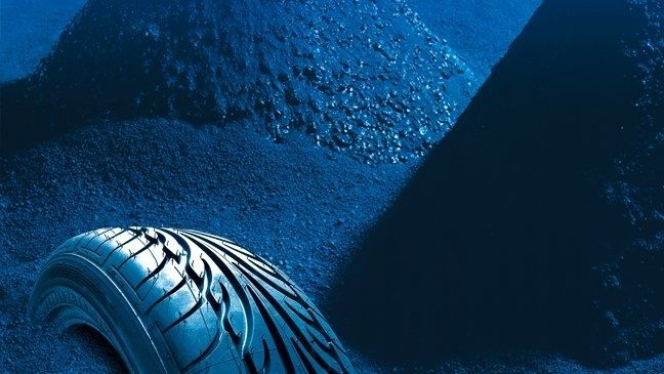
Zeppelin Systems has been awarded the engineering contract for constructing a second ReOil pyrolysis plant, with construction slated to commence in February 2024.
By establishing this new pyrolysis plant, ReOil has significantly expanded its annual recycling capacity, now capable of processing approximately 60,000 tons per year. This state-of-the-art facility, covering roughly 27 acres, is a testament to the ingenuity and engineering expertise provided by Zeppelin Systems.
Having already supplied the initial engineering groundwork for the new plant in 2019, Zeppelin Systems has been awarded the completion contract, underscoring the high level of customer satisfaction. As the primary engineering partner, Zeppelin Systems delivers comprehensive turnkey solutions, encompassing plant technology, process engineering, and final plant planning, all from a single source.
“A flagship project for Zeppelin Systems with a signalling effect. Only a few companies can implement such complex and extensive projects virtually anywhere in the world,” says Dr Markus Vöge, CEO of Zeppelin Systems GmbH, adding: “The aim is to offer process solutions in the future that can be provided as part of license models. For example, the ELT pyrolysis plant as a turnkey product from Zeppelin Systems.” Guido Veit, Vice President of Sales, Plastic and Rubber at Zeppelin Systems GmbH, adds: “ReOil’s engineering contract is the first project as part of the Zeppelin Sustainable Tyre Alliance. This makes us proud and demonstrates the strength of the alliance. In addition, we will continue to work hard to bring additional processes to technological maturity and strengthen the network in terms of the circular economy.”
ReOil Managing Director Paweł Mikuśkiewicz is also delighted with the very successful partnership between Zeppelin Systems and ReOil: “We knew that this major project could only be planned and built with the help of an experienced and internationally active plant engineering partner. That’s why we chose Zeppelin Systems, and we really appreciate our long-standing, trusting business relationship.”
Zeppelin Systems, a trusted partner in plant engineering for the rubber and tyre industry, has taken a significant step towards a more sustainable future by launching the Zeppelin Sustainable Tire Alliance in March 2023. This collaborative initiative aims to work alongside global partners in reshaping the tyre production and recycling process in a more environmentally conscious manner.
Among the esteemed members of this technology alliance is the Polish firm ReOil, known for establishing Europe’s largest pyrolysis plant dedicated to recycling old tyres in 2015. Over the years, ReOil has successfully recycled approximately 20,000 tonnes of old tyres annually. Once operational, this colossal plant is expected to reintegrate about 60,000 tonnes of old tyres into the sustainable circular economy annually.
ReOil, a leading operator in raw material recycling, employs continuous pyrolysis to break down rubber from discarded tyres into valuable substances like gas, oil and recovered Carbon Black (rCB). These recycled materials find application in various industries, including textiles, tyre manufacturing, rubber components, plastics, steel production, and even aviation fuel. Since its commissioning in 2015, ReOil has effectively recycled around 70,000 tonnes of old tyres, reaching a stable and profitable operational state in 2020.
ARLANXEO Launches Sustainable Rubber Portfolio in India as Demand for Green Materials Grows
- By TT News
- August 01, 2025
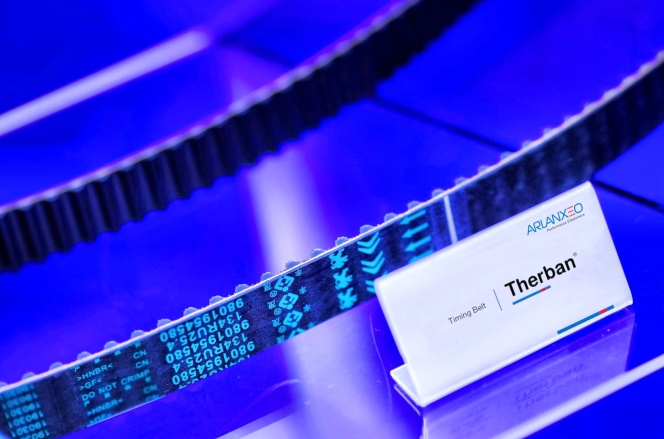
ARLANXEO has launched its ISCC PLUS-certified Keltan Eco rubber grades in India, responding to rising demand for sustainable materials in the world’s most populous nation.
