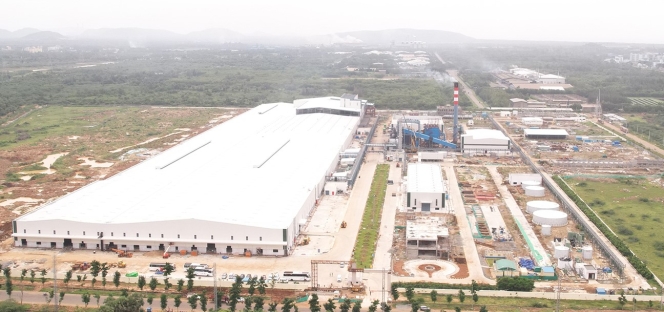
Yokohama Off-Highway Tires (YOHT), a Yokohama Rubber Group, has started production at its Visakhapatnam plant, India, which will respond more quickly to expanding global demand for off-highway tyres.
The new plant, which was originally scheduled to begin production in the first quarter of 2023, was inaugurated in the presence of Jagan Mohan Reddy, the chief minister of Andhra Pradesh, the Indian state where the plant is located, Masayuki Taga, Consul General of Japan in Chennai, and Nitin Mantri, a member of the board and managing officer of the Yokohama Rubber and the head of the Group’s OHT division.
In its initial production stage, the Visakhapatnam Plant will have a daily capacity of 69 tonnes (rubber weight). The plant’s daily capacity will be increased to 132 tonnes in the second stage planned to start in the first quarter of 2024. Further expansion of the plant’s capacity is under consideration, said the company.
Nitin Mantri said, “We are very excited with this best-in-class facility that will set a new benchmark for quality and productivity in the OHT segment. With our increased capacity we will reduce our lead times to better serve our global customer base”.
The company already has two plants – Dahej, Gujarat and Tirunelveli, Tamil Nadu, which produces three brands- ALLIANCE, GALAXY and PRIMEX used for agricultural, construction, industrial and forestry machinery.
YOHT also has two other tire plants in India—the Dahej Plant in the state of Gujarat and the Tirunelveli Plant in Tamil Nadu. The plants produce three of the Group’s core OHT brands—the ALLIANCE, GALAXY and PRIMEX brands—which are used on agricultural, construction, industrial and forestry machinery. YOHT sales have been expanding faster than the overall OHT market. To meet the demand for its products, Yokohama Rubber began the construction of the Visakhapatnam Plant in the third quarter of 2020 to supplement a 1.6x expansion of production capacity at the Dahej Plant.
- Hankook Tire
- Hankook Tire Hungary
- Hankook Tyres
- Key Supporter of Saint Pantaleon Hospital
- Semmelweis Day
Hankook Tire Hungary Honoured With ‘Key Supporter Of Saint Pantaleon Hospital’ Award
- By TT News
- July 09, 2025
Hankook Tire Hungary Ltd received the ‘Key Supporter of Saint Pantaleon Hospital’ award during the hospital's Semmelweis Day ceremony in Dunaújváros, Hungary. This recognition highlights the company's longstanding commitment to enhancing local healthcare quality through consistent contributions.
Marking a new tradition, this year's ceremony expanded beyond honouring healthcare workers to acknowledge institutional supporters. Hankook earned this distinction through multiple initiatives, including recent equipment donations for the paediatric ward and installation of a nurse call system in the surgical department. The company's support extends to previous years' projects such as ventilator procurement, maternity ward renovations, and pandemic-related protective equipment donations.
The award coincides with Hungary's annual Healthcare Day celebrations on 1 July, which since 1992 has honoured medical professionals nationwide. By recognising Hankook's sustained community involvement, Saint Pantaleon Hospital underscores the vital role of corporate partnerships in maintaining quality healthcare services.
Dr Örs Szilágyi, Director General of the Saint Pantaleon Hospital, said, “We are very grateful for the help and commitment of Hankook Tire Hungary. We are working together for a joint goal to improve continuously the standard of healthcare and thus create value for local citizen, help them in maintaining their health and in getting better. Hankook’s Corporate Social Responsibility sets an example to all. We are happy to award Hankook Tire Hungary Ltd as the first company with the ’Key Supporter of Saint Pantateon Hospital’ award.
