- Tire Technology Expo 2025
- Tony Robinson
- Deutsche Messe
- Hannover
- Bekaert
- Rockwell Automation
- VMI Group
- HF Group
- ARP Technologies
- Synthos
- Nynas
- Schill+Seilacher “Struktol” GmbH
- Kordsa
- Black Donuts
- Continental
- Bridgestone
- Claire Fiioretti
- European Sustainability Product Regulation
- Rockwell Automation
- Adam McCarthy
- ETRMA
Global Tyre Industry Converges In Hannover For Technology Exhibition
- By TT News
- April 28, 2025
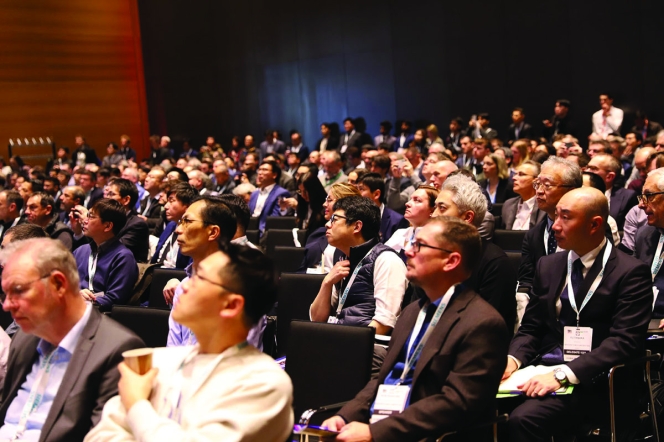
The global tyre industry’s top manufacturers and technology suppliers met at the Tire Technology Expo 2025 in Hannover on 4-6 March to unveil technologies focused on driving sustainability, digitalisation and road safety. At the Deutsche Messe, the exhibition featured advances in tyre engineering, materials science and manufacturing technologies that will define mobility in the future.
In opening the event, expo founder Tony Robinson called on manufacturers to close the knowledge gap with consumers, highlighting how most drivers undervalue the importance of tyres in ensuring a vehicle’s safety. He mentioned that safety rests on the four small ‘footprints’ of rubber linking a car to the road, which tends to be undervalued by the general driver.
Looking to the future, Robinson saw a day when tyres contain sensors that share real-time information with other cars and roadside infrastructure. These sensors could warn drivers of dangerous road conditions like flooding or new potholes, making roads safer and avoiding crashes. He predicted that information from tyres could also feed into weather forecasting services, providing useful real-time information on road conditions.
The exhibition floor showcased innovation and high-performance solutions from more than 240 exhibitors, with Bekaert, Rockwell Automation, VMI Group, HF Group, ARP Technologies, Synthos, Nynas, Schill+Seilacher “Struktol” GmbH, Kordsa, Black Donuts and others.
SUSTAINABILITY AND MATERIAL INNOVATION TAKE CENTRE STAGE
The expo also reflected the tyre industry’s growing focus on sustainability, with manufacturers launching new materials and processes to lower environmental impact. Bekaert launched its Mega Tensile reinforcement technology, a major innovation in its Elyta range. The technology enables tyre manufacturers to produce up to 20 percent less steel and 10 percent less rubber compound in belt plies, achieving a 2-4 percent drop in rolling resistance and a huge 15-20 percent reduction in CO₂ emissions per tyre.
Kordsa introduced its REV Technologies, which are specifically tailored to electric vehicle tyres. The company’s innovations include recycled PET (rPET) cord fabric and RFID tyre tags, enabling improved lifecycle monitoring and data collection. Kordsa expects to enhance sustainability and recycling practices by combining digital identification with tyre production.
Teijin Aramid featured its Twaron para-aramid reinforcement, a material that can manufacture lighter tyres with reduced rolling resistance and eventually lower emissions.
EV AND DIGITAL INNOVATION LEAD DISCUSSIONS
As the electric vehicle (EV) market grows, tyre makers focus on creating solutions specific to the special needs of EVs and autonomous vehicles. Continental Tires unveiled an overall sustainability strategy, emphasising the environmental impact of tyres throughout their life cycle. The firm detailed plans to incorporate more sustainable raw materials, minimise waste during production and enhance tyre durability.
