- CEAT
- SportDrive
- CALM Technology
- RPG Group
- Run-Flat Tyres
- Lakshmi Narayanan B
- Renji Issac
- Vishal Pawar
CEAT Gets Ready To Tap Into Premium Passenger Vehicle Market
- By Nilesh Wadhwa
- April 24, 2025
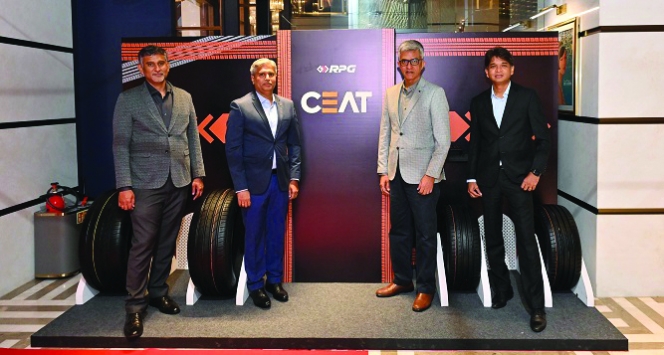
With a fresh onslaught of tyres for the luxury and premium performance vehicles, CEAT furthers its positioning in the PCR segment.
CEAT, the flagship company of the RPG Group, is targeting to be amongst the top 10 tyre makers globally and is outlining an ambitious growth strategy that looks to expand its product offerings across segments and the globe.
On 19 March 2025, CEAT expanded its SportDrive tyre series with the launch of new products targeted specifically for luxury and high-performance passenger vehicles. The idea, however, goes beyond just chasing volumes. The company launched Run-Flat tyres, which withstand punctures and can be safely driven at considerable speeds for up to 80 km before needing repair. This also made CEAT the first Indian tyre maker to roll out such a product in the country.
Furthermore, it has also introduced 21-inch ZR-rated tyres that are designed to handle speeds of up to 300 kmph while also being quieter due to the CALM technology, which utilises special foam inside the tyre.
The question is, what is CEAT looking to gain, given that the Indian premium luxury car market is just a fraction of total passenger vehicle sales?
For context, last year the luxury car segment crossed the 50,000-unit sales milestone for the first time in India. In total, the premium car market saw sales of around 51,200 units in CY2024, which was about six percent higher compared to 48,500 units sold last year. This translates to just about one percent of the total passenger vehicles sales in the country. In comparison, some of the Southeast Asian markets see luxury cars compromise about 5-6 percent of the total car sales, and for markets such as Taiwan, it has reached as high as 20 percent.
CEAT, however, believes that being present in the segment is important. Lakshmi Narayanan B, Chief Marketing Officer, CEAT, told Tyre Trends, “There are two main segments. One is the world of sport SUVs, which includes the 21-inch and larger tyres. Currently, this segment is dominated by imported vehicles, making it relatively small. However, our focus is on establishing our presence for brand stature. The second segment is the luxury ecosystem, where our SportDrive tyres cater specifically to high-end vehicles. This is also where the opportunity for run-flat tyres lies. While we are launching two specific sizes, we see significant potential for expansion.”
FOCUS ON R&D
CEAT has been investing significantly towards creating new patents. For instance, in FY2024, the company cumulatively filed 171 patents and spent around INR 1.73 billion in R&D expenditure.
Coming to the recently launched products, the tyre maker has been working on them for over three years. The company’s R&D Centre in Germany and India have worked in tandem to develop world-class products that can meet the needs of the Indian as well as global markets.
“We leverage European strengths while also utilising India’s manufacturing capabilities, which creates a great combination and a significant opportunity for us. Our priority is delivering value to the customer. As we continue expanding within this particular technology, we have introduced three specific deliverables. First, we have the 21-inch ZR-rated tyre, designed for both the Indian and European markets. The German market, especially the Autobahns, requires high-speed-rated tyres, and this offering allows us to cover the entire speed rating ecosystem essential for success there. Second, we have introduced Calm Technology. This technology expands our range into the existing SportDrive and SportDrive SUV segments, which we will continue to develop over time. Third, and most importantly for India, is our run-flat tyre. Our goal is to engage with consumers and provide more relevant value. As we monitor consumer adoption, we will explore opportunities for further expansion,” stated Narayanan B.
