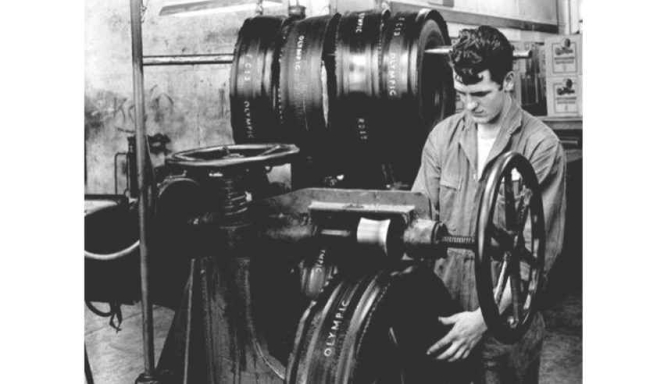
Nothing is stable. Technology is continuously evaluated. Materials science, electronics and software are the main three engines that reverse reactions or open new horizons.
Tyres are always known as black and round. However, the tyre engineers are aware of the weight achieved, the construction and the types of materials used in the tyres. What was the ancestor of the tyre, where is it going now?
The tyres were rated very quickly after vulcanisation 150 years ago. The first use of synthetic rubber and synthetic fibers, as well as the first radial tyre, go back around 70 years. Programming the control of the tyre building and curing machines with sensors and timer was a cornerstone. The new chemicals and advanced materials which suit well for process control, more homogeneous mixing, material integration and long-lasting rubber products.
Today's tyres last to the end of their useful life, which is primarily measured by the Remaining Tread Depth (RTD) which is greater than a limit value set by local legal approval. Twenty years ago, many defective tyres were found in scrapyards that were almost like new, but today the tyre will last almost lifetime.
Today, Mechanical rubber derivatives production machine parts are made to tighter tolerances. The integrity of the main body material is higher than in previous years. Alloys or composites are widely used compared to recent years. More controlled and homogeneous surface finishing is applied. Modern tyre production machines are equipped with robotics, full sensors and automation, stepper motors and greater controllability which are examples of the harmonization of creativity and innovation in the industry.
More than all that, today manufacturing machines are more purpose oriented, lighter, sensitive and modular.
The other very preliminary point of view is to analyse the needs of the main processes and what should be the strategy when you have an idea to buy new machines?
Every system needs new machines to install for a reason. It is used either to increase capacity or to renew a range of products, just to modernise or update technology. What should be the strategy when you have an idea to buy new machines? Either you are looking for a machine that matches your technology or you are taking the risk of a technology upgrade. The same category but a more efficient, more productive, safer and more controllable machine may be preferred or a completely new technology may be chosen.
If a very new technology is chosen, the time it takes to adapt can result in large production losses. It may take longer to adapt, etc. However, if you don't take such a risk, how will you manage the technology update in later years?
The other very preliminary point of view is to analyse the needs of the main processes. For example, if you are a tyre manufacturer, customers will only know your brand name. You are responsible for the end product. Third parties do not know where to start preparing tyres or what process to use to make them.
For example, you can have a textile calendar or you can get calendered textile and steel layers on the outside. When using a supplier, you don't need a factory calender machine. This also applies to the compounds used in the manufacture of the components. Today, a large volume of masterbatch is used in the rubber products industry. Organizing a good supply chain for manufacturing rubber compounds eliminates the need for mixers, a few mils, large silos, or process oil tanks.
A review of all processes and machine setup is necessary at regular intervals in order to remain competitive. Fewer production machines can increase productivity and controllability and intensify management. Less personal use, less energy and maintenance costs can be achieved. However, alternative suppliers need to be developed and diversified.
In the past, some particularly large tyre manufacturers had tyre cord treatment units in tyre factories. Some of them have steel wire production facilities for their own supply. Today we are witnessing a complete change of mind. The focus on the main process areas is mainly taken into account, which has completely changed the perspective in business. Today, most tyre manufacturers contract out the processing of 2nd class compounds. So, there is no refinery mill machines in tyre factories. The heating of the rubber in the preparation zones of the main components is carried out by cold feed extruders. Large capacity extruders are used under the drop door in mixing rooms. As a result, there are very few milling machine and milling operators in the tyre factory. Factory structures are smaller, parts production and machine maintenance are outsourced.
Full robot transfer units already exist, No man-tyre building and curing are achievable now. Profile extruders are already disabled, calendering might be totally needless by body ply webbing on tyre building drums.
