The 15th Asia Pacific Carbon Black Conference Concludes With Record-Breaking Attendance!
- By Gaurav Nandi
- December 03, 2024
The Asia Pacific Carbon Black Conference 2024 – Perspectives in Asia Pacific, one of the largest and most acknowledged global carbon black industry events, unfolded in Kolkata, India, marking a historic moment for the city. The 15th edition welcomed a record-breaking 252 delegates and featured compelling discussions on the future of the carbon black market, which is projected to reach USD 30.15 billion by 2029. Over three days, industry leaders explored key trends, sustainability efforts and technological innovations, underscoring the sector’s dynamic evolution and the growing importance of India in shaping its future.
The sprawling banquet of a renowned hotel in the City of Joy was attuned to the murmuring of delegates from across the globe when the speaker on the dais invited the International Advisory Committee Chairman Amit Choudhary to address the crowd. With utter excitement, the chairman ascended the stage and opened the 15th Asia Pacific Carbon Black Conference doors to the curious assembly. Over the next three days, the event featured – workshops, intriguing sessions and panel discussions on the global carbon black market, which is slated to reach USD 30.15 Billion by 2029, according to Mordor Intelligence.
From sessions on the latest trends within the space to the use of recovered carbon black and sustainability issues, the conference was a boiling cauldron of information, coupled with an exhibition spanning different makers and associated suppliers to the industry.
Speaking to Tyre Trends exclusively, Choudhary said, “Key takeaways from the conference were impactful for both participants and delegates, with a record-breaking 252 attendees from around the globe. The exhibition, featuring 36 stalls, marked the largest in the Asia-Pacific region in the event’s 31-year history. The conference kicked off with two workshops on day one, focusing on the technical aspects of carbon black and its applications across the tyre and other industries. About 70 attendees engaged in a robust discussion, addressing numerous technical queries from leading players in the carbon black industry, including Birla Carbon, Tokai Carbon, Himadri Speciality Chemical Ltd, Epsilon, PCBL, and so on.”
He added, “For the first time in its history, the conference featured panel discussions on different topics of the carbon black industry covering marketing, raw materials, application, technology and the future of carbon black, which fostered intense engagement from participants. These sessions provided valuable insights and sparked in-depth discussions, impacting all those who attended.”
Many companies attending the conference were not direct carbon black producers but played key roles in the carbon value chain, either as suppliers to the carbon black industry or as technological collaborators or customers. This diverse representation highlighted the industry’s interconnected nature, with attendees gaining exposure to the latest technologies and processes shaping the sector.
“The conference brought together a global audience, fostering collaboration and providing significant opportunities for local suppliers to engage with emerging technologies. Carbon black production in this region, particularly in India, is experiencing rapid growth.
Companies across the country, from Gujarat and Maharashtra in the west to the east and south, are expanding their operations to meet increasing demand. This growth presents ample opportunities for suppliers of essential equipment and consumables to the carbon black industry, such as refractory manufacturers, bag suppliers and packing material providers. Ultimately, the entire supply chain stands to benefit from the increased collaboration and knowledge exchange fostered at the conference,” averred Choudhary.
Quick view
George Haines, Global Product Director and Avijit Sasmal, Chief Sustainability Officer at Himadri Speciality Chemical Limited, highlighted the carbon black industry’s progress in sustainability and circularity. They emphasised advancements such as the use of recycled pyrolysis oil and reclaimed carbon black and achievements like EcoVadis and ISCC+ certifications. Himadri already achieved the milestones and is maintaining Zero Liquid Discharge (ZLD) across plants. Innovations like LFP Cathode Active Material for EV batteries and renewable energy showcased Himadri’s future readiness. This session set a benchmark for aligning industry practices with global climate goals.
Senior Manager - Technology, K. Arun Kumar, and Manager, Technology and Business Development, Dr. P.M. Sivaram, at CUMI Super Refractories, discussed enhancing reactor life in the carbon black industry through condition monitoring and refractory solutions. They emphasised the need for failure analysis, material characterisation, and data-driven strategies to predict failures, improve productivity, and reduce downtime, ultimately leading to more efficient and sustainable operations in the industry.
