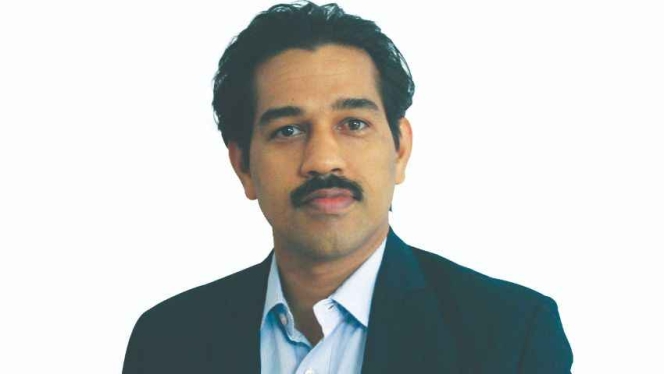
When we discuss about a motorcycle's performance, we generally speak about its engine power, torque, top speed, how fast it can accelerate, vehicle sound etc. Nevertheless, all these are meaningless if a driver cannot control the machine and/or is not comfortable while riding. There comes the importance of tyres. Tyres are the most crucial parts of a vehicle suspension system. Tyres are the only component in a motorcycle that constantly stays in contact with the road. The part of tread which is in contact with road surface is called ‘contact patch’ & Is about half the size of a post card. The overall suspension system (including tyres) ensures the right contact between the tires and the road surface at every stage of driving, thereby ensuring stability and good handling of the vehicle.
As tyres are the only contact with the road, they are responsible for multiple functions, such as –
Transfer the engine power to the road- meeting the demands of acceleration and braking
Provides right hold (grip) on different surfaces like dry, wet, snow, loose soils etc.
Helps the rider to steer the vehicle by responding to the handle movements
Carry the weight of the vehicle & rider
Ensuring the comfort of the rider by absorbing and dampening shock
Apart from the above aspects, tyres play a vital role in vehicle aesthetics, safety, fuel efficiency etc. These and several other challenges make Motorcycle tyre design a very interesting and responsible subject.
Apart from being a crucial part of a vehicle suspension system, tyres are the only contact between vehicle & road. Motorcycle vehicle dynamics and control characteristics are highly influenced by the tyre design. It is therefore highly imperative for a vehicle chase/suspension designer & tyre designer to work together in tandem. This will ensure that the part designs will complement each other and deliver the characteristic target performance of a motorcycle. A robust interaction mechanism between the R&Ds of OEM [Original Equipment Manufactures] and tyre manufactures is a growing necessity to cater to the ever‐increasing demands of performance entrusted upon the tyre of today. In case of tyres getting designed exclusively for aftermarket, a tyre designer work closely with the vehicle dynamics team to ensure that the retrofit design delivers desired target performance of the vehicle
Some of the major steps involved in motorcycle tyre design are
Product planning & Tyre “Size” finalization: During this stage a vehicle designer & tyre designer jointly review the vehicle performance requirements and decides the parameters specific to tyre performance. This includes:
Defying the application /terrine: Depending on application, 2 wheelers maybe broadly classified as Sport, Cruiser, Choppers, Touring, scooter, Step through, Sport touring, Enduro etc. Different OEM’s follow different terminologies, but a for a tyre designer to understand the final use by the user is of utmost importance. Demands from a tyre varies with each vehicle category, for example, for a cruiser the tyre is designed to be robust so as to hold up the weight of such heavy bikes and deliver long tyre life, whereas for a Sport touring /super sport bike, tyres are designed to deliver quick and precise handling with superior grip. These tires are lighter and made by using softer compounds for Superior grip.
Selection of Bias /Bias belted / Radial: At this juncture, I am not going to delve deeper into a detailed comparison of these constructions – however, it is important to acknowledge that both these construction types have their respective advantages and disadvantages. Each of these constructions has few specific applications where one performs better than the other. The selection of construction type mainly depends on vehicle category (application), vehicle Speed, load on the tyre, stability requirements, handling requirements, etc. for example Bias tyres are used in medium speed but heavy weight vehicles owing to their sturdy sidewalls, whereas Radial tyres are the ideal choice for high speed , vehicles because of their superior dimensional stability.
