WHEN ADDITIVES BECOME FUNCTIONAL, NEW POSSIBILITIES EMERGE!
- By Colin Clarke
- December 23, 2020
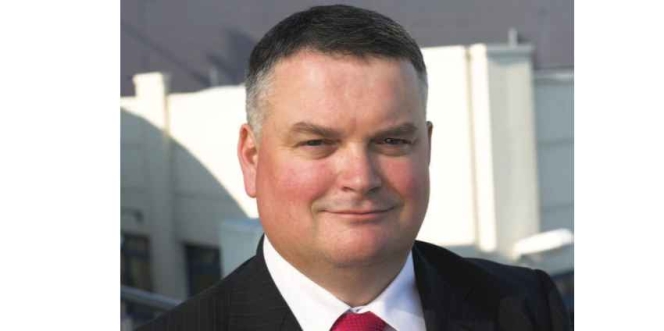
Polymer producers have responded to the changing tyre industry expectations, their innovations take into account a more reactive functionality within polymer architecture, and this is closely matched by increasingly greater degrees of filler surface chemistry. As a result, tyre compound properties may now be tailored to meet quite specific tyre performance targets.
Tyre processing methods also underwent progressive stages of modernisation in recent years, for example, more sophisticated reactive mixing technology together with high-speed extrusion systems allowing for direct extrusion onto the building drum become established as cost effective production routes for many of the major producers.
These advancements however bring about their own conflicts, processing pathways involving multiple stages, often with the ability to rework compound or adjust rheological properties by additional time or energy input during the process are no longer viable options for most tyre producers. It has thus become necessary to achieve processability through an increasingly narrow operating window.
Formulations optimised to achieve peak tyre performance in most cases also tend towards more challenging processing characteristics. This is to be expected; the use of high and narrow molecular weight reactive polymers alongside fillers having high surface area and chemistry, often in loadings above that of the polymer are the norm. The trend towards usage of high loading of plasticiser and resinous materials to adjust tyre tread grip and traction response all contribute to a less forgiving processing nature. Often those compounds that are highly reinforced appear the most fragile during processing and poor green strength with an easily tearing or crumbly compound appearance are often-discussed processability issues. By contrast, the use of high loadings of resins and plasticisers, for example in winter or high-performance tyre formulations, results in compounds that during processing can more resemble chewing gum than tyre treads!
The use of process additive chemicals in an attempt to overcome the processing limitations observed gives rise to further conflicts; Lubricant additives might improve compound surface appearance; however, green strength will probably further reduce due to the unwanted softening effect. The same is true for release additives where lower tack unfortunately remains at a higher value than the also lowered tensile strength of the compound. Filler dispersion is often targeted by additives, however higher loading of fillers mandate equally higher additive loadings, we should more accurately discuss loading as “parts per hundred of filler” not rubber, and under the appropriately higher additive loading, the risk of interference with vulcanisation properties or even additive migration leading to surface bloom become realistic concerns.
Conflicting performance characteristics
The development team at Schill + Seilacher has recognised the need to decouple conflicting performance characteristics found within conventional process additive chemistries. As a result, innovation within our Struktol® range offers tyre compounders opportunities to achieve processability without compromise.
Reduced viscosity leading to better extruder flow properties and improved surface appearance, whilst at the same time achieving an increased compound green strength can be realised by use of Struktol HT 300, a new generation of reactive process additive.
An extract of key processing and property influence in a typical highly silica filled sSBR tread compound are highlighted in the following data.
|
Control |
Struktol HT 300 6 phr |
Struktol HT 300 12 phr |
Mooney ML (1+4) 100 °C (MU) |
75 |
65 |
53 |
Loss of batch weight due to sticking in the mixer (%) |
1.9 |
0.6 |
0.4 |
Significantly lowered Mooney viscosity as well as better mixer batch off with reduced sticking to the mixer rotor and gate with Struktol HT 300 are observed.
An increase in compound green strength was obtained by the addition of Struktol HT 300; this is the opposite of expectation for conventional process additive chemistry, where reduced viscosity is obtained. In addition, the filler dispersion as evidenced by a reduction in the so-called “Payne Effect” as tested in uncured compound by means of RPA strain sweep, is also improved.
Lab extrusion trials, using cold feed extruder demonstrate improved surface appearance and lower compound pressure achieved by use of Struktol HT 300, both desirable processing conditions.
|
Control |
HT 300 6 phr |
HT 300 12 phr |
Hardness |
66 |
67 |
65 |
Abrasion loss (DIN) |
113 |
102 |
106 |
Physical properties are also acceptable, with a progressive increase in tensile strength an elongation and maintenance of stiffness with loading of 6 phr of process additive, only at higher loading of 12 phr would a balancing slight reduction in process oil be required.
