TYRE DEBRIS IN AQUATIC ENVIRONMENT: THE NEW BLACK?
- By Louise Lynn Halle*
- August 26, 2020
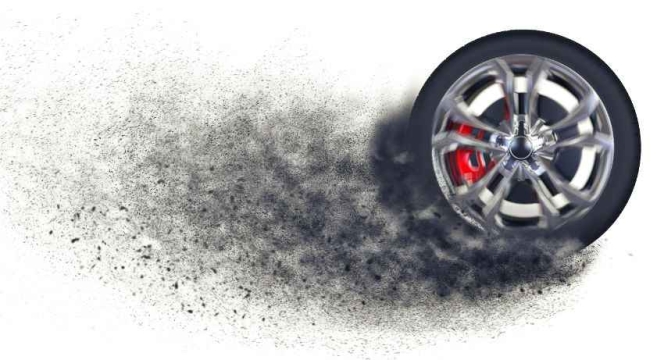
Recently, models on the fate of tyre wear particles (TWPs) have estimated that 18% of TWP emissions are transported from roads to freshwater bodies and approximately 2% are led out to estuaries and then marine habitats. What then happens to the remaining 16% of TWP emissions left in the freshwater compartment is not yet clear
_0.jpg)
at Roskilde University, Department of Natural Science and Environment, Denmark,
with funds from Danish Environmental Analysis
The presence of tyre wear particles (TWP) in the aquatic environment is considered an emerging contaminant, and one that has gained increasing interest during the past few years. Although the presence of TWPs in the environment is given greater attention these days, TWPs have probably been present since the dawn of the pneumatic car tyre production in the late 19th century. The first scientific report of tyre dust identification along a roadside was published in 1961. Different perspectives have since been applied to this field of research and almost decade by decade shifted foci from degradation patterns to heavy metal release, to impacts of scrap tyres on the aquatic environment and leaching of chemicals from tyres. More recently, research within this field has been directed towards repurposing scenarios using crumb rubber in turf fields and playground material. Finally, in the 2010s, micronised tyre rubber has become grouped with other polymer debris and hence become part of the polymer landscape usually referred to as ‘microplastics.’ TWPs are considered to represent the majority of microplastics (or polymer debris) in the environment, and the newest calculation on the wear of tyres is estimated at 0.81 kg per person per year.
Now, looking at TWPs through the lens of microplastic pollution, research and information from the microplastics field are very well applicable to TWPs in many instances. With this new perspective of TWPs, increasing awareness of possible adverse effects in the environment follows - how do TWPs distribute in the different environmental compartments (soil, air, sediment, water and biota (living organisms)) and how do TWPs behave when exposed to different abiotic factors in these environmental compartments. For example, UV-radiation or pH, temperature and salinity differences could affect TWPs, but to what degree? A recent paper on this very subject concluded that particularly temperature and mechanical stress could influence the toxicity of TWPs. The focus of tyre production and function have seemingly always been directed towards maximising the three hallmarks: grip, wear and rolling resistance, and rightfully so, but somewhere along the road we forgot to consider where tyre abrasion actually disappears to. Luckily, some scientists already thought of this and today we can begin to lay the foundation to our collected TWP knowledge, based on the available scientific literature.
From roads to water
Research shows that the minority of TWPs end up in the airborne fraction (0.1-10%) and recently TRWPs have been assessed to contribute a low risk to human health in the particulate matter (PM) PM2.5 and PM10 range. So, where to find the remaining 90.0-99.9% of tyre debris emissions? Early research on particulate distribution showed a decreasing concentration of TWPs with increasing distance from the road. From there, TWPs are expected to wash off during rainfalls, transporting them to different environmental compartments. Recently, models on the fate of TWPs have estimated that 18% of TWP emissions are transported from roads to freshwater bodies and approximately 2% are led out to estuaries and then marine habitats. What then happens to the remaining 16% of TWP emissions left in the freshwater compartment is not yet clear and more research is needed to answer this question.
Aquatic organisms living in the water column or the sediment can interact with TWPs in their natural habitats during this particle transportation through freshwater to the marine environment. Although there are no scientific references on field observations of TWP ingestion by aquatic biota yet, few recent observations of this behaviour under controlled laboratory settings have been reported. In 2009 the first observation of the water flea, Daphnia magna, ingesting TWPs was described in the scientific literature and only two years ago the first photos were published showing ingestion of TWPs in the benthic amphipod Gammarus pulex following sediment exposure. Shortly thereafter photos of TWP ingestion in the amphipod Hyalella azteca and opossum shrimps from the mysidae family followed after water-only exposures, and most recently freshwater and marine fish species have been documented ingesting TWPs under laboratory conditions.