The German-based performance elastomers manufacturer unveiled the portfolio through technical seminars and workshops, targeting automotive components, wires and cables applications where customers increasingly value environmental credentials.
The Keltan Eco range comprises Eco-B and Eco-BC grades derived from bio-based and bio-circular feedstocks, respectively, whilst maintaining identical physical and mechanical properties to conventional fossil fuel-based products. The materials offer resistance to oxygen, ozone, heat and radiation.
ARLANXEO employs a mass balance approach for certification, ensuring the volume of Eco-labelled products corresponds with sustainable source feedstock volumes. This methodology provides supply chain transparency and enables customers to verify sustainability claims in downstream applications.
“This new portfolio will help our customers seize sustainable growth opportunities in India and stay ahead amid industry transformation,” said Rupesh Shah, ARLANXEO India’s Managing Director and Regional Sales Head.
The company also showcased its Therban hydrogenated nitrile butadiene rubber speciality grades during the events, targeting original equipment manufacturers and component producers. Therban applications include air conditioning seals, timing belts, high-temperature gaskets for oil platforms and spacecraft components.
ARLANXEO operates as one of the world’s largest synthetic rubber producers with more than 10 production sites across eight countries and four research and development locations globally. The company serves automotive, tyre, electrical, construction and oil and gas sectors.
The Indian launch forms part of ARLANXEO’s broader strategy to expand sustainable product offerings across key growth markets. Additional ISCC PLUS-certified synthetic rubber grades will be introduced in India following the initial rollout.
India’s steady rubber consumption growth, driven by the automotive and infrastructure sectors, signals a significant opportunity for speciality chemical producers aiming for sustained market expansion. ARLANXEO is well-positioned to meet this demand, marking a decisive step toward a greener, more innovative rubber industry in India.
Rathi Group Marks Major Milestone With First Export Of ISCC-Certified Pyrolysis Oil
- By TT News
- August 01, 2025
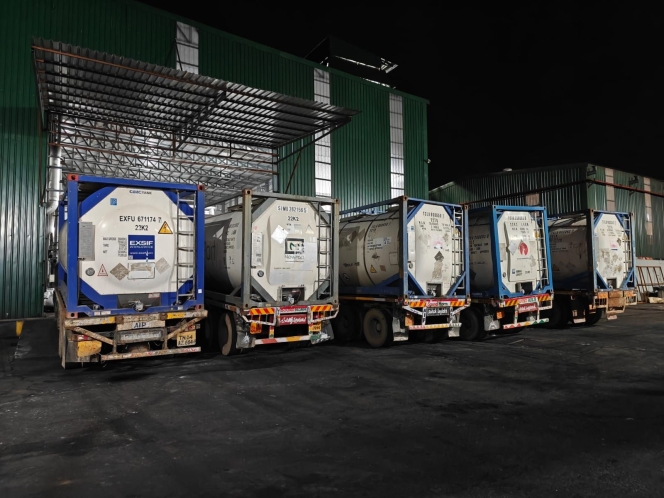
Rathi Group, a leader in pyrolysis and end-of-life tyre (ELT) recycling, has achieved a significant milestone with its first export shipment of ISCC PLUS-certified pyrolysis oil. With over 12 years of industry expertise, the company continues to set benchmarks in sustainable recycling, innovation and circular economy practices.
This landmark export highlights Rathi Group’s ability to supply globally recognised, eco-friendly alternatives to conventional fossil fuels. The company’s integrated operations – spanning ELT shredding, continuous pyrolysis, carbon black recovery and oil distillation – adhere to stringent international sustainability standards.
The ISCC PLUS certification underscores Rathi Group’s commitment to environmental responsibility, supply chain transparency and climate-conscious solutions. The accomplishment reflects the efforts of its dedicated team and partners, reinforcing the company’s mission to drive impactful change in sustainable tyre recycling.
