Collateral Damage
- By Gaurav Nandi
- April 25, 2025

Retread tyres in Malaysia are unfairly blamed for road accidents. While the tyres enjoy a pristine reputation in export markets, the notoriety within the local market stems from the lack of ability to differentiate them from low-cost and low-quality tyres that fail to comply with performance standards owing to overloading, maintenance and misapplication.
A total of 1.35 million lives are lost each year in road accidents, according to data from the Ministry of Transport Malaysia. Another data set from Statista highlighted that the South Asian country witnessed 545,000 road accidents in 2022, an increase from the previous year data of 370,000.
A large portion of these accidents involve commercial vehicles and the blame is also shared by retread tyres. A recent news report highlighted rising concerns within the Malaysian parliament to ban the use of retread tyres of commercial vehicles citing safety norms.
The situation seems ironic as the Malaysian retread industry enjoys a pristine reputation in export markets. Yet, the notoriety of retread tyres on home turf might be seen as ‘collateral damage’.
Speaking to Tyre Trends exclusively on why retread tyres remain a scapegoat for road accidents, Tyre Retreading Manufacturers Association of Malaysia (TRMAM) President Edmund Wong said, “Retread tyres are often unfairly blamed for road accidents because the public struggles to differentiate them from low-cost, low-quality tyres that fail due to poor maintenance, overloading and misapplication. Many people mistakenly associate tyre debris, especially when it reveals exposed steel cords, with retreads. However, this type of failure is more commonly linked to cheap, substandard tyres rather than retreads, which, when properly maintained and used correctly, can be as safe as new tyres. The focus on retreads allows the real issues such as inadequate tyres maintenance and overloading to remain overlooked.”
IMPROVING ROAD SAFETY
Malaysia has a higher road fatality rate compared to ASEAN peers like Singapore, largely due to motorcycle-related deaths, which make up over 65 percent of fatalities.
Malaysia’s road safety goals have reportedly fallen short despite setting out clear targets. In 2014, the government aspired to reduce road fatalities by 50 percent by 2020 as part of its alignment with United Nations’ Decade of Action for Road Safety 2011-2020. The initiative was a failure and the same target was reiterated in Malaysia Road Safety Plan 2022-2030.
Current figures also raise questions over the supposed success of the target. Commenting on ways that could make the reduction target a reality, Wong noted, “To reduce road fatalities by 50 percent by 2030, Malaysia should enforce traffic laws strictly, including penalties for speeding and disobeying traffic lights, while expanding automated systems like speed and red-light cameras. Enhancing road infrastructure with safety audits, smart technology and dedicated motorcycle lanes is essential.”
“Malaysia can adopt best practices, such as dedicated motorcycle lanes, public education campaigns and improved road infrastructure, while learning from Singapore’s success in enforcement, infrastructure and safety culture. Public awareness campaigns should target risky behaviours including running red lights and promote defensive driving. Protecting vulnerable road users, especially motorcyclists and pedestrians, through improved infrastructure and safety regulations is also crucial,” he added.
Alluding to why stringent safety campaigns or regulatory measures are not undertaken to reduce motorbike fatalities, he noted, “The lack of stringent safety campaigns or regulatory measures targeting motorbike users in Malaysia is due to several factors. Firstly, motorbikes are a vital mode of transport for many due to affordability and accessibility, especially in rural areas, making stricter regulations politically sensitive. Secondly, enforcement of existing laws such as helmet use and licensing is inconsistent, particularly in rural regions, allowing unsafe practices to persist. Thirdly, cultural factors like risk-taking behaviour, resistance to change and low awareness of safety risks hinder the adoption of safer practices. Lastly, limited resources, both financial and infrastructural, result in insufficient investment in targeted campaigns and dedicated motorcycle lanes, leaving riders vulnerable.”
CLOSING GAPS
Wong iterated that to improve road safety and support the retreading industry in Malaysia, several regulatory gaps and enforcement lapses need to be addressed. One significant issue is the inconsistent enforcement of tyre standards, especially for imported new tyres.
