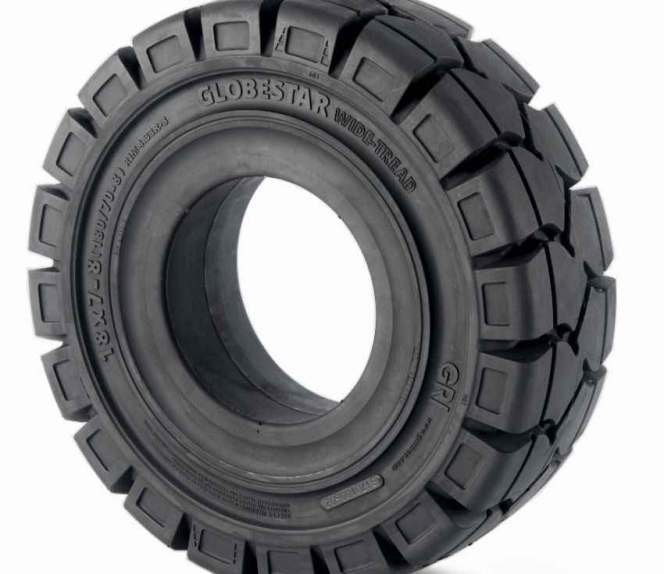
Like its peers, the Sri Lankan rubber industry has been hard hit by the COVID 19. However, the pandemics will bring some opportunities to the sector, believes Ravi Dadlani, Chairman of the Sri Lanka Association of Manufacturers and Exporters of Rubber Products (SLAMERP), and MD of CEAT Kelani Holdings. “The demand for PPE is high and will be sustained in time to come until COVID 19 is no longer a pandemic. Especially gloves and other wearables made of rubber will be a good area for the Sri Lankan rubber industry to focus on,” says Dadlani an interview with Tyre Trends.

How do you see the impact of COVID 19 on Sri Lanka’s rubber industry?
Sri Lanka, like all exporting countries, have been largely impacted. The shutdown has caused a tremendous loss both in terms of production and the subsequent shut down of countries resulting in the cancellation of orders widely across the tyre industry. We are concerned that the impact fully on the industry is still to be realised. We will, once the supply chain and the related industries come back online, be able to quantify the extent of the impact. We are however positive that the Sri Lanka rubber industry is poised to benefit from the need arising from the COVID 19 impact. Especially the demand for PPE is high and will be sustained in time to come until COVID 19 is no longer a pandemic. Especially gloves and other wearables made of rubber will be a good area for the Sri Lankan rubber industry to focus on. Also, the government suspension of importing of tyres is poised to increase demand for domestic manufacturers of tyres at least in the short term, which will be a boost to the local rubber industry. Impact on the loss of exports and the timings of the opening of overseas markets would be critical at this point.
The rubber industry has always been the country’s one of the main sectors and exporters. Do you think that the industry currently is being explored to its fullest potential?
There is a lot of potential for rubber in Sri Lanka. The need to increase the production of rubber through productivity improvements and the need to extend the rubber growing acreage is critical at this time. We have leading manufacturers of international repute and strong local manufacturers catering to export markets both in the tyre and gloves segments.
The country also has the potential to enter new markets and customer segments with new products. There is more that needs to be done in terms of R&D and technological collaborations to enter high-value rubber-based product segments. With major global brands producing in Sri Lanka, we have a greater ability to increase trading activity and improve international sales as a regional hub for the industry.
What kind of support do you expect from the government and industry-related bodies for the long term?
Firstly, the rubber sector was the first to benefit from the priority given by the government initiative to commence operations. The sector benefited by the fast track approval to be classified as an essential sector. We expect the government to continue to have consistency when it comes to policy matters. We are also seeing a strong support base coming in terms of the Board of Investment and the Export Development Board for the rubber cluster. We need to fast track the planned policy-based approach of increasing rubber production in the country through the rubber master plan, with incentives if need be for plantations to spearhead this initiative. Also, research and development on rubber yield increase, all-weather rubber tapping techniques need to be introduced with governments thrust towards increasing rubber production.
There should also be incentives for exporters to invest in high-value rubber product manufacturing. We expect the government to educate the smallholders with international best practices to manage the rubber crop for better yield and output through RDD & RRI as key government institutions. The industry prefers to buy more local rubber, but there is a shortfall every year vs the demand. We also need to drive the public-private partnership research & development and must invest more in laboratory and testing facilities to provide certifications that are required for the export markets within Sri Lanka. The Government will also need to look at domestic supply chain inefficiencies which may hold back on the growth potential of the industry.
When we talk about tyres, how does the Sri Lankan tyre industry make its mark globally, especially in the solid tyre segment?
Absolutely it does. Sri Lanka is considered market leaders in certain categories of the solid tyre export segment. There are the numbers of global and local companies operating out of Sri Lanka holding a good foothold in the global solid tyre market. The global rubber industry is worth around USD 400 billion, out of which 65% is the tyre industry, given this, we have a market that we can increase our supply of both off road and on-road tyres, Sri Lanka has aggressively ventured into the global pneumatic agriculture, Off-road and industrial tyre segment which is estimated at USD 44b. We are confident that this position of strength will be maintained in the future, too in these segments.
