahul Shringarpure
- February 22, 2021
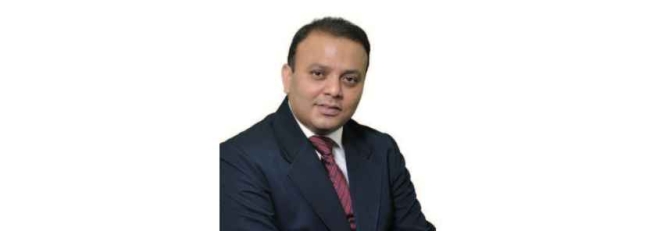
The year 2020 has been a year like no other. The pandemic has brought everyone on the same platform. We all have been a mute witness to the rage of Nature and the apocalypse it can create. The question which persists in my mind is ‘Have we really learnt any lessons from the same?’ Are we going to treat Mother Earth better and build a sustainable planet for our future generation?
On a brighter note, most economies are showing signs of phenomenal recovery. The automobile sector looks to be one of the biggest beneficiaries. Vehicular traffic on the road and the number of new vehicle registrations are a big indicator of the same. In fact, an Indian two-wheeler manufacturer broke its own export record in December 2020. Our belief has proved true again. The human race has endured many such pandemics throughout the years of evolution and evolved better, stronger, smarter.
Processing ELTs
Indogreen Enviro has been involved in the process of ELTs (End of life Tyres) for about a decade.
We have been witnessing the growth of the tyre recycling industry. From the 1970-2000, the majority of organised ELT recycling was about making ‘Devulcanised rubber reclaim sheets.’ These sheets are used in a wide range of applications like tyre re-treads, bicycle tyres, conveyor belts, rubber compounds to name a few.
From 2000 onwards the market started changing due to the introduction of radial tyres. The radial tyres had high tensile steel in them and now could not be grinded directly like the nylon tyres. They need new technology Shredders, Raspers, Granulators to make it ready for grinding. This decade saw many high technology shredding and granulation plants coming up across the country. This included India’s largest and fully automated 100 Mt/annum plant till date Vapi, Gujarat. These granulation plants created a new market for ELT granules-based playground tiles and mats. The CRMB(Crumb Rubber Modified Bitumen) also gained acceptance in large national road construction projects.
Batch type pyrolysis plants
From 2005 onwards, there was a new tyre recycling technology introduced to the Indian market - ‘Batch type pyrolysis plants.’ These plants were initially imported from China. Though profitable, they were extremely unstable, environmentally non-compliant and unsafe for operation. Due to their profitability ,By the year 2019,India had more than 1000 batch type-pyrolysis plants installed. The combined tyre requirement per day for these plants was about 10,000 Mt/day. That would mean a requirement of 10,00,000 passenger car tyres every day, to give a perspective. This monster had a huge appetite that could not be met with tyres from India. So these pyrolysis companies started looking for imported tyres with a perpetual supply possibility from round the globe.
There was only one challenge. The pyrolysis plants are not allowed to import tyres. The shredding companies were allowed to import with a license from DGFT. The batch type pyrolysis companies started buying container loads of tyres from the shredding companies. India started importing about 900,000 MT annually making it the largest importer of ELT in the world until July 2019.The Public Interest Litigation filed against the ‘Batch type pyrolysis plants’ put the brakes on these transactions. The government was forced to take cognisance of the humungous nature of the impending matter at hand.
This is the India story, but could be a similar story for any country from Asia where the Scrap Tyre disposal policy is not yet framed or implemented. I am taking the stance of the agitator than just being a mute spectator. There is so much that can be done than what is being done today.
Scrap tyre disposal policy
There is a strong buzz about ‘Circular Economy’ in Europe and the US. Large tyre companies and chemical giants are investing in various tyre technologies to bring the derivatives from the tyres to be reused in manufacturing new tyres. In India, we don’t even have a national scrap tyre disposal policy. Most local tyre companies are still waiting for an ‘EPR’ to start thinking of sustainable disposal.
In fact, we as a country need ‘Circular economy.’ The responsibly recycled ELT can create high quality reclaim rubber, High calorific value oil with possibility on further hydro treatment to distil commercial grade diesel & petrol, commercial grade carbon black for manufacturing pigments, etc, liberated fibre to make thermoplastics, liberated gases that can be further processed, this can go on and on. There is so much of interest from large companies to set up plants to process this waste but they hesitate because of the lack of a government framework to support the huge capital investment required.
