Making Tyre Testing Easier
- By Sharad Matade & Juili Eklahare
- February 13, 2023

Where would our vehicles be if their tyres weren’t appropriately tested? Well, probably not in the best or safest condition. While it’s thanks to testing companies, it’s no less thanks to testing solutions and equipment manufacturers, too. The latter’s accuracy and reliability make the former’s job easier, making our tyres safer and more efficient as vehicle wheels. In a tete-a-tete with Tyre Trends, Markus Winter, Director – Sales and Marketing, Kokusai Europe GmbH, a leading test and measurement solutions manufacturer founded in Tokyo, Japan, threw light on testing strategies, the need for indoor tyre testing, the company’s plan to establish itself in Europe and more. Read on…
Kokusai began as a sales company for dynamic balancing equipment and has since grown to become a major supplier in the Japanese and Asian industries. The test and solutions manufacturer really started with the balancing of electronical components, which was a huge business about 30 to 40 years ago. It is still a business of Kokusai’s, of course – the balancing of smaller part vans, electrical motors etc.
However, while transitioning to test and measurement (for the tyre industry in particular), it was testing for automotive parts. “And when it comes to automotive parts, it is the tyres, other rotary parts, shafts and drive shafts etc,” Markus Winter, Director – Sales and Marketing, Kokusai, told us. “So it was clear that in an encapsulated market, you start with everything that rotates. And therefore, Kokusai started with all the automotive components, and then tyres and wheels. In fact, we are the leading supplier in Asia. Moreover, we have expanded to the United States with a subsidiary 30 years ago. Plus, we expanded to Europe about five years ago,” he said.
Kokusai’s presence in Europe
In truth, Kokusai is available around the world but is just establishing itself in Europe more and more, which is part of the global strategy. “We do have a lot of very unique testing solutions that are not available in other markets. This is because other markets develop from Asia into Europe,” Winter pointed out.
Kokusai’s equipment
Speaking of interesting testing solutions, Winter asserted that they have tyre performance and tyre wear testing equipment, where they are just leading the market with the innovative ideas that Kokusai has developed.
“For example, for tyre performance testing, we have some competition from the United States and Europe,” Winter explained. “However, we have developed, for instance, an indoor 50-metre flat testing equipment to test tyre performance parameters – the machine named FLATROAD TESTER. And this, in fact, is the test bench with the highest repeatability that is available in the market. As for Kokusai, we have a solution where we accelerate the traversing carriage with a single tyre. We can manipulate all parameters in real-time during the movement and record the measured performance values.”
Winter further went on to throw light on testing the performance of a tyre on FLATROAD TESTER. He cited, “Our mechanical system is like a high-speed linear axis – it is computer controlled and has the precision of a Japanese CNC machine.”
“Hence, we can control all the parameters on the tyre in such a precise way that it’s not like driving a car and pressing the brake. We are exactly controlling the movement and rotation of the tyre. So it is more precise – it’s like having a CNC machine doing the testing,” Winter explained.
“There is another point that makes this kind of indoor testing more reliable,” Winter continued. “Using our indoor test bench, all the outer surrounding conditions affecting the measurement are significantly reduced. Hence, we can do the testing, and the results we measure are the real tyre behaviour between the tyre and the road, without any influence of weather, the driver skills or driving behaviour, car suspension or pavement. It is such a massively built machine equipment that one can be really assured of avoiding all the external factors and focus on the effects between the tyre and the road.”
Surrounding atmospheres affecting the testing
While it is an excellent circumstance to be able to focus completely on the parameters between the tyre and the road, it’s always safer to be aware of the external factors that might come in the way.
“Those are mainly humidity and temperature,” Winter told us. “If you’re doing outdoor testing, starting early in the morning and the sun shining on the pavement, you have a pavement temperature of maybe 15 degrees. If you’re doing breaking tests, it will really affect the results. Additionally, if there’s higher humidity, then there’s a little bit more of sliding that takes place.”
“Of course, you can conduct very long tests over a span of many days,” he further highlighted. “Hence, if you conduct the outdoor testing for a few weeks and also use reference tyres, then you can compensate a lot.”
