- Lanxess
- Lanxess India
- Vulkanox HS Scopeblue
- Matthias Zachert
- India Application Development Centre
- tyre
- rubber
Tyre Industry Continues To Be A Key Growth Driver For Lanxess India
- By Nilesh Wadhwa
- April 14, 2025
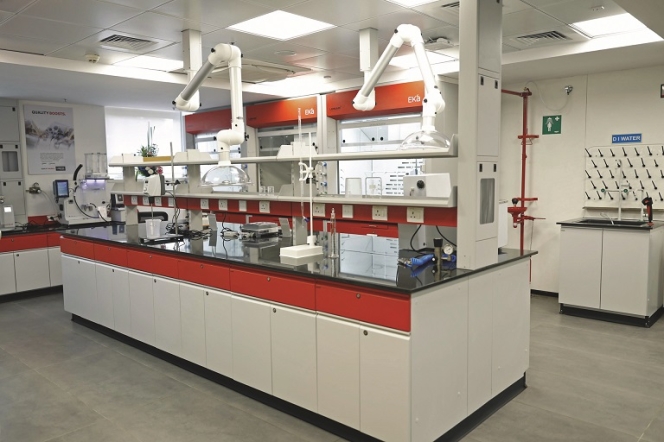
The German speciality chemicals company recently inaugurated the first India Application Development Centre (IADC) in the country’s financial capital, reinforcing its commitment and outlook for the country.
For Lanxess India, tyre industry accounts for almost 25 percent of its business, as against global average of around 10 percent. And the company’s management continues to be upbeat about the growth story for Indian tyre makers.
“India, from our point of view, will play a very important detrimental role (for Lanxess). Because when you want to grow your industry, which Prime Minister Narendra Modi clearly has as an ambition, you need the chemical industry and all their precursors. And if you want to help the Indian industry to further develop (new solutions), you need to have local application for local needs,” remarked Matthias Zachert, Chairman of the Board of Management of Lanxess.
He was speaking on the sidelines of the inauguration of the India Application Development Centre (IADC) in Thane, Mumbai, which also marks a significant commitment by the German chemical major for the country.
Lanxess is said to be the world’s largest supplier of rubber additives focusing on solutions around rubber chemicals, speciality chemicals and processing aids for the rubber industry. The company’s solutions find their way in high-performance rubber products such as tyres, treads, seals and even drive belts.
At present, Lanxess has established two production facilities in India – Jhagadia in Gujarat and Nagda in Madhya Pradesh. The tyre industry is primarily supported by Lanxess Rhein Chemie Additives Divisions, which manufactures Rhenogran and Rhenodiv at the Jhagadia facility. The company has invested over EUR 70 million in the Jhagadia facility, which not only supports the domestic customer base for Lanxess but also its customers in the Asia-Pacific region. The company has a longstanding presence in India, with representation from all 10 of its business units and a workforce of around 800 employees.
It comes as no surprise that Zachert sees India as a critical growth region for Lanxess, offering immense opportunities for collaboration and innovation.
INDIAN TYRE INDUSTRY A KEY GROWTH DRIVER
Globally, the automotive industry in particular is transitioning from being seen as a seller of products to a mobility solutions provider, what’s with new business models or service solutions.
Zachert sees that while the tyre market was consolidated for many years, it has started opening up in the last decade.
“The global tyre market has opened up, strongly driven by Chinese tyre manufacturers but also Indian tyre manufacturers. We have rising stars here in India. Mobility has always led to liberty and flexibility for mankind. This will be a trend that in the next 10-20 years is not going to vanish. Mobility will be important, which means the tyre industry is important. And therefore, I look positively at the tyre industry going forward, notably the one that is located here in India,” said an optimistic Zachert.
It is important to understand that the company has almost 25 percent of its business exposure to the Indian tyre segment, which could be amongst the highest for the company.
“For our group, the mobility exposure that we have worldwide as a company is 10 percent. We are over-proportionally present here in India, which is good and normal because the industry is expanding. The Indian tyre market is expanding not only locally but globally,” he said.
The recent setting up of IADC is part of Lanxess’ strategic focus on India as a key market and innovation hub. The strengthening of R&D will enable the company to enhance its ability to deliver high-value, specialised solutions tailored to local needs.