It is important to understand, as seen in global trends, that the Indian passenger vehicle segment’s shift towards SUVs is also driving demand for bigger tyre sizes. For instance, 16-inch tyres are becoming a common sight, while demand for 17-inch and 18-inch tyres are being demanded in the aftermarket segment.
But what about the recently introduced 21-inch tyres, where the demand in India remains miniscule?
“The 21-inch tyre has significant potential in Europe, particularly on Autobahns. However, cost advantages vary by region. In a competitive market with over 100 brands per country, success depends on positioning and perceived value rather than cost alone. In Italy, for example, our brand is well regarded due to historical trust in our products,” shared Narayanan B.
ENERGY-EFFICIENT & CALM TECHNOLOGY TYRES
Pollution, energy security and sustainability are pushing industries to embrace cleaner and efficient materials, processes, production and end-products.
In the automotive industry, this translates to automakers and suppliers adopting newer technologies, chemistries and improving efficiency. Electrification of vehicles is amongst one of the newer trends being seen as a significant way to cut down on carbon emissions.
CEAT on its part had introduced EnergyDrive tyre series, which was specially designed for electric vehicles. They not only provided better energy efficiency but also lower noise.
Renji Issac, Senior VP and Head of R&D and Technology, CEAT, explained, “We started with a dedicated product range for EVs called EnergyDrive. However, we realised that, over time, tyres for EVs and internal combustion engine (ICE) vehicles would converge. We have incorporated all our learnings from EV-specific tyre development into our standard product line, ensuring that our future tyres will be suitable for both EVs and ICE vehicles. This approach reduces manufacturing complexity while providing benefits such as extended tyre life, lower noise levels and improved durability for customers.”
Narayan B added that the company sees this trend not only in passenger cars but also scooter segment, especially in India, where electric two-wheelers is seeing significant uptick. “Our EnergyRide caters to two-wheelers, passenger cars and Winenergy supports commercial trucks and buses. We are the first company to offer a complete EV-centric platform across all vehicle categories,” he said.
Vishal Pawar, Senior Vice President – Global Sales & Supply Chain Head, CEAT, revealed that the company currently has around 25 percent market share in the electric two-wheeler segment.
“In the EV ecosystem, we are a leading player, both in OE (original equipment) fitments and the replacement market. However, many consumers do not distinguish between EV and ICE tyres when replacing them. Our marketing efforts include educating mechanics about the differences and best practices for EV tyres. For instance, the Tata Nexon EV was a significant starting point for EV adoption, and now we also supply tyres for the Tata Punch EV, incorporating Calm Technology and foam-based noise reduction. This is an evolving market, and we are positioning ourselves accordingly,” said Pawar.
Right from the start, CEAT worked upon identifying potential failure modes in early development and specifically tested the Calm Technology for such conditions. Issac explained that the adhesive and foam materials have been rigorously validated to withstand extreme conditions, including high-speed driving and water exposure.
“If a tyre requires repair, only a small portion of the foam needs to be removed, and this does not impact the performance. The Calm Technology tyre offers reduction of approximately six decibels in noise, which is a significant improvement. The noise perception is not linear in a vehicle, meaning each decibel reduction translates to a notable difference in actual experience,” said Issac.
Narayanan B added that the idea was to make “these tyres as close to conventional ones as possible, ensuring ease of use for consumers. We have rigorously tested them, and they are designed to deliver tangible value without requiring special treatment from users.”
CREATING AWARENESS
In India, most of the tyre purchase decisions in the aftermarket is heavily influenced by the tyre dealer partner. CEAT too believes that there is a lack of understanding amongst customers in India when it comes to selecting the right kind of tyre for their vehicles, especially in the passenger vehicle space.
For instance, if one asks an average consumer about the speed rating of the tyre, the ideal assumption is that a tyre which fits perfectly. The tyre speed rating is denoted as T, H, V, W, Y or Z – they basically indicate that they are designed to sustain a particular speed.