“In fact, one can put on one tyre on our measurement machine and run it three times, and the measurement curves will be overlapping perfectly three times. That would be the final result,” Winter put across.
More knowledge, better tyres
Outdoor testing brought us to the subject of tracks. This is when Winter informed us that Kokusai has analysed tracks. The complete 50 metres installed in the machine are divided into exchangeable segments.
Winter pointed out that they can use individual road segments with different surface characteristics in the area where they are doing the test. “We can look into factors such as what kind of friction do we want to have, what kind of macro structure do we need, do we want to have the stepping from a high friction value to a low friction value and so on,” he shared. “Thus, we can manipulate all the surfaces, do the testing and then see the effect.”
However, outdoor testing can be complicated, and sometimes they need to test on different standard asphalt pavements, tiles, water floating etc. “In such scenarios, we can exchange the pavement segments at our tester and do another test, which is much easier,” Winter explained. “Moreover, with the knowledge of these small changes – which even the tyres will go through from one test to another – the tyre development engineers will have more detailed information in order to take better steps in the development of the tyre. This is because the repeatability of our processes is so high. Of course, if you have an outdoor process, you can conduct a certain number of tests and do an average. But if your sigma is already that high, you don’t know if you’re developing into the right direction.”
Good or bad tyre?
While every aspect of testing is taken care of by the testing companies themselves, we know that customer demands are changing every day. If we consider a tyre, there are two different departments that Kokusai is serving. “One is tyre testing,” Winter put across. “When it comes to tyre testing, it involves the results for tyre engineering, tyre development, performance testing, wet grip testing, wear testing and so on. This is in order to meet regulations, or to even just develop the best tyres.”
The second part of the Kokusai production is the final finished testing. “This involves the end-of-the-line testing,” Winter further explained. “This is dynamic balance testing, uniformity testing and geometrical testing. However, we’re not doing X-ray. But we’re specialised in dynamic balancing, uniformity and the geometrical measurement. So companies do expect a low cycle time because they want to test as many tyres as possible. In addition, the testing equipment should not be the bottleneck for tyre production.”
Of course, stating the obvious, Winter told us that testing companies and tyre companies need high accuracy and repeatability. This is because only when they have very high accuracy on the testing equipment that they can make calls on whether the tyre is an okay tyre or if it needs to be rejected or downgraded etc.
“A tyre is not always good or bad – it is graded, and only the best tyres are available for the OEMs,” he pointed out. “As for the others, they might be available for the aftermarket, while some go through refinishing in order to get them to a better rate. A very accurate equipment allows the tyre manufacturer to do a very precise grading, which saves costs. And it is better to invest a little more in the precise grading technology than to scrap the tyre or to put it back into the process.”
Tyre wear test
No matter how, tyre testing goes beyond this. Here, we came to discuss tyre wear testing. Winter told us that a standard outdoor tyre wear test entails driving a couple of cars in convoy on selected routes in public road traffic.
“You have a representative circuit in a region with low traffic volume and stable weather forecast. The route needs to fit the logistics, such as hotels for the staff, a workshop, test equipment and so on,” Winter said.
He added, “Now you will drive the test tyres and a reference tyre in a convoy around the track in both directions and change the tyres and the drivers in a certain order. After a mileage of about 25,000 kilometres, you can well identify the wear results and the mass loss of the tyre.”
“This always takes a number of cars, and you have to do a high mileage on driving,” Winter further explained. “Normally, one can say that each kilometre driven on the car comes to about EUR 1 – that’s what we are calculating, including the driver.”
The cost of testing
While many discuss the cost of testing equipment, everybody also has to take the cost of tyre testing, along with the time, into consideration.
“That’s because you first need the tyre test, and then the results from that tyre test, in order to continue with your development,” Winter expounded. “So if you want to make a 25,000-kilometre test to see how a tyre is wearing over a certain distance, you have to conduct the test. The test takes one month, and once you have the results, you can move on to the next step. Therefore, there’s a waiting period of one month.”