Despite all odds, some companies from India have done some amazing work in developing innovative ELT recycling technologies. A fine example would be Radhe Renewable Energy Development Ltd, Rajkot. They conceived, developed and now operate the ‘World Largest 100 MT Per Day Single Reactor Continuous Pyrolysis Plant ‘ for the last 8 years in Bhilwara, Rajasthan. No other company from around the globe can boast of this feat.In fact some of the large global giants who were looking for a commercial scale large continuous plant could not believe that such a plant and technology existed, that too from a non-descript town from India. This company now supplies ASTM grade Carbon Black and High Calorie fuel to Indian tyre industry beginning the ‘Circular Economy.’
Another interesting Company is Hotfut Sports, an award-winning sports infrastructure development and management company that has been one of the largest consumers of turf technology and synthetic turf products across its various formats. These products have a primary infill requirement of SBR rubber. HotFut has consciously been adapting its procurement process to ensure all SBR and infill / shock-pad requirements are sourced responsibly using recycled ELT’s / rubber scrap making all their facilities more environmentally friendly. They have structured solutions for forward thinking tyre companies wanting to pro-actively process their ELT with a win -win proposition. Many major tyre companies have found their solution very sustainable as well as profitable.
Last year, Internet was abuzz about this start up ‘Blink Green’ from Pune, India. They used ELT for making attractive ladies’ footwear and purses. They have found the utility of this wonderful waste and now is utilising her designing skill and the expertise of the cobble community to churn out beautiful, durable items for the domestic and global market.
These kinds of stories are emerging from all across the continent Imagine the power of scalability of these kind of products with the right kind of financial and marketing support.
I look forward to the day (soon) when we have the ‘Scrap tyre disposal policy’ is finally rolled out and the top tyre companies wait for the EPR policy is over. With a sizeable contribution coming out of their respective CSR budgets and ATMA’s able guidance, a national body to look at new & innovative sustainable disposal practices for ELT could be established. This would be a giant first step taken in the Asian subcontinent towards sustainable recycling of this incredible waste and thus setting a precedence for other countries to follow.
ARLANXEO Launches Sustainable Rubber Portfolio in India as Demand for Green Materials Grows
- By TT News
- August 01, 2025
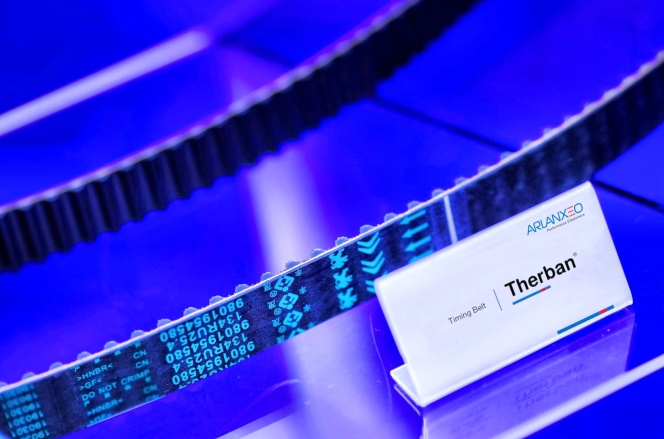
ARLANXEO has launched its ISCC PLUS-certified Keltan Eco rubber grades in India, responding to rising demand for sustainable materials in the world’s most populous nation.
The German-based performance elastomers manufacturer unveiled the portfolio through technical seminars and workshops, targeting automotive components, wires and cables applications where customers increasingly value environmental credentials.
The Keltan Eco range comprises Eco-B and Eco-BC grades derived from bio-based and bio-circular feedstocks, respectively, whilst maintaining identical physical and mechanical properties to conventional fossil fuel-based products. The materials offer resistance to oxygen, ozone, heat and radiation.
ARLANXEO employs a mass balance approach for certification, ensuring the volume of Eco-labelled products corresponds with sustainable source feedstock volumes. This methodology provides supply chain transparency and enables customers to verify sustainability claims in downstream applications.