The workshop by Himadri Speciality Chemicals Limited Plant Head Kingshuk Bose, on ‘Recent Advancements in Carbon Black Technologies’ provided an overview of carbon black, its applications, and recent technological innovations in its manufacturing processes. He discussed new technologies such as plasma and nanotechnology, which enhance production efficiency and product characteristics. Additionally, AI and machine learning were highlighted to optimise processes, improve quality and predict maintenance needs, ultimately advancing carbon black manufacturing and packaging strategies.
The former Chief Advisor of Research and Development at Apollo Tyres, P K Mohamed, an industry stalwart, addressed the future of the tyre industry, focusing on advancements in carbon black technology in his key note address. He noted that pneumatic tyres, essential for load support, require optimal structures to endure operational pressures. The industry faced megatrends such as mobility, digitisation, electrification, and the shift toward renewable materials. Key customer expectations centre on rolling resistance, traction, durability, and sustainability improvements. Enhancements in carbon black properties, including particle size and surface chemistry, are vital for achieving these goals. The industry’s evolution towards higher sigma levels indicated a commitment to quality and performance, necessitating collaborative efforts in research and development to meet future demands.
Notch Consulting Inc. Founder and President Paul Ita spoke on the outlook for 2024 and highlighted significant developments in the global carbon black and tyre industries. He noted a projected total investment of INR 27.3 billion in new tyre capacity from 2023 to 2028, with Asia, especially China and India, leading in new projects. He also discussed the impacts of EU sanctions on Russian carbon black imports. These sanctions are shifting trade flows, with India emerging as a key supplier to replace Russian volumes. The analysis included production capacity and utilisation trends with a forecast for growth in carbon black production despite current disruptions.
The AGM Strategy at Epsilon Carbon, Sagar Mathur, noted that geopolitical shifts, rapid urbanisation, climate change, sustainability, and technological advancements are shaping the future of the carbon black industry. Key trends included the growing demand for Electric Vehicle (EV) tyres, increased focus on circularity and recycling technologies, and the need for advanced speciality products. He highlighted that urbanisation is expected to strain resources while geopolitical conflicts are reshaping supply chains. The industry must adapt to these changes while addressing environmental concerns, leading to new product development, particularly in sustainable materials.
Vice President of Sales and Marketing (CBD), Kane Hanneke and Vice President of Business Development and Sales (CBD), Surge Klunder, at Himadri Specialty Chemical Ltd, focused on the current demand and supply dynamics of carbon black in North America and the European Union as of October 2024. In their presentations, they highlighted key economic indicators such as GDP growth, inflation, and the Manufacturing Purchasing Managers’ Index (PMI), while discussing challenges faced by domestic producers, including import duties, geopolitical tensions, and rising oil costs. Kane also mentioned a notable production increase among leading carbon black producers, particularly in China and India, and addressed the impact of new tariffs on Mexican imports.
Executive Vice-President and Regional Head of Sales and Marketing at Birla Carbon, Shashank Awasthi, discussed the dynamics of the carbon black market in Asia and Europe with a focus on growth plans and regional capacities. He highlighted that China dominates the market with a capacity share of 47 percent and a demand share of 37 percent. He also covered competition in India, where local producers faced challenges from imports, particularly from China, Korea, and Russia. His analysis indicated a projected CAGR of 5 percent for the Southeast Asia carbon black market from 2022 to 2027, driven by rising disposable incomes. It increased automotive production, with Asia accounting for approximately 60 percent of global automobile manufacturing.
The presentation by Zircoa Managing Director Thomas Bohm focused on the role of zirconia refractories in enhancing reactor performance during carbon black production. Zirconia, a unique ceramic material, offers exceptional properties such as high thermal resistance, lower thermal conductivity, and erosion resistance, making it suitable for high-temperature applications in reactors. The advantages of zirconia include increased reactor efficiency, improved product yields, and the ability to withstand aggressive process gases. However, challenges such as degradation from thermal shock and alkali attacks were noted, emphasising the importance of proper alignment and operational practices to maximise the lifespan of zirconia linings.
In his virtual keynote session, Zhu Zilong, deputy director of design at Doright, discussed the emerging supply trends in equipment manufacturing, particularly focusing on the shift from individual equipment supply to comprehensive equipment packages.