What are the challenges for tyre and rubber goods, especially for small and medium enterprises?
Key is the availability of rubber at consistent prices at the right quantities throughout the year. Currently, the industry is hampered with weather-related shortfalls in production coupled with plantations moving away from rubber and more profitable ventures depleting the total output. We consume 140,000 MT, and the local production is at 75,000 MT. Addressing these two areas will result in a stable supply of rubber for industries. It is very important that SMEs adopt technology and increase productivity and production to cater to the demand for rubber.
END
Zeon Develops Hydrophilic SBR For Winter Tyres
- By TT News
- July 16, 2025
Zeon Corporation has announced the development of Nipol BR1300, a novel hydrophilic styrene butadiene rubber (SBR) for winter tyres. Synthesised with a polybutadiene rubber base, the material delivers unprecedented hydrophilicity for tyre applications. Commercial production began in May 2025 at Zeon’s Tokuyama plant in Yamaguchi Prefecture.
As part of its strategic portfolio optimization, Zeon plans to phase out low-profitability products like ESBR-1 and NBR latex by 2026. However, it will continue manufacturing high-margin products, including ESBR-2, nitrile butadiene rubber and solution SBR. This shift underscores Zeon’s focus on advanced, value-driven rubber solutions.
- Covestro India
- CSIR-National Chemical Laboratory
- Circular Economy
- Polyurethane Waste
- Polyurethane Recycling
Covestro India Partners With CSIR-NCL To Pioneer Polyurethane Upcycling Solutions
- By TT News
- July 16, 2025
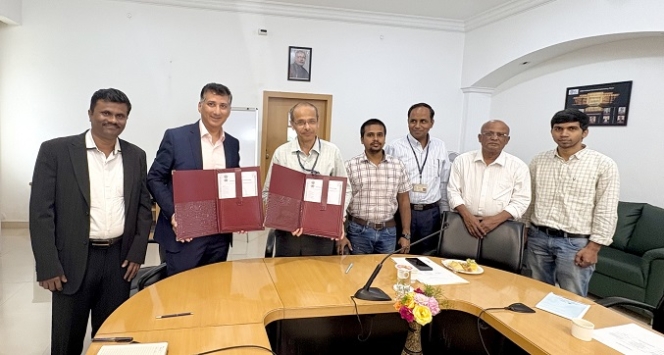
Covestro India has entered into a strategic collaboration with CSIR-National Chemical Laboratory (NCL) through an innovative CSR initiative focused on developing sustainable upcycling technologies for polyurethane waste. This partnership aims to overcome existing recycling limitations by transforming discarded polyurethane materials into valuable chemical feedstocks, potentially revolutionising the material's circular economy.
This collaboration underscores both organisations' commitment to environmental innovation, leveraging NCL's advanced research infrastructure and Covestro's market leadership to address critical gaps in plastic circularity. Current polyurethane recycling methods, predominantly mechanical with some emerging chemical processes, face substantial challenges including material degradation, high energy consumption and hazardous byproduct generation. The project seeks to develop commercially viable chemical recycling solutions that maintain material integrity while minimising environmental impact.
Polyurethanes, widely used in furniture, automotive parts and insulation, present unique recycling difficulties due to their complex molecular structure. Most end up in landfills after use, creating significant sustainability challenges. By combining Covestro's industrial expertise with NCL's seven decades of chemical research excellence, the partnership aims to create breakthrough upcycling technologies.
Avinash Bagdi, Director & Head of Sales & MD Solutions India & Projects – Tailored Urethanes, said, "This partnership strengthens our commitment to finding innovative solutions for polyurethane waste and directly supports Covestro's vision of becoming fully circular. By developing effective methods to upcycle polyurethanes, we're taking concrete steps towards creating a more sustainable future in line with our corporate vision of driving the transition to a circular economy."
Dr Ashish Lele, Director of NCL, said, "CSIR-National Chemical Laboratory is excited to partner with Covestro (India) in this groundbreaking initiative to develop novel chemical upcycling methods for polyurethane waste. The conventional and electrochemical strategies we're developing address the critical limitations of current recycling technologies and align perfectly with our shared vision of a circular economy. This collaboration represents a significant step towards sustainable plastic management in India and globally, with potential to transform polyurethane waste into valuable chemical resources."