The recent focus on particulate effects of TWPs on biota is still in its infancy and the latest development in this field investigates the possible effects of both the particulate fraction and the leachate fraction. The leachate fraction is the suite of chemicals that leach out from TWPs to the surrounding water. Previously, tyre toxicity investigations in the aquatic environment revolved solely around the leachate fraction, which has been the primary focus over the last 30 years. Among the first papers the effect of whole tyre leachate was investigated showing worn tyre leachate to exhibit greater toxicity than leachate from a pristine tyre to rainbow trout. Furthermore, decreasing toxicity was observed with increasing salinity indicating that salinity either influences the leachability of toxic constituents or that an interaction of salts and toxic chemicals is present. Exposure of shredded tyre chips to different bacteria likewise showed a correlation between decreasing toxicity and increasing salinity, concluding that tyre leachate is likely to be a greater threat to freshwater habitats than to estuarine or marine habitats.
Toxicity pattern

Further testing of TWPs and leachate on a freshwater species recently showed a dissimilar toxicity pattern when comparing acute toxicity responses of TWPs or leachate. Here, the amphipod H. azteca was exposed to either TWPs in freshwater or the leachate fraction alone, i.e. with no particulates present. This showed that leachate was more toxic in lower concentrations, presumably because dissolved chemicals are more bioavailable. Although, at higher concentrations, the particle fraction of TWPs became more toxic. This phenomenon very well describes the complexity and discrepancies when working with TWPs in the aquatic environment. It is not just a question of determining toxicity of a single chemical under controlled settings, but rather investigating a mixture of many chemicals in changing ambient environments. This complex matrix of polymer and chemicals can be more or less bound to the particle, which in itself might have adverse effects. However, the particle could also function as a vessel, containing chemicals and making them more or less bioavailable depending on the surrounding environment. Discovering exactly which chemicals leach out under different exposure scenarios, and most importantly, what of that is actually bioavailable to aquatic living species is the more interesting question to answer.
Due to the amorphous nature of rubber, end-of-life tyres (ELTs) have been used as leachate collection material and been used to collect polycyclic aromatic hydrocarbons (PAHs) and metals from contaminated waters. This discrepancy between the different TWP uses that in some cases could deem toxic and have adverse effects but at the same time might serve to mitigate other environmental issues is a great conflict of contradictory traits. Now, we need to unravel exactly when these contradictory traits are possibly affecting aquatic environments negatively and when these traits might be used for our advantage.
So how do scientists quantify TWPs and chemical constituents or ‘biomarkers’ from TWP leachate in water? The quick answer is that no tried and tested procedure is more right than any other now, we simply do not have conformity or guidelines on how to do this. Especially when looking to find particulates from tyre debris, as this is not usually detected when investigating for other polymer debris e.g. microplastics. Therefore, it is expected that the total amount of microplastics has been underestimated due to the lack of data from TWPs, which make up a large part of the estimated microplastic load worldwide and have not been reported on a regular basis. A multitude of methods have been used to estimate TWP emissions by measuring the concentration of chemicals in samples, with more or less success over the years. The biomarkers that have been used to determine TWP concentration most successfully include quantification of benzothiazoles and zinc. Both chemicals are used as part of the vulcanisation process and are also ubiquitous in nature. They are used for manufacturing of other materials, but specific versions can be attributed mainly to tyre manufacturing and are thus the most reliable compounds to measure.
How this emerging field of tyre ecotoxicology will progress ultimately depends on cooperation between different stakeholders having a common goal to pursue. The one thing that we can probably all agree on, is the need for tyres and other rubber products in our society. How we then fill that need, and what future decisions we make to maximise our understanding of the possible negative implications of TWPs in the aquatic environment is of paramount importance. Our job now is to continue our research within this field and ultimately prevent excess and unnecessary pollution of the water bodies that we all depend on, in a manner that stays true to both the environment and our need for safe and reliable tyres.
