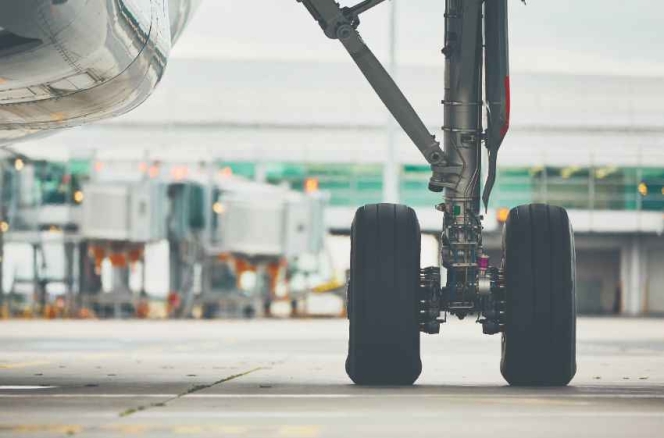
Some airlines may pay for their tyres by the retreads. There is an initial payment for the virgin tyre, and then a subsequent payment for the initial retread and further payments until the tyre account is settled. If the tyre fails prior to the final payment being made, then the tyre manufacturer wears the cost.
The secret (not so secret really!) to a successful retread programme is the pressure maintenance regime. If the appropriate pressures are applied to the tyre during its initial life, then we are able to deliver a sound virgin casing/carcass to the retreading plant.
In speaking with so many retreading facilities, they all detail a high rejection rate of casings submitted for retreading. The primary reason for rejection is the breakdown of the tyre’s structure as a result of under inflation.
So how does this affect the use of resources and subsequent emissions?
I have sighted figures purported to have been produced by the global accounting firm Ernst & Young (now EY), which detail a 70 percent reduction in natural resource extraction, 19 percent reduction in water consumption (potable water is one of the next global issues to deal with) and 21 percent reduction in air pollution. A truck tyre casing (say 11R22.5) that is retreaded will reduce oil consumption by about 50 litres – obviously more for a larger tyre.
Many tyre OEMs do promote the retreadability of their casings; it is just plain economic sense when you stop to think about it. Acquiring a product where you use 30 percent (by weight) only to then throw the rest onto the scrap pile is economic stupidity, but that is what seems to happen in most road transport organisations.
Maintaining tyre inflation pressures is too difficult, they say. Well, yes, if you are stuck in the 1950s where the only way to check inflation pressure was to use a manual gauge. In the 2000s, we started using tyre pressure monitoring systems (TPMS) to gain real time information about tyres in operation. Now we can stream data and identify issues such as binding brakes, wheel ends in failure mode as well as inappropriately inflated tyres. We’ve tuned operating tyres so that tyres operate in unison or as a team across an axle and so over the entire vehicle. Not being able to view tyre pressures in real time is so last century.
By tuning the inflation pressure of a tyre, the structural integrity can be assured so that when the tread worn tyre is presented at the retreading facility, it is accepted rather than rejected. Thus, a serious saving in resource use is generated; there is a substantial reduction in emissions as well as reduction in land use both from the initial growing of the natural rubber to the reduction of land fill.
A simple act can generate substantial savings. Why do so many educated people ignore this aspect? Why do bean counters not consider tyres in a holistic manner?
Purchasing a ’cheap’ tyre may appear to ‘save money’, but more often than not, the cost of operations actually rises. HOW? I hear the abacus jockeys cry! A low-cost tyre more often than not has a higher rolling resistance than a quality casing. Research and development costs, low cost operators that have copied or cloned don’t bear these costs. Consider the fuel burn over the life of a tyre, say 150,000 km. A two percent saving on the fuel burn equates to how much? When we consider the actual life of the low-cost tyre, more than likely it requires more maintenance, so there is more downtime, added rotations to gain the maximum wear from the tread package and then there is the disposal fee on the spent casing as it cannot be retreaded.
Considering tyres in a holistic manner is not something bean counters consider or actually even know about. Tyres directly influence the fuel burn of a vehicle, the wheel end life and the suspension life, even affecting the driver’s fatigue levels – not to consider the environmental aspects such as emissions and disposal.
