- Bridgestone
- Bridgestone E8 Commitment
- My Firestone
- Tires Plus
- Marko Ibrahim
- Bridgestone Retail Operations
- Bridgestone Americas
- Boys and Girls Clubs of Middle Tennessee
- Club’s Andrew Jackson Clubhouse
Connected Mobility Solutions: JK’s big differentiator
- By Sharad Matade
- December 23, 2020
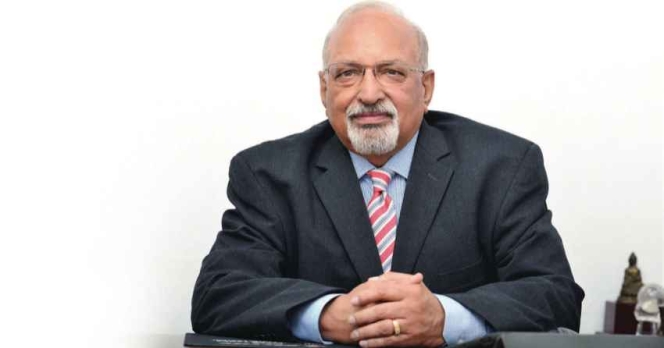
Around six years ago, JK Tyre joined hands with Pune-based Treel Mobility, which has now been acquired by the tyre company. Today JK Tyre is the only tyre company in India that indigenously manufacturers Tyre Pressure Monitoring Systems (TPMS) based on sensor technology. TREEL provides live data on the most important variables: tyre temperature, tyre pressure, tyre positions, locations, distance travelled and expected tyre life through our algorithm thus capture almost full health of the tyres. We provide our TMAS software for tyre management.
JK Tyre offers sensor technologies for both OE and aftermarket.
“The sensors can alert if the air pressure increases and drops by more than one psi. Our sensors are a multi-utility product and come with around five years of life,” Misra said, adding that the company’s sensor technologies are getting good response from the market.
JK Tyre’s manufacturing operations comprise of 12 state-of-the-art manufacturing facilities. The company has nine modern plants in India (three plants in Mysuru, three plants in Haridwar and one plant each in Banmore (M.P.), Kankroli (Rajasthan) and Chennai and three plants in Mexico – an aggregate production capacity of around 32 million tyres per annum.
The company is engaged in the manufacture and marketing of automotive tyres, tubes and flaps. JK Tyre’s products comprise Truck/Bus Radial & Bias, Passenger car radials, 2/3-wheeler tyres, LCV & SCV Bias & Radial, off-highway tyres (OTR and Farm), as well as speciality tyres for military/ defence, industrial and farm applications besides racing tyres.
Data generated through the sensors is not only helping JK Tyre to develop better products but provides an efficient and cost-effective service to its customers, especially in Truck Radial tyre space. “Service efficiency is what makes the difference to a customer. It is very important factor,” explained Misra.
JK Tyre is also in “Mobility Solutions”, where the company takes complete control of the tyre management and sells tyres by kilometres to the customers.
“Having such solutions availed, fleet owners do not have to worry about the most capital intensive part tyres. They do not have to buy tyres. We provide the right quality of tyres as per their requirements and then we make sure that tyres are optimally used and well maintained. To ensure performance and better life of tyres, we need lots of information and timely data collection which is not humanly possible. But now we can have all the data since tyres are fitted with sensors,” said Misra.
Misra claims that JK Tyres is the first company in India to provide such kind of services to the fleet companies.
“JK Tyre will continuously keep looking into the enhancement of sensor technologies in future,” he said.
With the help of JK Tyre’s service management and support around 3% fuel can be saved with the better pressure, alignment and maintenance of the tyres, whereas the tyre life is improved anywhere between 5% to 10%. “We have also seen big improvement in the downtime of the vehicles as well,” added Misra. The company extended this solution across more than 800 fleet owners. JK Tyre today has over 50 state-of-the-art Truck Wheels centres across the country which provides services enabled by high-quality machinery including computerised wheel alignment, wheel balancing, automated tyre changing, tyre rotation, nitrogen for tyre inflation, all under one roof to provide a 360-degree solution and excellent experience to the customer.
