SMART Sensors in tyres or on rims
- By Alan Bennetts
- December 23, 2020
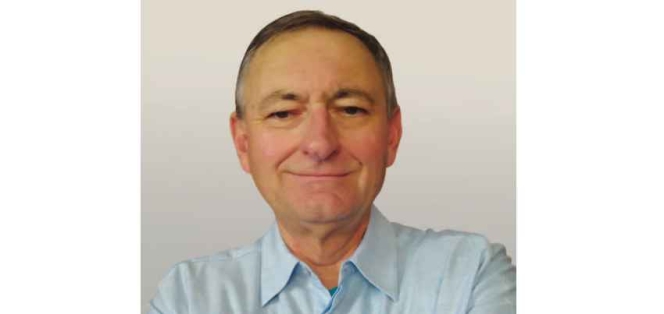
Since the 1970’s the Anti-Lock Braking system, now almost ubiquitous, has been helping drivers retain control during heavy braking on wet or slippery roads. The wheel rotation sensors, at the heart of ABS, have been co-opted into traction and stability control systems. Drivers do not consciously rely on these systems to save them from a mistake but seasoned drivers (code of older people) will have noticed that they appear to be much better drivers now than when they were in their 20’s. Which is surprising as reaction times increase with age.
What has been happening over the last thirty years is that vehicle safety systems have become more intelligent and tyres have more grip resulting in minor driver errors being recoverable by a combination of driver input, ABS, ESC and ATC. This list of potentially lifesaving innovations will soon include ‘look-ahead systems’ preventing us from tailgating the car in front or straying out of our motorway lane. None of these worthwhile advances has relied upon sensors embedded in the tyre because such sensors were not needed. Will embedded tyre sensors be capable of delivering worthwhile improvements to safety and/or vehicle dynamics without causing service and support problems for vehicle owners.
Quiet tyres
To develop tyres that run more quietly, with better grip and with lower rolling resistance knowledge of what is happening to the tyre as inputs change is vitally important. There will always be a need for tyre sensors that can provide real operating data that supports the predictions made by the analytic tyre models that are increasingly at the centre of our tyre development. Bay Systems responded to this need in 2006 by developing the Tyre Cavity Microphone (TCM) and other measurement modules that are used to study the behaviour of tyres in the laboratory and more importantly on the road, the environment where they are used. When comparing laboratory and road measurement it was clear that road data contains random variations not seen in the laboratory, see figures 1a & b.
The sound pressure level (SPL) inside a tyre is usually dominated by cavity resonance modes, the primary mode being strongest. The rms level of the noise inside the tyre’s cavity, at any given speed, responds to the texture of the road surface, the coarser the texture the higher the rms level. With a little signal processing the signal from the TCM’s microphone can be processed to give an indication of the road surface condition as can the signal from the TCA’s accelerometer mounted or embedded in the tyre liner, see figures 2 a & b.
The microphone positioned on the rim and integrated into the TPMS housing is potentially in a much safer location than a sensor buried in the tyre’s structure. Tyre fitters are used to remove and install TPMS modules making maintenance easier and more affordable than repairing sensors buried in a tyre’s structure. Inevitably sensors and systems will fail and any sensor mounted in the tyre is destined to have a stressful life. Tyre liner temperatures can exceed 120 degrees C depending on; speed, ambient temperatures and tyre type. Elevated temperatures (>50 degrees C) degrade batteries and semi-conductors. Most semi-conductors fail or suffer dramatically shorter service lives if their ambient temperature regularly reaches 80-100-degree C.
For many drivers the prospect of warning lights burning on their dashboards due to tyre mounted transducers failing will be very unwelcome, particularly if the recommended cure is to buy a new tyre. If the only way to pass the annual vehicle inspection, common in many countries, is for the tyre safety system to be working or not fitted then the not fitted option will be preferred by most buyers of used vehicles. If SMART wheel sensors can be shown to deliver genuine benefits then integrating them into a rim mounted package might be the lowest risk approach, at least from the customer’s perception.
