PHYSICS BEHIND RUBBER TRIBOLOGY
- By 0
- May 04, 2020
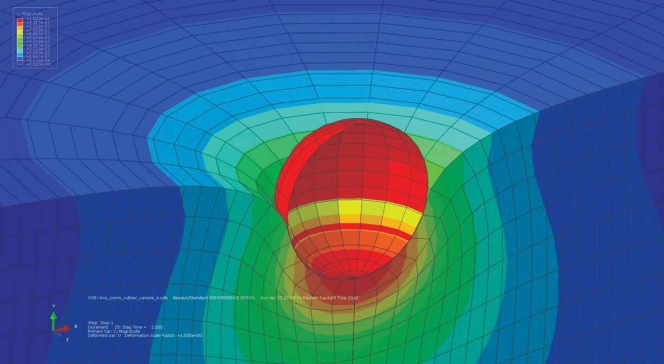
By Sunish Vadakkeveetil, Mehran Shams Kondori, and Saied Taheri
Center for Tire Research (CenTiRe), Virginia Tech
Rubber, mainly because of its viscous nature, is a widely used material for most contact applications such as, seals, tyres, footwear, wiper blades, bushings etc. The material possesses the property of both a liquid (viscous) and a solid (elastic). Hence, rubber frictional losses at the contact interface is classified into three mechanisms as shown in Figure 1. Hysteresis (μ_hys ) – Energy dissipated due to internal damping of rubber caused by undulation in the surface. Adhesion (μ_adh ) – Due to intermolecular or Vander Waals attraction at the contact interface. It vanishes in the presence of contaminants or lubricants on the surface. Viscous (μ_visc ) – Due to hydrodynamic resistance caused by the fluid in the contact interface. It mainly occurs under the presence of lubricant or fluid in between the contact interface.



Friction as a concept has evolved, as shown in Figure 2 from a simple empirical relation, developed by Amonton’s (1699) and Columb (1785) to more complex representations by considering these different mechanisms of friction. Initial experimental observations by Bowden and Tabor [1] observed the microscopic behaviour of the contact and obtained that the real area of contact is only a part of the nominal contact area. Grosch & Schallamach [2] performed experimental observation to determine the influential factors and obtain a relation between temperature and velocity-dependent friction to frequency-dependent viscoelastic behaviour. Savkoor[3] considers the frictional losses due to adhesive mechanism at the contact interface using a rudimentary theory where the interaction is considered as a series of processes from the growth of contact area in the initial stage to initiation and propagation of crack in the final stage.
Heinrich [4] developed an analytical representation to estimate the hysteretic component of friction by considering the energy losses at the contact interface to the internal damping of rubber from the undulations of the surface. The energy loss thus obtained is related to the frictional shear stress by the energy relation given by Eq. (2).
ΔE=∫d^3 x dt u ̇ . σ (1)
σ_f=ΔE/(A_0 v t) (2)
Persson and Klüppel [5] extended the theory to consider the effect of the surface roughness by assuming the surface to behave as a fractal nature and obtaining the total energy loss being the sum over the different length scales. Klüppel considers the GW theory to consider the contact mechanics where Persson developed a stochastic based contact mechanics theory assuming the rubber deformations to follow the surface asperities, the results are as shown in Figure 3. To consider the actual deformation profile of rubber, an affine transformation approach [6] is considered to obtain the actual deformation of rubber contact. The results are as shown in Figure 4.


In addition to analytical methods, computational approaches are also considered to estimate deformation behaviour of a rubber block on a rough substrate (Figure 5). The numerical model [7] is validated using indentation experiment and compared against a single asperity model as shown in Figure 6. This is later being extended to obtain friction and wear characteristics of rubber at the contact interface by considering the deformations at the contact interface and obtaining the frictional force [5], [8].