“This new portfolio will help our customers seize sustainable growth opportunities in India and stay ahead amid industry transformation,” said Rupesh Shah, ARLANXEO India’s Managing Director and Regional Sales Head.
The company also showcased its Therban hydrogenated nitrile butadiene rubber speciality grades during the events, targeting original equipment manufacturers and component producers. Therban applications include air conditioning seals, timing belts, high-temperature gaskets for oil platforms and spacecraft components.
ARLANXEO operates as one of the world’s largest synthetic rubber producers with more than 10 production sites across eight countries and four research and development locations globally. The company serves automotive, tyre, electrical, construction and oil and gas sectors.
The Indian launch forms part of ARLANXEO’s broader strategy to expand sustainable product offerings across key growth markets. Additional ISCC PLUS-certified synthetic rubber grades will be introduced in India following the initial rollout.
India’s steady rubber consumption growth, driven by the automotive and infrastructure sectors, signals a significant opportunity for speciality chemical producers aiming for sustained market expansion. ARLANXEO is well-positioned to meet this demand, marking a decisive step toward a greener, more innovative rubber industry in India.
Rathi Group Marks Major Milestone With First Export Of ISCC-Certified Pyrolysis Oil
- By TT News
- August 01, 2025
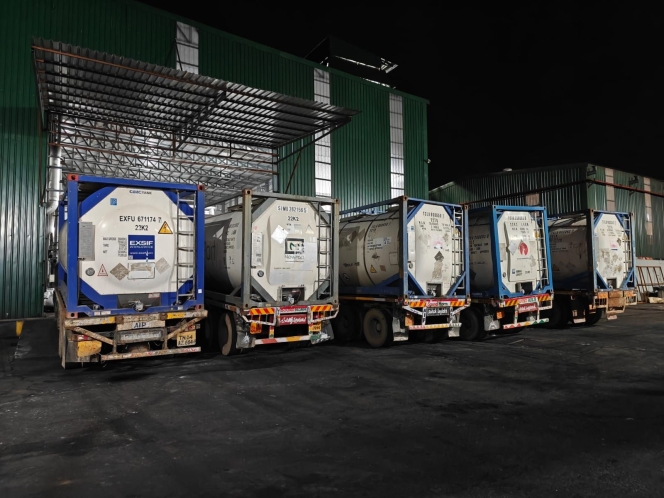
Rathi Group, a leader in pyrolysis and end-of-life tyre (ELT) recycling, has achieved a significant milestone with its first export shipment of ISCC PLUS-certified pyrolysis oil. With over 12 years of industry expertise, the company continues to set benchmarks in sustainable recycling, innovation and circular economy practices.
This landmark export highlights Rathi Group’s ability to supply globally recognised, eco-friendly alternatives to conventional fossil fuels. The company’s integrated operations – spanning ELT shredding, continuous pyrolysis, carbon black recovery and oil distillation – adhere to stringent international sustainability standards.
The ISCC PLUS certification underscores Rathi Group’s commitment to environmental responsibility, supply chain transparency and climate-conscious solutions. The accomplishment reflects the efforts of its dedicated team and partners, reinforcing the company’s mission to drive impactful change in sustainable tyre recycling.
- Kraton Corporation
- Speciality Polymers
- Renewable Biomaterials
- EcoVadis Platinum Rating
- Sustainability
Kraton Releases 2024 Sustainability Report Showcasing Sustainable Innovation
- By TT News
- July 30, 2025
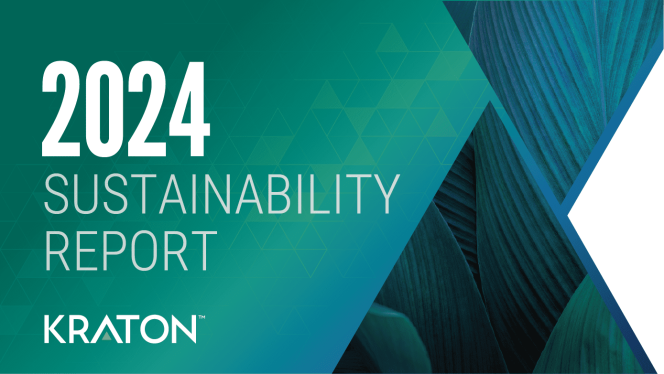
Kraton Corporation, a global leader in speciality polymers and renewable biomaterials, has published its 2024 Sustainability Report, Innovating with Purpose. The report outlines the company’s advancements in climate action, circular product solutions and supply chain sustainability, reinforcing its commitment to a greener future.
