- Lanxess
- Lanxess India
- Vulkanox HS Scopeblue
- Matthias Zachert
- India Application Development Centre
- tyre
- rubber
Tyre Industry Continues To Be A Key Growth Driver For Lanxess India
- By Nilesh Wadhwa
- April 14, 2025
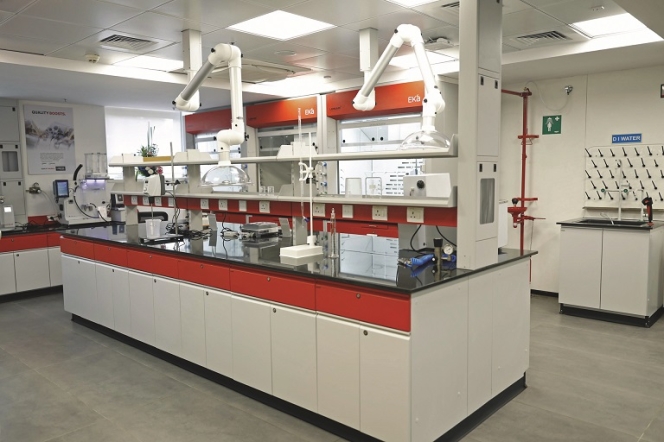
The German speciality chemicals company recently inaugurated the first India Application Development Centre (IADC) in the country’s financial capital, reinforcing its commitment and outlook for the country.
For Lanxess India, tyre industry accounts for almost 25 percent of its business, as against global average of around 10 percent. And the company’s management continues to be upbeat about the growth story for Indian tyre makers.
“India, from our point of view, will play a very important detrimental role (for Lanxess). Because when you want to grow your industry, which Prime Minister Narendra Modi clearly has as an ambition, you need the chemical industry and all their precursors. And if you want to help the Indian industry to further develop (new solutions), you need to have local application for local needs,” remarked Matthias Zachert, Chairman of the Board of Management of Lanxess.
He was speaking on the sidelines of the inauguration of the India Application Development Centre (IADC) in Thane, Mumbai, which also marks a significant commitment by the German chemical major for the country.
Lanxess is said to be the world’s largest supplier of rubber additives focusing on solutions around rubber chemicals, speciality chemicals and processing aids for the rubber industry. The company’s solutions find their way in high-performance rubber products such as tyres, treads, seals and even drive belts.
At present, Lanxess has established two production facilities in India – Jhagadia in Gujarat and Nagda in Madhya Pradesh. The tyre industry is primarily supported by Lanxess Rhein Chemie Additives Divisions, which manufactures Rhenogran and Rhenodiv at the Jhagadia facility. The company has invested over EUR 70 million in the Jhagadia facility, which not only supports the domestic customer base for Lanxess but also its customers in the Asia-Pacific region. The company has a longstanding presence in India, with representation from all 10 of its business units and a workforce of around 800 employees.
It comes as no surprise that Zachert sees India as a critical growth region for Lanxess, offering immense opportunities for collaboration and innovation.
INDIAN TYRE INDUSTRY A KEY GROWTH DRIVER
Globally, the automotive industry in particular is transitioning from being seen as a seller of products to a mobility solutions provider, what’s with new business models or service solutions.
Zachert sees that while the tyre market was consolidated for many years, it has started opening up in the last decade.
“The global tyre market has opened up, strongly driven by Chinese tyre manufacturers but also Indian tyre manufacturers. We have rising stars here in India. Mobility has always led to liberty and flexibility for mankind. This will be a trend that in the next 10-20 years is not going to vanish. Mobility will be important, which means the tyre industry is important. And therefore, I look positively at the tyre industry going forward, notably the one that is located here in India,” said an optimistic Zachert.
It is important to understand that the company has almost 25 percent of its business exposure to the Indian tyre segment, which could be amongst the highest for the company.
“For our group, the mobility exposure that we have worldwide as a company is 10 percent. We are over-proportionally present here in India, which is good and normal because the industry is expanding. The Indian tyre market is expanding not only locally but globally,” he said.
The recent setting up of IADC is part of Lanxess’ strategic focus on India as a key market and innovation hub. The strengthening of R&D will enable the company to enhance its ability to deliver high-value, specialised solutions tailored to local needs.