- Kraton Corporation
- Speciality Polymers
- Renewable Biomaterials
- EcoVadis Platinum Rating
- Sustainability
Kraton Releases 2024 Sustainability Report Showcasing Sustainable Innovation
- By TT News
- July 30, 2025
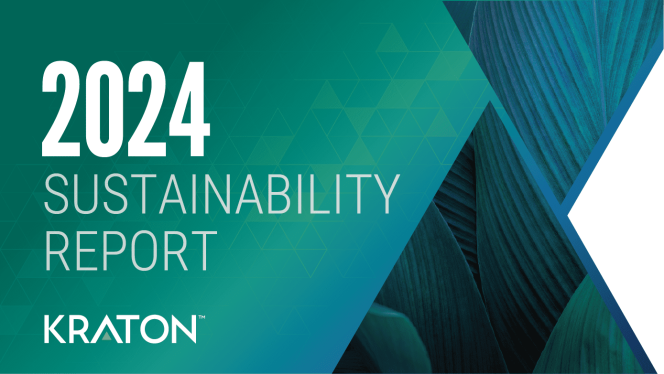
Kraton Corporation, a global leader in speciality polymers and renewable biomaterials, has published its 2024 Sustainability Report, Innovating with Purpose. The report outlines the company’s advancements in climate action, circular product solutions and supply chain sustainability, reinforcing its commitment to a greener future.
Key achievements include a 41 percent reduction in Scope 1 & 2 emissions since 2014, a 35 percent decrease in emissions intensity and maintaining EcoVadis’ Platinum rating for the fourth straight year. Kraton also received the 2024 Nitto Supplier Sustainability Award and conducted a Double Materiality Assessment to refine its ESG strategy.
Operational milestones feature a USD 35 million upgrade to its Florida biorefinery, expanded lifecycle assessment (LCA) data covering 90 percent of its product portfolio and a new data excellence programme to enhance ESG transparency.
Aligned with GRI, SASB, UN Global Compact and TCFD frameworks, the report emphasises Kraton’s sustainability pillars: Reliable Partnerships, Planetary Stewardship and Empowering People. These efforts reflect the company’s dedication to responsible innovation and measurable environmental progress.
Marcello Boldrini, CEO, Kraton, said, “2024 marked a pivotal year in Kraton’s sustainability journey. We turned ambition into action, significantly reducing our Scope 1 and 2 emissions by 41 percent from our 2014 baseline and earned an EcoVadis Platinum rating for the fourth consecutive year. We accelerated our decarbonisation strategy, advanced biobased innovation and partnered with customers such as WJ Group and Henkel to help address global sustainability challenges. As demand for sustainable chemicals grows, our focus remains on developing the right solutions, fostering strong partnerships and cultivating the culture necessary to lead this transformation responsibly and competitively.”
Rogier Roelen, Chief Sustainability Officer, Kraton, said, “We have established new processes to scale credible, data-driven sustainability across our business. In 2024, we enhanced our ESG reporting through a data harmonisation programme and completed a Double Materiality Assessment to better align with the Corporate Sustainability Reporting Directive (CSRD). We also expanded our Life Cycle Assessment (LCA) data to cover almost 90 percent of our product portfolio, providing customers with greater transparency into the environmental impact of our products. These efforts reinforce our ability to identify where we can make the most impact and support more informed, strategic decision-making.”
German Rubber Industry Faces Mixed Outlook Amid Persistent Challenges: wdk
- By TT News
- July 30, 2025
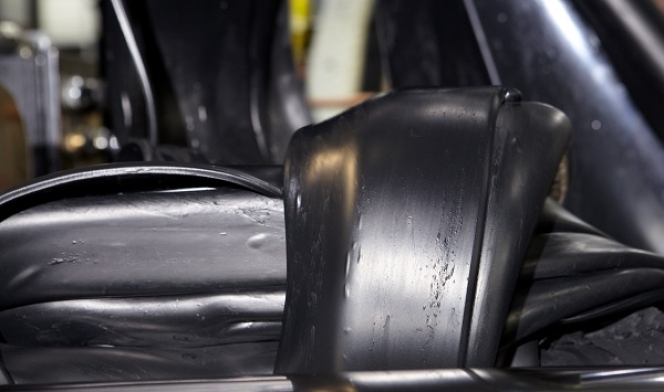
The German rubber industry is undergoing significant shifts, according to the German Rubber Industry Association (wdk) in its mid-2025 economic report. While order trends show improvement for the first time in years, domestic production continues to struggle, reflecting broader structural challenges.
High energy costs, excessive bureaucracy and rising labour expenses remain persistent hurdles, particularly for globally competitive firms. Although rising orders may boost annual sales slightly compared to 2024, domestic output is expected to decline by one percent. Many companies are relocating production abroad due to Germany’s worsening cost disadvantages.
The federal government’s ‘investment booster’ initiative has failed to inspire confidence, with only 27 percent of industry leaders anticipating positive effects. wdk President Michael Klein described this as an alarming sign, emphasising that businesses lack faith in current economic policies. He urged immediate relief measures rather than delayed solutions.
Klein also stressed the need for inclusive policymaking, criticising the government’s focus on large corporations while neglecting small and medium-sized enterprises (SMEs). He warned that without targeted support for these critical players, Germany risks losing its status as a key industrial hub for the rubber sector. The call for urgent action highlights growing concerns over the industry’s future viability in the country.
Comments (0)
ADD COMMENT