*The author is a PhD student in Environmental Biology at Roskilde University, Department of Natural Science and Environment, Denmark, with funds from Danish Environmental Analysis
References
1. Thompson. Identification of vehicle tyre rubber in roadway dust. Am Ind Hyg Assoc 27, 488–495 (1966).
2. Lassen, C., Hansen, S.F., Magnusson, K., Norén, F., Hartmann, N.I.B., Jensen, P.R., Nielsen, T.G., Brinch, A. Microplastics - Occurence, effects and sources of releases to the environment in Denmark. (Danish EPA, 2015).
3. Boucher, J. & Friot, D. Primary microplastics in the oceans: A global evaluation of sources. (2017). doi:10.2305/IUCN.CH.2017.01.en
4. Kole, P. J., Löhr, A. J., Belleghem, F. G. A. J. Van & Ragas, A. M. J. Wear and tear of tyres : A stealthy source of microplastics in the environment. Int. J. Environ. Res. Public Health 14, 1265 (2017).
5. Kolomijeca, A., Parrot, J., Khan, H., Shires, K., Clarence, S, Sullivan, C., Chibwe, L., Sinton, D., Rochman, C. Increased Temperature and Turbulence Alter the Effects of Leachates from Tyre Particles on Fathead Minnow (Pimephales promelas). Environ. Sci. Technol. 54, 1750–1759 (2020).
6. Unice, K. M., Panko, J.M.., Chu, J. & Kreider, M. L. Measurement of airborne concentrations of tyre and road wear particles in urban and rural areas of France, Japan, and the United States. Atmos. Environ. 72, 192–199 (2013).
7. Kreider, M. L., Unice, K. M. & Panko, J. M. Human health risk assessment of Tyre and Road Wear Particles (TRWP) in air. Hum. Ecol. Risk Assess. 0, 1–19 (2019).
8. Unice, K. M. et al. Characterizing export of land-based microplastics to the estuary - Part I: Application of integrated geospatial microplastic transport models to assess tyre and road wear particles in the Seine watershed. Sci. Total Environ. 646, 1639–1649 (2019).
9. Unice, K. M. et al. Characterizing export of land-based microplastics to the estuary - Part II: Sensitivity analysis of an integrated geospatial microplastic transport modeling assessment of tyre and road wear particles. Sci. Total Environ. 646, 1650–1659 (2019).
10. Wik, A. & Dave, G. Occurrence and effects of tyre wear particles in the environment - A critical review and an initial risk assessment. Environ. Pollut. 157, 1–11 (2009).
11. Redondo-Hasselerharm, P. E., de Ruijter, V. N., Mintenig, S. M., Verschoor, A. & Koelmans, A. A. Ingestion and chronic effects of car tyre tread particles on freshwater benthic macroinvertebrates. Environ. Sci. Technol. acs.est.8b05035 (2018). doi:10.1021/acs.est.8b05035
12. Khan, F. R., Halle, L. L. & Palmqvist, A. Acute and long-term toxicity of micronized car tyre wear particles to Hyalella azteca. Aquat. Toxicol. 213, 105216 (2019).
13. Halle, L. L., Palmqvist, A., Kampmann, K. & Khan, F. R. Ecotoxicology of micronized tyre rubber : Past , present and future considerations. Sci. Total Environ. 135694 (2019). doi:10.1016/j.scitotenv.2019.135694
14. LaPlaca, S. B. & van den Hurk, P. Toxicological effects of micronized tyre crumb rubber on mummichog (Fundulus heteroclitus) and fathead minnow (Pimephales promelas). Ecotoxicology (2020). doi:10.1007/s10646-020-02210-7
15. Kellough, R. M. The effects of scrap automobile tyres in water. (1991).
16. Day, K. E., Holtze, K. E., Metcalfe-Smith, J. L., Bishop, C. T. & Dutka, B. J. Toxicity of leachate from automobile tyres to aquatic biota. Chemosphere 27, 665–675 (1993).
17. Abernethy, S. The acute lethality to rainbow trout of water contaminated by an automobile tyre. (1994).
18. Hartwell, S. I., Jordahl, D. M., Dawson, C. E. O. & Ives, A. S. Toxicity of scrap tyre leachates in estuarine salinities: Are tyres acceptable for artificial reefs? Trans. Am. Fish. Soc. 127, 796–806 (1998).
19. Hartwell, S. I., Jordahl, D. M. & Dawson, C. E. O. The effect of salinity on tyre leachate toxicity. Water. Air. Soil Pollut. 121, 119–131 (2000).
20. Gunasekara, A. S., Donovan, J. A. & Xing, B. Ground discarded tyres remove naphthalene, toluene, and mercury from water. Chemosphere 41, 1155–1160 (2000).