Universal TMS
A Universal Tyre Monitoring System (UTMS) package would therefore appear to be the most attractive option in terms of convenience and minimising the costs associated with maintenance and repair. Essentially the Bay Systems’ TCM system is a UTMS system, albeit for R&D use only. The key question is therefore; ‘Can the data from UTMS be usefully employed to enhance vehicle utility, handling and safety?’ This is a difficult question to answer, for handling and safety, as for these applications the chassis management system (CMS) computer must receive and process signals in real time for the information to be usefully employed. Being informed that road surface icing has occurred some 30 metres after the vehicle has transitioned onto ice is liable to be too late. The signal from a tread liner accelerometer, see figures 3a. shows the transition from wet to flooded road, N.B. the vehicle was not aquaplaning but a slight increase in speed might well have invoked it. This raw time history would need to be processed before it could be used to trigger an intervention, in figure 3b a wavelet transform is used to highlight the differences between wet and flooded road surfaces. Real time responses imply high data rates from sensors, which in turn result in higher power consumption. Getting power to and signals back from the two front wheel sensors, rear wheel road surface information is typically front wheel data delayed by 3 metres, or from all wheels will be a challenge. Vehicles may be parked for days and even weeks, UTMS must shut down completely to conserve battery life. This may be achieved using a motion switch, these are readily available but as always adding complexity increases the risk of failures. The bigger problem is how to maintain and recharge the battery during normal usage. Any form of physical coupling through a connector will certainly be damaged or fail through water ingress making some type of induction coupled charging a more attractive option.
Low power radio transmission has worked well for TCM. However, such a system across the entire vehicle fleet may present problems on densely trafficked roads. On a busy motorway a vehicle might pass within 2 metres of another vehicle at a rate of 10 per second. Should all of these vehicles be using the UTMS radio spectrum then there will be up to 40 channel contentions per second to resolve. It is unlikely that radio spectrum will be made available that allows space for more than 100 channels. Each vehicle’s UTMS radio system must be primed to channel hop to avoid contentions from up to 10 interfering vehicles per second while sustaining a minimum data rate of 100kbytes per second.
Such a work load imposed be an ever-changing mix of vehicles will be difficult to manage without gaps in the data. A possible solution exists if the transmitted power from UTMS is very low, to the point that signals are only detectable inside the transmitting vehicle’s own wheel arch. Very low power radio transmission also brings low power drain at the transmitter making power supply easier. However, it also implies that a high receiver sensitivity might be needed. The extremely weak signals from nearby vehicles may therefore become detectable which returns us to the problem of radio channel contentions. Setting a low transmission power limit is therefore likely to be an area of diminishing returns and the channel contention issue is likely to always exist for high data rates.
To calculate the instantaneous rolling resistance of each wheel the CMS will require only two measurements; the temperature of the tyre and its pressure. A once per second reading rate for these two parameters would be enough, due to the tyre’s relatively high thermal inertia and
the normally slow rate of change of inflation pressure. The liner temperature measurement might be over a single area or across a section of the tyre. In the case of our TCT system (aimed at tyre R&D) the measurement is over 64 pixels and can stretch from bead to bead or be focused on an area if interest e.g. the tyre’s shoulder with an accuracy of 0.1 degrees C and resolution of 0.01 degrees C. A measurement cycle, even at high resolution would require a data packet of less than 200 bytes which with overhead might be 1kbytes. This rate would fit into the radio channels even on a busy motorway making dynamic estimation of rolling resistance possible while real time road surface measurement would be problematic.
Rolling resistance can account for up to 30% of battery energy in an EV making the choice of tire and the way the vehicle is driven very important; potentially being the difference between driving and walking the last few miles home on a cold wet night! There will be, for any journey, an optimum vehicle speed and route where energy consumption will be minimized. The probability of reaching the destination will be increased if this route is followed but it is more important to alert the driver if there is a significant probability of not reaching the destination on the remaining battery charge.
EVs with batteries that are over three years old may have battery capacities of 80% or less of the new capacity. This makes a planned journey of just 100miles (160km) problematic, particularly when air conditioning, heater and windscreen wipers are all operating. This range deficit may increase with traffic conditions such as road works, detours, accidents etc. To increase driver confidence a fully integrated vehicle management and GPS route planning system would need to use environmental data such as ambient temperature, wind speed and direction together with vehicle data such as load and UTMS derived tyre liner temperature and pressure to calculate the projected energy consumption for any proposed route. For this total tyre energy budget to be calculated for the journey the full tyre specification will be needed for each tyre i.e. the rolling efficiency for all temperatures, inflation pressures, loads and temperatures. The GPS navigation system, using these parameters and taking into account traffic updates would then evaluate the probability of reaching the destination without a battery recharge. If the journey was beyond the battery range an alternative route would be suggested that would pass a recharging station.