For EV mobility, the company is getting aggressive. JK Tyre has done benchmarking in the markets where the EV is largely being used. “We have tested and kept the tyres ready for EV cars. We have developed special tyres and have also done benchmarking with tyres which are being used by cars like Tesla / Kona,” said Misra. We intend offering special tyres for EV application backed with sensor technology.
The Bureau of Energy Efficiency (BEE), Bureau of Indian Standards (BIS) and Ministry of Road Transport and Highways (MoRTH) is planning to introduce star rating, like electric appliances, for tyres based on their rolling resistance, wet grip and rolling noise. In Europe also, the labelling is provided on tyres for rolling resistance, braking on wet surfaces and external noise.
However, India did not have facilities to test wet grip in India till recent times. For the export purpose, the Indian tyre companies used to get their tyres tested for wet grip from outside India.
“In India, the star ratings have been principally agreed and accepted. The levels from 1 to 5 for RR and wet grip have also been finalised for all type of tyres. The star rating will come soon in India,” said Misra. However, the data for wet grip & rolling noise is yet to be generated to confirm the specs so far considered.
Initially, the star rating will be voluntarily for the first two years and then it will become mandatory. “It will be interesting to see how star rating will influence customers’ buying behaviour,” he added.
The company is also establishing its wet grip testing capability. JK Tyre has become the first tyre company in India to buy a traction trailer to test wet grip. The traction trailer has been installed at NATRiP, Indore. International Centre for Automotive Technology and Automotive Research Association of India are in also in the process of certifying complete infrastructure for testing for Indian Tyre Industry for all category of tyres under review.
“Based on the readiness at ICAT and later at ARAI, the tyre industry will generate data on wet grip,” and approach certification body to align the specifications.
The company is currently using the traction trailer for its own purpose and will explore possibilities to provide wet grip testing service to other players in the Indian market.
For the commercial tyre business, the company’s recent breakthrough is Fuel Saver Technology, which saves up to 8% to 10% fuel. The company introduced its fuel-saving technology for its TBR tyres and now it will be brought for tubeless tyres which has also been extended to Tubeless Truck Tyres. The company has also successfully launched a radial mining tyre in the country.
As for as the passenger vehicle tyres, JK Tyre will launch an ultra-high-performance tyre, being developed in Europe. “We have tested our ultra-high-performance tyre up to 300 km/h on one of the best tracks available in Germany by test experts against best in class- tyres. We also picked up an Indian brand which declared their tyre as UHP tyre. Our tyre is far superior in terms of overall- handling, performance, control, wet grip and noise. We will launch this product soon,” said Misra.
In the auto industry, traditional rivals are coming together to meet future demand and tackle various challenges. For instance, BMW and Daimler have come together for autonomous cars. According to reports, the agreement to develop automated driving technology will focus on assisted driving systems, automated driving on highways, and automated parking. However, regarding this Misra does not see possibility of such collaborations on new technology sharing or development in the Indian tyre industry.
“Being a member of various committees in the industry, we had jointly mooted an idea of having a common research and development centre with the support of the Government of India where we have every possible capability for technology development. Even if we get into that, it will not be technology sharing but yes a great platform can get created for Technology development.
For JK Tyre, fuel economy, longevity and safety is paramount for its products. “Safety is expected to be inbuilt, though customers awareness needs to be enhanced. Now fuel efficiency and rolling resistance are gaining traction, particularly from OE perspective. For the aftermarket, longevity continues to be the top priority,” said Misra.
JK Tyre is also building capabilities in various fronts. JK Tyre’s new Research and Development (R&D) facility - Raghupati Singhania Centre of Excellence (RPSCOE) at Mysore has capabilities for all aspects right from testing the raw rubber sourced to creating simulations and predictive techniques for future offerings. Along with the installation of the traction trailer, the company was the first to have the Semi-Anechoic Chamber that uses specialised software for noise, vibration and harshness and data analysis. The company also has a centre of excellence at IIT Madras which is a joint venture between the company and IIT Madras. “We have developed many predictive technologies and other solution at the Centre. The virtual proving ground has been setup where you can establish the actual performance for the tyres on a vehicle without having actual tyres or vehicle. This is a very advanced concept. We are developing lot of techniques to master and get the full benefit in this virtual proving ground. Various data for the vehicles and a tyre is fed into the software and you can put data of any test track and drive the car with different speeds. You can feel the real performance. With this virtual proving ground capacity, we can generate data for tyres and determine what kind of tyres are best suited for a particular car.”