21. Edil, T. B., Park, J. K. & Kim, J. Y. Effectiveness of scrap tyre chips as sorptive drainage material. J. Environ. Eng. 130, 824–831 (2004).
22. Lisi, R. D., Park, J. K. & Stier, J. C. Mitigating nutrient leaching with a sub-surface drainage layer of granulated tyres. Waste Manag. 24, 831–839 (2004).
23. Aydilek, A. H., Madden, E. T. & Demirkan, M. M. Field evaluation of a leachate collection system constructed with scrap tyres. J. Geotech. Geoenvironmental Eng. 132, 990–1000 (2006).
24. Alamo-Nole, L. A., Perales-Perez, O. & Roman, F. R. Use of recycled tyres crumb rubber to remove organic contaminants from aqueous and gaseous phases. Desalin. Water Treat. 49, 296–306 (2012).
25. Alamo-Nole, L. A., Perales-Perez, O. & Roman-Velazquez, F. R. Sorption study of toluene and xylene in aqueous solutions by recycled tyres crumb rubber. J. Hazard. Mater. 185, 107–111 (2011).
26. Parker-Jurd, F. N. F. Napper, I. E. Abbott, G. D. Hann, S. Wright, S. L. Thompson, R. C. Investigating the sources and pathways of synthetic fibre and vehicle tyre wear contamination into the marine environment (project code ME5435). (2019).
27. Kumata, H., Yamada, J., Masuda, K., Takada, H., Sato, Y., Sakurai, T., Fujiwara, K. Benzothiazolamines as tyre-derived molecular markers: Sorptive behavior in street runoff and application to source apportioning. Environ. Sci. Technol. 36, 702–708 (2002).
28. Klöckner, P., Reemtsmp, T., Eisentraut, P., Braun, U., Ruhl, A.S., Wagner, S. Tyre and road wear particles in road environment – Quantification and assessment of particle dynamics by Zn determination after density separation. Chemosphere 222, 714–721 (2019).
- Kraton Corporation
- Kraton Sustainability Report
- Sustainability
- EcoVadis Platinum
- 2024 Nitto Supplier Sustainability Award
Kraton Corporation Publishes 2024 Sustainability Report
- By TT News
- July 01, 2025
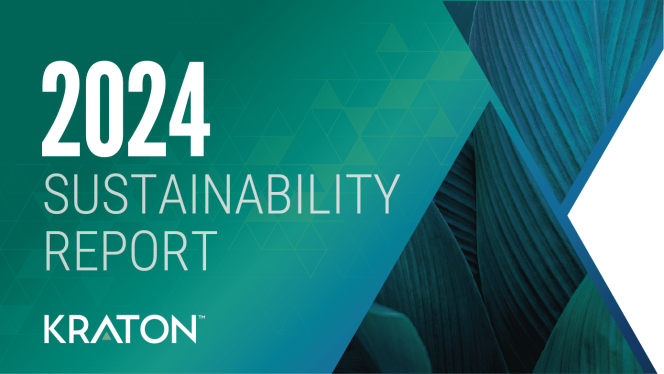
Kraton Corporation, a global leader in speciality polymers and biobased solutions derived from pine wood pulping co-products, has published its 2024 Sustainability Report, ‘Innovating with Purpose’. The report showcases the company’s advancements in climate action, circular product innovation and value chain partnerships, reinforcing its commitment to sustainable solutions.
Key achievements include a 41 percent reduction in Scope 1 & 2 greenhouse gas emissions since 2014 and a 35 percent decline in emissions intensity. Kraton also maintained its EcoVadis Platinum rating for the fourth consecutive year and received the 2024 Nitto Supplier Sustainability Award. Strategic initiatives such as a Double Materiality Assessment and a USD 35 million investment in biorefinery upgrades at its Panama City facility further demonstrate Kraton’s sustainability leadership.
The company enhanced transparency by expanding life cycle assessment (LCA) data to cover nearly 90 percent of its product portfolio, helping customers evaluate environmental impacts. Additionally, Kraton launched a data excellence program to streamline ESG reporting and refine decarbonisation goals.
Aligned with GRI, SASB, UN Global Compact and TCFD frameworks, the report reflects Kraton’s sustainability pillars: Being Reliable Partners, Preserving Planet and Empowering People. These efforts underscore Kraton’s dedication to driving meaningful progress across its operations and industries.