Michelin’s Director of Standards and Regulations for Connected Mobility, Claire Fioretti, outlined the company’s efforts around Digital Product Passports (DPP), a major initiative within the (ESPR). The regulation, enacted in 2024, aims to increase supply chain transparency by mandating that products carry a permanent, readable identifier usable throughout their life cycle. Michelin is already testing the programme in various industries, such as textiles, electronics and automotive components, with the cooperation of French, German and Swedish stakeholders.
The ESPR system, Fioretti characterised as an ‘ambitious information system’, will enable the maker, the recycler and the buyer to make environmentally informed decisions. She stressed that the movement is not so much about compliance as a transition towards the principles of the circular economy. By 2027, by the time broad adoption of the ESPR sets in, product design may improve, recycling efficiency will be elevated and buyers’ confidence will be boosted in second-hand markets.
MANUFACTURING INNOVATION AND AI TECHNOLOGY
The event showcased the latest digital manufacturing solutions to enhance efficiency, lower waste and better quality control. Rockwell Automation launched AI-driven tools to optimise tyre production, including digital thread technologies for tracking data without interruption through various manufacturing processes.
Black Donuts launched its Digital Twin Tyre Plant Simulation, a cutting-edge real-time virtual modelling tool that aids manufacturers in minimising downtime and optimising production. The company’s methodology involves end-to-end finite element analysis, enabling accurate tyre performance simulations before production.
HF dominated the manufacturing technology market with its state-of-the-art electric tyre curing presses. The company illustrated how its new electric curing technology could be applied to new and retrofit installations to minimise energy consumption and enhance process efficiency. Fischer TireTech exhibited computerised cord-cutting lines and premium extrusion technologies aimed at increasing accuracy in tyre production.
Uzer Makina launched a high-end electric tyre curing press focused on energy efficiency and precision production. ARP Technologies showcased its Electromagnetic Heating (EMH) curing system, a more energy-efficient curing process, alongside an artificial intelligence-based inspection machine that can spot tiny defects with great accuracy.
KraussMaffei featured its multiplex extrusion technology, which enhances first-time production quality and eliminates material bleeding during tyre formation. The company showed a new head clamping technology that maximises channel cleaning effectiveness, further expanding the limits of green manufacturing.
REGULATORY DEVELOPMENTS AND ENVIRONMENTAL CONSIDERATIONS
Regulatory matters were on the agenda at the expo, with leading experts discussing the changing scene for tyre production and green compliance. Adam McCarthy, Secretary General of the European Tyre and Rubber Manufacturers’ Association (ETRMA), gave a definitive overview of recent European Commission regulatory interventions impacting the sector.
A specific session on Tyre and Road Wear Particles (TRWP) collaborated with industry experts from Bridgestone, Continental and Michelin, as well as leading research institutions, to address the implications of future Euro 7 regulations. It was centred around reducing tyre wear’s environmental footprint without compromising performance levels.
FUTURE OUTLOOK AND INDUSTRY COLLABORATION
During the three-day conference, experts worldwide exchanged information, delved into future technologies and worked on crafting the mobility of the future. The event highlighted reducing carbon footprint, improving safety and customising solutions for future electric and self-driving cars.
The next edition will be held on 3 and 4 March 2026.
TIRE TECHNOLOGY INTERNATIONAL AWARDS FOR INNOVATION AND EXCELLENCE
A key highlight of the event was the prestigious Tire Technology International Awards for Innovation and Excellence 2025. Recognising achievements across 12 categories, the awards celebrate the latest advancements in tyre technology, progress towards a more sustainable industry and the outstanding contributions of individuals driving innovation. This year’s winners are as follows:
Goodyear bagged Environmental Achievement of the Year – Tire Design for its ElectricDrive Sustainable- Material (EDS) tyre.
Continental was awarded the Environmental Achievement of the Year – Manufacturing award for its CO2-neutral tyre production at the Lousado plant in Portugal.
Nokian Tyres won the Environmental Achievement – Industry Contribution award for its inauguration of the world’s first full-scale tyre factory with zero CO2 emissions in Oradea, Romania.
Bekaert received the Materials Innovation of the Year award for its next-generation reinforcement solution, Mega Tensile.
Sumitomo Rubber Industries won the R&D Breakthrough of the Year award for its Active Tread technology.
VMI was awarded for Tire Manufacturing Innovation of the Year award for its integrated quality monitoring for the MAXX and MILEXX platforms.