Testing strategy for final finish
Nevertheless, is every tyre that we see out there tested at the end of the production process? That depends on the testing strategy of every respective company. Winter emphasised that normally one can say that newcomers or smaller companies are trying to test at least 100 percent for OEM tyres and may conduct some statistical testing for aftermarket tyres. The processes of the really well-known tyre manufacturers are so good that they can reduce to statistical testing. Therefore, it’s just a question of how good the process and the process in tyre building are.
“On the other hand, there are a lot of companies that are still in the learning curve or are cautious about getting some tyres rejected,” Winter said. “These companies are conducting 100 percent testing. But one can say that the very old, established tyre plants, from Continental to Michelin, are doing a lot of statistical testing.”
Staying together while far apart
Yet, tyre testing does not stop at the grading or the testing process. It becomes pivotal for testing equipment manufacturers to make sure that their solutions and equipment are aligned with the current and upcoming regulations of the tyre industry. For this, Kokusai has its sales and application colleagues around the world.
Winter shared, “Our colleagues in America have their network and talk with all the big tyre manufacturers, the government, and attend various conferences to get a feel for what is happening in the market. Our Chinese and Japanese colleagues, too, are doing the same.”
“So we have a high number of offices and manufacturing plants around the world and in all the very important areas,” he further highlighted. “We have a direct network and contact with them. Hence, that’s one of our advantages. Internally, we are putting all this information together to see where there’s an overlap. For example, I have discussions with our European contacts that I meet at site or conferences. And I ask them their views on aspects. My colleagues in the US and Asia do the same and forward their feedback. Hence, it is local networking on one side and then getting the information together again on the other side in order to concentrate that internally. So it’s a big task.”
With Kokusai’s large number of offices and manufacturing plants across the globe, and moreover, all of them being highly connected with one another, the company uses this connection to be flexible with its suppliers as well.
“As we have a manufacturing plant in Japan, Korea, China and the US, if there’s a bottleneck somewhere, we try to get the same components from suppliers that are normally supplying to our other plants,” Winter commented. “To boot, we are looking for some components from Europe and the United States as well. Hence, there are different local purchasing organisations that we have within our group, and if they need to help one another, then our supply chain is quite well organised for that.”
More on Europe
While Winter mentioned that Kokusai has sales and application colleagues around the world, that is also one of the reasons why the company is pushing for the European market. Its manufacturing plant in Europe is in the planning phase.
“Although we think that the basic technology is developed in Japan, this is the heart of our engineering,” Winter put across. “Besides, the localisation and customisation are made where the customers are located and where they have their specifications, their needs and even need their technical support, which is why we are going to develop the main system in Japan.”
“As you know, China wants that certain percentage of the equipment to be built on the site,” Winter further remarked. “And it’s the same in the United States as well. Thus, we are pre-manufacturing the systems in Japan, sending them over to the United States and then making the final assembly, with all the specific American needs, on site. We will be doing the same in Europe in order to compete better against our local competitors in Europe.”
Also, while the test and measurement manufacturer is looking to establish itself in Europe, Asia happens to be its focus right now.
“I’m personally targeting the European market,” Winter told us. “Having been working for the tyre industry for many years, I’m just spreading out the network to get Kokusai well known in the continent by talking to the right people and getting the right enquiries. On top of that, I’m talking about the very interesting future projects for the new labelling topics, new testing devices, testing concepts and more.”
On these lines, Kokusai hasn’t been left behind in terms of aftersales services either. With all of its local offices and manufacturing plants proving to be a great strength, the company has engineers and a team for setting up its machines and servicing them.
“We’re actually building this up for Europe with our partner; we have gone for an established partner, as we would not be building up a complete company with all the service structures and everything else from scratch,” Winter explained.
Investment in technology
Kokusai certainly has big plans for Europe. But at the same time, as mentioned by Winter earlier, the basic technology is developed in Japan. And that is the heart of the company’s engineering. In fact, Winter claims that he is very happy that Kokusai started investigating on its technology over the years.