The landmark event saw the attendance of dignitaries and industry stalwarts, including the Chief Secretary to the Government of West Bengal, Dr Manoj Pant, Himadri Speciality Managing Director Anurag Choudhary, Tokai Carbon President Hagime Hagasaka, Group Country Head, Aditya Birla Group Thailand, and Chief Expansion Officer Birla Carbon Asia, Sanjeev Sood, among others.
Key Speakers included Aditya Birla Group’s Chief Sustainability Officer Deeksha Vats, Former President at ALSTOM Power Energy Recovery CP Natarajan, Vidhitech Solutions Founder Vinod Taneja, ABG Trading President John Kennelly, Senior Manager Research and Development of Compound Development at CEAT Limited Dr Pranab Dey, Head - Projects Business at Thermax Limited Naveen Sadhu and Rathi Group Director Ravi Rathi among others.
The event was attended by delegates from leading carbon black producers, such as Thai Tokai Carbon Product Company Limited, Hyundai OCI, Aegean First Company, Zircoa Inc., Phillips Carbon Black Limited, CITGO Corp and others.
Curtain Call
Amit Choudhary commented about the conference, “Conferences like this serve as crucial platforms for advancing technological progress in the industry. They provide insights into global trends, revealing which players are exploring new technologies and how different governments are approaching industry expectations. These events create an opportunity for stakeholders to understand evolving needs as well as the requirements of end customers.”
He added, “For instance, during our recent conference, several customers presented compelling insights, with both in-person and online interactions offering a deeper understanding of the tyre industry’s future. The rise of EVs is a key development demanding a shift in tyre technology and manufacturing processes. Current tyres are general-purpose, but as EV adoption accelerates, specialised tyres will become necessary. In the near future, we will see the emergence of EV-specific tyres alongside innovations in related non-tyre markets.”
He also noted that India, with its significant market share, is poised for substantial growth. Established markets in the US and Europe are facing challenges with plant closures and shifting demands. The ongoing geopolitical landscape, including tensions in China and Russia, is influencing market dynamics. However, India remains in a favourable position for investment and is set to experience impressive growth in the sector.
Looking ahead, the next conference is set to take place in 2026.
Nexen Tire Bags Gold Rating From EcoVadis For 2nd Consecutive Year
- By TT News
- July 15, 2025
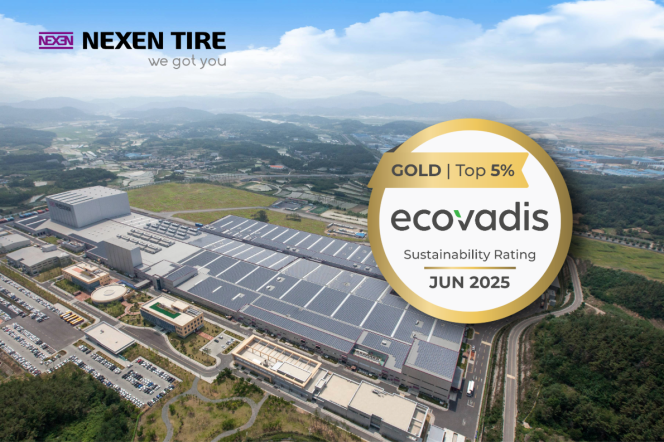
South Korean tyre major Nexen Tire has added another feather to its cap and has received a Gold rating from EcoVadis for the second year in succession. This places the company among the top 3 percent of over 150,000 companies assessed globally.
Established in 2007 in France, EcoVadis evaluates corporate sustainability performance across Environment, Labour & Human Rights, Ethics and Sustainable Procurement. Its ratings are Platinum (top 1 percent), Gold (top 5 percent), Silver (top 15 percent) and Bronze (top 35 percent).
Nexen Tire showed improvements across all assessment areas. In the Environment category, the company's involvement in global sustainability initiatives, including the Global Platform for Sustainable Natural Rubber (GPSNR), the UN Global Compact (UNGC) and the Science Based Targets initiative (SBTi) was noted. Climate education programmes and greenhouse gas emissions disclosure were contributors.