Compound hardness remained unchanged alongside improved wear resistance, as measured by DIN abrasion loss testing, even when using higher loading of process additive, are important aspects.
The ability to decouple the relationship between lubrication, important for improved rheological behaviour, and the maintenance of strength and stiffness in both the uncured and vulcanised condition is only possible with such new and innovative class of process additive. This departure from conventional thinking offers the tyre compounder significant degree of freedom to retain the benefits in terms of easier processability without sacrifice of key tyre performance properties.

In this example, the use of Struktol HT 300 prioritised green strength alongside reduced viscosity. By contrast, our new Struktol HT 250 decouples release from other properties, especially effective for winter tyre tread; compound stickiness is resolved without compromise of viscoelasticity.
Ensuring that migration and ultimately bloom within rubber compounds is kept to the lowest level is important for final article aesthetics, for tyres additional considerations arise; they are composite structures, therefore it is imperative that chemicals do not migrate across boundary layers in an uncontrolled manner, which could result in changed behaviour or interfacial adhesion failure over time. In order to limit migration, the compatibility, solubility and concentration of chemicals are carefully considered. However, one method of ensuring long-term stability involves chemically binding the additive within the vulcanisation network.
At Schill + Seilacher, we have achieved this degree of crosslinking capability for a number of new-generation Struktol process additives. Their usage allows the compounder to avoid completely the risk of migration and bloom due to additive presence.
Photographs of two vulcanised rubber sheets based on the same formulation. On the left-hand side, evidence of typical surface bloom, which may occur due to migration of a conventional process additive, on the right, containing reactive additive Struktol HT 600 as replacement, it can be seen that bloom was eliminated.
This technology also opens tremendous opportunities to “fix” process additives in place within the respective component, the role of additives withinthe cross-linking mechanism may additionally lead to vulcanisate performance characteristics.

One interesting tyre related example involves the development of a superior tyre curing bladder performance, here we have developed new reactive plasticisers called Struktol HT 815 and Struktol HT 820, their use is directed towards resin-cured butyl rubber. This combination of polymer and curing system provides for superior heat resistance with excellent flex fatigue resistance and is used as the basis for tyre curing bladders. Here the replacement of widely used castor oil as plasticiser with new Struktol HT 800 series product leads to a significantly improved bladder performance life, with greater stability in viscoelastic properties. Reduced stiffening of the bladder, due to lower degree of plasticiser migration translated into a much lower flex-cracking rate, especially after high temperature steam ageing.
Reactive Struktol plasticisers, HT 815 and HT 820 exhibit a significantly reduced flex cracking rate when compared to the widely used castor oil, which readily migrates from the bladder; as a result, significant extension of bladder service life is possible.
New reactive process additives, with tailored functionality to closely match the specific chemistry of polymers, fillers and cure systems are actively developed. These innovative products under the Struktol brand offer tyre compounders a more comprehensive toolkit in order to tailor compound performance to meet tyre performance demands. The conflicts of property versus processability diminish and new possibilities emerge!
ARLANXEO Launches Sustainable Rubber Portfolio in India as Demand for Green Materials Grows
- By TT News
- August 01, 2025
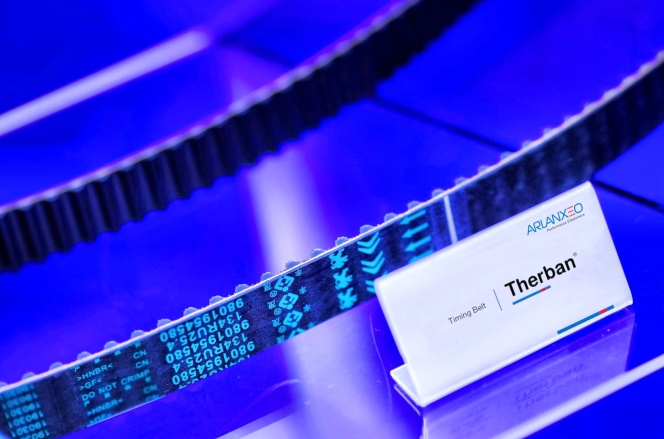
ARLANXEO has launched its ISCC PLUS-certified Keltan Eco rubber grades in India, responding to rising demand for sustainable materials in the world’s most populous nation.
The German-based performance elastomers manufacturer unveiled the portfolio through technical seminars and workshops, targeting automotive components, wires and cables applications where customers increasingly value environmental credentials.