Marcello Boldrini, Kraton Chief Executive Officer, said, “2024 marked a pivotal year in Kraton’s sustainability journey. We turned ambition into action, significantly reducing our Scope 1 and 2 emissions by 41 percent from our 2014 baseline and earned an EcoVadis Platinum rating for the fourth consecutive year. We accelerated our decarbonisation strategy, advanced biobased innovation and partnered with customers such as WJ Group and Henkel to help address global sustainability challenges. As demand for sustainable chemicals grows, our focus remains on developing the right solutions, fostering strong partnerships and cultivating the culture necessary to lead this transformation responsibly and competitively.”
Rogier Roelen, Kraton Chief Sustainability Officer, said, “We have established new processes to scale credible, data-driven sustainability across our business. In 2024, we enhanced our ESG reporting through a data harmonisation programme and completed a Double Materiality Assessment to better align with the Corporate Sustainability Reporting Directive (CSRD). We also expanded our Life Cycle Assessment (LCA) data to cover almost 90 percent of our product portfolio, providing customers with greater transparency into the environmental impact of our products. These efforts reinforce our ability to identify where we can make the most impact and support more informed, strategic decision-making.”
Michelin Collaborates With Murfitts For Tyre Pyrolysis Plant
- By TT News
- July 01, 2025
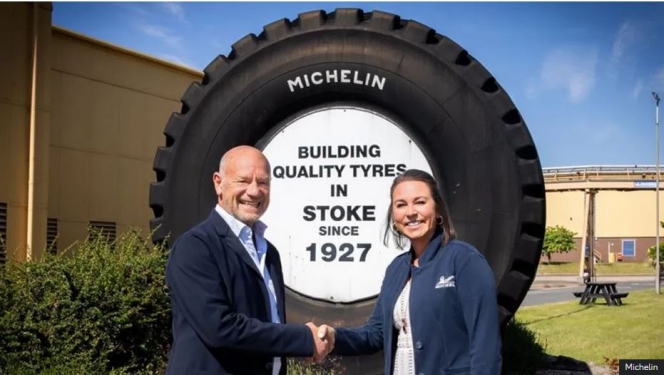
Murfitts Industries, the UK’s largest tyre recycling company, has unveiled plans for a state-of-the-art materials recovery facility at Michelin’s Stoke-on-Trent tyre plant. This groundbreaking initiative will transform end-of-life tyres into valuable resources while significantly reducing the site’s environmental footprint. The advanced recycling process will recover energy to power Michelin’s manufacturing operations, cutting annual CO₂ emissions by 1,500 tonnes. Additionally, the facility will produce high-quality recovered carbon black (rCB) and tyre pyrolysis oil (TPO), supporting sustainable material production.
Under the agreement, Michelin will supply Murfitts with 12,500 tonnes of discarded tyres annually – equivalent to 1.35 million car tyres. This capacity far exceeds local demand, with the plant able to process the equivalent of two tyres from every car registered in Stoke-on-Trent and Staffordshire. Slated for completion by late 2026, the facility will apply Murfitts’ proprietary pyrolysis technology at commercial scale, extracting reusable raw materials from tyres. The rCB will serve as a sustainable alternative in tyre manufacturing and other industrial applications, while TPO will be used in material production and alternative fuels, displacing virgin petroleum feedstocks.
Beyond material recovery, the process generates steam that will directly supply Michelin’s tyre-curing operations, replacing natural gas and further reducing fossil fuel reliance. Murfitts, which already recycles 20 million tyres yearly for applications like sports surfaces and road asphalt, continues to pioneer circular economy solutions – ensuring tyre-derived materials re-enter production cycles, closing the loop on waste. This collaboration marks a major step toward greener tyre manufacturing and resource-efficient industrial practices.
Mark Murfitt, Founder, Murfitts Industries, said, “We believe this plant could be a breakthrough in the life cycle of a tyre. It moves tyre recycling on from recovering energy and material for other uses to being able to feed it directly back into factories for new tyre production. Our core ethos at Murfitts has always been that end-of-life tyres are a valuable resource and we need to do all we can to maximise the use of the energy and materials within them. We have been developing our pyrolysis process for a number of years and our results now show we can produce material from end-of-life tyres which can perform better than the virgin equivalent for some applications. This plant will be a win-win for the tyre industry, the local and national economy and the environment.”