“Kokusai has invested so much money in its own engineering over the last years that it has its own testing centre just to make the application development. In truth, we are the only company within the tyre testing equipment manufacturers to do so,” Winter shared. “Additionally, we have a new 1,200-square metre testing facility in the Greater Tokyo Area; we are inviting customers to bring their tyres and parts, and we are developing the applications with them. I think this is very unique around the world.”
Furthermore, Winter cited that during the period of the pandemic, the company made Teams presentations with video systems and presented the equipment in China and Japan, along with doing conferences. “Our customers were so happy that we were even able to show them this kind of equipment and make tests on their tyres just through web meetings.”
Also, Kokusai provides new testing concepts, where some of the systems are still being developed. However, the test and measurement solutions manufacturer already offers to start making all the tests with tyre companies’ tyres and develop their customised application.
The need for indoor testing
While Kokusai’s plants and offices across the world stay linked in order to keep up with regulations and be on the same page in general as a group, there are no standards at the moment for the very technical specification of the equipment themselves.
“The European Union is just developing the standards for wear testing. And they are, in fact, developing the standards for outdoor driving,” Winter explicated. “However, we will need indoor testing in the future. The tyre engineers will especially need it because they will want to have the results in a couple of days and not months. Therefore, there is a need for the development area and the future regulations to also focus on indoor drum testing.”
One leap at a time
Kokusai is clearly spreading its wings gradually, not just by expanding geographically but even by enhancing itself by really investing in engineering and development. It is one of the few major players in testing equipment and invests tremendously in further building up itself.
Michelin Launches CrossClimate 3 Sport Performance Tyre
- By TT News
- July 08, 2025
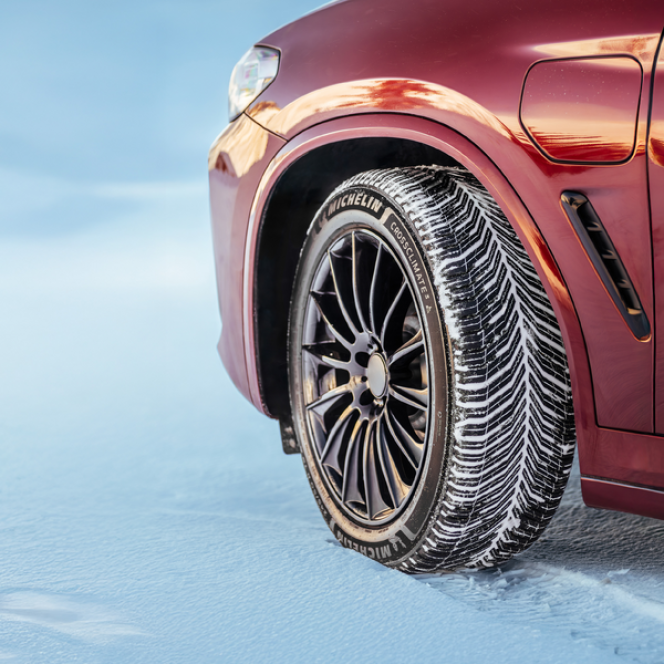
A decade after pioneering the first winter-approved summer tyre, Michelin pushes boundaries again with its groundbreaking MICHELIN CrossClimate 3 Sport. Designed specifically for high-performance sports cars, this innovative tyre merges the dynamic handling of summer sport tyres with certified winter capability – a first for the market.
Engineered for powerful gas and electric vehicles, the CrossClimate 3 Sport delivers year-round confidence with exceptional wet grip (rated ‘A’ on the EU label) and durability. Its advanced materials and motorsport-derived technologies achieve what was once deemed impossible: combining summer tyre responsiveness with Three Peak Mountain Snowflake (3PMSF) winter certification.
Available since 1 July in 29 sizes (205/40R18 to 315/35R20), with 30 additional variants coming in 2026, the tyre has already secured its first OEM partnership. The new Alpine A390 will feature a custom A39-marked version, optimised for the model’s sporty agility in 245/45 R20 sizing. Alpine selected the CrossClimate 3 Sport from three contenders, valuing its all-season precision and winter-ready 3PMSF performance.