While Malaysia requires that imported tyres have certifications like the E-mark, DOT or MS, these standards can sometimes fail to verify the genuineness and reliability of the tyres, leading to concerns about the quality and safety of some imports. This lack of stringent checks on tyres authenticity puts road users at risk and undermines confidence in tyre safety.
Additionally, there is a gap in regulations requiring regular tyre maintenance checks, particularly for retread tyres. Without mandatory inspections for tread depth, pressure and overall tyre condition, vehicles, especially commercial fleets, are at higher risk of tyre-related accidents.
Another issue is the weak enforcement of penalties for overloading and the misapplication of tyres such as using retreads in unsuitable conditions. Overloading vehicles puts excessive stress on tyres, increasing the likelihood of tyre failure, and stricter penalties are needed to deter this dangerous practice.
There is limited education on the benefits of retreads and how to use them safely, which affects their acceptance and proper usage. Implementing campaigns that highlight the safety, environmental and economic benefits of retreads could help improve perceptions and encourage safer practices.
Moreover, government procurement policies should prioritise retread tyres for public transportation fleets, encouraging their use across sectors and providing a market boost to the retreading industry.
Lastly, there is a lack of clear regulations on tyre end-of-life management including guidelines for recycling and disposal. Establishing clear regulations for the responsible management of worn-out tyre, including retreads, would support the circular economy and further promote the sustainability of the retreading industry.
Addressing these regulatory gaps and enforcement lapses would not only improve road safety but also foster the growth of a reliable, safe and sustainable retreading industry in Malaysia.
REPUTATION REVIVAL
The shadow of malignance over the local retread industry is daunting, especially considering its stellar reputation abroad. A methodical plan is urgently needed to change the prevailing perception.
Commenting on how the industry can leverage its foreign reputation to promote retreads domestically, Wong explained, “Malaysia can leverage its reputation in the global retreading industry to promote retreads domestically by focusing on education, policy support and sustainability initiatives.”
“Firstly, educating the public about the benefits of retreads, such as safety, environmental advantages and cost-effectiveness, can shift perceptions. Secondly, incentivising businesses to adopt retread tyres would not only increase its usage but also align with sustainability practices. Retreads significantly reduce waste by reusing tyre casings, contributing to lower carbon footprints and less landfill waste. Offering tax breaks, rebates or financial incentives to businesses that adopt retreads can encourage the adoption of this eco-friendly practice, benefiting both companies and the environment,” he added.
He also noted that Malaysia has a well-established certification system with Malaysian Standard 224 (MS 224), which sets high-quality standards for retread tyres. This national standard ensures that domestically produced retreads meet rigorous safety and quality requirements, reinforcing consumer confidence and helping local manufacturers maintain global competitiveness. By promoting this certification and its benefits, Malaysia can further build trust in its retreading industry and drive domestic demand for high-quality retreads.
He also noted that partnerships with universities, research institutions and organisations such as the Malaysian Rubber Board (MRB) could play a pivotal role in establishing Malaysia as a hub for innovation in tyre retreading. These collaborations would enable research and development focused on improving the quality, safety and efficiency of retread tyre, which could enhance their appeal domestically and internationally.
“The Malaysian Rubber Board has extensive expertise in rubber technology and the development of new rubber compounds, which are crucial for retreading. By working with these organisations, Malaysia could explore advanced rubber materials and improve the durability and performance of retread tyres. MRB’s research could focus on optimising the rubber used in tyre retreading, enhancing its resilience and performance under various road conditions, thus improving the overall safety of retreads. Universities and research institutions bring additional expertise in materials science, engineering and sustainability and can help address any technical gaps in the retreading process. They could collaborate with retreading companies, fleet operators and tyre manufacturers to develop new retreading technologies, better tyre monitoring systems and more efficient processes,” explained Wong.
He added, “These partnerships could also produce credible, science-backed data on the reliability and safety of retread tyre, helping to build public trust and dispel misconceptions about retreads.”
FILLING DATA GAPS
The lack of local data to validate the reliability and safety of both retread and new tyres in Malaysia stems from several key factors, according to Wong.