Figure 6: FE Model Of Single Asperity Model & Comparison Of Results With Experimental & Analytical Approach
Wear is mainly due to the frictional shear stress generated at the contact interface leads to energy dissipation at the rubber – substrate contact interface that is either transformed into heat or responsible for crack initiation and propagation eventually leading to material removal. The major contribution of the wear occurs either due to the interaction of smooth asperity and rubber surface (adhesive wear), Figure 7 (a) instantaneous tearing of rubber by sharp asperities (abrasive wear), Figure 7 (b) or due to repeated cyclic contact stress (fatigue wear, Figure 7 (c)).
Due to the importance and complexity of the wear problem, it has been a vital topic of interest studied by many researchers [2]. Numerical techniques and empirical approaches have seen their light in the midst of the expensive and cumbersome experimental observations [9], [10]. Archard’s law states that “the volume rate of wear (W) is proportional to the work done by the frictional forces” as given by Eq. (3), where τ_f is the frictional shear stress and v is sliding velocity.
W∝τ_f v (3)




In the case of road surfaces, the removal of rubber particles can be considered as a process of nucleation and propagation of crack like defects until it is detached to form a wear particle, as shown in Figure 8. Based on this mechanism of crack propagation, a physics-based theory assuming the crack propagates (Figure 9 & Figure 10) from already present defects or voids on the rubber surface was considered and then later compared with experimental methods performed using Dynamic Friction Tester (Figure 11) [6], [11], [12]. Future studies are being performed using analytical and computational approached to estimate the wear characteristics of a rubber material considering damage mechanics [8] and crack propagation theory considering the effect of surface roughness. An experimental technique is also being developed based on the Leonardo Da Vinci concept to experimental test the friction and wear characteristics of a rubber block under pure sliding.
References:
[1] D. Bowden, F. P., & Tabor, The friction and lubrication of solids. Oxford university press., 2001.
[2] A. Gent and J. Walter, The Pneumatic Tire, no. February. 2006.
[3] A. R. Savkoor, “Dry adhesive friction of elastomers: a study of the fundamental mechanical aspects,” 1987.
[4] H. Gert, “Hysteresis friction of sliding rubber on rough and fractal surfaces,” Pochvozn. i Agrokhimiya, vol. 25, no. 5, pp. 62–68, 1990.
[5] S. Vadakkeveetil, “Analytical Modeling for Sliding Friction of Rubber-Road Contact,” Virginia Tech, 2017.
[6] A. Emami and S. Taheri, “Investigation on Physics-based Multi-scale Modeling of Contact, Friction, and Wear in Viscoelastic Materials with Application in Rubber Compounds,” Virginia Tech, 2018.
[7] S. Vadakkeveetil, A. Nouri, and S. Taheri, “Comparison of Analytical Model for Contact Mechanics Parameters with Numerical Analysis and Experimental Results,” Tire Sci. Technol., p. tire.19.180198, May 2019.
[8] S. Vadakkeveetil and S. Taheri, “MULTI – LENGTH SCALE MODELING OF RUBBER TRIBOLOGY FOR TIRE APPLICATIONS,” Virginia Tech, 2019.
[9] K. R. Smith, R. H. Kennedy, and S. B. Knisley, “Prediction of Tire Profile Wear by Steady-state FEM,” Tire Sci. Technol., vol. 36, no. 4, pp. 290–303, 2008.
[10] B. W. and R. N. D. Stalnaker, J. Turner, D.Parekh, “Indoor Simulation of Tire Wear: Some Case Studies,” Tire Sci. Technol., vol. 24, no. 2, pp. 94–118, 1996.
[11] A. Emami, S. Khaleghian, C. Su, and S. Taheri, “Comparison of multiscale analytical model of friction and wear of viscoelastic materials with experiments,” in ASME International Mechanical Engineering Congress and Exposition, Proceedings (IMECE), 2017, vol. 9.
[12] M. Motamedi, C. Su, M. Craft, S. Taheri, and C. Sandu, “Development of a Laboratory Based Dynamic Friction Tester,” in ISTVS 7th Americas Regional Conference, 2013.