ARP Technologies was selected as Industry Supplier of the Year for its many innovations in the tyre curing sector.
Bridgestone bagged Tire Concept of the Year for its Lunar concept tyre.
Michelin was awarded Tire of the Year for its Primacy 5 tyre.
Continental won the Tire Manufacturer of the Year award for the fourth time, acknowledging the scale and breadth of the company’s achievements over the last year.
Two further awards were also given for individual achievements in the industry:
Katerina Filzer, a PhD student at Twente University in the Netherlands, was awarded the 2025 Young Scientist Award for her presentation, ‘An Innovative Method to Incorporate a Devulcanization Aid into Rubber’.
Anke Blume, head of elastomer technology and engineering at the University of Twente, received the Lifetime Achievement Award for her outstanding contributions to the tyre industry.
TÜV SÜD Appoints Ishan Palit As Interim CEO During Leadership Transition
- By TT News
- July 11, 2025
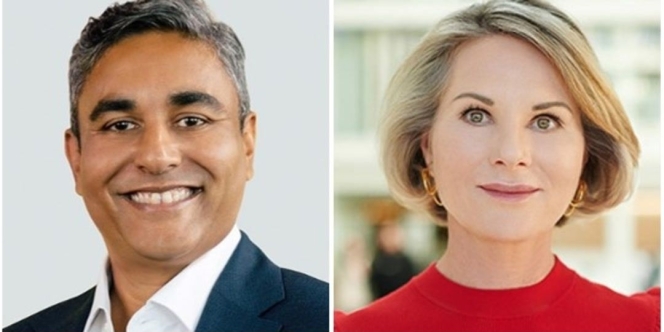
TÜV SÜD AG’s Supervisory Board has named Ishan Palit as Interim CEO (Chairman of the Board of Management) effective 15 July 2025, following Dr Johannes Bussmann’s departure to assume the CEO role at MTU Aero Engines AG. Bussmann will leave TÜV SÜD on 14 July 2025. Palit will co-lead the company with CFO Sabine Nitzsche until a permanent successor is appointed.
With over 30 years at TÜV SÜD, Palit has held key leadership roles, including establishing the company’s India operations, serving as Asia Pacific CEO and leading the global Product Service Division. Since 2017, he has been Chief Operating Officer, driving strategic and operational initiatives.
Nitzsche, who joined as CFO in March 2025, brings extensive financial and executive expertise from the high-tech and automotive sectors. Her prior roles include CFO of Vitesco Technologies AG and senior financial leadership positions at Infineon Technologies and GlobalFoundries.
Frank Hyldmar, Chairman of the Supervisory Board of TÜV SÜD AG, said, “We are very pleased that Ishan and Sabine will oversee the interim management of TÜV SÜD during this transition. Ishan is a seasoned TÜV SÜD senior executive with deep knowledge of our business and strong global leadership experience. Sabine brings a proven track record as CFO across multiple multinational enterprises. Together, they form a strong leadership team as we work towards appointing a long-term CEO.”
Hankook Tire Rejigs North American Sales And Marketing Team
- By TT News
- July 09, 2025
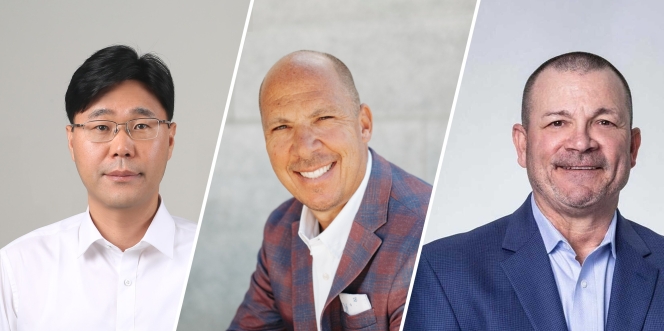
Hankook Tire & Technology has announced a series of executive leadership changes at its North American headquarters in Nashville, reinforcing its commitment to growth in passenger and commercial tyre markets. The restructuring brings fresh leadership across key sales and marketing functions.
Kyuwang (Ken) Cho assumes the role of Senior Vice President of North America Marketing, transitioning from his previous dual leadership of PC/LT Sales and Marketing. The industry veteran brings 25 years of Hankook experience, including a stint as Vice President of Global Sales in Korea. K C Jensen steps up as Vice President of US PC/LT Sales, expanding his responsibilities from regional to national oversight after demonstrating strong leadership in the Western market since 2018.