The company has introduced the ZR-rated tyres that cater to the increasing demand for high-performance vehicles in India, particularly performance-oriented SUVs and sedans that require tyres capable of handling speeds above 220–240 kmph.
The SportDrive SUV tyres feature a dual-layer high-denier nylon overlay to minimise tyre growth at high speeds, enhancing stability and grip, along with a high-denier polyester fabric for durability and the ability to withstand high torque. Available in larger sizes such as 315/40ZR21, 275/45ZR21 and 285/45ZR21, these tyres cater to the super-premium segment.
They have been tested on Germany’s Autobahns and are engineered to meet global standards while being optimised for Indian driving conditions.
CEAT sees export potential in markets such as Europe and Middle East where the demand for high-performance tyres, especially in the 21-inch segment, is quite high.
GROWTH OUTLOOK
CEAT has outlined its ambition of being the second largest tyre manufacturer in the Indian passenger car radial (PCR) segment.
For this, Narayanan B shared that the company is pursuing focus on both premium as well as mass-market segments.
“Our CrossDrive, Secura SUV and Mileage X5 tyres have been well received. Success will come from balancing premium offerings like SportDrive with high-volume products that cater to the broader market,” he shared.
But what about impact of the natural rubber shortage?
Issac shared that at present India witnesses almost 500,000 metric tonnes of natural rubber shortfall and relies on import. The country has a requirement of almost 1.3 million metric tonnes of natural rubber and growing but only around 800,000 metric tonnes is currently produced domestically.
“While initiatives like the INROADS programme aim to boost domestic production, substantial benefits will only be seen post-2030. Until then, securing supply remains a priority,” added Issac.
On the other hand, Narayanan B remains upbeat on the Indian automotive industry’s growth.
“While volume growth remains uncertain, value growth is evident. People are driving more, increasing tyre demand. Despite market fluctuations, we remain focused on moving towards a leadership position in the industry,” signed off an optimistic Narayanan B.
Nexen Tire Bags Gold Rating From EcoVadis For 2nd Consecutive Year
- By TT News
- July 15, 2025
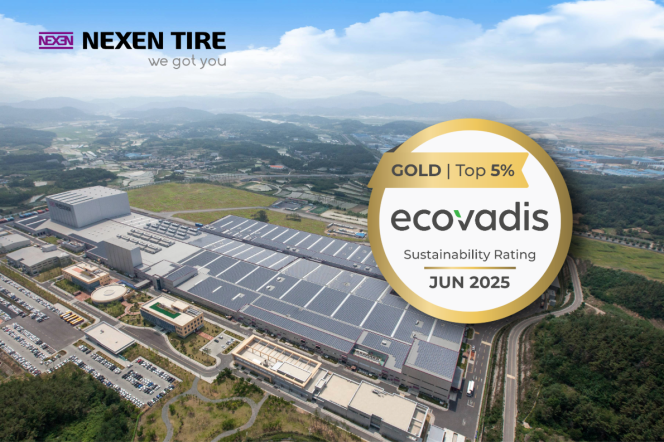
South Korean tyre major Nexen Tire has added another feather to its cap and has received a Gold rating from EcoVadis for the second year in succession. This places the company among the top 3 percent of over 150,000 companies assessed globally.
Established in 2007 in France, EcoVadis evaluates corporate sustainability performance across Environment, Labour & Human Rights, Ethics and Sustainable Procurement. Its ratings are Platinum (top 1 percent), Gold (top 5 percent), Silver (top 15 percent) and Bronze (top 35 percent).
Nexen Tire showed improvements across all assessment areas. In the Environment category, the company's involvement in global sustainability initiatives, including the Global Platform for Sustainable Natural Rubber (GPSNR), the UN Global Compact (UNGC) and the Science Based Targets initiative (SBTi) was noted. Climate education programmes and greenhouse gas emissions disclosure were contributors.
For Labour & Human Rights, Nexen Tire's human rights policy aligns with international standards from the United Nations and the International Labour Organization (ILO). The company also began human rights assessments for risk management.