“Primarily, there is a significant gap in research due to the lack of collaboration between tyre manufacturers, retreaders, fleet operators, research institutions and government agencies. Without cooperation among these stakeholders, there is little incentive or infrastructure to collect and analyse tyre failure data in the local context. This leads to a situation where tyre failure research is outdated or non-existent, leaving the industry to rely on studies from other countries such as US, which may be many years old and not reflective of current tyre technology or local conditions,” noted Wong.
He added, “This problem is not unique to Malaysia; many countries face similar challenges in gathering and sharing tyre-related data. For example, tyre debris reports and studies on tyre failures tend to be infrequent and may not accurately capture the complexities of modern tyre usage, road conditions or fleet operations. To address this gap, a collaborative effort among different stakeholders, both local and international, could be instrumental.”
Collaborations could fund and conduct comprehensive studies on tyres performance under local conditions. By sharing data and expertise, these stakeholders can develop a more accurate understanding of the causes of tyre failures, improve maintenance practices and promote better safety standards for both new and retread tyres.
Additionally, international partnerships could allow for access to global tyre failure databases and new research, enabling Malaysia to adopt best practices from countries like US, Japan or the EU, where more tyre safety research is available.
Establishing a framework for ongoing research and data sharing with regular updates and reports would help fill the data gap and improve tyre safety standards locally. This collaborative approach could ultimately lead to the development of localised tyre safety standards, improved regulations and more informed decision-making by all stakeholders involved.
NEW LEARNING
According to Wong, Malaysia can learn important lessons from countries like Japan and UK, where retread tyres are promoted effectively for their cost-efficiency and environmental benefits. Both Japan and the UK have robust local manufacturing industries for new, high-quality tyres, which ensure a consistent supply of durable tyre casings for retreading.
This industrial advantage helps protect the respective retreading industries by ensuring the availability of reliable casings that meet safety and performance requirements. Japan enforces stringent standards for both new and retread tyres through the Japanese Industrial Standards (JIS) such as JIS D 4202, which defines specifications for automobile tyres. These regulations ensure high-quality tyre production and maintenance, supporting a thriving retreading ecosystem.
Similarly, UK relies on the ‘E’ mark certification system, which aligns with European safety and performance regulations. The ‘E’ mark, prominently displayed on compliant tyres, indicates that a tyre has undergone rigorous testing and meets safety standards. This harmonised approach in UK ensures that only certified-quality tyres are used, reducing risks and building trust in retread tyres.
In Malaysia, the absence of a local new tyre manufacturing industry for trucks presents a challenge. The reliance on imported new tyres, coupled with the fact that Malaysia’s new tyre standard (MS 1394) is not compulsory, allows low-cost and lower-quality imports to flood the market.
These tyres often produce casings unsuitable for retreading, which undermines the retreading industry. To address these issues, Malaysia could make MS 1394 mandatory for new tyres, ensuring better-quality casings and fostering trust in retreads.
Additionally, promoting awareness of retreads’ economic and environmental benefits, strengthening enforcement of Malaysian Standard 224 (MS 224) for retread quality and offering incentives for their adoption could help the industry grow.
Technology, such as tyre monitoring systems, can play a significant role in addressing concerns about retread tyres and improving road safety. These systems provide real-time data on tyre pressure, temperature, tread depth and overall tyre health, helping to ensure that all tyres, including retreads, are properly maintained.
By monitoring tyre performance, these systems can detect early signs of wear, overloading or misapplication, reducing the risk of tyre failure. This not only enhances the safety of retread tyre but also helps prevent accidents caused by poor tyre maintenance or low-quality tyres, leading to a change in perception.