The Keltan Eco range comprises Eco-B and Eco-BC grades derived from bio-based and bio-circular feedstocks, respectively, whilst maintaining identical physical and mechanical properties to conventional fossil fuel-based products. The materials offer resistance to oxygen, ozone, heat and radiation.
ARLANXEO employs a mass balance approach for certification, ensuring the volume of Eco-labelled products corresponds with sustainable source feedstock volumes. This methodology provides supply chain transparency and enables customers to verify sustainability claims in downstream applications.
“This new portfolio will help our customers seize sustainable growth opportunities in India and stay ahead amid industry transformation,” said Rupesh Shah, ARLANXEO India’s Managing Director and Regional Sales Head.
The company also showcased its Therban hydrogenated nitrile butadiene rubber speciality grades during the events, targeting original equipment manufacturers and component producers. Therban applications include air conditioning seals, timing belts, high-temperature gaskets for oil platforms and spacecraft components.
ARLANXEO operates as one of the world’s largest synthetic rubber producers with more than 10 production sites across eight countries and four research and development locations globally. The company serves automotive, tyre, electrical, construction and oil and gas sectors.
The Indian launch forms part of ARLANXEO’s broader strategy to expand sustainable product offerings across key growth markets. Additional ISCC PLUS-certified synthetic rubber grades will be introduced in India following the initial rollout.
India’s steady rubber consumption growth, driven by the automotive and infrastructure sectors, signals a significant opportunity for speciality chemical producers aiming for sustained market expansion. ARLANXEO is well-positioned to meet this demand, marking a decisive step toward a greener, more innovative rubber industry in India.
Rathi Group Marks Major Milestone With First Export Of ISCC-Certified Pyrolysis Oil
- By TT News
- August 01, 2025
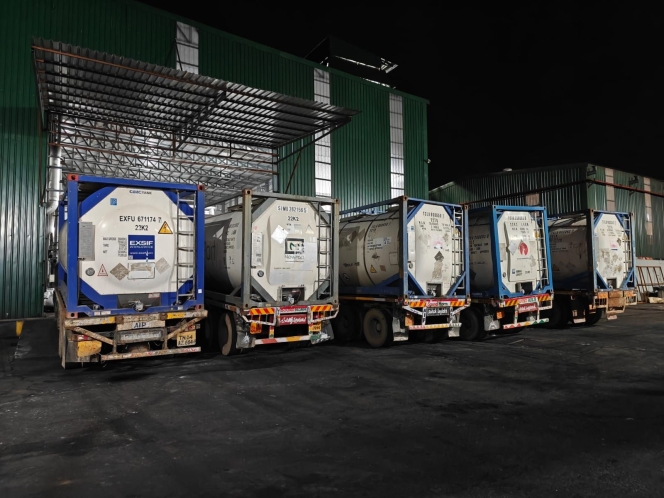
Rathi Group, a leader in pyrolysis and end-of-life tyre (ELT) recycling, has achieved a significant milestone with its first export shipment of ISCC PLUS-certified pyrolysis oil. With over 12 years of industry expertise, the company continues to set benchmarks in sustainable recycling, innovation and circular economy practices.
This landmark export highlights Rathi Group’s ability to supply globally recognised, eco-friendly alternatives to conventional fossil fuels. The company’s integrated operations – spanning ELT shredding, continuous pyrolysis, carbon black recovery and oil distillation – adhere to stringent international sustainability standards.
The ISCC PLUS certification underscores Rathi Group’s commitment to environmental responsibility, supply chain transparency and climate-conscious solutions. The accomplishment reflects the efforts of its dedicated team and partners, reinforcing the company’s mission to drive impactful change in sustainable tyre recycling.
- Kraton Corporation
- Speciality Polymers
- Renewable Biomaterials
- EcoVadis Platinum Rating
- Sustainability
Kraton Releases 2024 Sustainability Report Showcasing Sustainable Innovation
- By TT News
- July 30, 2025
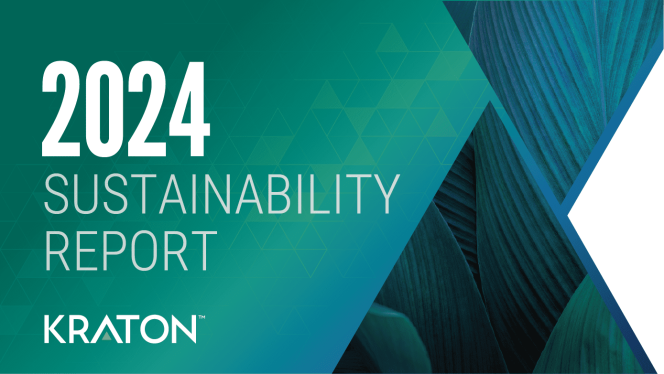
Kraton Corporation, a global leader in speciality polymers and renewable biomaterials, has published its 2024 Sustainability Report, Innovating with Purpose. The report outlines the company’s advancements in climate action, circular product solutions and supply chain sustainability, reinforcing its commitment to a greener future.