Data accuracy
The key to all this working reliably will be the accuracy of the tyre specification data entered into the CMS. What will be needed will be the full energy dissipation profile for all conditions, not just the laboratory performance rating, though this would be better than nothing. Tyres are currently rated for energy dissipation (rolling resistance) when operating in a laboratory at 25 +/- 4 degrees C while running on a smooth steel road wheel. The tyre is run for 30 minutes at 80kph before the test, is correctly inflated and is carrying 80% of its maximum load. Our measurements have revealed that the liner temperature across similar tyres from different manufacturers can vary from 50 to 90 degrees C for this test.
Energy dissipation drives the liner temperature higher until thermal equilibrium is reached. On the road, in the real world, the maximum temperature measured on the liner of a Mazda BT50 pickup truck tyre was 45 degrees C when pulling a trailer at a steady 100kph for 6 hours with an air ambient temperature of 22 degrees C. i.e. much lower than would have been expected. Energy efficiency improves with increasing temperature at the rate of 0.6% per degree C, over the temperature range 15-50 degrees C. It is highly likely that most tyres operating in temperate regions are not delivering their labeled energy efficiencies because they are running cool. This applies even in the summer when ambient temperatures are near those specified for the laboratory. In the winter the Mazda truck tyre did not reach 30 degrees C. i.e. half of the lab test result and probably 2 full tyre grades worse performance than the label states, possibly resulting in a 5+ mile shortfall in vehicle range.
While the case for in tyre sensors and even rim-based sensor fitment to vehicles is open to debate the case for their use in R&D is now well proven and accepted. Tyre internal noise and tyre cavity resonance is easily and reliably measured with good accuracy, both on a laboratory road wheel and on the highway. The differences between tyres from different manufacturers can be quickly evaluated, see figures 4 a & 4b, allowing car makers to choose a tyre best suited to their vehicle and the road surfaces it is most likely to be driven over. For the tyre companies their new product development can be steered towards lower levels of noise and cavity resonant modes.
The primary cavity resonance mode if heard in the vehicle cabin is annoying and is often interpreted by the owner as a defect. For auto makers noise complaints are a concern as investigation in the field is costly and if unresolved becomes a barrier to a repeat sale. Tyre companies are encouraged by auto makers to reduce cavity resonant mode levels and reduce road noise. The loss of vehicle control is a much more serious matter and has always been at the top of the priority list for tyre and auto companies. The measurement of tyre liner acceleration provides a great deal of information including early warning that the threshold for aquaplaning is imminent, see figure 3a.
Reductions in pre and post contact patch waves, see them clearly in figure 5, that propagate around the tyre will lead to reductions in radiated noise and lower pass-by noise levels. No improvement in a tyre’s characteristic comes free of charge and this cost is often a trade off with other equally desirable characteristics. Typically, less grip and faster wear rates are what result when a tyre’s energy dissipation is improved. Wet grip performance is featured on the tyre label and who would deliberately choose a tyre with lower wet grip. Leaving the most likely trade off candidate as wear and of course faster wear means more particulates shed into the environment which is undesirable. It seems likely that wear rate will soon appear on the tyre label. There seem to be no unalloyed successes, only the least worst choices to be made!
Smithers Earns ISO 17025 Accreditation For Texas Proving Ground
- By TT News
- July 13, 2025
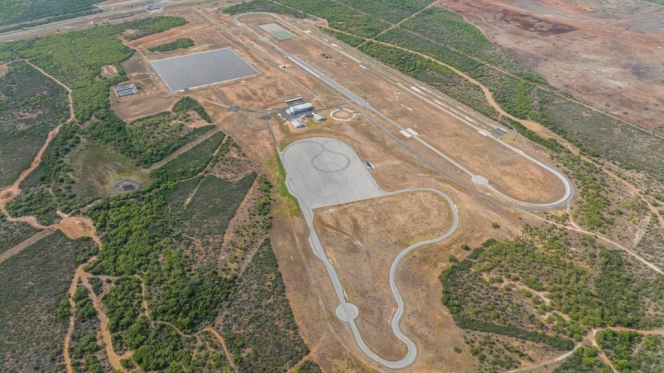
Smithers, a renowned provider of testing, consulting, information and compliance services, has announced that its proving ground at Treadwell Research Park in Pearsall, Texas, has achieved ISO 17025 accreditation.