To begin with, the company has integrated expertise from two key businesses in India: Lubricant Additives (high-performance additives and additive systems, synthetic base fluids and ready-to-use lubricants) and Material Protection Products (antimicrobial, disinfection and preservation solutions). Going forward, the idea is to be present with all business units’ expertise at the IADC.
Namitesh Roy Choudhury, Vice-Chairman and Managing Director, Lanxess India, said, “By establishing the IADC, we are bringing our expertise closer to our Indian customers. This centre will not only support innovation but also strengthen our ability to address evolving market trends with speed and precision.”
For Lanxess India, the IADC aligns with its transformation journey towards a speciality chemicals company. The aim is to focus less on cyclical business areas and solutions for critical applications and move towards a partner for sustainable mobility or consumer protection. And the company sees India’s growing industrial base and expanding consumer markets as an ideal platform for driving such advancements.
SUPPORTING THE TYRE INDUSTRY
The production of the plain looking black tyre is more than just moulding of rubber; it is a complex process, which includes incorporating various raw materials and scientific steps to ensure that the tyres are built up to a particular specification. After all, tyres remain and are supposed to be the sole point of contact between a vehicle and the road when in motion.
Lanxess, for its part, supplies solutions across mixing, batch-off, extrusion & tread marking, tyre inspection & repair, tyre curing, green tyre spraying and tyre building processes.
According to the company, a durable car tyre is the result of a complex manufacturing process in which the tyre is built-up from various rubber compounds and reinforcing materials. It explains that by using rubber chemicals and various fillers, the raw material rubber is turned into a high-performance product. This is because rubber is soft and not very durable until vulcanisation. By selecting the type of rubber, the crosslinking chemicals and additives required for the desired technical properties of the end-product, high-performance products such as tyres and other rubber products are created.
EUROPEAN COMPANIES TO STEP OUT OF PETROCHEMICALS
The chemicals industry has undergone a sea of change, especially given the evolving trend from geography-focused development to globalisation. For the last few years, there has been a growing pressure, especially given the focus on sustainability.
To support the sustainability drive, the company recently introduced Vulkanox HS Scopeblue, a next-generation rubber additive designed to help tyre manufacturers produce more durable and environmentally friendly tyres. The anti–degradant effectively protects tyres from the damaging effects of oxygen and heat while offering reduced environmental impact. Its low volatility and minimal migration tendency further enhance tyre performance and longevity, making it an optimal solution for modern, eco-conscious manufacturing.
The company claims that the Vulkanox HS Scopeblue boasts a carbon footprint more than 30 percent lower than its conventionally produced counterpart thanks to the use of bio-circular acetone and renewable energy in its production process. It is being currently manufactured at an ISCC PLUS-certified plant in Germany; this mass-balanced additive retains the same chemical structure as the original product, allowing tyre manufacturers to adopt it seamlessly without altering their existing production processes.
Zachert further said, “Times lead to change. The industry dynamics of chemicals has been adjusting to change for the last decade and will continue to see changes for the next decades. If I look into the next 10 years of the chemical industry, my personal prognosis is that you will see that the European chemical companies will more and more step out of petrochemicals and go upstream. And this is happening as we speak. My thesis also is that the European industry will focus more on niche polymers and speciality chemicals. The upstream and volume polymers will go elsewhere, where you have the raw materials and cheap energy. Countries that are destined to dominate these kinds of chemicals over the next 10 years, is the Middle East and the United States. Europe used to be the epicentre of chemicals 20-30 years ago from polymers to chemicals to pharmaceuticals.”
Then there is the shift from global supply chain to more of regional supply chain given the geopolitical situation.
“I see that with the current world with geopolitical tensions, the likelihood is high that we will go back to trade zones. And therefore, the global value chain in chemicals is one where many companies will have to rethink the global approach and turn towards a more regional approach,” added Zachert.