Zeon Board Approves Higher Budget For Cyclo Olefin Polymer Facility
- By TT News
- September 03, 2025
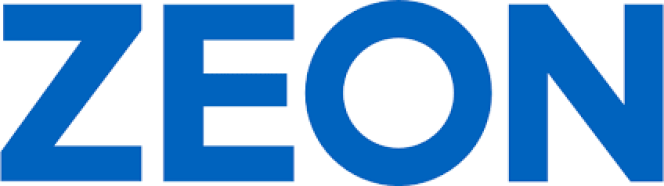
Following a resolution by its Board of Directors on 29 August 2025, Zeon Corporation has formally revised the total investment for its upcoming cyclo olefin polymer (COP) production plant. The new total investment is now projected to be approximately JPY 78.0 billion (approximately USD 525.70 million), a significant increase from the initial estimate of approximately YEN 70.0 billion (approximately USD 471.77 million) announced in June 2024.
This upward revision is attributed to anticipated increases across key construction areas, including rising costs for labour, raw materials and equipment. The updated financial framework incorporates both confirmed and projected cost escalations to ensure accurate budgeting. Zeon Corporation intends to fund the entire investment through a combination of internally generated capital and loans from financial institutions.
The new facility remains on schedule for completion in the first half of fiscal year 2028. Due to this timeline, the substantial investment is not expected to materially affect the company's consolidated financial results for the fiscal year ending 31 March 2026. The project is a central pillar of the company’s medium-term business strategy, identified as a major future growth driver.
The decision to proceed with the plant underscores the strong market outlook for Zeon’s cyclo olefin polymers. These advanced materials are prized for their superior optical clarity, extremely low water absorption and high purity. While already established in applications like optical films and lenses, demand is growing rapidly from the medical and semiconductor industries. By expanding its production capacity, Zeon aims to capitalise on this robust and expanding demand, thereby strengthening its market position and enhancing its corporate value over the medium to long term.
Kraton And International Paper Finalise Agreements For Operational Continuity In Savannah
- By TT News
- September 02, 2025
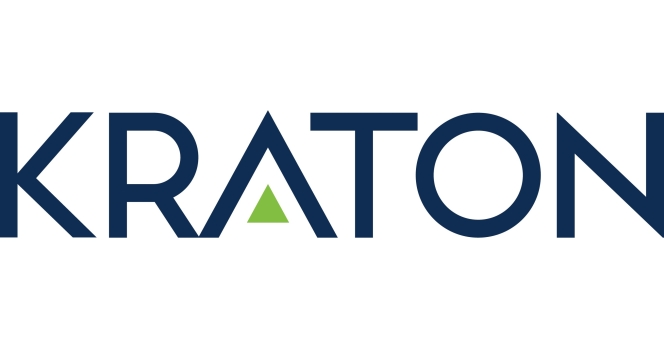
In a move to ensure operational continuity, Kraton Corporation has finalised service agreements with International Paper for its Savannah, Georgia facility. As a leading global producer of specialty polymers and biobased pine chemical products, Kraton will continue to receive essential site services from International Paper, a leader in sustainable packaging. This arrangement guarantees an uninterrupted production and supply of critical pine chemicals for the global market.
The agreements solidify both companies' shared commitment to reinforcing the pine chemicals value chain and providing reliable service to their customers. For Kraton, this partnership provides stability as it makes strategic infrastructure investments at the Savannah plant. These planned upgrades are designed to facilitate the site's long-term independent operations, supporting Kraton’s broader focus on business resilience and future growth. This initiative reinforces Kraton's position as a global leader in delivering high-performance, sustainable, bio-based solutions.
Minco van Breevoort, President, Kraton Pine Chemicals, said, “Securing this agreement reinforces our unwavering commitment to our customers and the pine chemicals industry. It’s business as usual. Our teams are fully aligned to ensure reliable operations, and this agreement provides continuity of supply to pine chemical markets as we invest in our long-term capabilities.”