The company also uses a steering robot to collect data to have accurate and objective information.
For two-wheeler tyres, JK Tyre is focusing on tubeless tyres. The company plans to expand its two-wheeler tyre production from the current capacity of 650000 tyres per month. “We are in the process of expanding the range for high-end bikes. We are also planning to penetrate deeper into the OE space,” said Misra. The company is already OE supplier of two-wheeler tyres for Hero and Bajaj.
The biggest challenge for a technical person in the tyre industry is to anticipate the customer requirement stated as well as unstated and develop the right tyre. “The main challenge is to keep improving the performance and keep the cost low,” added Misra.
The Indian customer is very aware and knowledgeable hence continuous upgradation of technology and products is the key to success.
Powering Retrospection In Tyres Through Tags
- By Sharad Matade & Gaurav Nandi
- July 01, 2025
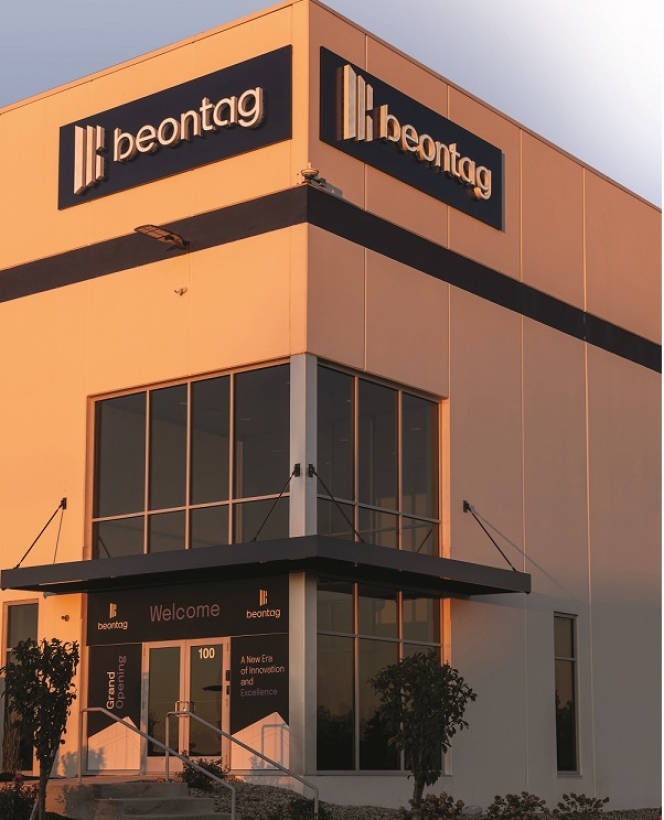
The integration of Radio Frequency Identification (RFID) technology into the tyre industry is gaining momentum, offering solutions for traceability, sustainability and lifecycle management. Beontag, in collaboration with Michelin, is spearheading this innovation by jointly designing specialised RFID tags that can withstand the harsh conditions tyres face, such as extreme heat and pressure. The tags store crucial data, enabling efficient recycling, retreading and warranty management. As the tyre industry evolves, RFID adoption is seen as essential for ensuring authenticity, improving asset management and supporting regulatory frameworks. However, challenges remain in scaling production and increasing industry awareness.
Punch card systems, barcodes, dog tags, biometric scanners etc. are all instruments that offer basic information about humans and commodities for identification, authentication, traceability and retrospection.
The tyre industry is similarly standing at a crossroad where the demand for traceability and retrospection is growing. Tyre manufacturers, retailers, retreaders and recyclers are showing a growing exuberance for digital footprints that can record, summarise and authenticate information related to each existing and new tyres throughout the commodities lifecycle.
And the simple solution catering to such demands is a radio frequency identification (RFID) tags. While the use of RFID tags is new within the global tyre market, these have found a stronghold across retail, logistics, manufacturing, healthcare etc.
The tag is changing the game of traceability within tyre markets as the adoption grows. Technological companies are collaborating with tyre manufacturers to develop tailor-made RFIDs.