The company welcomes back Mark Roe as Vice President of US TBR Sales, where his four decades of commercial tyre expertise will guide replacement and OE sales strategies. Roe's extensive background includes previous leadership roles at Hankook and most recently at Ralson Tire North America.
Regional sales teams also see strategic promotions. Shaun Prott advances to Regional Director of PC/LT Sales for the West, building on his eight-year tenure with Hankook and prior experience with National Tire Warehouse. Travis Jones rejoins the organisation as Northeast Regional Director, bringing valuable perspective from Michelin and Pirelli. Brian Ford earns promotion to Regional Director of TBR Sales for the West after successfully managing key commercial accounts since 2021.
Rob Williams, President of Hankook Tire America Corp, said, "These leadership appointments reflect Hankook's strong momentum in North America. Ken, K.C. and Mark each bring exceptional industry experience, strategic focus and leadership qualities to their roles. Together, they will help elevate our presence across both consumer and commercial channels, and support our long-term growth ambitions in the US. These moves speak to the strength of our internal talent pipeline & ability to attract top talent and our continued investment in customer relationships. Shaun, Travis and Brian all bring deep knowledge of their markets and proven ability to grow key partnerships."
Michelin X Line Grip D Tyre Promises Range Of Upto 1 Million Miles & Upto 4 Retreads
- By TT News
- July 08, 2025
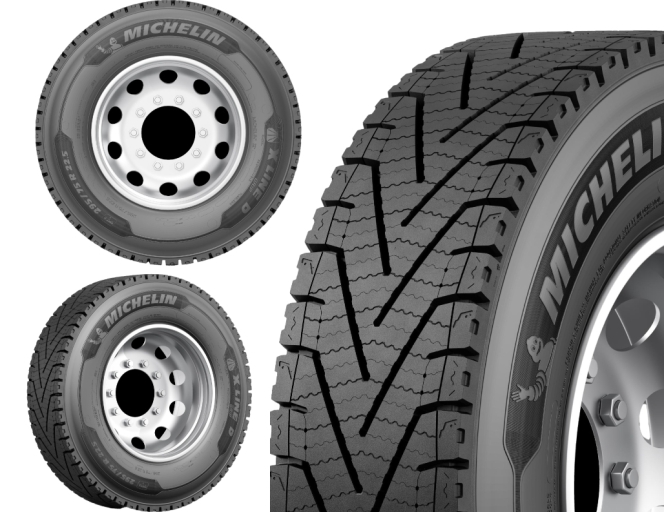
French tyre major Michelin has introduced its new X Line Grip D range, which is designed to work up to 1 million miles (1.6 million kilometres) with up to four retreads. The company shared its designers' claim that this is a ‘once-in-a-lifetime’ leap in tyre technology for fleets.
In addition to the higher range, the tyres also provide 20 percent more mileage and a 20 percent reduction in rolling resistance compared to the Michelin XDN2 tyre.
Designed to meet both wet and snowy conditions thanks to the chevron tread design, these tyres are said to prove 90 percent better starting traction in snow and over 25 percent better wet starting traction.
Fleets also benefit from using the Michelin X Line Grip D tyre, as it is built on the company’s Duracore casing, featuring Infinicoil and Powercoil technologies.
Pierluigi Cumo, VP – B2B Marketing, Michelin North America, said, “Michelin is never satisfied with current tyre technology when it comes to constantly improving and innovating our products. That’s why Michelin is so proud to introduce the Michelin X Line Grip D tyre. This tyre has the potential going forward to redefine the drive tyre standard in fleets for years to come. It is not an evolution to existing products, but something entirely different the fleet world has never seen before.”
“Michelin has a proven track record of delivering high-quality, reliable products that exceed performance expectations. This fantastic leap in drive tyre technology bring new levels of performance to the road and new levels of savings to our customers,” he concluded.
The Michelin X Line Grip D tyre is available in sizes 295/75R22.5 and 11R22.5.