Chris Roeder, Vice President and General Manager, Pine Chemicals and Low Carbon Solutions, International Paper, said, “We are pleased to renew and extend our partnership with Kraton. This arrangement confirms our long-standing relationship with Kraton and our commitment to being a reliable, long-term partner to Kraton and participant in the pine chemicals markets for years to come.”
Retreading’s Stubborn Struggle
- By Gaurav Nandi
- August 29, 2025
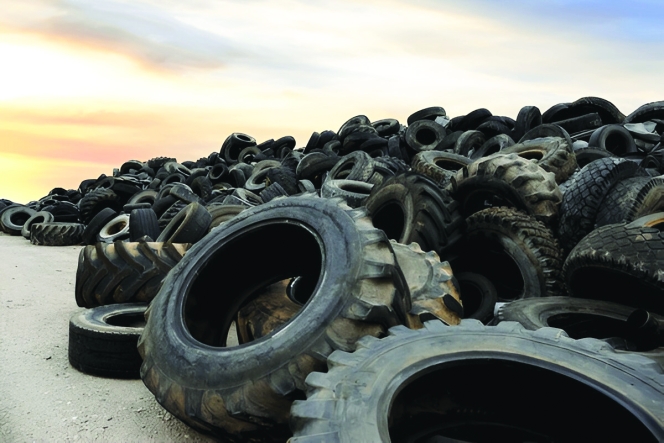
Despite decades of presence and proven sustainability benefits, the global truck tyre retreading industry remains mired in perception problems and systemic inertia. As raw material costs rise and environmental pressures mount, retreading should be a no-brainer. Yet, it continues to be sidelined by outdated mindsets, customer ignorance and a lack of cohesive industry messaging. Tirecore CEO Garry Drisdelle, in a candid interview with Tyre Trends, paints a picture of a sector at risk – not because it lacks value, but because it has failed to communicate it. The stakes, he warns, are too high for complacency.
Despite decades of existence, the retreading industry still wrestles with fundamental challenges across the world – not least the stubborn perception among customers and stakeholders about the true value of retreaded truck tyres. Tirecore Chief Executive Officer Garry Drisdelle pulls no punches in diagnosing the sector’s issues and outlining the uphill battle ahead.
Speaking to Tyre Trends, he said, “Tirecore is primarily a supplier of quality truck tyre casings to the retread industry. But while retreading should logically form the cornerstone of sustainable tyre use, the industry remains far from mainstream acceptance.”
“Educating the customers really as to how much upcycling, how much can we save – it’s beyond the pennies or pounds you save on the initial purchase,” Drisdelle said. Yet, frustratingly, many customers remain fixated on upfront costs instead of the total lifecycle value of a tyre.
This fixation, he implies, represents a systemic failure within the industry. “The industry has to do a better job towards educating the consumers, which primarily are fleet owners, beyond the initial purchase,” said Drisdelle. The inability to shift consumer mindset threatens to leave retreading as a niche rather than a necessity.
Tirecore positions itself primarily as a global supplier of high-quality truck tyre casings to the retread industry, operating across markets that include the United States, Canada and India. Rather than manufacturing or retreading tyres directly, the company serves as a critical node in the circular economy of commercial tyres, ensuring that valuable casings find extended life through retreading.
“We are in the business of preserving 85 percent of the tyre components existing material’s value saving valuable resources,” said Drisdelle.
The company’s operational model is rooted in the principle of upcycling over replacement, focusing on longevity and material reuse rather than disposability. While Tirecore’s precise logistical affiliations remain unspecified, its strategic direction is clearly aimed at aligning with sustainability mandates and evolving global market demands.