Christina Peloquin, Site Director, Michelin UK, said, “This is a really exciting project which reduces our environmental impact at the same time as helping us stay competitive by lowering our energy costs. The team has worked exceptionally hard on this project, and we’re looking forward to welcoming Murfitts to our Stoke-on-Trent site.”
Maria Röttger, CEO and President, Michelin Europe North, said, “At Michelin, we see every challenge as a chance to lead positive change – and end-of-life tyres are no exception. As shapers, innovators and pioneers of sustainable mobility, Michelin is committed to transforming the way tyres are handled at every stage of their life cycle. Through our deep expertise and forward-thinking approach, we are co-building a robust recycling ecosystem that redefines what has previously been possible. This project with Murfitts Industries is a powerful reflection of Michelin’s enduring commitment to sustainability and responsible leadership in the tyre and rubber industry.”
Evonik to Boost Asia Supply Chain with Shanghai Production Expansion
- By TT News
- June 30, 2025
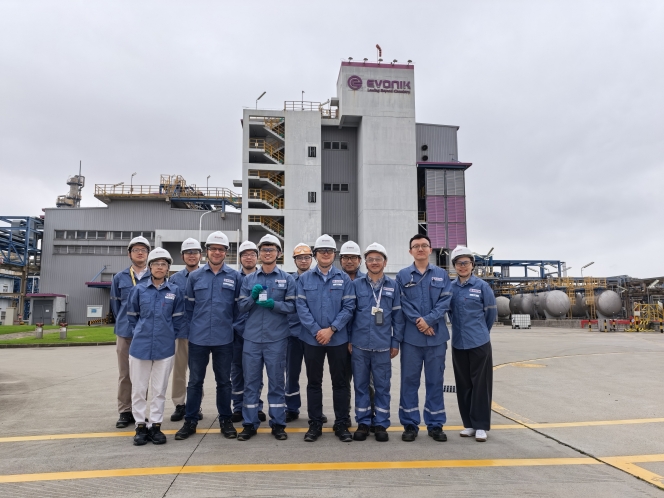
Evonik Industries will localise production of a key tyre additive in Shanghai, marking a strategic shift to enhance supply security across Asia amid growing regional demand.
The Essen-based company announced plans to establish the final production step of its POLYVEST ST-E 60 product at its Shanghai facility, with operations expected to commence by the third quarter of 2025. The expansion will significantly increase the global production capacity of silane-functionalised polybutadienes.
The move represents Evonik’s latest effort to strengthen supply chains and reduce dependency on European manufacturing for Asian markets. POLYVEST serves as a reactive plasticiser in tyre formulations and is also used in rubber compounds, adhesives, tyres, coatings, and sealants.
“This strategic investment will enhance our production capabilities and ensure that our customers in Asia benefit from improved supply security and shorter lead times,” said Dr Anna Maria Ickert, Head of Evonik Coating & Adhesive Resins. “In today’s environment, fostering independent supply chains and bringing our products closer to our customers is essential, enabling us to respond more effectively to their needs.”
The Shanghai expansion comes as global chemical companies reassess manufacturing footprints following supply chain disruptions experienced during the pandemic and ongoing geopolitical tensions. China remains a crucial market for speciality chemicals, particularly in the automotive and construction sectors.
Evonik’s decision reflects broader industry trends towards regionalisation of production, with companies seeking to reduce logistics costs whilst improving responsiveness to local market demands. The tyre industry, a key end-market for POLYVEST, has experienced robust growth in Asia driven by expanding automotive production.
Dr Jürgen Herwig, Head of Evonik’s polybutadienes and speciality acrylics business, emphasised the expansion’s strategic importance. “This expansion aligns with our long-term strategy to strengthen our global footprint while maintaining a strong focus on sustainability and operational excellence,” he said. “The new capacity will enable Evonik’s customers to achieve their business goals while participating in the region’s growth.”
POLYVEST products utilise rubber-based chemistry to ensure compatibility with tyre tread compounds, thereby addressing performance requirements in an increasingly demanding automotive market. The localisation strategy aims to reduce lead times whilst maintaining product quality standards.
Collaboration Is A Growing Need!