In the Ethics pillar, the company reinforced internal systems for risk prevention, monitoring, and mitigation. The Sustainable Procurement score improved through ESG assessments, supplier audits and risk response strategies.
John Bosco (Hyeon Suk) Kim, CEO, Nexen Tire, said, “Receiving the Gold rating from EcoVadis for the second consecutive year is a significant affirmation of our global ESG efforts. We remain committed to responsible and transparent management practices that meet the expectations of our stakeholders worldwide.”
TÜV SÜD Appoints Ishan Palit As Interim CEO During Leadership Transition
- By TT News
- July 11, 2025
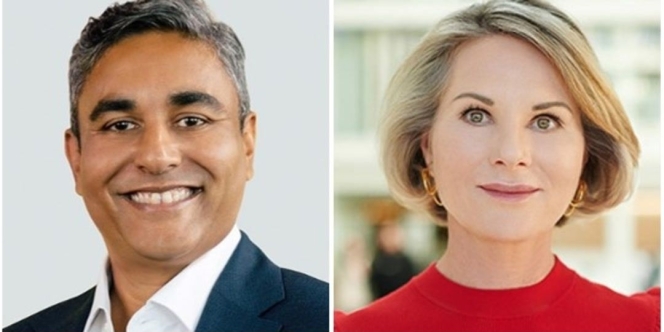
TÜV SÜD AG’s Supervisory Board has named Ishan Palit as Interim CEO (Chairman of the Board of Management) effective 15 July 2025, following Dr Johannes Bussmann’s departure to assume the CEO role at MTU Aero Engines AG. Bussmann will leave TÜV SÜD on 14 July 2025. Palit will co-lead the company with CFO Sabine Nitzsche until a permanent successor is appointed.
With over 30 years at TÜV SÜD, Palit has held key leadership roles, including establishing the company’s India operations, serving as Asia Pacific CEO and leading the global Product Service Division. Since 2017, he has been Chief Operating Officer, driving strategic and operational initiatives.
Nitzsche, who joined as CFO in March 2025, brings extensive financial and executive expertise from the high-tech and automotive sectors. Her prior roles include CFO of Vitesco Technologies AG and senior financial leadership positions at Infineon Technologies and GlobalFoundries.
Frank Hyldmar, Chairman of the Supervisory Board of TÜV SÜD AG, said, “We are very pleased that Ishan and Sabine will oversee the interim management of TÜV SÜD during this transition. Ishan is a seasoned TÜV SÜD senior executive with deep knowledge of our business and strong global leadership experience. Sabine brings a proven track record as CFO across multiple multinational enterprises. Together, they form a strong leadership team as we work towards appointing a long-term CEO.”
Hankook Tire Rejigs North American Sales And Marketing Team
- By TT News
- July 09, 2025
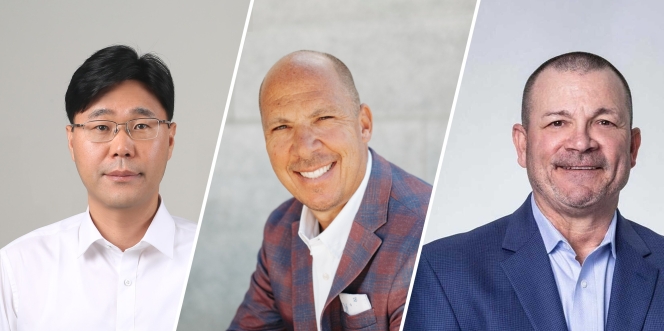
Hankook Tire & Technology has announced a series of executive leadership changes at its North American headquarters in Nashville, reinforcing its commitment to growth in passenger and commercial tyre markets. The restructuring brings fresh leadership across key sales and marketing functions.
Kyuwang (Ken) Cho assumes the role of Senior Vice President of North America Marketing, transitioning from his previous dual leadership of PC/LT Sales and Marketing. The industry veteran brings 25 years of Hankook experience, including a stint as Vice President of Global Sales in Korea. K C Jensen steps up as Vice President of US PC/LT Sales, expanding his responsibilities from regional to national oversight after demonstrating strong leadership in the Western market since 2018.