DISPOSABLE TREATMENT
Drisdelle highlights a critical contradiction. Tyres are one of the most safety-critical components on the road, yet they are taken for granted at a staggering scale. “Picture a truck is rolling down the highway at 100km/h pulling 20,000 kilogrammes of freight, riding on just 6-8-10 rolling rubber contact points. Tyres are one of the most critical transportation components, yet we treat them like disposable goods. How taken for granted is that product?”
Even as raw material prices surge and truck tyre costs climb, the entrenched perception treats tyres as disposable consumables. “We need to reframe the conversation – a tyre should be seen as an asset and not a consumable,” Drisdelle emphasises.
This disconnect reveals deeper issues prevalent within the industry. Retreading has not been effectively communicated as a financial and environmental beneficial in the long tome. Moreover, legislative inconsistency and lack of incentives for the industry as a whole is a deterrent that needs to be addressed immediately.
Drisdelle insists that retreading should be the environmental rallying point for the sector. “We have 85 percent of the material in the original product that is quite capable of being reprocessed and upcycled many times,” he said.
He contrasts upcycling favourably with recycling, which he argues requires more energy and effort than the original production process, especially in plastics and other materials: “By the time you just recycle something, the energy to recycle it is more than the process.”
Yet these arguments come with an implicit critique that the industry has failed to effectively translate this environmental rationale into a compelling value proposition for customers and regulators alike.
LEGISLATIVE MOMENTUM
Drisdelle points to potential legislation requiring truck tyres to be recyclable or retreadable as a possible catalyst for change. “Picture if legislation comes out that you’re not allowed to sell truck tyres unless they’re recyclable from their ingredients unless they’re retreadable,” he noted.
However, he quickly tempers this with realism stating, “We can never get to zero. That’s a cool little marketing thing but it’s an impossibility in the world of physics and science.”
This admission highlights the gap between aspirational sustainability goals and practical realities, a gap that leaves retreading vulnerable to accusations of greenwashing or insufficient progress.
ADAPT OR STAGNATE
Looking to the future, Drisdelle’s plan is pragmatic but cautious. “Our future plans are to keep up with the market demand, to evolve as the market evolves. Pivot and prosper,” he said.
Such a measured approach reflects the uncertainty and fragmentation within the industry. The promise of retreading remains strong, but without decisive action on education, regulation and innovation, the sector risks losing ground to cheaper, new tyres or alternative technologies.
The recurring theme throughout Drisdelle’s commentary is education, or rather, the lack of it. “The education of the fleet owners is primary to everything. The education of the industry to build a better tyre is somewhat secondary,” he stated.
This stark admission speaks volumes. Despite retreading’s environmental and economic advantages, a fundamental communication failure continues to hobble the industry.
Drisdelle points out the irony stating, “Without a widespread cultural shift in perception, retreading will struggle to move beyond a cost-saving niche for price-sensitive fleets to a mainstream standard.”
Drisdelle’s blunt assessment of the retread industry reveals a sector caught between its potential and its persistent shortcomings. Tirecore’s role as a global supplier to retreaders is clear but the wider challenge remains.
Without significant progress on education and regulatory backing, the retread industry risks remaining on the margins, overshadowed by the convenience of new tyres and the pressures of market inertia.