To begin with, the company has integrated expertise from two key businesses in India: Lubricant Additives (high-performance additives and additive systems, synthetic base fluids and ready-to-use lubricants) and Material Protection Products (antimicrobial, disinfection and preservation solutions). Going forward, the idea is to be present with all business units’ expertise at the IADC.
Namitesh Roy Choudhury, Vice-Chairman and Managing Director, Lanxess India, said, “By establishing the IADC, we are bringing our expertise closer to our Indian customers. This centre will not only support innovation but also strengthen our ability to address evolving market trends with speed and precision.”
For Lanxess India, the IADC aligns with its transformation journey towards a speciality chemicals company. The aim is to focus less on cyclical business areas and solutions for critical applications and move towards a partner for sustainable mobility or consumer protection. And the company sees India’s growing industrial base and expanding consumer markets as an ideal platform for driving such advancements.
SUPPORTING THE TYRE INDUSTRY
The production of the plain looking black tyre is more than just moulding of rubber; it is a complex process, which includes incorporating various raw materials and scientific steps to ensure that the tyres are built up to a particular specification. After all, tyres remain and are supposed to be the sole point of contact between a vehicle and the road when in motion.
Lanxess, for its part, supplies solutions across mixing, batch-off, extrusion & tread marking, tyre inspection & repair, tyre curing, green tyre spraying and tyre building processes.
According to the company, a durable car tyre is the result of a complex manufacturing process in which the tyre is built-up from various rubber compounds and reinforcing materials. It explains that by using rubber chemicals and various fillers, the raw material rubber is turned into a high-performance product. This is because rubber is soft and not very durable until vulcanisation. By selecting the type of rubber, the crosslinking chemicals and additives required for the desired technical properties of the end-product, high-performance products such as tyres and other rubber products are created.
EUROPEAN COMPANIES TO STEP OUT OF PETROCHEMICALS
The chemicals industry has undergone a sea of change, especially given the evolving trend from geography-focused development to globalisation. For the last few years, there has been a growing pressure, especially given the focus on sustainability.
To support the sustainability drive, the company recently introduced Vulkanox HS Scopeblue, a next-generation rubber additive designed to help tyre manufacturers produce more durable and environmentally friendly tyres. The anti–degradant effectively protects tyres from the damaging effects of oxygen and heat while offering reduced environmental impact. Its low volatility and minimal migration tendency further enhance tyre performance and longevity, making it an optimal solution for modern, eco-conscious manufacturing.
The company claims that the Vulkanox HS Scopeblue boasts a carbon footprint more than 30 percent lower than its conventionally produced counterpart thanks to the use of bio-circular acetone and renewable energy in its production process. It is being currently manufactured at an ISCC PLUS-certified plant in Germany; this mass-balanced additive retains the same chemical structure as the original product, allowing tyre manufacturers to adopt it seamlessly without altering their existing production processes.
Zachert further said, “Times lead to change. The industry dynamics of chemicals has been adjusting to change for the last decade and will continue to see changes for the next decades. If I look into the next 10 years of the chemical industry, my personal prognosis is that you will see that the European chemical companies will more and more step out of petrochemicals and go upstream. And this is happening as we speak. My thesis also is that the European industry will focus more on niche polymers and speciality chemicals. The upstream and volume polymers will go elsewhere, where you have the raw materials and cheap energy. Countries that are destined to dominate these kinds of chemicals over the next 10 years, is the Middle East and the United States. Europe used to be the epicentre of chemicals 20-30 years ago from polymers to chemicals to pharmaceuticals.”
Then there is the shift from global supply chain to more of regional supply chain given the geopolitical situation.
“I see that with the current world with geopolitical tensions, the likelihood is high that we will go back to trade zones. And therefore, the global value chain in chemicals is one where many companies will have to rethink the global approach and turn towards a more regional approach,” added Zachert.