Key achievements include a 41 percent reduction in Scope 1 & 2 emissions since 2014, a 35 percent decrease in emissions intensity and maintaining EcoVadis’ Platinum rating for the fourth straight year. Kraton also received the 2024 Nitto Supplier Sustainability Award and conducted a Double Materiality Assessment to refine its ESG strategy.
Operational milestones feature a USD 35 million upgrade to its Florida biorefinery, expanded lifecycle assessment (LCA) data covering 90 percent of its product portfolio and a new data excellence programme to enhance ESG transparency.
Aligned with GRI, SASB, UN Global Compact and TCFD frameworks, the report emphasises Kraton’s sustainability pillars: Reliable Partnerships, Planetary Stewardship and Empowering People. These efforts reflect the company’s dedication to responsible innovation and measurable environmental progress.
Marcello Boldrini, CEO, Kraton, said, “2024 marked a pivotal year in Kraton’s sustainability journey. We turned ambition into action, significantly reducing our Scope 1 and 2 emissions by 41 percent from our 2014 baseline and earned an EcoVadis Platinum rating for the fourth consecutive year. We accelerated our decarbonisation strategy, advanced biobased innovation and partnered with customers such as WJ Group and Henkel to help address global sustainability challenges. As demand for sustainable chemicals grows, our focus remains on developing the right solutions, fostering strong partnerships and cultivating the culture necessary to lead this transformation responsibly and competitively.”
Rogier Roelen, Chief Sustainability Officer, Kraton, said, “We have established new processes to scale credible, data-driven sustainability across our business. In 2024, we enhanced our ESG reporting through a data harmonisation programme and completed a Double Materiality Assessment to better align with the Corporate Sustainability Reporting Directive (CSRD). We also expanded our Life Cycle Assessment (LCA) data to cover almost 90 percent of our product portfolio, providing customers with greater transparency into the environmental impact of our products. These efforts reinforce our ability to identify where we can make the most impact and support more informed, strategic decision-making.”
German Rubber Industry Faces Mixed Outlook Amid Persistent Challenges: wdk
- By TT News
- July 30, 2025
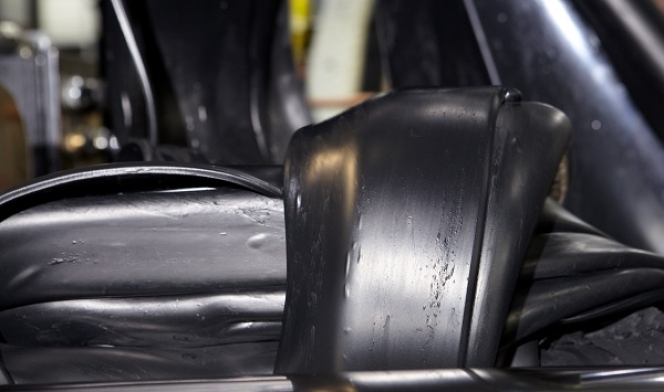
The German rubber industry is undergoing significant shifts, according to the German Rubber Industry Association (wdk) in its mid-2025 economic report. While order trends show improvement for the first time in years, domestic production continues to struggle, reflecting broader structural challenges.
High energy costs, excessive bureaucracy and rising labour expenses remain persistent hurdles, particularly for globally competitive firms. Although rising orders may boost annual sales slightly compared to 2024, domestic output is expected to decline by one percent. Many companies are relocating production abroad due to Germany’s worsening cost disadvantages.
The federal government’s ‘investment booster’ initiative has failed to inspire confidence, with only 27 percent of industry leaders anticipating positive effects. wdk President Michael Klein described this as an alarming sign, emphasising that businesses lack faith in current economic policies. He urged immediate relief measures rather than delayed solutions.
Klein also stressed the need for inclusive policymaking, criticising the government’s focus on large corporations while neglecting small and medium-sized enterprises (SMEs). He warned that without targeted support for these critical players, Germany risks losing its status as a key industrial hub for the rubber sector. The call for urgent action highlights growing concerns over the industry’s future viability in the country.
Comments (0)
ADD COMMENT