The company welcomes back Mark Roe as Vice President of US TBR Sales, where his four decades of commercial tyre expertise will guide replacement and OE sales strategies. Roe's extensive background includes previous leadership roles at Hankook and most recently at Ralson Tire North America.
Regional sales teams also see strategic promotions. Shaun Prott advances to Regional Director of PC/LT Sales for the West, building on his eight-year tenure with Hankook and prior experience with National Tire Warehouse. Travis Jones rejoins the organisation as Northeast Regional Director, bringing valuable perspective from Michelin and Pirelli. Brian Ford earns promotion to Regional Director of TBR Sales for the West after successfully managing key commercial accounts since 2021.
Rob Williams, President of Hankook Tire America Corp, said, "These leadership appointments reflect Hankook's strong momentum in North America. Ken, K.C. and Mark each bring exceptional industry experience, strategic focus and leadership qualities to their roles. Together, they will help elevate our presence across both consumer and commercial channels, and support our long-term growth ambitions in the US. These moves speak to the strength of our internal talent pipeline & ability to attract top talent and our continued investment in customer relationships. Shaun, Travis and Brian all bring deep knowledge of their markets and proven ability to grow key partnerships."
Michelin X Line Grip D Tyre Promises Range Of Upto 1 Million Miles & Upto 4 Retreads
- By TT News
- July 08, 2025
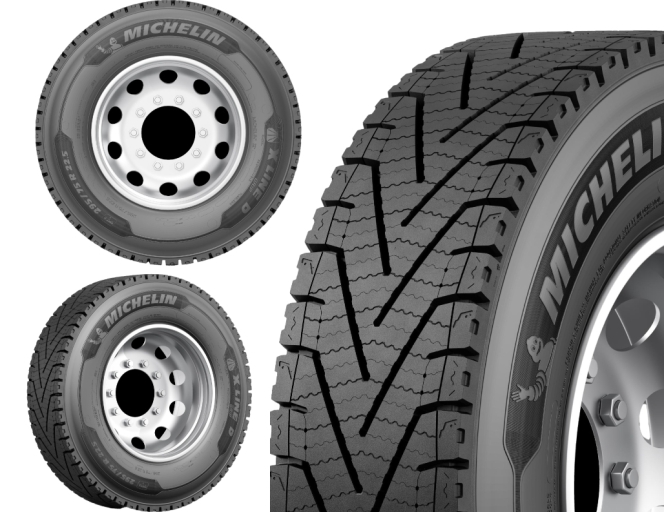
French tyre major Michelin has introduced its new X Line Grip D range, which is designed to work up to 1 million miles (1.6 million kilometres) with up to four retreads. The company shared its designers' claim that this is a ‘once-in-a-lifetime’ leap in tyre technology for fleets.
In addition to the higher range, the tyres also provide 20 percent more mileage and a 20 percent reduction in rolling resistance compared to the Michelin XDN2 tyre.
Designed to meet both wet and snowy conditions thanks to the chevron tread design, these tyres are said to prove 90 percent better starting traction in snow and over 25 percent better wet starting traction.
Fleets also benefit from using the Michelin X Line Grip D tyre, as it is built on the company’s Duracore casing, featuring Infinicoil and Powercoil technologies.
Pierluigi Cumo, VP – B2B Marketing, Michelin North America, said, “Michelin is never satisfied with current tyre technology when it comes to constantly improving and innovating our products. That’s why Michelin is so proud to introduce the Michelin X Line Grip D tyre. This tyre has the potential going forward to redefine the drive tyre standard in fleets for years to come. It is not an evolution to existing products, but something entirely different the fleet world has never seen before.”
“Michelin has a proven track record of delivering high-quality, reliable products that exceed performance expectations. This fantastic leap in drive tyre technology bring new levels of performance to the road and new levels of savings to our customers,” he concluded.
The Michelin X Line Grip D tyre is available in sizes 295/75R22.5 and 11R22.5.
Comments (0)
ADD COMMENT