For Labour & Human Rights, Nexen Tire's human rights policy aligns with international standards from the United Nations and the International Labour Organization (ILO). The company also began human rights assessments for risk management.
In the Ethics pillar, the company reinforced internal systems for risk prevention, monitoring, and mitigation. The Sustainable Procurement score improved through ESG assessments, supplier audits and risk response strategies.
John Bosco (Hyeon Suk) Kim, CEO, Nexen Tire, said, “Receiving the Gold rating from EcoVadis for the second consecutive year is a significant affirmation of our global ESG efforts. We remain committed to responsible and transparent management practices that meet the expectations of our stakeholders worldwide.”
TÜV SÜD Appoints Ishan Palit As Interim CEO During Leadership Transition
- By TT News
- July 11, 2025
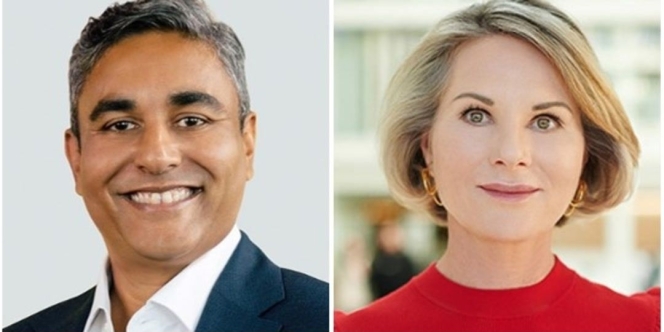
TÜV SÜD AG’s Supervisory Board has named Ishan Palit as Interim CEO (Chairman of the Board of Management) effective 15 July 2025, following Dr Johannes Bussmann’s departure to assume the CEO role at MTU Aero Engines AG. Bussmann will leave TÜV SÜD on 14 July 2025. Palit will co-lead the company with CFO Sabine Nitzsche until a permanent successor is appointed.
With over 30 years at TÜV SÜD, Palit has held key leadership roles, including establishing the company’s India operations, serving as Asia Pacific CEO and leading the global Product Service Division. Since 2017, he has been Chief Operating Officer, driving strategic and operational initiatives.
Nitzsche, who joined as CFO in March 2025, brings extensive financial and executive expertise from the high-tech and automotive sectors. Her prior roles include CFO of Vitesco Technologies AG and senior financial leadership positions at Infineon Technologies and GlobalFoundries.
Frank Hyldmar, Chairman of the Supervisory Board of TÜV SÜD AG, said, “We are very pleased that Ishan and Sabine will oversee the interim management of TÜV SÜD during this transition. Ishan is a seasoned TÜV SÜD senior executive with deep knowledge of our business and strong global leadership experience. Sabine brings a proven track record as CFO across multiple multinational enterprises. Together, they form a strong leadership team as we work towards appointing a long-term CEO.”
Hankook Tire Rejigs North American Sales And Marketing Team
- By TT News
- July 09, 2025
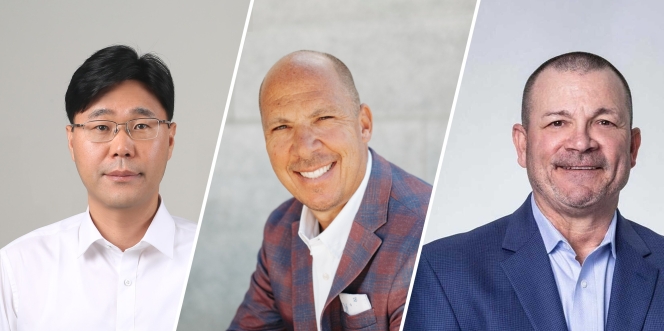
Hankook Tire & Technology has announced a series of executive leadership changes at its North American headquarters in Nashville, reinforcing its commitment to growth in passenger and commercial tyre markets. The restructuring brings fresh leadership across key sales and marketing functions.
Kyuwang (Ken) Cho assumes the role of Senior Vice President of North America Marketing, transitioning from his previous dual leadership of PC/LT Sales and Marketing. The industry veteran brings 25 years of Hankook experience, including a stint as Vice President of Global Sales in Korea. K C Jensen steps up as Vice President of US PC/LT Sales, expanding his responsibilities from regional to national oversight after demonstrating strong leadership in the Western market since 2018.