Zeon Starts Construction Of Bench-Scale Facility For Sustainable Butadiene Production
- By TT News
- July 11, 2025
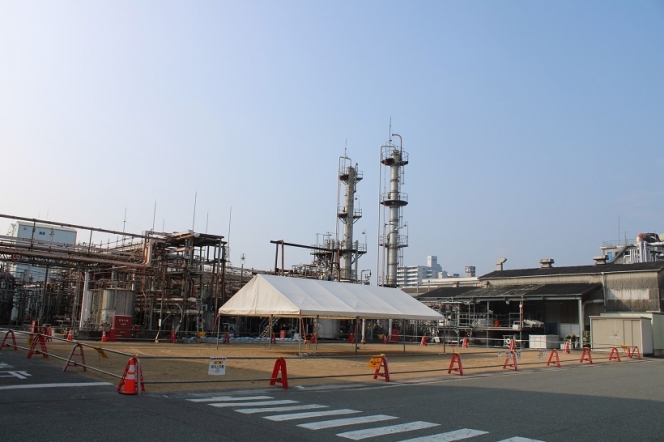
Zeon Corporation has begun building a pilot facility at its Tokuyama Plant in Shunan City, Yamaguchi Prefecture, to test a new method for efficiently producing butadiene from plant-derived ethanol. The demonstration plant, expected to start operations in 2026, will supply butadiene for manufacturing trial batches of polybutadiene rubber, bringing the company closer to commercialising this sustainable production process.
This project is a key part of a joint initiative between Zeon and The Yokohama Rubber Co., Ltd. to develop eco-friendly methods for producing butadiene and isoprene from renewable sources, with full-scale adoption targeted for the 2030s. Under the collaboration, Zeon will produce butadiene rubber at the new facility, while Yokohama Rubber will use the material to create experimental tyres and conduct performance testing. The data collected will help refine the technology ahead of larger-scale trials. The companies aim to finalise the production process by 2030 using an expanded pilot plant, with plans for industrial-scale commercialisation by 2034.
A ceremonial groundbreaking event took place on 10 July 2025, with 33 attendees, including local government officials from Yamaguchi Prefecture and Shunan City, construction partners and Zeon executives such as Chairman Kimiaki Tanaka and Tokuyama Plant Manager Akira Honma. The gathering included traditional safety prayers for the construction phase, marking the official start of this sustainability-focused industrial project.
Rice Husk Ash Revolution: Continental's Eco-Friendly Tyre Fillers
- By TT News
- July 11, 2025
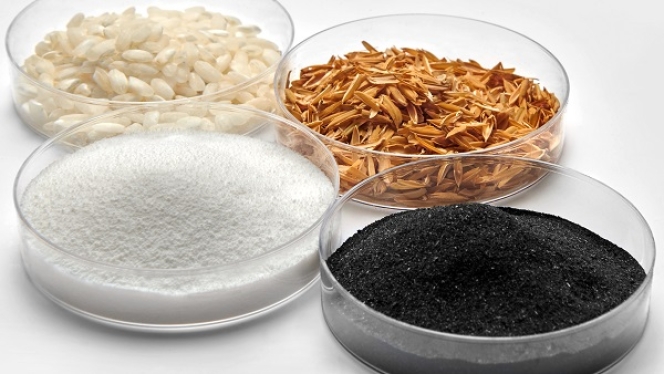
Continental is increasing its use of renewable and recycled materials in tyre production, aiming to exceed 40 percent by 2030 while maintaining high safety and performance standards. In 2024, these materials accounted for 26 percent of tyre composition, with a projected 2-3 percent increase in 2025. Key to this shift are carbon black and silica – essential fillers that enhance durability, grip and braking performance.
Silica, a critical component for optimising grip and minimising rolling resistance, is traditionally derived from quartz sand. However, Continental now obtains silica from rice husks, an agricultural by-product of risotto rice production. This innovative approach not only repurposes waste but also requires less energy than conventional methods. Partnering with manufacturers like Solvay in Italy, Continental integrates rice husk-derived silica across its entire tyre portfolio. Silica has been a game-changer in tyre technology for decades, significantly improving safety and energy efficiency. Its use in tread compounds has contributed to a nearly 50 percent reduction in braking distances while also lowering rolling resistance, thereby reducing fuel consumption and CO₂ emissions.
Carbon black, another vital material making up to 20 percent of a passenger car tyre's weight, is being sourced through sustainable alternatives. Continental employs three innovative methods: bio-based carbon black from tall oil (a paper industry by-product), recycled carbon black from pyrolysis oil derived from end-of-life tyres and a direct recovery process that extracts carbon black from used tyres via pyrolysis. The company collaborates with suppliers like Orion Engineered Carbons and Tokai Carbon, utilising different carbon black variants tailored to specific tyre components, such as sidewalls and treads. Through the mass balance approach, Continental substitutes fossil-based raw materials with bio-based or recycled alternatives without altering existing production processes.