Operated on behalf of Discount Tyre, the facility’s accredited scope currently covers wet grip testing and tyre buffing, with plans to expand accreditation to include rolling resistance and pass-by-noise testing. The site boasts diverse paved and off-road test surfaces for comprehensive tyre performance validation. Additionally, it complies with UNECE Regulation No. 117 for Wet Grip and Pass-by Noise standards. This accreditation underscores Smithers' commitment to delivering high-quality testing services in the tyre industry.
Sean Connolly, Director of Test Track Operations at Smithers Winter Test Centre/Pearsall Test Track, said, “The tyre industry is currently focused on a variety of sustainability initiatives, such as reducing the rate of tread wear to extend the life of the tyre. Understanding tyre performance at varying levels of tread wear is critical for tyre manufacturers looking to get the most out of their designs.”
Jim Popio, PhD, Vice President, Smithers Materials Science and Engineering Division, North America, said, “We’re incredibly proud that our existing processes and procedures meet the rigorous requirements of ISO 17025 accreditation. Accurate data, on time, is central of the Smithers promise on a global scale, and we strive to go above and beyond our clients’ expectations with exceptional service as well.”
Michelin Launches Maiden Experience Store In Nashik, It’s Biggest Facility In India
- By TT News
- July 12, 2025
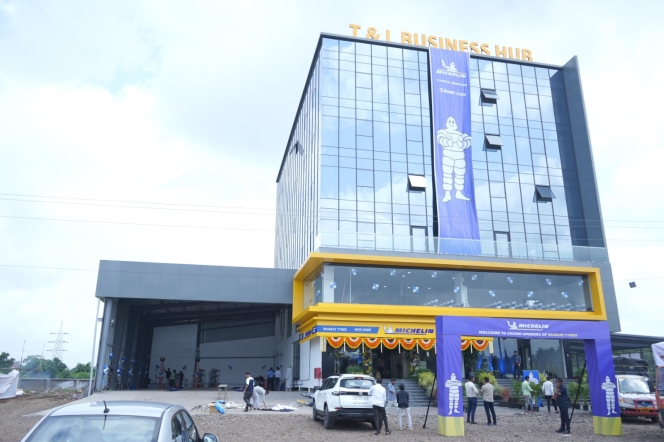
Michelin, a leading tyre technology company, has launched its first Michelin Experience Store in India, in partnership with Bharat Tyres. The facility spread across 25,000 sqft is located in Adgaon on the Mumbai-Agra highway, Nashik and is Michelin’s largest store in the country.
It is designed not only to provide a premium experience, but also showcases the company’s global legacy through the Michelin Wall. Customers will also be to experience the Heritage Wall that visualise the heritage of both Michelin and its local dealership partner.
The Michelin Experience Store also has a Display Zone that showcases Michelin’s innovations in electric mobility, materials science and environmental responsibility.
The dealership also includes service areas for cars and trucks, PPF coating, precision wheel alignment, advanced balancing services, innovative puncture repair solutions, professional car detailing and a wide array of car accessories.
Shantanu Deshpande, Managing Director, Michelin India, said, “We are proud to unveil Michelin’s first Experience Centre in India. The sole purpose of this store is to go beyond traditional tyre retail and provide customers an immersive experience of the brand, of our dealer partners and of the technological prowess of our tyre solutions that are safe and sustainable. Nashik, a key hub with growing premium vehicle ownership, is the first of many such centres that will further strengthen our footprint in the western region while providing state-of-the-art experience and services to evolving customers.”
Finnish Olympic Champion Sami Jauhojärvi Is Radar Tyres’ Official Brand Ambassador
- By TT News
- July 12, 2025
Radar Tyres, the flagship brand of Omni United, has appointed Sami Jauhojärvi, Olympic gold medallist and one of Finland’s most celebrated cross-country skiers, as its official brand ambassador.
Jauhojärvi's sporting excellence – built on resilience, performance and a profound connection with nature – mirrors Radar Tyres' commitment to delivering premium-quality tyres across all seasons and terrains at accessible prices. The brand's comprehensive range includes Summer, All Season, Winter and specialist Ice tyres, designed to meet diverse driving needs with reliable performance.
This collaboration represents a strategic alignment as Radar Tyres expands its European and UK presence. Jauhojärvi will serve as brand ambassador, featuring in marketing campaigns, digital initiatives and local events while sharing his expertise to support Radar Tyres' mission of making high-performance tyres available to all drivers.
G S Sareen, Founder and CEO of Omni United, said, “We’re excited to welcome Sami to the Radar family. Sami’s authenticity, credibility and strong connection with his audience make him an ideal partner for us. He embodies the spirit of perseverance and performance – the same qualities we build into every Radar tyre. As we continue to grow our brand across Europe, partnerships like this play a key role in building deeper connections with consumers. We’re excited to build on this momentum with more such collaborations in the near future.”