So if an aircraft can take off and land safely on retreaded tyres, then why can’t on-road transport trucks use retreaded casings? It comes back to the neglect shown to the tyre during the initial life. It seems that people just don’t care; they don’t understand the criticality of appropriate tyre inflation pressures.
Within the Performance Based Standards for high performance trucks operating on Australian roads (think triple trailers running quad axles), there is a statement that succinctly details what a tyre contributes, to wit ;
“All the forces needed to both support and guide a vehicle ultimately arise in the area of contact between the tyre and the roadway. These forces are generated at the road surface in response to the deformation of the tyre structure.”
As tyre deformation is the product of inflation levels, there is a direct relationship between tyre inflation levels and vehicle safety. Why do people choose to ignore tyre inflation when it is so easy to monitor and comes with so many positive benefits?
So installing a simple regime of monitoring tyres in real time tyre casings to evidence that the tyres have not experienced a low pressure event (so destroying the casing’s integrity) means they can be selected for retreading. This eliminates the main excuse for not retreading, i.e. the rejection rate is too high. It is that simple!
A cheap tyre is not necessarily an economic positive. A well-maintained quality tyre will generate savings upon savings and then will also be able to do it all over again after retreading.
Many governments mandate the use of retreaded tyres on utility vehicles as it is well understood there is not only an economic benefit but an environmental benefit too!
If we, the global community, continue to consume resources without considering a reduction in the rate of consumption, then we’re doomed to exhaustion. Using a resource (read tyre) at only 30 percent and then disposing it of does not make any sense (nor cents!). Retreading of tyres is a sound practice based upon sound science. Why are so many businesses throwing their hard earned cash away because the abacus jockeys don’t know and don’t care about tyres?
Success does not reward a lack of effort. How much effort are your bean counters making in respect of tyres ?
Finnish Olympic Champion Sami Jauhojärvi Is Radar Tyres’ Official Brand Ambassador
- By TT News
- July 12, 2025
Radar Tyres, the flagship brand of Omni United, has appointed Sami Jauhojärvi, Olympic gold medallist and one of Finland’s most celebrated cross-country skiers, as its official brand ambassador.
Jauhojärvi's sporting excellence – built on resilience, performance and a profound connection with nature – mirrors Radar Tyres' commitment to delivering premium-quality tyres across all seasons and terrains at accessible prices. The brand's comprehensive range includes Summer, All Season, Winter and specialist Ice tyres, designed to meet diverse driving needs with reliable performance.
This collaboration represents a strategic alignment as Radar Tyres expands its European and UK presence. Jauhojärvi will serve as brand ambassador, featuring in marketing campaigns, digital initiatives and local events while sharing his expertise to support Radar Tyres' mission of making high-performance tyres available to all drivers.
G S Sareen, Founder and CEO of Omni United, said, “We’re excited to welcome Sami to the Radar family. Sami’s authenticity, credibility and strong connection with his audience make him an ideal partner for us. He embodies the spirit of perseverance and performance – the same qualities we build into every Radar tyre. As we continue to grow our brand across Europe, partnerships like this play a key role in building deeper connections with consumers. We’re excited to build on this momentum with more such collaborations in the near future.”
Jauhojärvi said, “I am thrilled to represent Radar Tyres, a brand that has a remarkable mission to make premium quality and performance accessible to all and also has deep-rooted values of giving back to society via various initiatives it has undertaken over the years such as supporting breast cancer research. I’m sincerely surprised about the performance and silence of my Radar Tyres and happy to deliver this feedback to all the people.”