TÜV SÜD Appoints Ishan Palit As Interim CEO During Leadership Transition
- By TT News
- July 11, 2025
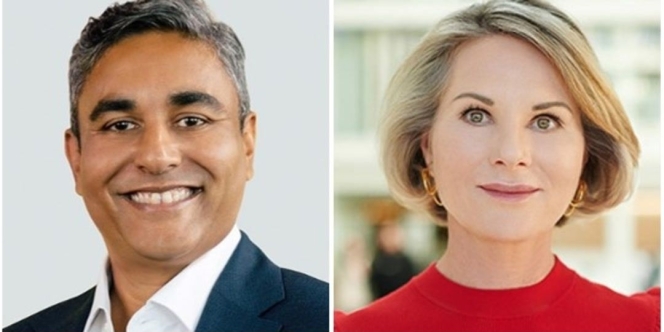
TÜV SÜD AG’s Supervisory Board has named Ishan Palit as Interim CEO (Chairman of the Board of Management) effective 15 July 2025, following Dr Johannes Bussmann’s departure to assume the CEO role at MTU Aero Engines AG. Bussmann will leave TÜV SÜD on 14 July 2025. Palit will co-lead the company with CFO Sabine Nitzsche until a permanent successor is appointed.
With over 30 years at TÜV SÜD, Palit has held key leadership roles, including establishing the company’s India operations, serving as Asia Pacific CEO and leading the global Product Service Division. Since 2017, he has been Chief Operating Officer, driving strategic and operational initiatives.
Nitzsche, who joined as CFO in March 2025, brings extensive financial and executive expertise from the high-tech and automotive sectors. Her prior roles include CFO of Vitesco Technologies AG and senior financial leadership positions at Infineon Technologies and GlobalFoundries.
Frank Hyldmar, Chairman of the Supervisory Board of TÜV SÜD AG, said, “We are very pleased that Ishan and Sabine will oversee the interim management of TÜV SÜD during this transition. Ishan is a seasoned TÜV SÜD senior executive with deep knowledge of our business and strong global leadership experience. Sabine brings a proven track record as CFO across multiple multinational enterprises. Together, they form a strong leadership team as we work towards appointing a long-term CEO.”
Hankook Tire Rejigs North American Sales And Marketing Team
- By TT News
- July 09, 2025
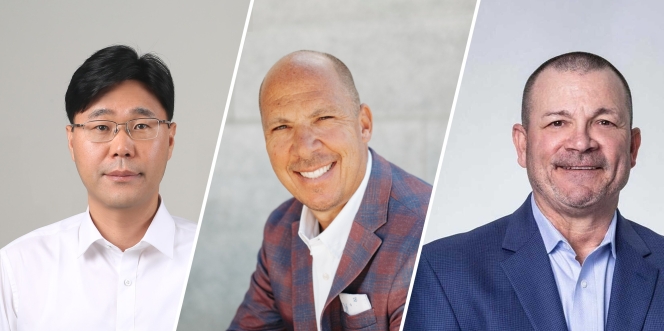
Hankook Tire & Technology has announced a series of executive leadership changes at its North American headquarters in Nashville, reinforcing its commitment to growth in passenger and commercial tyre markets. The restructuring brings fresh leadership across key sales and marketing functions.
Kyuwang (Ken) Cho assumes the role of Senior Vice President of North America Marketing, transitioning from his previous dual leadership of PC/LT Sales and Marketing. The industry veteran brings 25 years of Hankook experience, including a stint as Vice President of Global Sales in Korea. K C Jensen steps up as Vice President of US PC/LT Sales, expanding his responsibilities from regional to national oversight after demonstrating strong leadership in the Western market since 2018.
The company welcomes back Mark Roe as Vice President of US TBR Sales, where his four decades of commercial tyre expertise will guide replacement and OE sales strategies. Roe's extensive background includes previous leadership roles at Hankook and most recently at Ralson Tire North America.
Regional sales teams also see strategic promotions. Shaun Prott advances to Regional Director of PC/LT Sales for the West, building on his eight-year tenure with Hankook and prior experience with National Tire Warehouse. Travis Jones rejoins the organisation as Northeast Regional Director, bringing valuable perspective from Michelin and Pirelli. Brian Ford earns promotion to Regional Director of TBR Sales for the West after successfully managing key commercial accounts since 2021.