Selection of Tube type Vs Tubeless: Functionally both types of tyres have a proven track record for almost all applications. Hence this choice mainly depends on vehicle Rim design, which is decided by the overall aesthetic demand & application of the motorcycle.For high speed application, tubeless is always preferred
Finalizing the Tyre size / Tyre Geometry: In general, we may call it as tyre “size” – which includes tyre width, tyre diameter, rim diameter etc. Tyre geometry affects the vehicle dynamics like caster, trail, vehicle Center of gravity [CoG], etc. It also influences the area of contact between vehicle and road surface under different riding conditions & load-carrying capacity of the tyres. Furthermore, tyre size significantly influences vehicle aesthetic as well. Tyre “size” and vehicle rim size are always interconnected. Decision on one influence the decision on the other. Usually motorcycles have different front and rear tyre sizes depending on vehicle geometry & load distribution. Tyre “sizes” are decided considering all these parameters & the designers ensures that it follows the standards’ guidelines applicable in target countries.
Tyre tread profile design:
Contrary to the passenger car tyre designs which have almost flat tread surface, motorcycle tires have a U-shaped profile and a contact patch that changes size and shape during cornering. There is a major difference in the way lateral force is built up in passenger car and two wheelers. In case of passenger car, mechanism of lateral force builds up is due to slip angle whereas in two-wheeler it is mainly because of the camber or the leaning of the vehicle. Hence you see a flat tread area for passenger car tyre and U-shaped profile for Motorcycle tyre
This U-shaped profile is an important design factor having a direct influence on vehicle performances such as drivability (handling) durability, ride comfort, noise and wear resistance etc.
These tread contours are designed as the arc of one radius, or a combination of arcs with two or more radii. These profiles ensure the required contact patch availability at different lean angles & are controlled by the lean characteristic of the vehicles. It is very critical to balance the performance of front tyre & rear tyre of s motorcycle for precise handling of the vehicle. The contour designs play an important role in front /Rear tyre balance.
Tyre tread pattern design:
Patterns are molded in the tread area of tyre by repeated arrangement of ‘Groves’ or ‘Blocks’ & are generally referred to as “tread pattern”.
Significance of tread pattern:
Tread pattern plays a vital role in tyre performance such as:
Optimizing the traction on the riding surface
Eliminating aquaplaning
Optimizing the” Wear” of tread area·
Ensuring the continuity of tyre performance at different wear Stages [ wear %] of tyre.
Rolling resistance of the tyre
Noise generation
roviding a measurable clue to the owner on time for removal /suitability for continuous usage. etc.
Tread patterns not only helps in achieving the target performance, but also impart unique look to tyres and enhance aesthetics
Tyre patterns are broadly classified into 4 Major headings
- Rib patterns
- Directional
- Block [ Knobby]
- Slick tyres [Pattern less]
Selection of which group of patterns is mainly controlled by the terrain of application, e.g. Directional patterns are preferred in paved roads and knobby pattern ae mainly used on off-road applications. Pattern less tyres are normally used in racing track applications to provide maximum traction. Vehicles are designed to work in a combination of different terrains – similarly, tread patterns also have subgroups– which are optimized to operate in different combination of terrains. E.g. Semi knobby patterns for on – off allocations, High land – minimum grove patterns for Supersport highway applications etc.
Designer alter the direction of the grove, depth of the grove, number of groves, the ratio between Grove area & non grove area [ Land- sea ratio] , shape of the grove, the width of the grove etc. to optimize the performance of tread pattern. These patterns are designed to perform under different dynamic conditions. Nowadays designers seek the help of computer-aided simulations to predict the performance under different loading /riding conditions to optimize the pattern design.
Tyre as an Aesthetic component
The visual appeal of tyre is significant contributor in the overall aesthetics of a motorcycle. Hence in addition to performing all the functional requirements discussed so far, tyres ought to look good too.
The tread pattern should complement the overall styling language of a motorcycle. This attracts the attention of OEM’s vehicle styling studios towards tyre tread designs as well. In fact, most of the new tyre designs are done first at styling studio and then technically optimized by the tyre engineer to guarantee the functionality.