Zeon Starts Construction Of Bench-Scale Facility For Sustainable Butadiene Production
- By TT News
- July 11, 2025
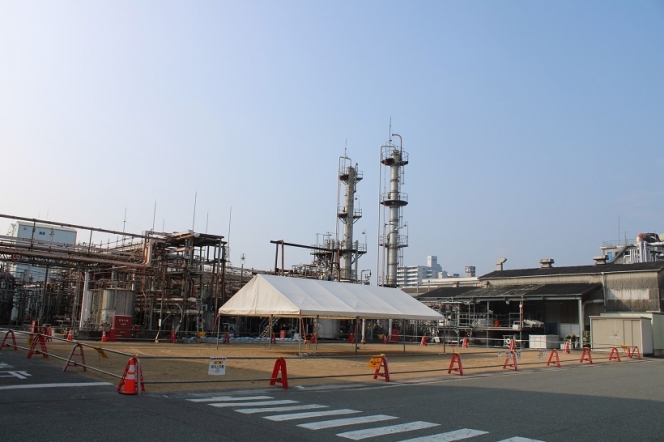
Zeon Corporation has begun building a pilot facility at its Tokuyama Plant in Shunan City, Yamaguchi Prefecture, to test a new method for efficiently producing butadiene from plant-derived ethanol. The demonstration plant, expected to start operations in 2026, will supply butadiene for manufacturing trial batches of polybutadiene rubber, bringing the company closer to commercialising this sustainable production process.
This project is a key part of a joint initiative between Zeon and The Yokohama Rubber Co., Ltd. to develop eco-friendly methods for producing butadiene and isoprene from renewable sources, with full-scale adoption targeted for the 2030s. Under the collaboration, Zeon will produce butadiene rubber at the new facility, while Yokohama Rubber will use the material to create experimental tyres and conduct performance testing. The data collected will help refine the technology ahead of larger-scale trials. The companies aim to finalise the production process by 2030 using an expanded pilot plant, with plans for industrial-scale commercialisation by 2034.
A ceremonial groundbreaking event took place on 10 July 2025, with 33 attendees, including local government officials from Yamaguchi Prefecture and Shunan City, construction partners and Zeon executives such as Chairman Kimiaki Tanaka and Tokuyama Plant Manager Akira Honma. The gathering included traditional safety prayers for the construction phase, marking the official start of this sustainability-focused industrial project.
Rice Husk Ash Revolution: Continental's Eco-Friendly Tyre Fillers
- By TT News
- July 11, 2025
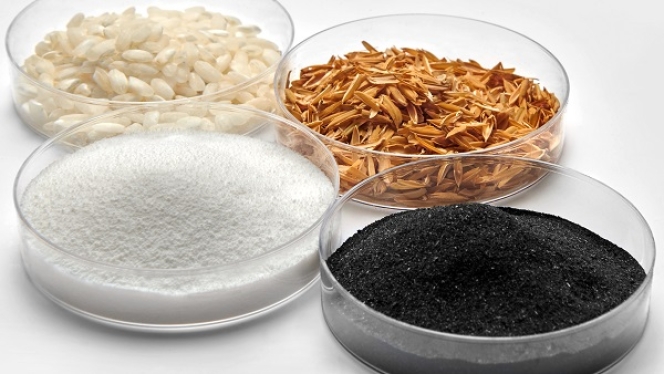
Continental is increasing its use of renewable and recycled materials in tyre production, aiming to exceed 40 percent by 2030 while maintaining high safety and performance standards. In 2024, these materials accounted for 26 percent of tyre composition, with a projected 2-3 percent increase in 2025. Key to this shift are carbon black and silica – essential fillers that enhance durability, grip and braking performance.
Silica, a critical component for optimising grip and minimising rolling resistance, is traditionally derived from quartz sand. However, Continental now obtains silica from rice husks, an agricultural by-product of risotto rice production. This innovative approach not only repurposes waste but also requires less energy than conventional methods. Partnering with manufacturers like Solvay in Italy, Continental integrates rice husk-derived silica across its entire tyre portfolio. Silica has been a game-changer in tyre technology for decades, significantly improving safety and energy efficiency. Its use in tread compounds has contributed to a nearly 50 percent reduction in braking distances while also lowering rolling resistance, thereby reducing fuel consumption and CO₂ emissions.
Carbon black, another vital material making up to 20 percent of a passenger car tyre's weight, is being sourced through sustainable alternatives. Continental employs three innovative methods: bio-based carbon black from tall oil (a paper industry by-product), recycled carbon black from pyrolysis oil derived from end-of-life tyres and a direct recovery process that extracts carbon black from used tyres via pyrolysis. The company collaborates with suppliers like Orion Engineered Carbons and Tokai Carbon, utilising different carbon black variants tailored to specific tyre components, such as sidewalls and treads. Through the mass balance approach, Continental substitutes fossil-based raw materials with bio-based or recycled alternatives without altering existing production processes.
Additionally, Continental has partnered with Pyrum Innovations to advance tyre recycling through pyrolysis, a process that recovers carbon black from end-of-life tyres for reuse. While currently applied in forklift tyres, efforts are underway to adapt this recycled carbon black for broader tyre applications, ensuring compliance with performance and safety standards. These initiatives underscore Continental’s dedication to sustainable innovation, demonstrating how eco-friendly materials can enhance both tyre performance and environmental responsibility across the value chain.
Jorge Almeida, head of Sustainability at Continental Tire, said, “Innovation and sustainability go hand in hand at Continental. Using silica from the ashes of rice husks in our tyres shows that we are breaking completely new ground – without compromising on safety, quality or performance.”
Comments (0)
ADD COMMENT