International RFID and IoT expert Beontag is one such company that has developed RFID tags for the tyre industry. Divulging deep into the engineering mechanics of the tag, APAC Senior Sales Manager Evelyn Ong told Tyre Trends, “RFID technology used in tyres is significantly different from conventional RFID applications due to the harsh conditions tyres endure, such as high temperature, pressure and wear and tear. Unlike RFID tags used in retail or medical settings, tyre RFID tags must be engineered to survive extreme conditions. As a result, traditional RFID designs, which use PET labels and conductive paste for chip attachment, are unsuitable. Instead, tyre RFID tags rely on a mechanically robust and inductively coupled antenna structure.”
“Designing RFID for tyres required a completely new approach, and the current version (generation four) is believed to be durable enough to last the entire lifecycle of a tyre. This innovation aligns with initiatives like the European Digital Product Passport (DPP), which mandates that products must be identifiable throughout their life cycle. Although RFID chips themselves only store a unique identifier (similar to a FASTag or car license plate), all detailed data such as manufacturing date, plant origin, distribution history, usage, retreading details and material composition is stored in backend software systems. As the tyre moves through the supply chain, each stakeholder adds relevant data to the software based on the RFID, creating a comprehensive database that supports traceability and lifecycle management including recycling or retreading,” she added.
The company’s main RFID tag for the tyre industry includes a chip with memory, enabling it to store data and serve as a digital identifier for the physical tyre using radio waves. This transforms a traditional tyre into a digitally traceable product.
Beontag jointly designed this RFID tag with Michelin, exploring the benefits of embedding a chip in tyres for purposes like asset management and product authentication and was instrumental in driving standardisation across the industry. While Michelin is the first tyre manufacturer to roll out the new ‘smart tyres’ with Beontag technology, the manufacturer recently announced a partnership with Kumho Tire and aims to go into partnership with other brands in the near future.
DEMAND AND SUPPLY
The company recently participated in a global tyre exhibition and rationalised its participation with significant long-term potential of the tyre RFID market. “With over 30 billion tyres in circulation globally, the scale of the opportunity is enormous. Having worked in RFID for over 20 years, the technology excels in applications involving products that are physically similar and difficult to differentiate visually like tyres. This makes tyres an ideal use case for RFID,” said the official.
Ong explained that beyond the European Digital Product Passport regulation, a key driver for embedding RFID in tyres is the fundamental need for every product to have a unique identity, whether through a barcode, QR code or digital tag. In the tyre industry, this need has been especially pressing due to the limitations of traditional identification methods like hot stamping, which often wear off over time and result in a loss of traceability.
She noted that the absence of a durable, readable ID creates challenges in verifying authenticity, determining warranty status and tracing the tyre’s origin. For instance, without a reliable identifier, it becomes difficult to confirm whether a tyre is genuinely from Michelin or to retrieve key manufacturing details such as plant location, batch number or intended distribution path.
By embedding RFID tags with unique digital identities, the industry gains the ability to link every part of the tyre’s lifecycle across the value chain. This ensures consistent traceability, facilitates better inventory and warranty management and combats counterfeiting.
“We are actively engaging with the top 10 global tyre manufacturers in the transition towards RFID-enabled tyres. While the European market is leading adoption driven largely by regulatory frameworks, we are also working with tyres manufacturers across the Asia-Pacific region and beyond.
“Although OEMs like Michelin are beginning to integrate RFID tags, starting with high-end passenger tyres, there is a growing and immediate demand from the aftermarket. This secondary market includes fleet operators, leasing companies and pay-per-use models, where the need for tyre tracking is urgent. These businesses want to monitor retreading cycles, ensure asset recovery and verify ownership, especially to prevent tyre theft or unauthorised replacements,” she added.
According to Ong, some aftermarket players are even looking to embed RFID tags independently rather than waiting for OEMs to standardise the process, underscoring strong demand outside the traditional supply chain.
When asked about growth potential between the passenger and commercial segments, she indicated that although current OEM efforts are focused on high-end passenger tyres, interest from the commercial and aftermarket sectors is strong and could drive faster adoption due to practical and financial incentives.
Furthermore, RFID tags play a key role in sustainability by enabling traceability throughout a tyre’s lifecycle. It allows manufacturers to capture crucial data at the point of manufacture, which is essential for tracking and recycling. With RFID, recycling processes become more efficient because tyres can be easily sorted based on type, size and materials. This minimises waste, reduces sorting time and improves the overall effectiveness of recycling efforts.