Material design
Tyre is a composite material made of different rubber compounds and reinforcing materials. Right compound and reinforcing material selection are crucial to achieve the target performance of tyre.
- Reinforcing materials:
Reinforcing materials provides the required strength and stiffness for tyre body [carcass]. This includes “tyre cords” used in tyre body ply & “bead wires” used in bead construction of tyres. Most used tyre cord materials are Nylon 6, Nylon 6-6, Polyester, Aramid, Rayon, Steel, etc.
These materials differ in their chemical composition, tensile strength, elongation properties, impact strength, temperature resistance, rubber adhesion, etc. Tyre engineer must choose the right tyre cords depending on the performance demands of the tyre like load carrying capacity, durability, impact resistance, drivability, speed of operations etc. Cost & availability also are few decisive parameters during selection of reinforcing materials.
Tyre Cord denier, cord style, EPI (Ends Per Inch), angle of cords and number of plies affect the strength of a tyre and are chosen based on engineering, and design criteria.
structural durability of a tyre is Primarily determined by the reinforcing material
- Rubber compound design
Each part of the tyre must dispense different functions and are thus designed with different rubber compounds like tread compound, sidewall compound, carcass compound, bead wire coat compound, etc. Though all these compounds have their own importance, but tread compound selection is the most critical, as it has a direct impact on tyre traction, handling, wear performance, durability, rolling resistance, etc.
-
- Trends of tread compound design:
Even though smaller number of components are used in a motorcycle tyre, than as compared with passenger car tyres, but performance challenges involved in compounding are far more complex considering less area of tyre in contact with road. 3 major performance requirements in motorcycle tread compound are (1) Grip (2) Rolling resistance [fuel efficiency] and (3) Tyre life which is generally referred as the magic triangle in tyre rubber compounding. This is due to the contradictory response of these 3 performance characteristics to rubber compounding approach. For example, improvement in Grip normally comes with an increase in rolling resistance with conventional compounding as both are related to energy loss. It is always a challenge for tyre compounder to improve all three performance requirements together and this calls for the incorporation of advanced polymers and fillers.
Performance priorities for tread compound changes based on operating terrain, type of vehicle, etc. e.g. Street two-wheeler tread compound designs primarily focus on high grip and high-speed capabilities, whereas an on-off application tyre require higher cut and chunk resistance tread compound.
Demand for lower rolling resistance tyre is showing a steady increase Year-on-Year. Major divers for this growing demand are Electric vehicle introduction & increased focus on vehicle fuel efficiency, in few segments. Tread compounds are expected to deliver lower rolling resistance, without compromising the Grip – typical “magic triangle” puzzle for any tyre compounding engineer. Tyre industry can address this challenge by usage of new generation materials like SSBR, functionalized SSBR, high molecular
Design for manufacturing
For success of any product – Design & manufacturing sync is a must. While designing, to accommodate all functional requirements, a designer cannot ignore the significance of manufacturing process. Hence every tyre design is optimized to satisfy both functional & manufacturability needs. This if not done properly may result in suboptimal performance of the product,
Product Performance Testing
It’s important to review and verify the product performance before releasing it into the market. There are a set of Indoor & Outdoor tests for performance review. A few of them are listed below,
Indoor tests: High-speed drum test, Endurance test, Rolling resistance test, Force and moment testing, Stiffness test, Footprint etc.
Outdoor tests: Ride and Handling testing (track, off-road, public road etc.], Braking test [wet, dry], tyre wear test etc.
Blend of Engineering & Art
Being an integral part of vehicle suspension system & only contact point with road, a tyre plays significant role in motorcycle performance [safety, drivability etc.]. In addition to these performance parameters, tyres have significant influence on the overall styling of the vehicle. It complements the primary theme of the vehicle. A right blend of engineering and art is essential for a successful tyre design. One cannot substitute the other. Amongst different steps of tyre design like, dimension finalization, tread design & martial design etc. the most critical step is tread design (profile, pattern & compound)
Few areas designers are focusing today to meet the near/middle future demands are
- Lowering the rolling resistance – without compromising grip
- Shortening the time to market.