Being open and innovative in the tyre and rubber industry is important. Support for technological innovation and productivity, as well as the vision to find more efficient devices, is required. New control systems with computers and automation are inevitable. Indeed, the company's employees must have a vision to choose the last and the best for the future. The most important thing is to find profitable solutions for the entire company.
As you follow the progress of the machine, keep in mind that new materials are coming. Any fashionable material will one day be a burden on the staff. Major hardware changes require new processes or machines. The ultimate case is the cancellation of part of the process, which means the cancellation of the production machines. Such a case can be irresistible at any time.
The increasingly demanding structure of the automotive industry and regulations will demand ever lighter, more environmentally friendly and more rolling-resistant tyres, which repeatedly calls for ambitious innovations. Innovative materials are inevitable to exceed expectations. Just as new materials come out of the R&D thicket box and enter the daily production inventory, the production area and machinery should be reorganised.
Full robot transfer units already exist in many phases instead of being transported. There are automatic scan and uniformity checks. No man tyre building and curing operations are achievable now. Profile extruders are already being phased out in some tyre factories. Body ply webbing could be more of a standard technology in tyre building. Calendering may be totally needless in tyre plants.
As far as automation and controllability technologies assess, there is still room for refinement or cancellation of production processes and machines in tyre factories.
Today, Mechanical rubber products production machine’ parts are made to tighter tolerances. The integrity of the main body material is higher than in previous years. (TT)
Eurogrip Tyres Displays Premium Two-Wheeler Tyres At F2R Expo
- By TT News
- May 16, 2025
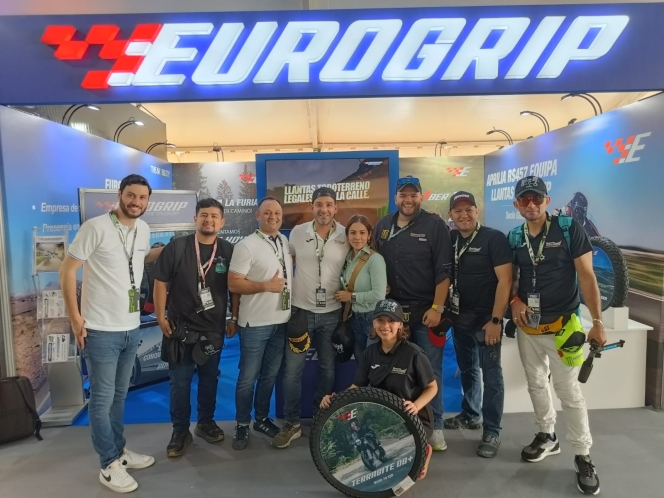
Eurogrip Tyres, the leading tyre manufacturer in India, showcased its premium two-wheeler tyres at the 17th edition of Feria 2 Ruedas (F2R) International Motorcycle exhibition held at Plaza Mayor, Medellin, Colombia. The dates of this high-profile business event in South America's two-wheeler sector are 15–18 May 2025.
For more than 17 years, the Feria de las 2 Ruedas (F2R) has been the leading motorcycle industry event in Latin America. The expo, which takes place every year in Medellín, Colombia, is a vibrant venue for commerce, innovation and growth in the motorcycling sector. Additionally, it gives aficionados the chance to investigate the most recent developments and trends in the industry. The company showcased its premium lineup at exhibit N24 in the Tented Pavillion, which included a range of sport touring, off-road and trail tyres. High-performance versions including the Roadhound, Protorq Extreme, Trailhound STR, Climber, Bee Connect, Terrabite DB+ and Badhshah LX were on display.
P Madhavan, Executive Vice-President – Marketing & Sales, TVS Srichakra Ltd, said, “Eurogrip is focused to deliver innovative products for the global markets. Latin America is a priority market for us, and F2R Expo is a promising platform to engage with our target audience. We are looking forward to interesting business opportunities arising from this expo. Such specialised industry tradeshows add exceptional value to our quest in becoming a leading global tyre brand delivering world class tyre technology.”