Rob Williams, President of Hankook Tire America Corp, said, "These leadership appointments reflect Hankook's strong momentum in North America. Ken, K.C. and Mark each bring exceptional industry experience, strategic focus and leadership qualities to their roles. Together, they will help elevate our presence across both consumer and commercial channels, and support our long-term growth ambitions in the US. These moves speak to the strength of our internal talent pipeline & ability to attract top talent and our continued investment in customer relationships. Shaun, Travis and Brian all bring deep knowledge of their markets and proven ability to grow key partnerships."
Michelin X Line Grip D Tyre Promises Range Of Upto 1 Million Miles & Upto 4 Retreads
- By TT News
- July 08, 2025
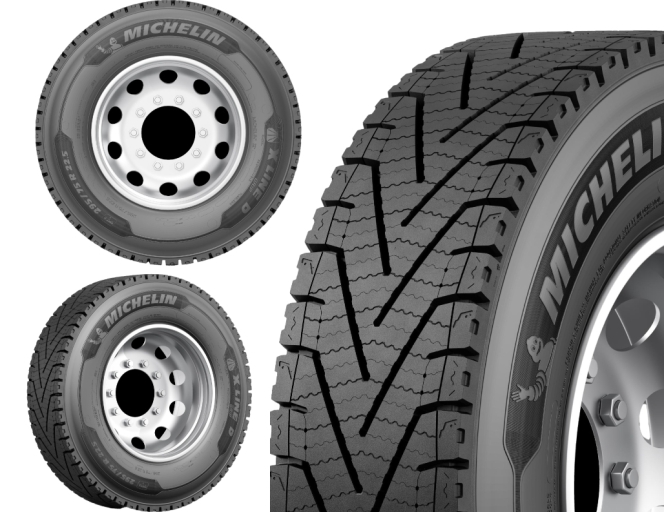
French tyre major Michelin has introduced its new X Line Grip D range, which is designed to work up to 1 million miles (1.6 million kilometres) with up to four retreads. The company shared its designers' claim that this is a ‘once-in-a-lifetime’ leap in tyre technology for fleets.
In addition to the higher range, the tyres also provide 20 percent more mileage and a 20 percent reduction in rolling resistance compared to the Michelin XDN2 tyre.
Designed to meet both wet and snowy conditions thanks to the chevron tread design, these tyres are said to prove 90 percent better starting traction in snow and over 25 percent better wet starting traction.
Fleets also benefit from using the Michelin X Line Grip D tyre, as it is built on the company’s Duracore casing, featuring Infinicoil and Powercoil technologies.
Pierluigi Cumo, VP – B2B Marketing, Michelin North America, said, “Michelin is never satisfied with current tyre technology when it comes to constantly improving and innovating our products. That’s why Michelin is so proud to introduce the Michelin X Line Grip D tyre. This tyre has the potential going forward to redefine the drive tyre standard in fleets for years to come. It is not an evolution to existing products, but something entirely different the fleet world has never seen before.”
“Michelin has a proven track record of delivering high-quality, reliable products that exceed performance expectations. This fantastic leap in drive tyre technology bring new levels of performance to the road and new levels of savings to our customers,” he concluded.
The Michelin X Line Grip D tyre is available in sizes 295/75R22.5 and 11R22.5.
- Dr D Banerjee Centre of Excellence
- DBCOE
- Raghupati Singhania
- Dr Raghupati Singhania
- Mysore District Magistrate Lakshmikanth Reddy
- Dr R Mukhopadhyay
- V K Misra
- P K Mohamed
- JSS Mahavidyapeetha
Advancing Rubber Industry Deadlocks
- By Sharad Matade & Gaurav Nandi
- July 04, 2025
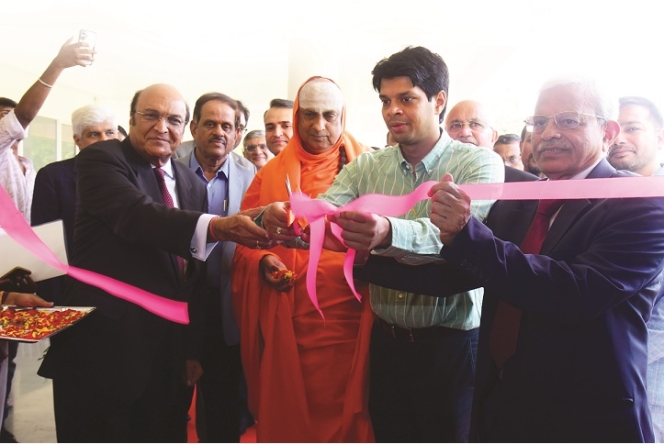
The launch of the Dr D Banerjee Centre of Excellence at JSS Technical Institutions marks a pivotal step towards transforming India’s rubber and tyre industry. By fostering collaboration between academia and industry, the centre aims to break longstanding deadlocks, equipping the workforce with advanced skills and driving innovation in polymer science and sustainable rubber technologies. With a focus on supporting MSMEs and addressing emerging challenges, especially those posed by electric vehicles and stricter regulations, the DBCOE seeks to become a national hub for research, training and certification, ultimately positioning India as a leader in the evolving global rubber sector.