- Covestro
- Flame-Retardant Encapsulation Foam
- Flame-Retardant Foam
- Polyurethane Foam
- Baysafe BEF
- Electric Vehicles Traction Battery Safety Requirements
- EV Battery
Covestro Enhances EV Battery Safety With New Flame-Retardant Encapsulation Foam
- By TT News
- July 17, 2025
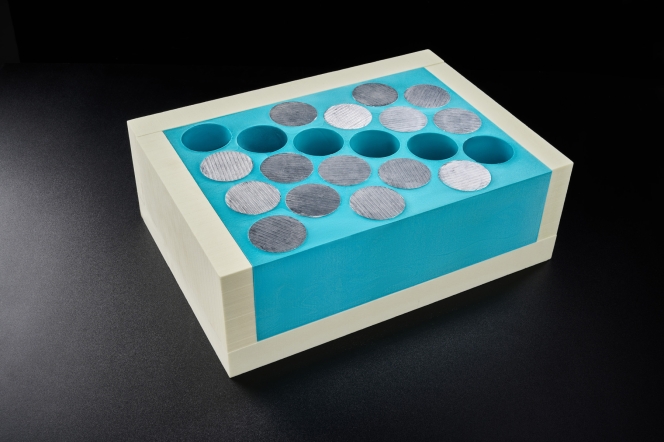
Covestro has introduced its next-generation Baysafe BEF flame-retardant polyurethane foam, a breakthrough in EV battery safety. Designed to prevent thermal runaway propagation between cells, this lightweight foam meets stringent global safety demands, particularly in China, where the new GB 38031-2025 standard will require fireproof batteries from 2026.
As the world’s largest EV market, China’s regulations are expected to influence global standards, making Covestro’s innovation critical for automakers. The foam’s superior flame resistance enhances safety in EVs, e-bikes and portable energy storage, addressing a key consumer concern. By combining cutting-edge flame-retardant technology with lightweight performance, the Baysafe BEF series helps drive the transition to sustainable transportation and energy storage worldwide.
With EV adoption accelerating, Covestro’s material solutions support manufacturers in meeting stricter safety requirements while enabling international expansion. Beyond encapsulation, the company offers polyurethane-based battery covers and shock-absorbing components, strengthening its position in the fast-growing new energy sector.
Akhil Singhania, Global Head of PU Specialties in Covestro’s Tailored Urethanes Business Entity, said, “This innovation represents a significant step towards enabling sustainable mobility through enhanced safety. By launching our advanced flame-retardant technology, Covestro reaffirms its commitment to innovation and strengthens our product portfolio to meet the evolving needs of the EV industry.”
Zeon Develops Hydrophilic SBR For Winter Tyres
- By TT News
- July 16, 2025
Zeon Corporation has announced the development of Nipol BR1300, a novel hydrophilic styrene butadiene rubber (SBR) for winter tyres. Synthesised with a polybutadiene rubber base, the material delivers unprecedented hydrophilicity for tyre applications. Commercial production began in May 2025 at Zeon’s Tokuyama plant in Yamaguchi Prefecture.
As part of its strategic portfolio optimization, Zeon plans to phase out low-profitability products like ESBR-1 and NBR latex by 2026. However, it will continue manufacturing high-margin products, including ESBR-2, nitrile butadiene rubber and solution SBR. This shift underscores Zeon’s focus on advanced, value-driven rubber solutions.
- Covestro India
- CSIR-National Chemical Laboratory
- Circular Economy
- Polyurethane Waste
- Polyurethane Recycling
Covestro India Partners With CSIR-NCL To Pioneer Polyurethane Upcycling Solutions
- By TT News
- July 16, 2025
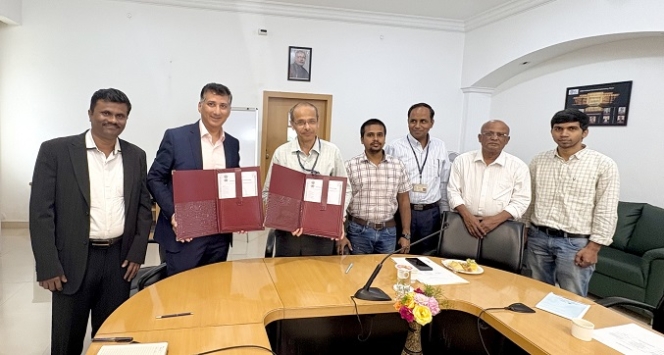
Covestro India has entered into a strategic collaboration with CSIR-National Chemical Laboratory (NCL) through an innovative CSR initiative focused on developing sustainable upcycling technologies for polyurethane waste. This partnership aims to overcome existing recycling limitations by transforming discarded polyurethane materials into valuable chemical feedstocks, potentially revolutionising the material's circular economy.