Key achievements include a 41 percent reduction in Scope 1 & 2 emissions since 2014, a 35 percent decrease in emissions intensity and maintaining EcoVadis’ Platinum rating for the fourth straight year. Kraton also received the 2024 Nitto Supplier Sustainability Award and conducted a Double Materiality Assessment to refine its ESG strategy.
Operational milestones feature a USD 35 million upgrade to its Florida biorefinery, expanded lifecycle assessment (LCA) data covering 90 percent of its product portfolio and a new data excellence programme to enhance ESG transparency.
Aligned with GRI, SASB, UN Global Compact and TCFD frameworks, the report emphasises Kraton’s sustainability pillars: Reliable Partnerships, Planetary Stewardship and Empowering People. These efforts reflect the company’s dedication to responsible innovation and measurable environmental progress.
Marcello Boldrini, CEO, Kraton, said, “2024 marked a pivotal year in Kraton’s sustainability journey. We turned ambition into action, significantly reducing our Scope 1 and 2 emissions by 41 percent from our 2014 baseline and earned an EcoVadis Platinum rating for the fourth consecutive year. We accelerated our decarbonisation strategy, advanced biobased innovation and partnered with customers such as WJ Group and Henkel to help address global sustainability challenges. As demand for sustainable chemicals grows, our focus remains on developing the right solutions, fostering strong partnerships and cultivating the culture necessary to lead this transformation responsibly and competitively.”
Rogier Roelen, Chief Sustainability Officer, Kraton, said, “We have established new processes to scale credible, data-driven sustainability across our business. In 2024, we enhanced our ESG reporting through a data harmonisation programme and completed a Double Materiality Assessment to better align with the Corporate Sustainability Reporting Directive (CSRD). We also expanded our Life Cycle Assessment (LCA) data to cover almost 90 percent of our product portfolio, providing customers with greater transparency into the environmental impact of our products. These efforts reinforce our ability to identify where we can make the most impact and support more informed, strategic decision-making.”
German Rubber Industry Faces Mixed Outlook Amid Persistent Challenges: wdk
- By TT News
- July 30, 2025
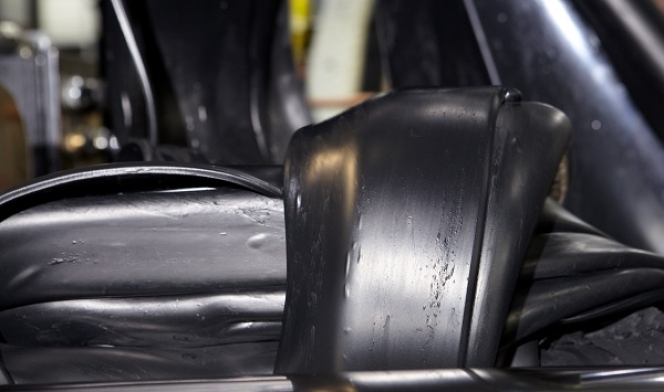
The German rubber industry is undergoing significant shifts, according to the German Rubber Industry Association (wdk) in its mid-2025 economic report. While order trends show improvement for the first time in years, domestic production continues to struggle, reflecting broader structural challenges.
High energy costs, excessive bureaucracy and rising labour expenses remain persistent hurdles, particularly for globally competitive firms. Although rising orders may boost annual sales slightly compared to 2024, domestic output is expected to decline by one percent. Many companies are relocating production abroad due to Germany’s worsening cost disadvantages.
The federal government’s ‘investment booster’ initiative has failed to inspire confidence, with only 27 percent of industry leaders anticipating positive effects. wdk President Michael Klein described this as an alarming sign, emphasising that businesses lack faith in current economic policies. He urged immediate relief measures rather than delayed solutions.
Klein also stressed the need for inclusive policymaking, criticising the government’s focus on large corporations while neglecting small and medium-sized enterprises (SMEs). He warned that without targeted support for these critical players, Germany risks losing its status as a key industrial hub for the rubber sector. The call for urgent action highlights growing concerns over the industry’s future viability in the country.
Comments (0)
ADD COMMENT