- By Sharad Matade & Gaurav Nandi
- June 30, 2025
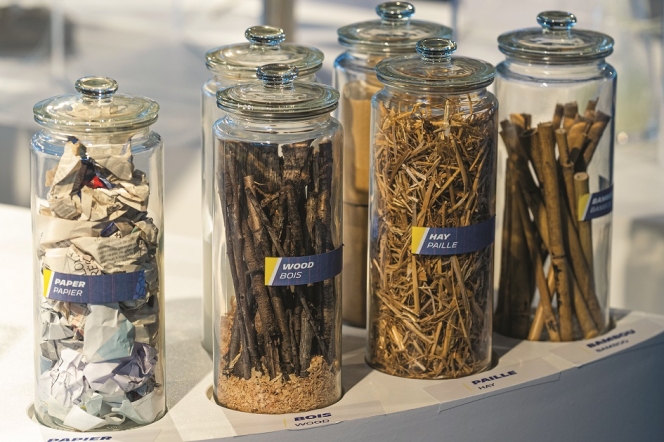
The tyre industry has undergone significant changes over the past century, particularly in material composition and performance optimisation. While the external appearance of tyres may remain similar, advancements in rolling resistance and the integration of sustainable materials have reshaped the sector. Michelin, alongside its competitors, has been embracing innovation through collaborations to meet its ambitious 2050 sustainability goals, focusing on using 100 percent renewable and recycled materials. However, the challenge lies in scaling up recycling technologies and ensuring effective sorting. As the industry shifts, RFID technology and extended producer responsibility (EPR) regulations are emerging as critical tools for achieving material circularity and enhancing recycling efficiency.
Tyres have changed in the last 100 years. While the basic shape and colour might look the same, the internal composition has evolved significantly. Over the past century, and especially in the last 30 years, there have been major advances. One of the most significant has been the improvement in rolling resistance. Achieving lower rolling resistance without compromising grip has been a major technical challenge, and it has had a direct impact on fuel efficiency. In parallel, there’s been increasing focus on using more sustainable materials in tyre manufacturing. So, while it might not be obvious from the outside, there’s been substantial innovation under the surface.
However, it is a well-known fact that the tyre industry is secretive. Companies keep their research and development as tight as possible, but endeavours for including recyclable materials seem to break that ceiling, prompting towards collaborations.
Speaking exclusively to Tyre Trends, Sander Vermeulen, Vice President for End-of-life Rubber Products Recycling Business at Michelin, said, “There is a growing need and momentum for tyre companies to work more closely together, particularly around sustainability and materials innovation. Many companies have set ambitious goals for 2050, which include using 100 percent sustainable materials, achieving full recyclability or becoming carbon neutral. While each company may define these goals differently, the overarching direction is very similar.”
“A good example of this shift is our recent collaboration with Bridgestone through the ‘Call for Action’ initiative. We discovered that both companies shared similar long-term ambitions. One major challenge we identified was the scalability of innovations, especially from recycling companies. Many of these innovations work well at small scale, but scaling them up to meet the needs of the global tyre industry is a different story. What’s promising is that instead of working in silos, we began engaging in open dialogue. Both Michelin and Bridgestone were receiving proposals for new materials but often found them unsuitable for tyre applications. Rather than simply rejecting these proposals, we asked that how we can help these suppliers improve the products,” he added.
He noted that together the tyre makers started defining shared specifications that outline the minimum criteria a new material must meet to be viable for tyre manufacturing. “It’s not a guarantee of adoption, but it provides a clear, transparent benchmark. And if a material doesn’t fall within that box, we can save time for ourselves and the suppliers,” added Vermeulen.
He also quipped that he had never imagined working so openly with a competitor like Bridgestone whilst strictly respecting antitrust rules. But the experience has been incredibly constructive.
Michelin’s 2050 target is bold as it seeks to make 100 percent of its tyres from renewable, recycled or sustainable materials. Recycling sits at the core of that ambition. Internally, the company is aligning efforts across departments to meet this goal with a near-term milestone of 40 percent sustainable content by 2030.
That percentage includes both recycled and bio-based materials. However, Michelin isn’t developing recycling technologies in-house. Instead, it’s working with a network of external partners to identify and scale promising innovations.
Among its collaborators are Enviro and Infiniteria as well as broader initiatives like Biobutterfly and the WhiteCycle consortium, which focuses on recovering textile fibres for tyres. The company remains open to any solution that can help close the loop on tyre materials.
As of the most recent annual report, Michelin reported that 31 percent of the materials used in its tyres are either renewable or recycled. This figure reflects the combined share of both categories, not recycled content alone.