- Dr D Banerjee Centre of Excellence
- DBCOE
- Raghupati Singhania
- Dr Raghupati Singhania
- Mysore District Magistrate Lakshmikanth Reddy
- Dr R Mukhopadhyay
- V K Misra
- P K Mohamed
- JSS Mahavidyapeetha
Advancing Rubber Industry Deadlocks
- By Sharad Matade & Gaurav Nandi
- July 04, 2025
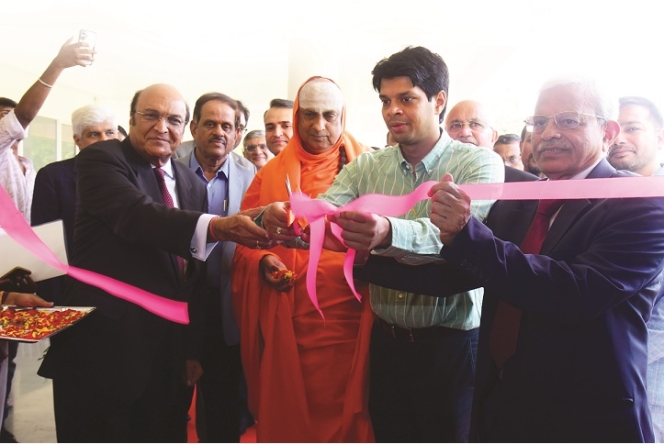
The launch of the Dr D Banerjee Centre of Excellence at JSS Technical Institutions marks a pivotal step towards transforming India’s rubber and tyre industry. By fostering collaboration between academia and industry, the centre aims to break longstanding deadlocks, equipping the workforce with advanced skills and driving innovation in polymer science and sustainable rubber technologies. With a focus on supporting MSMEs and addressing emerging challenges, especially those posed by electric vehicles and stricter regulations, the DBCOE seeks to become a national hub for research, training and certification, ultimately positioning India as a leader in the evolving global rubber sector.
The Indian Institute of Rubber (IRI) and JSS Technical Institutions inaugurated the Dr D Banerjee Centre of Excellence (DBCOE) recently at the Raghupati Singhania auditorium at JSS Technical Institutions’ Mysore campus.
The institute will serve as a proactive platform for academic and industrial collaboration for polymer science and rubber technology aiming to bridge different industrial deadlocks within the rubber industry.
The event was attended by JK Tyres and Industries CMD Dr Raghupati Singhania, Mysore District Magistrate Lakshmikanth Reddy (IAS), H.H. Jagadguru Sri Shivarathri Deshikendra Mahaswamiji, IRI Chairman Dr R Mukhopadhyay, IRI Vice Chairman V K Misra and industry veteran P K Mohamed, among others.
Setting the stage for the occasion, Mahaswamiji stated, “This is a remarkable coincidence that JSS Science and Technology is associating with Dr D Banerjee Centre of Excellence to usher in new vistas for innovation in rubber technology, where science meets technology for the benefit of society. The centre is dedicated to focusing on innovation, research and new product development and creating high-performance tyres, thereby contributing to sustainability efforts by developing eco-friendly tyre technologies.”
Drawing on the same lines, Misra went on to say, “This is a dream come true as the decision was taken to establish a Centre of Excellence at the occasion of IRCO RubberCon Conference held at Chennai in the year 2015. It gives all of us an immense sense of pride to be associated with the establishment of this Centre of Excellence. It will provide a unique platform to the rubber and allied industry for skill development, training, technology development etc. in the coming years.”
The centre honours the contribution of Dr Banerjee, a pioneering figure in Indian rubber and tyre technology. The initiative was supported by JSS Mahavidyapeetha, IRI and numerous industry leaders and technologists.
Dr Singhania was recognised at the event not only for his leadership in the tyre industry but also for his commitment to nation-building and youth empowerment.
“I am glad that the Indian Rubber Institute, in association with JSS Mahavidyapeetha and the larger Indian rubber fraternity, has set up this centre in memory of Dr Banerjee, the doyen and father of the Indian rubber industry. It is heartening to know that this Centre of Excellence has been established with a clear and noble vision. In fact, this initiative resonates deeply with our Prime Minister’s vision of a ‘Skilled India Mission’,” said Dr Singhania.
He added, “This centre has the potential to play a vital role in realising the vision within the rubber sector. I was delighted to tour the centre and see the comprehensive infrastructure and facilities put in place to fulfil these objectives. I am confident that this centre will soon earn the reputation and recognition it rightly deserves.”