The Indian Institute of Rubber (IRI) and JSS Technical Institutions inaugurated the Dr D Banerjee Centre of Excellence (DBCOE) recently at the Raghupati Singhania auditorium at JSS Technical Institutions’ Mysore campus.
The institute will serve as a proactive platform for academic and industrial collaboration for polymer science and rubber technology aiming to bridge different industrial deadlocks within the rubber industry.
The event was attended by JK Tyres and Industries CMD Dr Raghupati Singhania, Mysore District Magistrate Lakshmikanth Reddy (IAS), H.H. Jagadguru Sri Shivarathri Deshikendra Mahaswamiji, IRI Chairman Dr R Mukhopadhyay, IRI Vice Chairman V K Misra and industry veteran P K Mohamed, among others.
Setting the stage for the occasion, Mahaswamiji stated, “This is a remarkable coincidence that JSS Science and Technology is associating with Dr D Banerjee Centre of Excellence to usher in new vistas for innovation in rubber technology, where science meets technology for the benefit of society. The centre is dedicated to focusing on innovation, research and new product development and creating high-performance tyres, thereby contributing to sustainability efforts by developing eco-friendly tyre technologies.”
Drawing on the same lines, Misra went on to say, “This is a dream come true as the decision was taken to establish a Centre of Excellence at the occasion of IRCO RubberCon Conference held at Chennai in the year 2015. It gives all of us an immense sense of pride to be associated with the establishment of this Centre of Excellence. It will provide a unique platform to the rubber and allied industry for skill development, training, technology development etc. in the coming years.”
The centre honours the contribution of Dr Banerjee, a pioneering figure in Indian rubber and tyre technology. The initiative was supported by JSS Mahavidyapeetha, IRI and numerous industry leaders and technologists.
Dr Singhania was recognised at the event not only for his leadership in the tyre industry but also for his commitment to nation-building and youth empowerment.
“I am glad that the Indian Rubber Institute, in association with JSS Mahavidyapeetha and the larger Indian rubber fraternity, has set up this centre in memory of Dr Banerjee, the doyen and father of the Indian rubber industry. It is heartening to know that this Centre of Excellence has been established with a clear and noble vision. In fact, this initiative resonates deeply with our Prime Minister’s vision of a ‘Skilled India Mission’,” said Dr Singhania.
He added, “This centre has the potential to play a vital role in realising the vision within the rubber sector. I was delighted to tour the centre and see the comprehensive infrastructure and facilities put in place to fulfil these objectives. I am confident that this centre will soon earn the reputation and recognition it rightly deserves.”
A FULFILMENT CENTRE
According to Dr Singhania, in India’s rapid growth trajectory, institutions like this will play a crucial role in empowering youth with the skills needed to serve this vital sector. Vocational education is a key enabler of employability and plays a transformative role in facilitating a smooth transition of individuals into the industrial workforce.
“I am tempted to share our own experience with industry-academia partnership. We have been successfully running one at IIT Madras for the last 18 years. I believe this kind of close collaboration between industry and academia is something we have been missing in India, and it is indeed a critical step forward,” he stated.