Industry recognition followed swiftly, with Michelin winning the 2025 ‘Ze Award for Technological Innovation’ on 3 July. Judged by automotive experts and journalists, the accolade underscores Michelin’s leadership in the booming all-season segment, now representing 37 percent of the market. By redefining performance boundaries, the CrossClimate 3 Sport reaffirms Michelin’s commitment to innovation that meets evolving driver needs.
Serge Lafon Director of the Original Equipment Business Line, said, “When designing this tyre for Alpine, we paid close attention to the vehicle’s specific characteristics. Developed for the largest and most powerful Alpine ever built, this tyre combines winter performance, energy efficiency, optimal grip and sporty responsiveness. It delivers consistent performance, so drivers can count on the tyre throughout its lifespan. Alpine is the first auto manufacturer to select the brand-new MICHELIN CrossClimate 3 Sport. We are confident that this tyre meets the vehicle's demands and the expectations of consumers seeking long-term safety, simplicity and sportiness. We’re very proud of Alpine’s trust in us.”
Dominique Stempfel President of the French Tyre Manufacturers Association (Syndicat du Pneu), said, “The jury chose to honour the MICHELIN CrossClimate 3 Sport for pioneering a new segment: an all-season tyre designed specifically for sports car drivers seeking the year-round advantages of an all-season tyre without compromising on performance or safety.”
- Continental
- Continental Tyres
- Continental UltraContact NXT
- KS Energy and Environment Award
- Sustainability
- Sustainability Awards
Continental Wins KS Energy And Environment Award 2025 For UltraContact NXT Tyre
- By TT News
- July 08, 2025
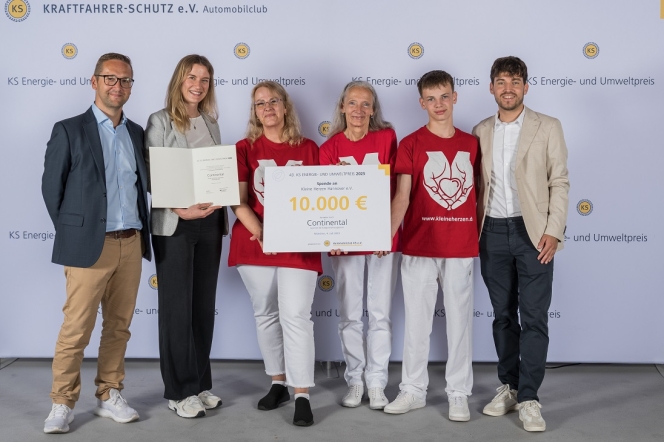
Continental has received the 43rd KS Energy and Environment Award in the vehicle technology category from Germany's Automobilclub KS e.V., recognising its leadership in sustainable mobility. The honour highlights Continental's UltraContact NXT, its most eco-friendly series tyre to date, which contains up to 65 percent renewable, recycled and ISCC PLUS-certified materials.
As part of the award, Automobilclub KS e.V. is donating EUR 10,000 to Kleine Herzen Hanover, a charity supporting paediatric heart care at Hanover Medical School since 2006. The funds will aid therapies and facility improvements for young patients.
The UltraContact NXT combines sustainability with performance: up to 32 percent renewable content, five percent recycled materials and 28 percent ISCC PLUS-certified bio-based and circular-sourced components. All available sizes achieve the EU tyre label's top 'A' rating for efficiency, wet grip and noise reduction.
Established in 1981, the KS Energy and Environment Award has long promoted emissions-reducing innovations in transport. Under the patronage of Germany's Federal Ministry for Economic Affairs and Climate Protection since 2022, the award underscores Continental's alignment with national sustainability goals through cutting-edge tyre technology.
Kristina Kumme, Continental Tires' Strategic Program Manager, EMEA, said, "With the UltraContact NXT, we have taken a significant step forward by combining maximum sustainability with excellent performance. We are pleased that the KS Energy and Environment Award jury recognised this innovative development, and we are honoured to support a significant charitable organisation with a EUR-10,000 donation through this award.”