Receiving the award from Dr Szilágyi on behalf of the company, Ho Taek Lim, Managing Director of Hankook Tire's Hungary Plant, said, “We are honoured to receive this recognition from Saint Pantaleon Hospital. At Hankook, we believe in long-term partnerships and consider the health of the people living here, our employees and their families to be our most important investment, which is why we intend to continue supporting local initiatives and institutions in the future.”
Metso Expands Screening Solutions With New Production Centre In Romania
- By TT News
- July 09, 2025
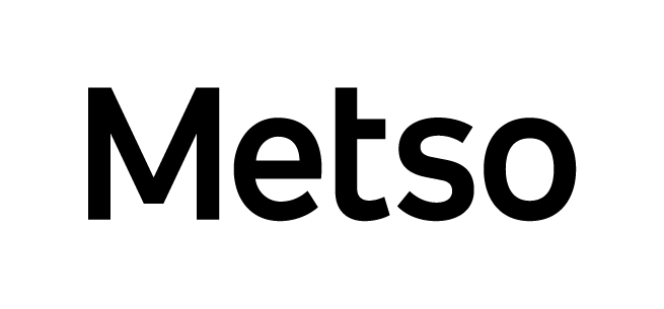
Metso is strengthening its position in sustainable screening technologies by establishing a new manufacturing facility in Oradea, Romania. This strategic investment supports the company's growth plans by boosting production capacity and enhancing service capabilities for customers across Europe, Central Asia and the Middle East.
The new centre will focus on manufacturing stationary screening equipment while expanding spare and wear parts supply, including rubber screening media. Expected to employ 70-80 people by 2026, the facility will improve regional customer support in minerals and aggregates markets where demand is growing.
The Romanian production hub complements Metso's existing global manufacturing network, which includes facilities in France, Brazil, India, South Africa and China. This expansion reinforces Metso's commitment to delivering efficient, localised solutions while supporting customers with faster service and optimised screening technologies.
Jouni Mähönen, Vice President of the Screening business line, said, “This investment is a continuation of our regional strategy implementation. A new centre in Romania will improve responsiveness to meet customer needs, answer to growing demand in growth markets and strengthen our ability to deliver tailored screening solutions efficiently.”
Adrian Wood, Vice President, Central Region Screening business line, said, “Customer proximity is at the heart of our service philosophy. Through this investment, we enhance our ability to serve customers by being faster and efficient. We will be able to be more flexible, allowing us to meet regional specifications and needs while also ensuring strong service capabilities through integrated screening media production.”
Michelin Reinforces Leadership In Reducing Tyre Wear Particles With New ADAC Recognition
- By TT News
- July 09, 2025
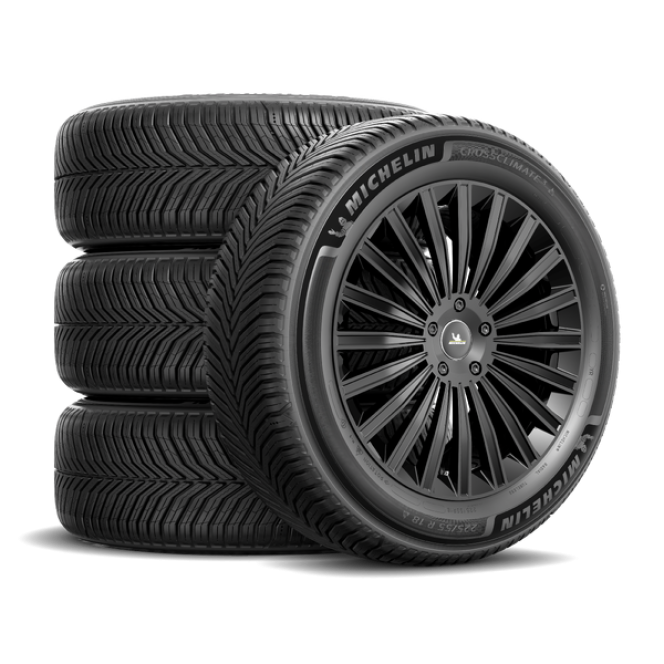
Michelin has once again been recognised by ADAC, Germany's leading automobile association, as the industry leader in reducing particle emissions from tyre abrasion. This marks the second consecutive time Michelin has received this distinction, reinforcing its commitment to sustainable mobility. Recent ADAC tests on 160 tyre models revealed that Michelin tyres emit 26 percent fewer particles than the premium competitor average, building on similar results from a 2021 study, where Michelin outperformed rivals by 28 percent. Notably, Michelin's closest competitor emitted 20 percent more particles per kilometre and per metric tonne transported.