A FULFILMENT CENTRE
According to Dr Singhania, in India’s rapid growth trajectory, institutions like this will play a crucial role in empowering youth with the skills needed to serve this vital sector. Vocational education is a key enabler of employability and plays a transformative role in facilitating a smooth transition of individuals into the industrial workforce.
“I am tempted to share our own experience with industry-academia partnership. We have been successfully running one at IIT Madras for the last 18 years. I believe this kind of close collaboration between industry and academia is something we have been missing in India, and it is indeed a critical step forward,” he stated.
India today stands at a unique juncture with a demographic advantage expected to last for the next 25–30 years. Equipping the population with the right skill sets – both technical and entrepreneurial – opens the opportunity to transform an advantage into a demographic dividend that drives economic growth not just within India but globally.
The employment landscape is evolving rapidly. Business models are being disrupted and new job roles are emerging at an unprecedented pace. The skills and job profiles that were relevant five years ago may no longer be sufficient today. This rapid change demands a dynamic skilling ecosystem – one that is agile, industry-responsive and inclusive.
To meet the future demands of the tyre and rubber industry, such as the increasing use of speciality polymers, advanced materials and the rising adoption of electric vehicles, a technically confident and highly trained workforce is needed.
“This Centre of Excellence can play a vital role not only as a hub for education and hands-on training but also as a platform for testing, research and technology development. Its contribution, particularly to MSMEs in the rubber and allied sectors, will be significant. This centre will evolve into a beacon for the rubber industry, not just in India but across the Asia-Pacific region,” said an optimistic Dr Singhania.
VETERAN’S TALK
Commenting on the occasion, former IRI Chairman P K Mohamed stated that after several years of earnest effort by the officials and members of the IRI, a world-class institute for rubber technology, education, research, testing and skill development has been established.
“Currently, industries recruit students directly from colleges after they complete their BTech degrees. These companies then invest one to two years in training them before assigning them to regular roles. This approach is both expensive and time-consuming. To address this, we propose the introduction of a preparatory course for students, developed jointly by industry and academic institutions, based on a mutually agreed syllabus. Experienced professionals from industry, raw material and equipment suppliers as well as research organisations could be invited to deliver these classes,” said Mohamed.
He added, “We are also in the process of working out an appropriate methodology for funding these programmes. This initiative will significantly benefit industries by enabling them to hire job-ready candidates directly, eliminating the need for extensive post-recruitment training.”
The industry veteran highlighted that forensic analysis of failed products remains a key challenge for small and medium enterprises. To address this, DBCOE has developed comprehensive analytical capabilities and plans to recruit a specialist for failure analysis. This facility will help industries identify root causes of failures and implement corrective actions to ensure continuity.
A material characterisation and wet chemistry lab has been set up to analyse raw materials such as carbon black, rubber chemicals, various rubbers, accelerators, antioxidants and process aids. In-house capability also exists to draft material specifications for future quality control. Plant audits and merit-based approvals can be arranged.
Plans are underway to offer short courses in collaboration with equipment manufacturers and suppliers. Topics will include mixing, extrusion, calendering, tyre building, compounding, engineering, moulding, retreading, footwear, belt technology and latex products. These courses will combine practical and theoretical content, including testing methods and failure analysis. Notably, discussions with HF Mixing Group on mixing technology are progressing well. Additionally, a recognition programme is being developed to honour individuals contributing to different segments.
DEFEATING DEADLOCKS
India’s automotive industry is undergoing a seismic shift, driven by the rapid adoption of electric vehicles and rising performance expectations. While tyres often dominate the conversation, rubber components account for up to 10 percent of the overall value in an automobile and its role is growing more critical than ever.
As vehicle design evolves, so do the demands on rubber parts in the wake of higher torque, lighter weight, reduced rolling resistance and near-silent operation as can be seen in case of EVs. For manufacturers, especially the MSMEs that make up much of the sector, these shifts present a formidable challenge. Existing designs and materials no longer suffice.
Speaking on the vision of the centre and how it will meet industry deadlocks, Dr Mukhopadhyay said, “The mission is fourfold viz-a-viz upskill the current workforce, offer technical support for regulatory compliance and homologation, enable technology advancement for MSMEs and drive sustainable material innovation in collaboration with raw material suppliers. This centre aims to be more than just an academic institution; it’s envisioned as an ecosystem that fuels India’s rubber sector with skilled talent and cutting-edge know-how.”