Additionally, Continental has partnered with Pyrum Innovations to advance tyre recycling through pyrolysis, a process that recovers carbon black from end-of-life tyres for reuse. While currently applied in forklift tyres, efforts are underway to adapt this recycled carbon black for broader tyre applications, ensuring compliance with performance and safety standards. These initiatives underscore Continental’s dedication to sustainable innovation, demonstrating how eco-friendly materials can enhance both tyre performance and environmental responsibility across the value chain.
Jorge Almeida, head of Sustainability at Continental Tire, said, “Innovation and sustainability go hand in hand at Continental. Using silica from the ashes of rice husks in our tyres shows that we are breaking completely new ground – without compromising on safety, quality or performance.”
JLR To Use Tyres Made From Recyclable Materials On Its Vehicles
- By TT News
- July 10, 2025
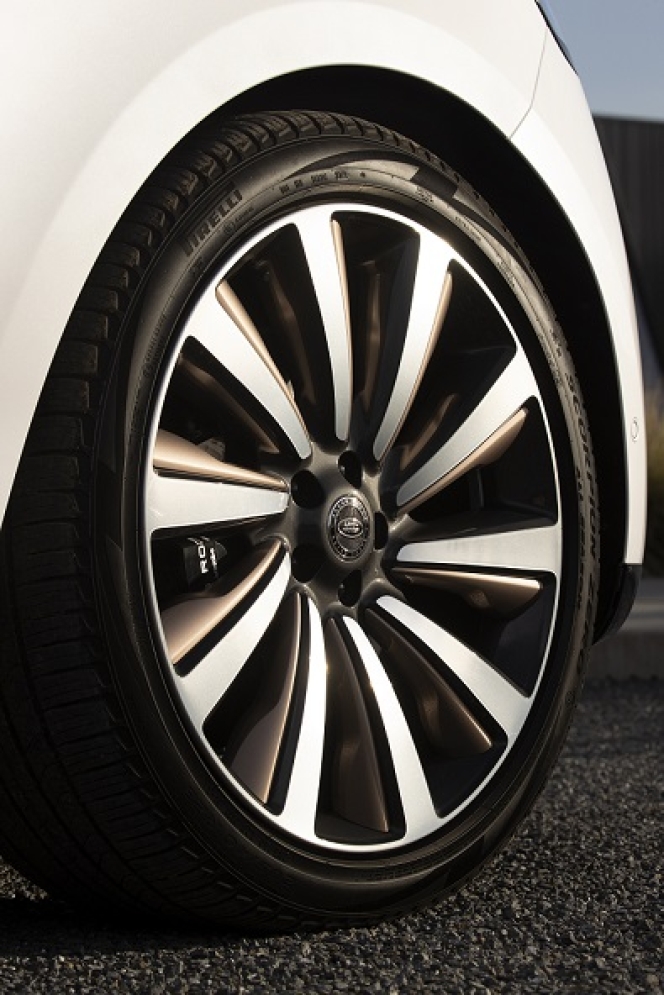
Tata Motors-owned British-luxury brand Jaguar Land Rover is said to become the first global automaker to commit to use tyres made from renewable materials as part of its sustainability commitment.
The automaker will soon become the first to soon adopt tyres made from more than 70 percent renewable and recycled materials, such as silica from rice husks and plant‑based resins at scale in its upcoming range of vehicles. In fact, the upcoming select models from Range Rover are already planned to come with Pirelli’s new P Zero tyres, which contain silica used to enhance wet performance. The material is sourced from rise husks, a natural by-product of rice milling.
These tyres do away with fossil‑based polymers and resins, which are typically used to help optimise the balance between dry and wet performance. Instead, they use plant‑based alternatives such as agricultural by‑products or used cooking oils. By using recycled materials, they reduce reliance on primary source materials to help alleviate resource consumption. Furthermore, carbon black, a crucial filler in rubber compounds used to improve stability, strength and durability, is recovered from end‑of‑life tyres and recycled steel is used to enhance handling and stability.
The automaker believes that bio‑based and recycled materials are generally more sustainable to obtain, more energy efficient to process and easier to manage at end‑of‑life than virgin and fossil‑based materials such as synthetic polymers and silica obtained from conventional materials such as quartz sand, yet perform similarly.