- Kenda Tires
- Dan ‘The Flying Dutchman’ Vanden Heuvel
- Dan Vanden Heuvel
- The Flying Dutchman
- Off-Road Motorsports Hall of Fame
Kenda Tires Celebrates Dan Vanden Heuvel's Hall Of Fame Nomination
- By TT News
- July 12, 2025
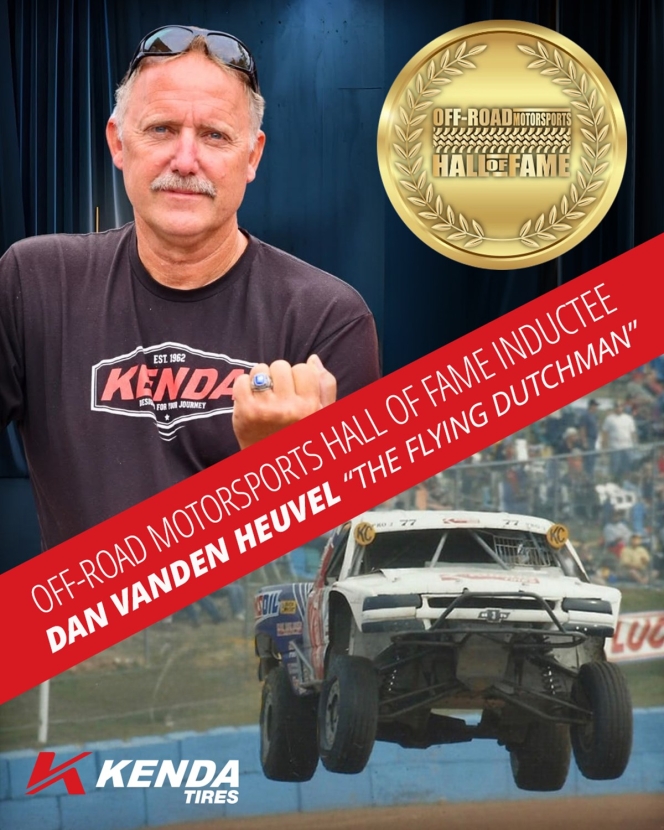
Kenda Tires is celebrating Dan ‘The Flying Dutchman’ Vanden Heuvel's nomination to the Off-Road Motorsports Hall of Fame's Class of 2025, recognising his legendary 49-year career as both a champion racer and community leader.
Since entering his first race at age 15 in 1977 at Crandon International Raceway, Vanden Heuvel has become one of off-road racing's most respected figures. His aggressive driving style earned him 20+ Pro-Class wins, five Crandon World Championships and a PRO-2 title. As owner of Flying Dutchman Racing, he mentored numerous drivers including his son Mikey, who secured Kenda Tires' historic first PRO-2 victory.
Beyond competition, Vanden Heuvel's greatest impact comes from his tireless community work. He co-founded the Midwest Off-Road Racing Association, created the Short Course Kart Series for young racers and established the MORR Injured Driver Fund with his wife Nancy. His hands-on approach – from building tracks to mentoring drivers – has shaped generations of off-road enthusiasts.
Now as Kenda Tires' Product Display Manager, Vanden Heuvel continues supporting the sport, assisting drivers across multiple series while representing Kenda at events nationwide. His dedication embodies the brand's values of community and passion for motorsports.
The formal induction ceremony will be held on 2 November 2025 in Las Vegas. This honour celebrates not just Vanden Heuvel's remarkable racing achievements but his enduring legacy as an ambassador who has profoundly influenced off-road culture.
Brandon Stotsenburg, VP of Automotive Division, Kenda Tires USA, said, “Dan is more than a legend – he is a mentor, a servant-leader and the beating heart of the off-road community. He helped deliver Kenda’s first PRO championship and still shows up for others every single weekend. We are honoured to have him represent Kenda and even more proud to call him family.”
Tire Industry Association Opens Voting For 2025–26 Board Of Directors
- By TT News
- July 11, 2025
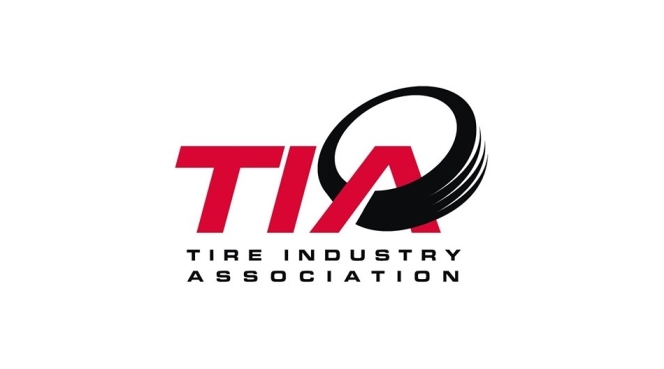
The Tire Industry Association (TIA) has officially opened voting for its 2025–2026 Board of Directors election, with five seats available – four carrying a standard three-year term and one two-year term to fill a vacancy. Nine candidates, including two current board members, are vying for these positions.