Jauhojärvi said, “I am thrilled to represent Radar Tyres, a brand that has a remarkable mission to make premium quality and performance accessible to all and also has deep-rooted values of giving back to society via various initiatives it has undertaken over the years such as supporting breast cancer research. I’m sincerely surprised about the performance and silence of my Radar Tyres and happy to deliver this feedback to all the people.”
- Kenda Tires
- Dan ‘The Flying Dutchman’ Vanden Heuvel
- Dan Vanden Heuvel
- The Flying Dutchman
- Off-Road Motorsports Hall of Fame
Kenda Tires Celebrates Dan Vanden Heuvel's Hall Of Fame Nomination
- By TT News
- July 12, 2025
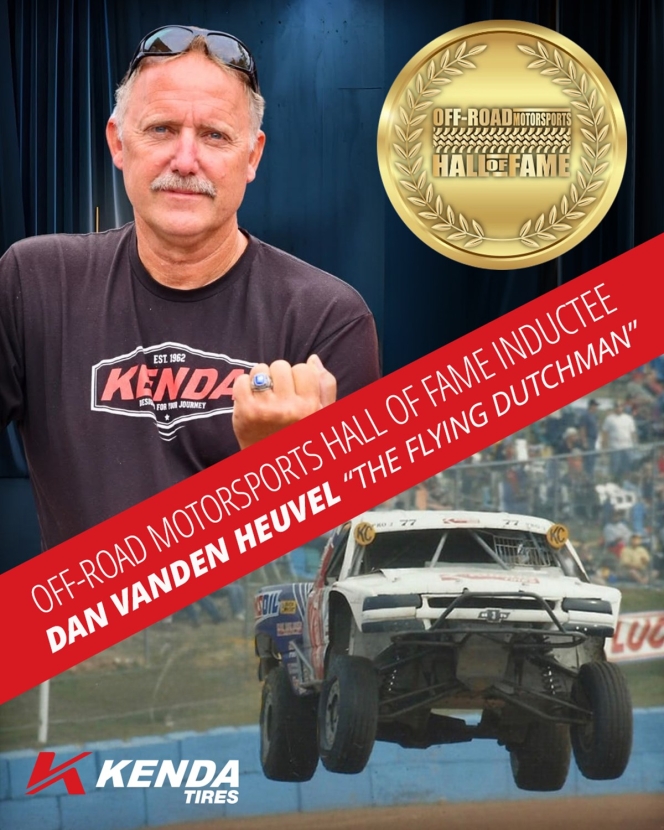
Kenda Tires is celebrating Dan ‘The Flying Dutchman’ Vanden Heuvel's nomination to the Off-Road Motorsports Hall of Fame's Class of 2025, recognising his legendary 49-year career as both a champion racer and community leader.
Since entering his first race at age 15 in 1977 at Crandon International Raceway, Vanden Heuvel has become one of off-road racing's most respected figures. His aggressive driving style earned him 20+ Pro-Class wins, five Crandon World Championships and a PRO-2 title. As owner of Flying Dutchman Racing, he mentored numerous drivers including his son Mikey, who secured Kenda Tires' historic first PRO-2 victory.
Beyond competition, Vanden Heuvel's greatest impact comes from his tireless community work. He co-founded the Midwest Off-Road Racing Association, created the Short Course Kart Series for young racers and established the MORR Injured Driver Fund with his wife Nancy. His hands-on approach – from building tracks to mentoring drivers – has shaped generations of off-road enthusiasts.
Now as Kenda Tires' Product Display Manager, Vanden Heuvel continues supporting the sport, assisting drivers across multiple series while representing Kenda at events nationwide. His dedication embodies the brand's values of community and passion for motorsports.
The formal induction ceremony will be held on 2 November 2025 in Las Vegas. This honour celebrates not just Vanden Heuvel's remarkable racing achievements but his enduring legacy as an ambassador who has profoundly influenced off-road culture.
Brandon Stotsenburg, VP of Automotive Division, Kenda Tires USA, said, “Dan is more than a legend – he is a mentor, a servant-leader and the beating heart of the off-road community. He helped deliver Kenda’s first PRO championship and still shows up for others every single weekend. We are honoured to have him represent Kenda and even more proud to call him family.”
Comments (0)
ADD COMMENT