HURDLES IN ADOPTION
The executive noted that there are unique challenges of designing an RFID tag for tyres given the nature of its operations. To address these hurdles, the company and Michelin jointly designed and extensively validated a specialised RFID tag consisting of a chip and an antenna, which is fully embedded within the tyre.
This tag is designed to be invisible from the outside and integrated into the tyre structure in a way that ensures durability without compromising performance. The antenna’s spring-like structure allows it to expand and contract along with the tyre’s movement without affecting its function.
Crucially, the connection between the chip module and spring antenna is linkless, using inductive coupling instead of mechanical connection. This inductive mechanism ensures reliability even under extreme conditions like high temperature, pressure and physical deformation.
Although the tag is not constantly read during vehicle operation, it must remain functional and readable during inspections or servicing.
Alluding to broader industry challenges towards adoption, Ong said, “Current challenges centre primarily around a lack of awareness and industrialisation of the production process in existing tyre production lines and factories. Unlike retail, where RFID is well-established, the tyre sector is still in the early stages of adoption. Because of this, there is a need to educate the market, build trust and demonstrate real-world use cases. Potential customers are hesitant to act as first movers and prefer to see proven implementations to reduce perceived risk. A hopeful future challenge would be demand outpacing production capacity. However, a more realistic and significant long-term challenge lies in technological evolution, particularly around IC size, performance development and adding more functionality through sensor information.”
INTEGRATING RFIDS
The RFID chip used in tyres stores a minimum of 96 bits of data, which aligns with the standard size modelled after barcodes. This size is sufficient to encode essential identifying information including a serialised number.
While barcodes only identify products at the SKU level, RFID allows each item to have a unique identifier, making it far more powerful for inventory management. At every stage in the tyre’s lifecycle, it is the responsibility of the user or stakeholder to read the RFID tag and input relevant data into the software system, linking it to the tag’s unique identifier.
One of the most compelling applications of tyre RFID is during the tyre’s second life – especially in retreading. In this stage, the retreader can embed a new RFID tag and effectively reset the tyre’s lifecycle. This allows the retreading company to claim and track the work they’ve done including how many times the tyre has been retreaded and when.
Fleet operators or regulators can use this data to verify authenticity, ensure compliance and manage safety.
At the end of the tyre’s life, especially during the recycling stage, RFID continues to offer value by recording the tyre’s complete journey. Recyclers can access a tyre’s full history by ensuring proper handling and reporting.
The key challenge in placing the RFID tag is ensuring its proper location and integration into the tyre’s structure. This process must be carefully controlled as the tag must not only be positioned in the optimal spot but also withstand the stresses and heat of the curing process. If the tag was placed improperly, it could potentially cause issues with its performance, especially in terms of readability after the tyre is fully cured and ready for use.
COMPETITION AND EVOLUTION
Besides Beontag, there are other companies operating within the tyre RFID space. Alluding to the distinction between them, Ong explained, “The main difference of our product lies in the patented POD design (POD = IC module/package). Our product utilises a special alloy for the antenna, which prevents deformation and ensures consistent diameter and gap size. Additionally, the chip packaging has been specifically designed to offer better protection, reducing the risk of damage and ensuring reliable readings.”
She explained that the company’s business case for RFID technology in the tyre industry is clear and it believes strongly in its potential. She emphasised the importance of spreading awareness about the technology, as Europe will be implementing the technology first, but other regions including APAC and the Americas will be catching up as the technology is proven in the coming years.
NIRA Dynamics Partners BANF Smart Tire System For Advanced Vehicle Safety And Predictive Maintenance
- By TT News
- June 16, 2025
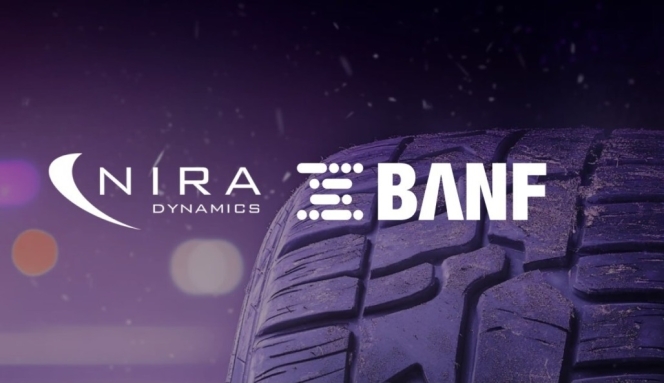
Swedish automotive software leader NIRA Dynamics AB and BANF Smart Tire System of South Korea have announced a new partnership aimed at significantly enhancing vehicle safety and predictive maintenance for commercial vehicles. The collaboration will see BANF integrate its high-frequency tyre sensors into NIRA's established software ecosystem.