The nominees include industry leaders from across the tyre sector: Stephen Callahan of Liberty Tire Recycling (Pittsburgh, PA); Jeff Campbell from Tire Discounters Inc. (Cincinnati, OH); John Evankovich representing Sam’s Club Tire and Battery Centers (Bentonville, AR); Darrel Jackson of Big O Tires (Kernersville, NC); Michael Jacobsen from Purcell Tire Company (Potosi, MO); Al Klinge of Klinge Group (Sherwood, Australia); Brian Laughlin with Technical Rubber Company (Johnstown, OH); Seth Murphree from Travel Centers of America (Anderson, SC) and Jason Rook of Independent Tire Dealers Group (Wimberley, TX).
All TIA members in good standing are eligible to vote either by mail-in ballot or online at the association’s election portal. The voting period runs from 9 July through 1 September 2025, with election materials distributed to primary contacts at qualifying member companies.
Results will be announced in mid-September, and the newly elected directors will be formally installed during TIA’s Annual Membership Meeting on 3 November 2025, in Las Vegas, held in conjunction with the Global Tire Expo/SEMA Show. This election marks a key opportunity for members to shape the association’s leadership and strategic direction for the coming years.
Maxion Wheels Pioneers Advanced Wheel Solutions For Battery-Electric Trucks
- By TT News
- July 11, 2025
As the transportation sector accelerates its shift towards electrification, Maxion Wheels is spearheading the development of specialised wheel technologies to address the distinct requirements of battery-electric trucks. The company's deep engineering expertise and innovative approach position it as a leader in creating solutions that meet the evolving demands of electric mobility.
Electric trucks present unique technical challenges due to their substantial battery weight, which can add 2-3 tonnes compared to conventional diesel vehicles. Proposed European regulations allowing increased gross vehicle weights for zero-emission trucks further intensify the demands on wheel systems. The instant torque characteristics of electric drivetrains, often delivering 2-3 times more torque than traditional engines, combined with the stresses of regenerative braking, create unprecedented loads. These factors can increase front axle loads by up to 500 kg per wheel, necessitating stronger yet lightweight wheel designs.
Maxion addresses these challenges through material science innovation, employing micro-alloyed high-strength steels with yield strengths exceeding 550 MPa – approximately 20 percent stronger than standard wheel steels. The company's proprietary Lightweighting Process integrates advanced engineering techniques including topology optimisation algorithms that simulate natural growth patterns, finite element analysis of over 5,000 load scenarios and precision forming methods that enhance material properties.
The company's substantial investments in high-performance computing have revolutionised its development capabilities. These powerful systems enable evaluation of more than 15,000 design iterations during development cycles, sophisticated multi-physics simulations combining mechanical, thermal and fatigue analysis and digital twin validation that has reduced physical prototyping requirements by 40 percent.
Current production solutions include certified 22.5-inch steel wheels with exceptional 4,250 kg load capacity, weight-optimised designs saving approximately 50 kg per axle compared to conventional wheels, and customized variants tailored to different battery configurations. Looking ahead, with market analysts projecting electric trucks will capture 25 percent of the commercial vehicle market by 2030, Maxion is actively developing next-generation solutions including aluminium hybrid wheels for premium applications, advanced composite materials for lightweight designs and enhanced testing protocols for extreme fast-charging thermal conditions.
Ralf Duning, Vice President of Global Engineering at Maxion Wheels, said, “At Maxion Wheels, we are committed to leading the charge in e-mobility by developing lightweight wheel solutions that meet the unique demands of battery-electric trucks. Our latest designs not only enhance payload capacity but also ensure that our customers can transition to sustainable transport without compromising on performance or durability.”
Comments (0)
ADD COMMENT