At the heart of the initiative lies a simple truth that knowledge alone is no longer enough. According to Dr Mukhopadhyay, India’s tyre and rubber sector needs a convergence of skill and science that demand a confluence of practical expertise and theoretical depth. With an eye on decarbonisation, the centre will also push research into bio-based alternatives for carbon black, synthetic rubber, tackifiers and processing oils. From tyre-to-tyre recycling to steel reuse and low-emission polymers, the effort reflects a broader ambition to modernise the industry not just for EV readiness but for long-term sustainability.
“In a market where regulatory demands are intensifying and global competitiveness is rising, this centre represents a strategic leap. It promises to future-proof India’s rubber industry by training the next generation, empowering MSMEs and leading the shift towards a cleaner, more resilient manufacturing base,” he said.
THE NON-TYRE SECTOR
The centre will primarily focus on the tyre industry but aims to support the wider rubber ecosystem, especially MSMEs producing non-tyre components. While large tyre firms have testing and certification infrastructure, smaller players often lack access to technology, skilled labour and analytical facilities. The centre will bridge this gap through hands-on training, consultancy and development support. It will act as a national hub for tyre technology, BIS certification and sustainability compliance while also helping non-tyre manufacturers enhance technical capabilities.
“This sort of institution has been both our dream and our vision. We’ve worked hard to bring it to life, and I’m heartened to see the industry now stepping up. Of course, execution and funding remain challenges. Nothing happens overnight, but I’m confident that with time and collective effort, we will overcome these hurdles. As a PhD holder in this field, I’ve witnessed the struggles students face, particularly during their research projects. Dealing with limited equipment, recruitment issues and maintenance challenges are plenty,” averred Dr Mukhopadhyay.
HURDLES IN THE WAY
Despite India’s robust tyre and rubber sector, a culture of collaboration remains elusive, especially among tyre companies, which have largely remained conservative and insular in their approach.
Industry veterans have long observed that companies prefer to operate in silos, wary that cooperation might breed competition.
According to Dr Mukhopadhyay, the initiative of collaboration has come in the form of grassroots movements like the Wisdom Club – an informal alliance led by senior industry professionals like himself and Mohamed – who have pooled their knowledge and experience to mentor the next generation and drive development where institutions have fallen short.
“Unlike government-backed Centres of Excellence, which number over 40 yet often lack focused activity, and with only one national body showing limited development momentum, these independent efforts fill a critical gap. Furthermore, there are no large grants, no access to state support and infrastructure must be built slowly, piece by piece – often through deferred payments and personal negotiations. We don’t have capital. Yet, against these odds, progress is being made often over decades.”
While attempts to find institutional partners in Chennai and other cities have met resistance or failed to materialise, the effort continues.
EDUCATIONAL PROWESS
Highlighting the nuances of the educational programmes offered by the centre, IRI Advisor S Vasudeva Rao mentioned, “The centre offers two flagship programmes, namely the Diploma in Rubber Technology for diploma holders and fresh recruits and the Postgraduate Diploma in Rubber Technology for science and engineering graduates. Both combine online theoretical modules (delivered on Sundays) with practical assignments and hands-on crash courses at the Mysuru campus. Final examinations are conducted and evaluated by IIT Kharagpur, lending strong academic credibility.”
Rao also noted that the new training powerhouse is an INR 280 million facility funded entirely through industry donations. It brings in over 40 industry experts to teach domain-specific topics ranging from tyre and conveyor technology to PU foams and latex composites. Curriculum is aligned with real-world applications and transparency is ensured via digital course materials and regular assessments.
The initiative has gained formal endorsement across the tyre industry. Companies like Apollo, Yokohama, BKT and JK Tyre now embed course completion as a pre-condition for employment confirmation, reimbursing 100 percent of the INR 40,000 course fee. While the centre is new, the course dates back to 1995 and over 1,200 professionals have graduated with average annual enrolment now exceeding 250.
The centre represents a rare model of successful industry-academia collaboration in India’s manufacturing sector, combining infrastructure, expertise and funding to systematically upskill the rubber workforce.
While the establishment of the DBCOE represents a significant milestone, the broader challenge lies in overcoming the entrenched conservatism and fragmented nature of India’s tyre and rubber industry.
Comments (0)
ADD COMMENT