This strategic alliance aims to disrupt Tyre Pressure Monitoring Systems (TPMS), providing commercial fleets and automakers with unprecedented real-time insights into tyre health and road safety. NIRA Dynamics, founded in 2001, is a global automotive software powerhouse with its technologies deployed in over 120 million vehicles worldwide, including an indirect TPMS (iTPMS) that has surpassed 110 million units sold.
Under the agreement, NIRA will incorporate BANF's triaxial tyre sensors into its Road Surface Information (RSI) and Wheel Safety Insights (WSI) platforms. These platforms already utilise existing vehicle sensor data and proprietary algorithms for functions like tyre grip estimation, tread wear analysis and loose wheel detection.
BANF's key innovation lies in its Smart Profiler system, which wirelessly powers internal tyre sensors directly from the vehicle battery, overcoming the challenge of continuous power and real-time data transmission from rotating tyres. This integration will significantly enhance NIRA's capabilities, particularly for monitoring commercial vehicle loads and dual-tyre setups, by providing sensor data at high sampling rates of 1kHz and 4kHz.
Otto Johansson, Head of Innovation at NIRA Dynamics, said, "This collaboration accelerates our vision of creating a comprehensive vehicle intelligence network. While our software solutions already process data from millions of vehicles, adding specialised hardware enables new use cases in predictive maintenance and ADAS applications."
NIRA's evolution from software-only tyre pressure monitoring to multi-layered safety systems is evident in its flagship Tyre Pressure Indicator (TPI) technology, which has eliminated the need for physical sensors in many applications, significantly reducing electronic waste. The company has also collaborated with automotive giants like Volkswagen Group on innovations such as Road Surface Alerts.
The partnership also addresses critical safety needs in commercial vehicles. NIRA's Loose Wheel Indicator (LWI), already deployed in Audi vehicles, will now be extended to heavy-duty vehicles through the BANF collaboration, aiming to mitigate the thousands of annual wheel detachment incidents reported.
For fleet operators, the integrated system promises substantial operational benefits. NIRA's Winter Road Insights product, which helps optimise road maintenance, combined with BANF's wear prediction algorithms, is expected to lead to reduced tyre replacement costs and improved fuel efficiency.
Ron Yoogun Lee, Head of Business Development, BANF, said, “Our goal is to enhance cost-effectiveness, save lives and preserve the environment by digitising tyres, which are the last analog domain in the mobility industry.”
Looking ahead, NIRA's technology roadmap includes developing ‘grip maps’ for SAE Level 2-3 autonomous vehicles and leveraging data from millions of vehicles to create AI models for predictive infrastructure maintenance, further solidifying its position at the forefront of automotive innovation.
Anyline Launches TireBuddy App to Streamline Tyre Inspections
- By TT News
- June 13, 2025
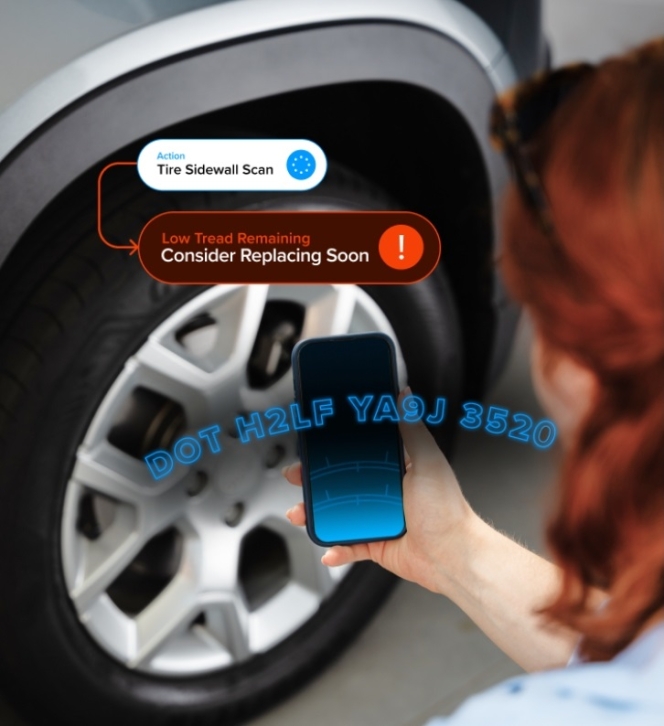
AI-powered mobile data capture company Anyline has launched TireBuddy, a smartphone-based app designed to modernise tyre inspections in automotive service bays. The app replaces traditional, manual inspection methods with a standardised digital workflow that delivers consistent, data-backed results and clear customer reports.