Reuben Chorley, Sustainable Industrial Operations Director, Jaguar Land Rover, said, “This is another example of how JLR is leading on sustainable design innovation in collaboration with its supply chain partners to deliver at scale, while reducing the environmental impact of our products. Achieving a more sustainable composition without compromising quality and performance is a challenge because of the complexity of tyre design. But working closely with Pirelli and leveraging both company’s expertise in procurement and engineering, we have been able to deliver this industry first.”
JLR and Pirelli are strengthening their commitment to sustainability with the introduction of the new P Zero tyre, featuring FSC (Forest Stewardship Council)-certified natural rubber. This initiative builds on JLR's pioneering move last year to incorporate FSC-certified natural rubber across its entire vehicle portfolio, ensuring responsible sourcing within its supply chain.
Both companies are dedicated to increasing the use of recycled and bio-based materials in their products. All such materials will undergo third-party certification to verify their quality and quantity. The long-term ambition for JLR and Pirelli is to achieve 100 percent sustainable materials in their tyres.
Prism Worldwide Unveils Major Innovations In Recycled Tyre Materials
- By TT News
- July 10, 2025
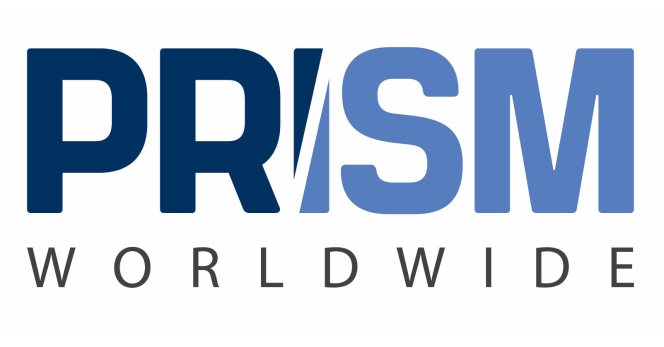
Prism Worldwide, a pioneer in converting discarded tyres and plastic waste into high-value circular polymers, has introduced three revolutionary advancements that promise to reshape the sustainable materials landscape. The company's breakthroughs in eliminating rubber odours, creating tyre-derived thermoplastic vulcanizates (TPV) and enabling high-content EPDM recycling address longstanding obstacles that have hindered widespread adoption of recycled materials across industries.
The company's cost-efficient, American-made production methods offer significant savings compared to virgin materials – a critical advantage amid fluctuating tariffs and increasing demand for domestic supply chains. This economic benefit allows manufacturers to embrace sustainable solutions without compromising profitability, removing a major barrier to eco-friendly material adoption.
Prism's innovations enable manufacturers to seamlessly integrate up to 50 percent recycled tyre content into existing production processes like injection moulding and extrusion – a dramatic improvement over previous limitations. This technological leap expands applications beyond traditional compression moulding, allowing for odour-free recycled materials in premium products like automotive interiors and fitness equipment.
The company's odour-elimination technology, rigorously tested to meet automotive industry standards, solves one of recycling's most persistent challenges. Equally groundbreaking is Prism's development of sustainable TPV derived entirely from end-of-life tyres – an industry first that creates new possibilities for high-value applications. Equally significant is their breakthrough in EPDM recycling, overcoming the material's inherent resistance to reuse through an innovative devulcanisation process that maintains critical performance characteristics.
These collective advancements represent more than incremental improvements – they fundamentally redefine what's possible with recycled materials. By tackling odour, performance and cost challenges simultaneously, Prism is transforming sustainability from a compliance obligation into a competitive advantage.
Bob Abramowitz, CEO, Prism Worldwide, said, “This is a turning point for end-of-life tyre recycling and sustainable polymer development. These are not incremental improvements. We’ve tackled odour, cost and performance, three of the biggest barriers to more widespread adoption of recycled materials, and overcome them all with commercially viable solutions. Our team’s diligence in developing solutions that solve these challenges allows us to deliver cost-effective, high-performance materials without requiring customers to pay a green premium. Companies pay lip service to sustainability values, but they change their tune when it costs more. We are creating additional profit opportunities while helping them to meet corporate sustainability objectives.”
Comments (0)
ADD COMMENT