Retreading’s promise is substantial. But, as Drisdelle’s comments underscore, fulfilling that promise demands a candid reckoning with the industry’s educational failures and a relentless push for change or face stagnation in a rapidly evolving tyre market. n
India’s Tyre Recycling Industry Enters New Era With Gujarat’s Green Light To Continuous Pyrolysis
- By Gaurav Nandi
- August 28, 2025
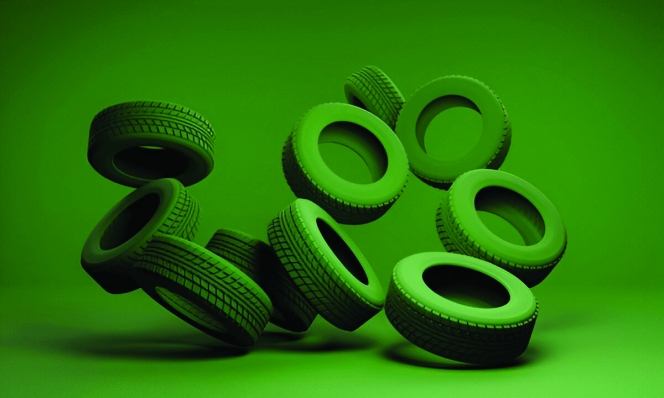
India’s tyre recycling sector, long plagued by fragmented operations and lax compliance, is undergoing a critical overhaul. With Gujarat’s recent approval for continuous pyrolysis plants, the industry is moving decisively towards cleaner, scalable and regulation-driven solutions. This shift signals more than a technological upgrade and it’s a rebuke of outdated batch systems and a call for formalisation, traceability and environmental accountability. As global demand for sustainable materials rises, India’s pivot positions it as a potential leader in circular economy practices. In conversation with TRRAI President Chetan Joshi, we explore how this development could redefine the future of tyre waste management at home and abroad.
India’s tyre recycling sector is on the cusp of a transformational shift with the Gujarat Pollution Control Board (GPCB) approving the establishment of continuous pyrolysis plants in the state. The move marks a significant departure from traditional batch-based tyre processing systems, promising to boost efficiency, environmental compliance and resource recovery at an industrial scale.
“This shift is nothing short of revolutionary,” said President of the Tyre and Rubber Recyclers Association of India (TRRAI) Chetan Joshi. “We’re moving from outdated, fragmented batch operations to streamlined, automated continuous pyrolysis systems. This is going to uplift the entire industry, from cleaner emissions to higher resource recovery, better traceability and serious investor interest. It sets a new national standard and will accelerate formalisation, industrial-scale operations and a far more sustainable approach across India.”
The approval has been met with optimism by recyclers and environmental advocates alike as it signifies a structural change in how end-of-life tyres will be handled in India, which is home to more than 1.8 million tonnes of tyre waste annually.
The Gujarat model mandates stringent adherence to environmental standards, particularly concerning air quality and emissions. Continuous pyrolysis plants approved under the new framework are required to incorporate top-tier pollution control mechanisms.
“We see compliance not as an obligation but as a core design principle. Our plants are being built with advanced air pollution control devices (APCDs), real-time emissions monitoring and automation that ensures consistent performance. We’re aligning with both GPCB and CPCB regulations through pro-active design, third-party audits and integrating global best practices. It’s not just about meeting today’s standards but staying ahead of tomorrow’s,” said Joshi.
The approach reflects a broader shift in the recycling sector, where regulatory compliance is no longer viewed as a hurdle but as a strategic advantage and market differentiator.
Industrial scale
Under the new directive, each continuous pyrolysis facility must operate at a minimum capacity of 60 tonnes per day (TPD). This scale reflects the government’s push to industrialise tyre recycling and eliminate inefficient, informal practices.
“Scaling to 60 TPD is a serious industrial commitment and it means heavy investment in automation, utilities, safety systems and logistics. But it’s also the only way forward. India generates over 1.8 million tonnes of end-of-life tyres annually. This scale allows us to handle the problem responsibly while creating traceable and economically viable recycling ecosystems,” Joshi said.
With India’s growing automotive base, the urgency to develop sustainable, high-capacity recycling infrastructure has never been higher.
One of the key advantages of continuous pyrolysis lies in its outputs that include valuable petrochemical byproducts like pyrolysis oil, sustainable fuels and recovered carbon black (rCB). These materials are increasingly in demand across a range of industries, from rubber manufacturing to renewable energy.
“These by-products are entering a new phase of global relevance. Recovered carbon black is being adopted in rubber, plastics and even pigments. Pyro oil, when upgraded, is a viable alternative fuel. We’re actively engaging with global buyers and certifiers to standardise and integrate these outputs into international supply chains. The world is ready for sustainable alternatives and it’s up to us to deliver with consistency and quality,” averred Joshi.