The company welcomes back Mark Roe as Vice President of US TBR Sales, where his four decades of commercial tyre expertise will guide replacement and OE sales strategies. Roe's extensive background includes previous leadership roles at Hankook and most recently at Ralson Tire North America.
Regional sales teams also see strategic promotions. Shaun Prott advances to Regional Director of PC/LT Sales for the West, building on his eight-year tenure with Hankook and prior experience with National Tire Warehouse. Travis Jones rejoins the organisation as Northeast Regional Director, bringing valuable perspective from Michelin and Pirelli. Brian Ford earns promotion to Regional Director of TBR Sales for the West after successfully managing key commercial accounts since 2021.
Rob Williams, President of Hankook Tire America Corp, said, "These leadership appointments reflect Hankook's strong momentum in North America. Ken, K.C. and Mark each bring exceptional industry experience, strategic focus and leadership qualities to their roles. Together, they will help elevate our presence across both consumer and commercial channels, and support our long-term growth ambitions in the US. These moves speak to the strength of our internal talent pipeline & ability to attract top talent and our continued investment in customer relationships. Shaun, Travis and Brian all bring deep knowledge of their markets and proven ability to grow key partnerships."
Michelin X Line Grip D Tyre Promises Range Of Upto 1 Million Miles & Upto 4 Retreads
- By TT News
- July 08, 2025
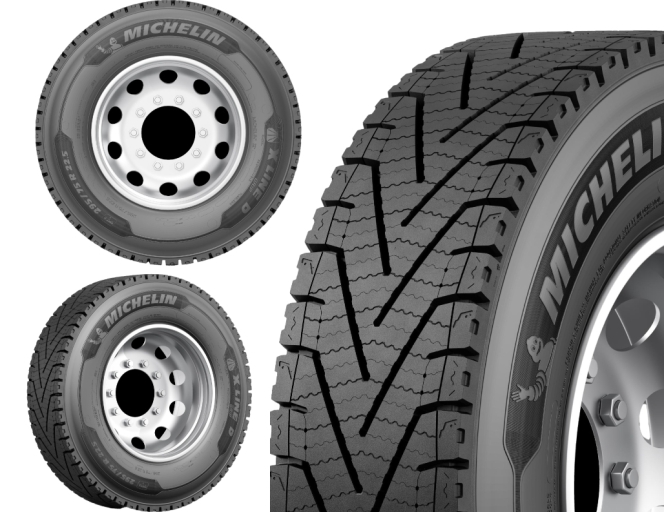
French tyre major Michelin has introduced its new X Line Grip D range, which is designed to work up to 1 million miles (1.6 million kilometres) with up to four retreads. The company shared its designers' claim that this is a ‘once-in-a-lifetime’ leap in tyre technology for fleets.
In addition to the higher range, the tyres also provide 20 percent more mileage and a 20 percent reduction in rolling resistance compared to the Michelin XDN2 tyre.
Designed to meet both wet and snowy conditions thanks to the chevron tread design, these tyres are said to prove 90 percent better starting traction in snow and over 25 percent better wet starting traction.
Fleets also benefit from using the Michelin X Line Grip D tyre, as it is built on the company’s Duracore casing, featuring Infinicoil and Powercoil technologies.
Pierluigi Cumo, VP – B2B Marketing, Michelin North America, said, “Michelin is never satisfied with current tyre technology when it comes to constantly improving and innovating our products. That’s why Michelin is so proud to introduce the Michelin X Line Grip D tyre. This tyre has the potential going forward to redefine the drive tyre standard in fleets for years to come. It is not an evolution to existing products, but something entirely different the fleet world has never seen before.”
“Michelin has a proven track record of delivering high-quality, reliable products that exceed performance expectations. This fantastic leap in drive tyre technology bring new levels of performance to the road and new levels of savings to our customers,” he concluded.
The Michelin X Line Grip D tyre is available in sizes 295/75R22.5 and 11R22.5.
Comments (0)
ADD COMMENT