Prof Dr-Ing. Dieter Anselm, a member of the expert jury, said, "For us, this volume tire is clear proof that Continental is working hard to promote innovative technologies and sustainable solutions throughout the entire value chain. Given that every car, regardless of its drive type, needs tyres today and will continue to need them in the future, this innovation has a significant impact.”
Bridgestone Announces Strategic Sale Of Carbon Black Business To Strengthen Core Operations
- By TT News
- July 08, 2025
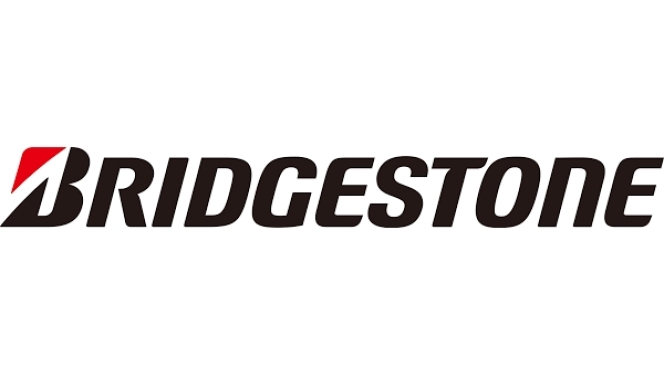
Bridgestone Corporation has reached an agreement to sell its subsidiary, Bridgestone Carbon Black (Thailand) Co., Ltd. (BSCB), to Tokai Carbon Co., Ltd. and Thai Tokai Carbon Product Co., Ltd. This divestment aligns with Bridgestone’s strategy to enhance its global business resilience by adapting to market changes and focusing on high-value segments.
As part of its Mid-Term Business Plan (2024–2026), Bridgestone is optimising its operations to strengthen growth and competitiveness. The company is prioritising its premium tyre business, aiming to boost productivity and innovation across the entire value chain – from materials development to logistics and sales – with a focus on its Dan-Totsu (best-in-class) products. The sale of BSCB supports this strategy by allowing Bridgestone to collaborate with specialised partners like Tokai Carbon, which possesses deep expertise in carbon black production and supply chain management.
Beyond securing a stable carbon black supply, Bridgestone and Tokai Carbon are jointly exploring sustainable solutions, including producing carbon black from recycled tyres. This partnership will enhance Bridgestone’s long-term competitiveness while advancing its sustainability goals. However, the company will retain in-house carbon black production for strategic applications, such as premium and motorsport tyres, through its Japanese subsidiary, Asahi Carbon Co., Ltd. This ensures control over critical technologies that align with its core business and sustainability initiatives.
The transaction, part of Bridgestone’s second-stage business restructuring, is expected to have minimal impact on its current fiscal year financial performance. The company remains committed to sustainable growth, balancing strategic in-house capabilities with collaborative ventures to maintain its leadership in the tyre industry.
Goodyear India Uncovers INR 39 Mln Tyre Theft at Ballabgarh Plant
- By Sharad Matade
- July 07, 2025
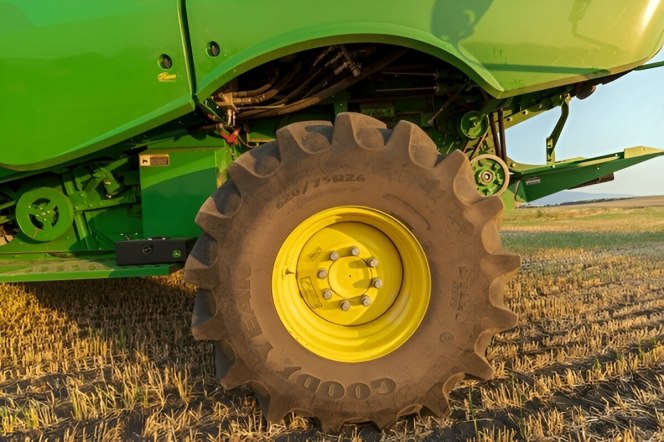
Investigation reveals coordinated theft by contractors and employees through bulk pilferage and excess loading schemes
Goodyear India Limited disclosed that a comprehensive investigation by Ernst & Young uncovered a sophisticated theft operation at its Ballabgarh manufacturing plant, resulting in the loss of 4,571 tyres valued at approximately INR 39.11 million.