India’s entry into this global supply chain positions it not just as a recycler of waste but as a producer of sustainable industrial materials.
Circular economy
TRRAI views this milestone as more than an environmental success. It’s a step towards realising India’s vision of a circular economy, where tyre waste is fully reintegrated into the production cycle.
“We aim to be more than recyclers. We want to be circular economy enablers. That means building systems where tyre waste is traceable from collection to output, where value is recovered and re-injected into the economy. We’re developing collection infrastructure, digital traceability and offtake agreements with industries globally. This is not just about waste; it’s about resource optimisation and environmental stewardship,” Joshi explained.
Such a shift could significantly reduce the country’s carbon footprint while fostering job creation and industrial growth.
Despite the enthusiasm, industry leaders acknowledge that challenges remain, particularly in terms of adoption among legacy operators and infrastructure gaps.
“The biggest challenge is inertia as many operators are still working in the unorganised sector with outdated setups. Then there’s infrastructure as a hurdle as tyre collection networks are underdeveloped in many parts of India. To overcome this, we’re advocating policy changes, investing in reverse logistics and training the workforce. Regulatory clarity and enforcement will be key and we’re working closely with industry associations and government bodies to drive this,” said Joshi.
Stakeholders believe that education, investment and enforcement will be pivotal to ensuring widespread transition to continuous pyrolysis systems.
Global trends
Globally, countries like those in Europe and North America have already adopted advanced tyre recycling technologies. But Joshi believes India has a unique opportunity to leapfrog older systems and build world-class facilities from scratch.
“Europe and North America have a head start, especially in policy frameworks and end-use applications. But India’s opportunity lies in scale and adaptability. We can leapfrog legacy systems and build efficient, tech-driven plants from the ground up. If we get the ecosystem right – collection, compliance and capital – we can set new benchmarks, not just catch up. India could become a global hub for tyre recycling technology,” he said.
The industry’s fast pace of development combined with India’s manufacturing and engineering capabilities could make the country a case study in sustainable industrial transformation.
Innovations in emission reduction
In line with global best practices, TRRAI and its partners are integrating innovations to ensure safety and minimal environmental impact.
“We’re integrating closed-loop systems, AI-driven control logic and multi-stage gas cleaning technology. Real-time emissions data will be available both internally and to regulators. Safety protocols are built into every operational layer, from material feeding to shutdown procedures. We’ve also prioritised workforce training and regular third-party safety audits. The goal is to operate with zero compromise on health or the environment,” Joshi explained.
Such innovations are crucial not only to maintaining regulatory compliance but also to building public and investor confidence.
The entry of advanced technologies is expected to catalyse foreign investment and technical collaboration.
“Our approach is partnership-driven. We’re already working with European and Australian technology providers and are in discussions with institutional investors. We see India as a platform for co-creation, where global IP meets local scale and agility. Through industry associations like TRRAI, we’re building collaborative networks to ensure knowledge sharing, investment facilitation and joint innovation,” Joshi noted.
This strategy could help India become a global innovation hub for recycling technologies applicable across other emerging markets.
The vision
Looking to the long term, the industry’s goals extend far beyond domestic waste management. TRRAI envisions exporting its model to developing nations facing similar challenges.
“Our vision is bold but simple. It is to create a fully circular, scalable and replicable tyre recycling ecosystem. India should not only solve its own tyre waste crisis but become a global model for how emerging markets can tackle resource recovery. We see this model being exported to Southeast Asia, Africa and Latin America. With continuous pyrolysis, India can move from reactive recycling to proactive resource management on a global stage,” Joshi concluded.
As Gujarat lights the way with its approval of continuous pyrolysis plants, India’s tyre recycling sector is poised to become a beacon of innovation and sustainability – one that could shape the future of global recycling practices. n
Comments (0)
ADD COMMENT