Denka Records USD 108 Mln Impairment Loss, Halts US Chloroprene Rubber Production
- By TT News
- May 16, 2025
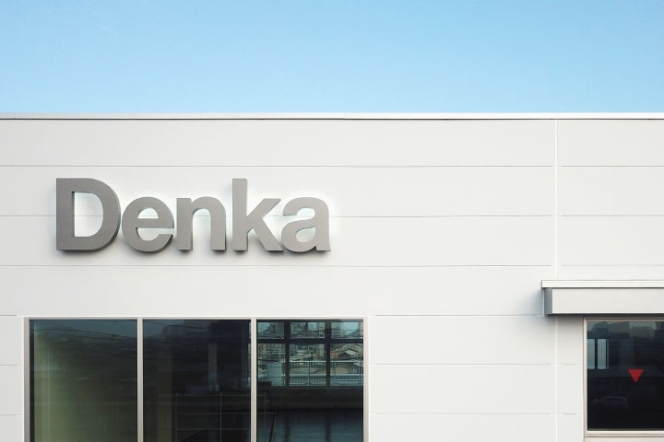
Denka Company Limited announced it would record an extraordinary loss of approximately 16.1 billion yen (£85.8 million) as an impairment on manufacturing facilities at its US subsidiary. It will indefinitely suspend chloroprene rubber production at the Louisiana plant.
The Japanese chemical manufacturer, which holds a 70 percent stake in Denka Performance Elastomer LLC (DPE), cited mounting operational challenges, including unexpectedly high costs for pollution control equipment and declining production volumes at the American facility.
“DPE has faced significant cost, production and other challenges at its facility in the United States,” the company said in a statement. “Rising costs are attributable to, among other factors, identification, design, purchase, installation, and operation of pollution control equipment to reduce chloroprene emissions that DPE did not anticipate being required when it acquired the facility from E.I. DuPont de Nemours and Company.”
The subsidiary was established in December 2014 and acquired the chloroprene rubber business from DuPont in November 2015. The Louisiana facility was intended to serve as a second manufacturing site in North America, complementing Denka’s Omi Plant in Itoigawa, Niigata, Japan.
However, according to the company statement, DPE has struggled with multiple operational issues, including “rising energy costs and a shortage of qualified staff necessary to operate new pollution control equipment and implement other emission reduction measures. “
Production volumes have declined partly due to “operational restrictions arising from the pollution reduction measures and unscheduled plant outages associated with supply chain disruptions and severe weather events,” Denka said.
The company noted that these challenges, combined with changes in the global economic environment for chloroprene rubber, have pressured profitability, making near-term improvement difficult.
Denka confirmed that DPE employs 250 people as of December 2024 and will not restart its chloroprene rubber manufacturing facilities following a regular maintenance shutdown. Instead, “all options for the business, including a potential sale of the business or its assets, will be considered,” the statement said.
The company emphasised that “no decision regarding a permanent closure of the facility has been made at this time.”
Customers will continue to be supplied from current inventories and production at the company’s Omi Plant in Japan.
DPE is 70 percent owned by Denka USA LLC, a wholly owned subsidiary of Denka Company Limited, and 30 percent by Diana Elastomers, Inc., a subsidiary of Mitsui & Co., Ltd.
Yokohama Rubber Posts Sharp Profit Drop Despite Revenue Growth in Q1
- By TT News
- May 16, 2025
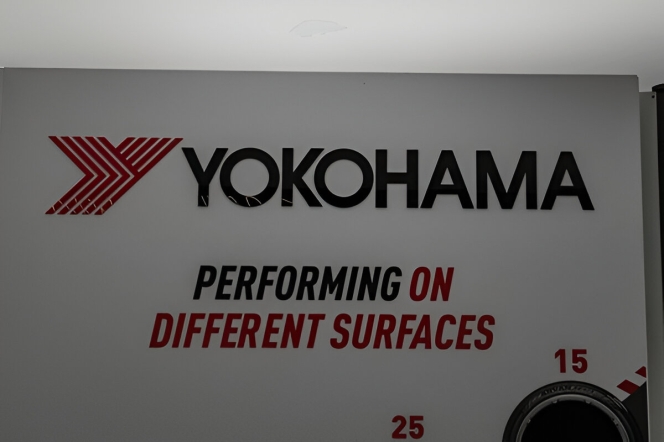
Yokohama Rubber reported a 56.9 percent year-on-year decline in profit attributable to owners for the first quarter of 2025, despite posting a 9.0 percent increase in sales revenue.
The Japanese tyre maker recorded a profit of 8.53 billion yen for the three months ended 31 March, down from 19.8 billion yen in the same period last year. Business profit fell 3.2 percent to 24.07 billion yen, while sales revenue rose to 275.12 billion yen.
The company maintained its full-year forecast, projecting an 11.4 percent increase in sales revenue to 1.22 trillion yen and an 8.8 percent rise in profit to 81.5 billion yen for the fiscal year ending 31 December 2025.
Yokohama Rubber attributed the profit decline to one-time costs related to its February acquisition of Goodyear’s off-the-road (OTR) tyre business, which it purchased for approximately 143 billion yen.