The tyre manufacturer’s board reviewed the investigative findings during a meeting that concluded last week, revealing what the company described as “potential theft of tyres in bulk by contractual workers involved in security, warehousing and loading operations, acting in collusion.”
Dual Theft Operations Exposed
The Ernst & Young investigation, spanning October 2023 to November 2024, identified two primary theft methods that enabled the systematic pilferage of farm tyres from the Faridabad-based facility.
Bulk Theft Scheme: The more significant operation involved truckloads of tyres being removed from the plant through coordination between third-party loading supervisors, warehouse workers, security guards, and external accomplices. Electronic communications reviewed by investigators revealed references to 4,057 tyres across 20 dates between July and December 2024, with detailed SKU counts discussed among the conspirators.
Security records were deliberately manipulated to conceal the theft, with one security contractor admitting to accepting kickbacks from a loading supervisor to avoid recording truck details carrying stolen merchandise.
Excess Loading Operation: A secondary scheme involved loading additional tyres beyond invoiced quantities onto legitimate shipments, with the excess stolen during transit. The investigation revealed a significant increase in overweight dispatches during the July-November 2024 period, with 50 per cent of overweight trucks dispatched during this timeframe, compared to historical patterns.
Quality assurance protocols were compromised, with one employee admitting to receiving instructions from a third-party warehouse vendor to disregard overweight trucks and dispatch them without conducting mandatory quality studies. The employee estimated that 5-6 excess tyres were loaded per truck in select shipments to Goodyear warehouses.
Quality Control Manipulation
The investigation also uncovered systematic inflation of tyre rejection quantities during pre-dispatch inspections. A quality assurance employee acknowledged receiving kickbacks to artificially inflate rejected tyre counts in daily reports, despite no physical rejections having occurred, allegedly to help manage inventory shortfalls maintained by the third-party warehouse vendor.
Data analysis revealed an increase in rejection rates in 2024 compared to 2023, with the manipulation involving collusion between employees and third-party quality inspectors.
Operational Control Gaps
Beyond the theft schemes, Ernst & Young identified significant weaknesses in Goodyear’s inventory management and production processes. The manual production handover system lacked proper verification, with multiple employees admitting that the defined processes weren’t followed.
Production records maintained manually revealed discrepancies, with multiple spreadsheets containing different production numbers for the same periods. The investigation found that production during shutdown periods wasn’t recorded in the Production Management Information System, creating variances that couldn’t be validated due to unreliable manual records.
Financial Impact and Response
The financial impact of the inventory shortage identified in November 2024 was already recognised in Goodyear India’s financial statements for the quarter ended 31 December 2024. “The management has taken cognisance of the findings and initiated appropriate legal and disciplinary actions against those involved,” the company stated in its regulatory filing. “Proactive measures, including a site security assessment and tightened controls, have been implemented.”
Investigation Methodology
Ernst & Young’s fact-finding review employed comprehensive investigative techniques, including data analytics, transaction testing, background checks on suspected third parties, forensic imaging of electronic devices, and interviews with employees and contractual workers.
The investigation covered electronically stored information from the laptops and server backups of suspected individuals, utilising keyword-based searches to identify suspicious communications that proved crucial in establishing the theft patterns.
Regulatory Compliance
The disclosure fulfils Goodyear India’s obligations under Regulation 30 of the Securities and Exchange Board of India’s Listing Obligations and Disclosure Requirements Regulations, 2015. The company initially informed stock exchanges of the inventory variance on 12 February 2025.
“The Company remains committed to upholding the highest standards of corporate governance and safeguarding stakeholder interests,” Goodyear India stated in its filing.
Comments (0)
ADD COMMENT