These findings highlight Michelin's dedication to innovation, delivering tyres that balance longevity, safety and minimal environmental impact. The company has focused on reducing tyre abrasion – a key contributor to road transport emissions – for nearly two decades. Between 2015 and 2020, Michelin’s advancements led to a five percent reduction in wear emissions, preventing an estimated 100,000 metric tonnes of particles from entering the environment.
The issue of tyre abrasion has gained regulatory attention, with the Euro 7 standard, enacted in July 2024, setting strict limits on particle emissions for tyres sold in Europe. This regulation aims to curb the 500,000 metric tonnes of tyre and road wear particles generated annually across the continent.
Michelin continues to invest heavily in R&D, allocating EUR 786 million in 2024 alone, to further mitigate abrasion through advanced materials and optimised tyre design. Recent innovations, such as the MICHELIN Primacy 5 (14 percent fewer emissions than its predecessor) and the CrossClimate 3 Sport (23 percent reduction compared to the Pilot Sport 5), demonstrate tangible progress. Additionally, Michelin’s BioDLab—a collaboration with CNRS and the University of Clermont Auvergne—focuses on studying particle biodegradation to develop eco-friendly solutions.
By combining cutting-edge research with sustainable design, Michelin aims to further reduce emissions while maintaining high safety and performance standards, reinforcing its role as a pioneer in environmentally responsible tyre technology.
Continental Educates Fleets On Rolling Resistance’s Growing Role In Cost And Emissions Savings
- By TT News
- July 09, 2025
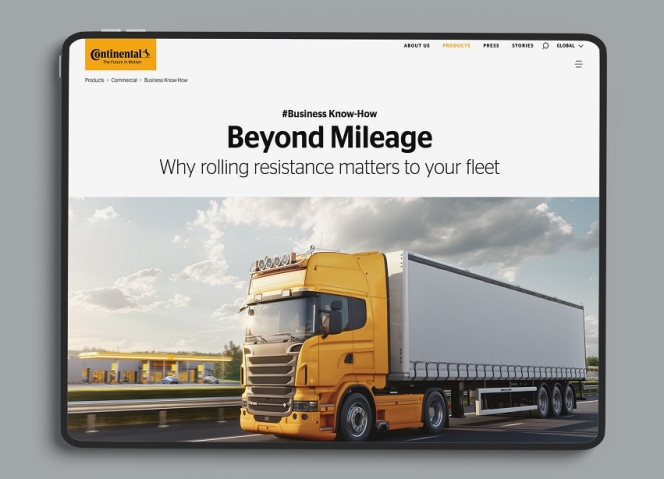
Continental has launched an educational initiative highlighting how rolling resistance-optimised tyres can enhance efficiency and sustainability in commercial vehicle fleets. The campaign, anchored by a dedicated website, provides fleets with interactive tools, videos and data-driven insights to demonstrate how strategic tyre selection impacts total operating costs.
While many fleet operators traditionally prioritise mileage-optimised tyres for their longer tread life, Continental emphasises that rolling resistance plays an increasingly critical role – especially with tightening EU emissions standards and the logistics sector’s shift towards greener transport. Tyres influence not just direct costs (around two percent of fleet expenses) but also fuel consumption, toll fees and CO₂ emissions, affecting up to 31 percent of total operating expenses.
The campaign compares Continental’s fifth-generation tyre lines – Conti Eco, Conti Hybrid and Conti EfficientPro – in various applications, showing how low rolling resistance can reduce fuel use by up to 2,105 litres per vehicle annually. For a 150-truck fleet, proper tyre selection can yield over EUR 300,000 in yearly savings. Continental’s calculations, based on VECTO and its proprietary LODC (Lowest Overall Driving Costs) tool, illustrate these benefits for long-haul and regional transport scenarios.
Beyond tyres, Continental integrates digital solutions like ContiConnect and retreading services (ContiLifeCycle) to further optimise fleet efficiency. Customers like Remondis, a German waste management firm, report tangible benefits, including lower fuel consumption, extended tyre life and proactive maintenance through digital monitoring.
With this initiative, Continental aims to help fleets balance economic and environmental goals, proving that rolling resistance-optimised tyres are not just a compliance measure but a strategic tool for cost savings and emissions reduction in modern logistics.
Comments (0)
ADD COMMENT