Opining on whether recycled materials are easier to use in commercial or passenger tyres, Vermeulen said, “It really depends on the specific application. Some applications allow for a higher percentage of renewable or recycled content than others. But we don’t break down our targets or current performance by tyre category. The current figure we’ve communicated in our annual report is a global average across all types of tyres.”
EVOLVING VALUE CHAIN
As tyre companies remain steadfast towards the respective goals of using recycled and renewable materials, a glaring question that remains is the fate of current suppliers. Explaining how the value chain will be impacted once tyre companies reach the goals, Vermeulen stated, “They will also need to adapt. The entire value chain must evolve. That means synthetic rubber producers and oil suppliers need to develop renewable or recycled versions of the materials they currently provide. Everyone, from upstream raw material providers to downstream manufacturers, will need to contribute if we’re going to meet these ambitious goals.”
Commenting on whether such shift will restructure the entire tyre industry, he said, “It’s hard to make specific predictions, but one thing is clear that the entire value chain is already beginning to change. All raw material suppliers now understand the direction tyre manufacturers are heading. We’re already seeing many traditional suppliers exploring new approaches to reduce the reliance on fossil-based materials. Some are developing recycled alternatives, while others are exploring biobased feedstocks.”
“In this effort, a concept we explored in a large-scale European project was called BlackCycle. It brought together various actors from the entire tyre industry value chain including raw material suppliers and other stakeholders to map out how we can extract maximum value from end-of-life tyres. It looked at viable recycling pathways including how pyrolysis oil can be integrated into chemical supply chains. We all need to work together to co-create solutions based on renewable and recycled materials,” he added.
Michelin doesn’t plan to produce recycled materials itself. Instead, its focus is on defining performance and quality specifications, then partnering with companies ranging from start-ups to established suppliers that can deliver materials meeting those standards.
Commenting on the same lines, he added, “The entire tyre industry has a strong interest in gaining access to recycled materials that can be reused in new products. And to achieve that, partnerships are essential. There’s no way we can meet these ambitions if every company stays within its traditional boundaries and works in isolation. We believe in collaborating across the value chain. Often, smaller companies have breakthrough technologies or innovative ideas but lack the resources or infrastructure to scale. In those cases, if we can help them access funding or industrialise the processes, it’s a win-win for the industry as a whole.”
While performance gaps between recycled and virgin materials are a known concern, Michelin sees scalability as the more critical barrier. Many recycling innovations show promise at the lab or prototype level, but few are ready for industrial-scale production.
To bridge that gap, Michelin and others in the sector are working closely with innovators to help mature these technologies to meet industry demands.
REGULATION & TECHNOLOGY
The extended producer responsibility (EPR) has been a staunch advocate for recycling end-of-life tyres across countries. The regulation is not only limited to European markets but has expanding into countries like India too.
Commenting on whether EPR regulations will help drive more effective recycling, Vermeulen said, “Extended producer responsibility plays a key role in tyre recycling by making manufacturers responsible for collecting and recycling tyre after use. In countries with EPR laws, such as most of Europe, producers and importers must ensure proper tyre collection and recycling. This legally mandates tyre producers to manage the end-of-life stage of the products. However, EPR is not the only model that can ensure effective recycling. In regions without EPR, like the United States, tyre recycling is still managed through a free-market system driven by industry and service providers. Even in Germany, which lacks an EPR law, tyres are still collected and managed properly through industry-driven solutions.”
“While EPR can certainly help in places with limited infrastructure, the key to effective tyre recycling lies in how well the system is organised. Whether through EPR or free-market models, both can be effective as long as the collection and recycling infrastructure is well established,” he added.
Vermeulen also views RFID technology as a crucial enabler for achieving material circularity in the tyre industry. By embedding RFID tags, tyres can be tracked and identified with precise information about its composition, helping to streamline the recycling process. This technology allows for better sorting of tyres based on specific material make-up, which is critical for maximising the quality of recycled materials.
Just as with household recycling, the challenge is to ensure that materials are sorted effectively. With too many sorting categories, costs rise without guaranteeing better quality. RFID makes it easier to identify the correct ‘bin’ for each tyre, whether it’s a winter, truck or passenger car tyre.
Additionally, RFID can help differentiate between new, retreaded and partially worn tyres, which often have varying materials and recycling needs. This enables more efficient sorting, improving the overall quality of the recycling output while keeping costs manageable. Michelin sees RFID as an essential tool in making the recycling process more effective and economically viable.
Comments (0)
ADD COMMENT