India today stands at a unique juncture with a demographic advantage expected to last for the next 25–30 years. Equipping the population with the right skill sets – both technical and entrepreneurial – opens the opportunity to transform an advantage into a demographic dividend that drives economic growth not just within India but globally.
The employment landscape is evolving rapidly. Business models are being disrupted and new job roles are emerging at an unprecedented pace. The skills and job profiles that were relevant five years ago may no longer be sufficient today. This rapid change demands a dynamic skilling ecosystem – one that is agile, industry-responsive and inclusive.
To meet the future demands of the tyre and rubber industry, such as the increasing use of speciality polymers, advanced materials and the rising adoption of electric vehicles, a technically confident and highly trained workforce is needed.
“This Centre of Excellence can play a vital role not only as a hub for education and hands-on training but also as a platform for testing, research and technology development. Its contribution, particularly to MSMEs in the rubber and allied sectors, will be significant. This centre will evolve into a beacon for the rubber industry, not just in India but across the Asia-Pacific region,” said an optimistic Dr Singhania.
VETERAN’S TALK
Commenting on the occasion, former IRI Chairman P K Mohamed stated that after several years of earnest effort by the officials and members of the IRI, a world-class institute for rubber technology, education, research, testing and skill development has been established.
“Currently, industries recruit students directly from colleges after they complete their BTech degrees. These companies then invest one to two years in training them before assigning them to regular roles. This approach is both expensive and time-consuming. To address this, we propose the introduction of a preparatory course for students, developed jointly by industry and academic institutions, based on a mutually agreed syllabus. Experienced professionals from industry, raw material and equipment suppliers as well as research organisations could be invited to deliver these classes,” said Mohamed.
He added, “We are also in the process of working out an appropriate methodology for funding these programmes. This initiative will significantly benefit industries by enabling them to hire job-ready candidates directly, eliminating the need for extensive post-recruitment training.”
The industry veteran highlighted that forensic analysis of failed products remains a key challenge for small and medium enterprises. To address this, DBCOE has developed comprehensive analytical capabilities and plans to recruit a specialist for failure analysis. This facility will help industries identify root causes of failures and implement corrective actions to ensure continuity.
A material characterisation and wet chemistry lab has been set up to analyse raw materials such as carbon black, rubber chemicals, various rubbers, accelerators, antioxidants and process aids. In-house capability also exists to draft material specifications for future quality control. Plant audits and merit-based approvals can be arranged.
Plans are underway to offer short courses in collaboration with equipment manufacturers and suppliers. Topics will include mixing, extrusion, calendering, tyre building, compounding, engineering, moulding, retreading, footwear, belt technology and latex products. These courses will combine practical and theoretical content, including testing methods and failure analysis. Notably, discussions with HF Mixing Group on mixing technology are progressing well. Additionally, a recognition programme is being developed to honour individuals contributing to different segments.
DEFEATING DEADLOCKS
India’s automotive industry is undergoing a seismic shift, driven by the rapid adoption of electric vehicles and rising performance expectations. While tyres often dominate the conversation, rubber components account for up to 10 percent of the overall value in an automobile and its role is growing more critical than ever.
As vehicle design evolves, so do the demands on rubber parts in the wake of higher torque, lighter weight, reduced rolling resistance and near-silent operation as can be seen in case of EVs. For manufacturers, especially the MSMEs that make up much of the sector, these shifts present a formidable challenge. Existing designs and materials no longer suffice.
Speaking on the vision of the centre and how it will meet industry deadlocks, Dr Mukhopadhyay said, “The mission is fourfold viz-a-viz upskill the current workforce, offer technical support for regulatory compliance and homologation, enable technology advancement for MSMEs and drive sustainable material innovation in collaboration with raw material suppliers. This centre aims to be more than just an academic institution; it’s envisioned as an ecosystem that fuels India’s rubber sector with skilled talent and cutting-edge know-how.”