TireBuddy offers technicians tools to detect tread depth issues, tyre age, alignment concerns and sidewall damage using AI-powered analysis and visual reporting – without the need for additional hardware. Reports can be instantly shared in digital or printed formats, helping to reduce manual entry errors and increase customer trust.
The launch comes ahead of National Tire Safety Week (30 June 30 – 4 July), positioning the app as a timely solution for shops preparing for the summer travel season.
Lukas Kinigadner, Co-Chief Executive Officer, Anyline, said, “TireBuddy is not only about faster inspections — it’s about more trustworthy ones. We’re helping garages and service centres replace subjective tyre checks with data-backed insights and visual reporting that both technicians and customers can rely on.”
Frederic Baroin, Global Head of Automotive Business at Anyline, said, “TireBuddy empowers technicians with real-time, reliable data that strengthens recommendations and builds customer confidence. We designed it to deliver clarity, not complexity, in every inspection.”
By enhancing inspection accuracy and transparency, Anyline said TireBuddy can also drive higher service approvals and boost shop revenue.
CEAT Acquires India’s First Scania Heavy-Duty Truck to Boost Tyre Testing
- By TT News
- June 03, 2025
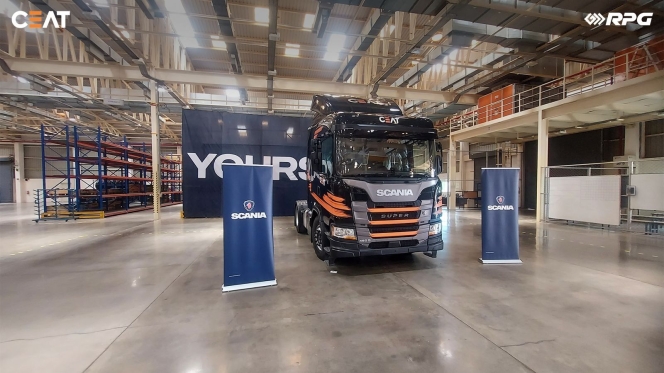
Indian tyre maker CEAT said it has purchased the country’s first Scania 460 G prime mover truck to strengthen its research and development operations as the company pushes to expand in overseas markets.
The Mumbai-based manufacturer described the acquisition as part of efforts to upgrade its commercial vehicle tyre testing capabilities to international standards, particularly for certification in Europe and the United States.
The Scania G460 produces 460 horsepower from its 12.7-litre engine and can handle a gross vehicle weight of 150,000 kilograms (330,693 pounds). The truck features Scania’s Super engine technology, which the Swedish manufacturer says improves fuel efficiency while cutting emissions.
CEAT officials stated that the new testing platform will help accelerate product development and reduce costs while meeting stricter global standards.
“This high-performance vehicle is not just a prime mover — it’s a strategic investment in our Commercial Vehicle Tyre Testing Infrastructure, aimed at elevating our research & development capabilities to meet global standards,” the company said in a statement.
The investment comes as Indian tyre companies grapple with volatile raw material prices while trying to capitalize on strong domestic demand from India’s growing automotive sector. Industry analysts say that manufacturers are under pressure to improve efficiency and expand internationally in order to maintain profitability.
CEAT joins other major Indian tyre makers in ramping up research capabilities as they compete for market share both domestically and abroad.
The company said the new truck will support vehicle dynamics testing and help reduce the time needed to bring new commercial tyre products to market.
Comments (0)
ADD COMMENT