This collaboration underscores both organisations' commitment to environmental innovation, leveraging NCL's advanced research infrastructure and Covestro's market leadership to address critical gaps in plastic circularity. Current polyurethane recycling methods, predominantly mechanical with some emerging chemical processes, face substantial challenges including material degradation, high energy consumption and hazardous byproduct generation. The project seeks to develop commercially viable chemical recycling solutions that maintain material integrity while minimising environmental impact.
Polyurethanes, widely used in furniture, automotive parts and insulation, present unique recycling difficulties due to their complex molecular structure. Most end up in landfills after use, creating significant sustainability challenges. By combining Covestro's industrial expertise with NCL's seven decades of chemical research excellence, the partnership aims to create breakthrough upcycling technologies.
Avinash Bagdi, Director & Head of Sales & MD Solutions India & Projects – Tailored Urethanes, said, "This partnership strengthens our commitment to finding innovative solutions for polyurethane waste and directly supports Covestro's vision of becoming fully circular. By developing effective methods to upcycle polyurethanes, we're taking concrete steps towards creating a more sustainable future in line with our corporate vision of driving the transition to a circular economy."
Dr Ashish Lele, Director of NCL, said, "CSIR-National Chemical Laboratory is excited to partner with Covestro (India) in this groundbreaking initiative to develop novel chemical upcycling methods for polyurethane waste. The conventional and electrochemical strategies we're developing address the critical limitations of current recycling technologies and align perfectly with our shared vision of a circular economy. This collaboration represents a significant step towards sustainable plastic management in India and globally, with potential to transform polyurethane waste into valuable chemical resources."
Zeon Starts Construction Of Bench-Scale Facility For Sustainable Butadiene Production
- By TT News
- July 11, 2025
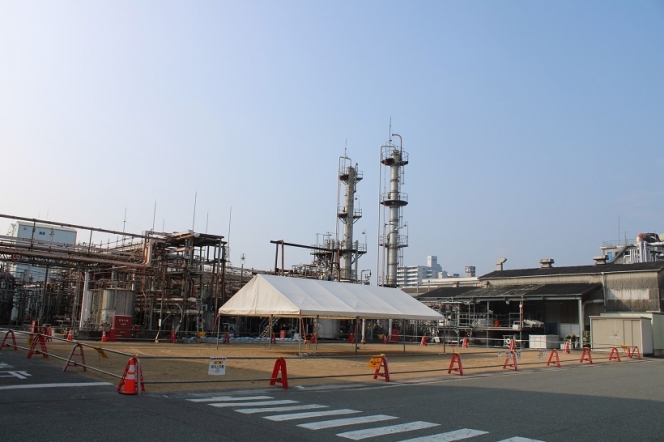
Zeon Corporation has begun building a pilot facility at its Tokuyama Plant in Shunan City, Yamaguchi Prefecture, to test a new method for efficiently producing butadiene from plant-derived ethanol. The demonstration plant, expected to start operations in 2026, will supply butadiene for manufacturing trial batches of polybutadiene rubber, bringing the company closer to commercialising this sustainable production process.
This project is a key part of a joint initiative between Zeon and The Yokohama Rubber Co., Ltd. to develop eco-friendly methods for producing butadiene and isoprene from renewable sources, with full-scale adoption targeted for the 2030s. Under the collaboration, Zeon will produce butadiene rubber at the new facility, while Yokohama Rubber will use the material to create experimental tyres and conduct performance testing. The data collected will help refine the technology ahead of larger-scale trials. The companies aim to finalise the production process by 2030 using an expanded pilot plant, with plans for industrial-scale commercialisation by 2034.
A ceremonial groundbreaking event took place on 10 July 2025, with 33 attendees, including local government officials from Yamaguchi Prefecture and Shunan City, construction partners and Zeon executives such as Chairman Kimiaki Tanaka and Tokuyama Plant Manager Akira Honma. The gathering included traditional safety prayers for the construction phase, marking the official start of this sustainability-focused industrial project.
Comments (0)
ADD COMMENT