At the heart of the initiative lies a simple truth that knowledge alone is no longer enough. According to Dr Mukhopadhyay, India’s tyre and rubber sector needs a convergence of skill and science that demand a confluence of practical expertise and theoretical depth. With an eye on decarbonisation, the centre will also push research into bio-based alternatives for carbon black, synthetic rubber, tackifiers and processing oils. From tyre-to-tyre recycling to steel reuse and low-emission polymers, the effort reflects a broader ambition to modernise the industry not just for EV readiness but for long-term sustainability.
“In a market where regulatory demands are intensifying and global competitiveness is rising, this centre represents a strategic leap. It promises to future-proof India’s rubber industry by training the next generation, empowering MSMEs and leading the shift towards a cleaner, more resilient manufacturing base,” he said.
THE NON-TYRE SECTOR
The centre will primarily focus on the tyre industry but aims to support the wider rubber ecosystem, especially MSMEs producing non-tyre components. While large tyre firms have testing and certification infrastructure, smaller players often lack access to technology, skilled labour and analytical facilities. The centre will bridge this gap through hands-on training, consultancy and development support. It will act as a national hub for tyre technology, BIS certification and sustainability compliance while also helping non-tyre manufacturers enhance technical capabilities.
“This sort of institution has been both our dream and our vision. We’ve worked hard to bring it to life, and I’m heartened to see the industry now stepping up. Of course, execution and funding remain challenges. Nothing happens overnight, but I’m confident that with time and collective effort, we will overcome these hurdles. As a PhD holder in this field, I’ve witnessed the struggles students face, particularly during their research projects. Dealing with limited equipment, recruitment issues and maintenance challenges are plenty,” averred Dr Mukhopadhyay.
HURDLES IN THE WAY
Despite India’s robust tyre and rubber sector, a culture of collaboration remains elusive, especially among tyre companies, which have largely remained conservative and insular in their approach.
Industry veterans have long observed that companies prefer to operate in silos, wary that cooperation might breed competition.
According to Dr Mukhopadhyay, the initiative of collaboration has come in the form of grassroots movements like the Wisdom Club – an informal alliance led by senior industry professionals like himself and Mohamed – who have pooled their knowledge and experience to mentor the next generation and drive development where institutions have fallen short.
“Unlike government-backed Centres of Excellence, which number over 40 yet often lack focused activity, and with only one national body showing limited development momentum, these independent efforts fill a critical gap. Furthermore, there are no large grants, no access to state support and infrastructure must be built slowly, piece by piece – often through deferred payments and personal negotiations. We don’t have capital. Yet, against these odds, progress is being made often over decades.”
While attempts to find institutional partners in Chennai and other cities have met resistance or failed to materialise, the effort continues.
EDUCATIONAL PROWESS
Highlighting the nuances of the educational programmes offered by the centre, IRI Advisor S Vasudeva Rao mentioned, “The centre offers two flagship programmes, namely the Diploma in Rubber Technology for diploma holders and fresh recruits and the Postgraduate Diploma in Rubber Technology for science and engineering graduates. Both combine online theoretical modules (delivered on Sundays) with practical assignments and hands-on crash courses at the Mysuru campus. Final examinations are conducted and evaluated by IIT Kharagpur, lending strong academic credibility.”
Rao also noted that the new training powerhouse is an INR 280 million facility funded entirely through industry donations. It brings in over 40 industry experts to teach domain-specific topics ranging from tyre and conveyor technology to PU foams and latex composites. Curriculum is aligned with real-world applications and transparency is ensured via digital course materials and regular assessments.
The initiative has gained formal endorsement across the tyre industry. Companies like Apollo, Yokohama, BKT and JK Tyre now embed course completion as a pre-condition for employment confirmation, reimbursing 100 percent of the INR 40,000 course fee. While the centre is new, the course dates back to 1995 and over 1,200 professionals have graduated with average annual enrolment now exceeding 250.
The centre represents a rare model of successful industry-academia collaboration in India’s manufacturing sector, combining infrastructure, expertise and funding to systematically upskill the rubber workforce.
While the establishment of the DBCOE represents a significant milestone, the broader challenge lies in overcoming the entrenched conservatism and fragmented nature of India’s tyre and rubber industry.
Comments (0)
ADD COMMENT