“Profit from existing businesses was strong,” the company said in its earnings statement. “In addition to increased sales volume for the company’s consumer tyres, mainly in overseas markets, and continued expansion of sales of high-value-added ADVAN, GEOLANDAR, and Winter tyres as well as high-inch tyres, profit was boosted by the MB segment’s MIX improvements and structural reforms.”
The tyre segment, which accounts for 91percent of the group’s consolidated sales revenue, saw a 10.4 percent increase in sales to 250.32 billion yen. Original equipment tyre sales were higher year-on-year, driven by “strong sales in Japan of vehicle models equipped with YOKOHAMA tyres and expansion of shipments for Chinese automakers’ new energy vehicles,” the company said.
Replacement tyre sales also increased, supported by higher sales of summer and winter tyres in Japan, increased sales of high-inch tyres in Europe, and stepped-up sales efforts in Asia.
The MB (Multiple Businesses) segment, which represents 8.4 percent of total sales, experienced a 3.2 percent revenue decline to 23.02 billion yen. This was attributed to lower demand from construction machinery makers in Japan and automakers in North America.
The company described an “upbeat” business sentiment in Japan for the quarter, noting that “a steady recovery in inbound demand and increasing orders for construction and logistics projects compensated for weak consumption by domestic households curbing spending in response to rising prices of consumer goods.”
Overseas, the company observed rising inflation concerns weighing on consumer spending in the United States, while in Europe, “manufacturing industries are rebounding and corporate business sentiment is improving.” In China, personal consumption was boosted by the Spring Festival holiday, but high US tariffs “reduced China’s exports and created uncertainty about the future that is weakening industrial activity.”
Nynas Delivers Robust 2024 Performance, Outlines Strategy Through 2035
- By TT News
- May 16, 2025
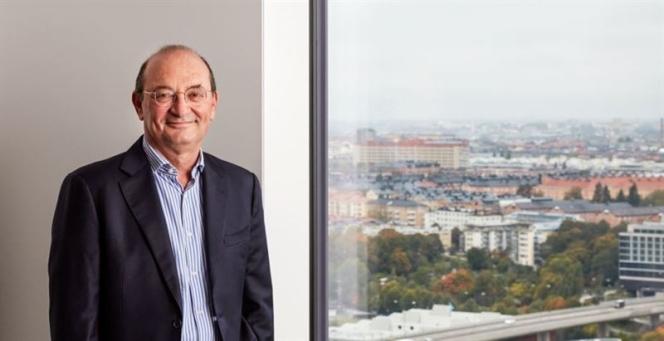
Swedish speciality chemicals firm Nynas reported solid financial results for 2024, posting an Adjusted EBITDA of 1,333 million Swedish kronor, marginally higher than the 1,316 million kronor recorded in 2023.
The company, which specialises in naphthenic speciality oils and bitumen products, attributed its performance to operational efficiency and commercial success in its niche markets.
“We are delighted with the progress made during 2024, evidencing our right-sized cost base and a more targeted commercial and manufacturing footprint. We have redefined our strategic direction, positioning Nynas as a speciality chemicals company, enabling the energy transition and setting our course for 2035,” Nynas CEO Eric Gosse said in a statement.
The firm highlighted strong cash generation from operations, which it said would support planned investments and longer-term growth initiatives. Nynas also mentioned the ongoing transformation of its Harburg site with plans to monetise the asset eventually.
All three of the company’s production facilities maintained high operational reliability between 95 percent and 99 percent. The Nynäshamn refinery achieved a notable milestone: in May 2024, it set a new monthly production record for naphthenic speciality oils at 42,000 tonnes.
Strategic pivot towards sustainability
Nynas outlined a strategic shift focused on higher-margin speciality materials with sustainable characteristics. The company aims to strengthen its position in European markets through innovation and sustainability initiatives.
“Nynas is uniquely positioned to contribute to the energy transition. Our strategy reflects our purpose to advance a more sustainable society, and our product development pipeline is fully aligned with this goal," Gosse added.
In 2024, the company received an EcoVadis Gold rating, placing it in the top 5 percent of globally rated businesses for sustainability performance.
With consecutive years of strong financial performance, Nynas indicated it continues to monitor debt capital markets to optimise its capital structure “at the appropriate time potentially”.
The Swedish chemicals producer noted that, having ceased operations in the United States in 2022, it remains largely insulated from recent global trade tensions surrounding US import tariffs. The company imports only minimal feedstock from America, shielding it from potential cross-border trade disputes.
Comments (0)
ADD COMMENT