- virtual simulation of tyre performance
References
- ‘’The pneumonic tyre’’, National Highway Traffic Safety Administration, Feb 2006
- T. French, Tyre Technology, Hilger, New York, 1989.
- Mechanics of Pneumatic Tires, S. K Clark, ed., University of Michigan, US Department of Transportation, National Highway Traffic Safety Administration, Washington, DC, 20590, 1891.
4. Handbook of vehicle-road interaction: vehicle dynamics, suspension design, and road damage / edited by David Cebon. p. cm. - (Advances in engineering), ISBN 9026515545
5. “Tyre and Vehicle Dynamics” , Hans B. Pacejka, Professor Emeritus Delft University of Technology, Consultant TNO Automotive Helmond
The author is General Manager - Product Development,2&3-Wheeler tyres, CEAT Tyres
The Last Man Standing: How A Perth Startup Became The Mining Industry’s Tyre Whisperer
- By Sharad Matade
- August 13, 2025
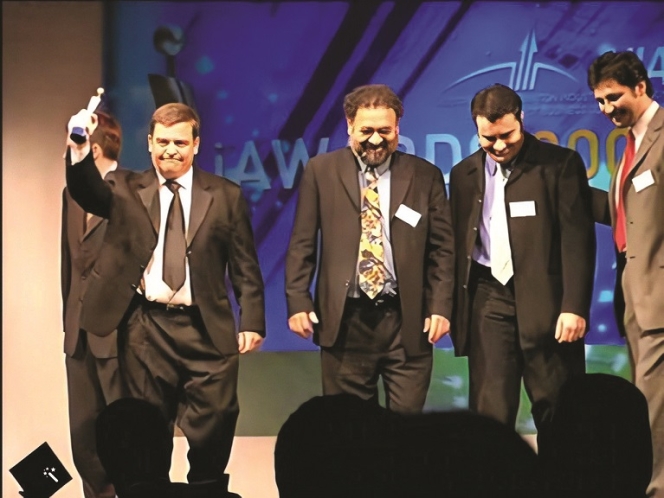
Vehicle Management Corporation survived industry consolidation to dominate a USD 1.5 billion niche managing mining’s most expensive consumables.
More than 30 years after its modest beginnings, Fernie’s Vehicle Management Corporation (VMC) now leads the global independent tyre management software sector. The company oversees USD 1.5 billion in tyre and rim assets across 480 mining sites on multiple continents. With individual mining tyres costing upward of USD 50,000, VMC’s enTIRE software has become critical for operators aiming to maximise the value of their most expensive consumables.
“We don’t sell tyres or offer tyre services – software is our sole focus,” Fernie said. This specialisation has been VMC’s core competitive strength and a key reason it outlasted larger, better-funded competitors during two decades of industry consolidation.
VMC’s journey from a single-client DOS application to managing billions of dollars in assets demonstrates how even small software firms can thrive by addressing highly specialised industry needs that larger solutions often overlook.
THE CONSOLIDATION SURVIVOR
VMC’s fierce independence stands out in a tyre industry where consolidation is accelerating. While giants like Bridgestone and Michelin snapped up rivals – Otraco and Klinge, respectively – VMC has held the line, rebuffing takeover interest and prioritising customer relationships over shareholder pressure or supplier alliances.
“With Bridgestone acquiring Otraco and Michelin purchasing Klinge, VMC became the only independent, commercially viable tyre management software provider remaining,” Fernie explained. “Developing a competitive independent system today would require USD 5+ million in funding and years of field testing, making our market position difficult to replicate and any alternatives difficult to justify.”
This independence is now central to VMC’s appeal for multinational miners working with multiple suppliers. Unlike manufacturer-backed software, VMC’s enTIRE system is completely agnostic, allowing clients to base their purchasing decisions solely on performance data and cost-effectiveness.
That strategy has earned VMC unusually durable client ties. Its three-decade partnership with Freeport Indonesia – one of the world’s largest mining operations –underscores the appeal of a model that favours operational flexibility over vendor lock-in, a growing concern among customers wary of manufacturer-driven ecosystems.
“Most of our clients are long-term,” Fernie noted, emphasising how this stability has become increasingly valuable as mining companies seek to avoid the disruption and data loss that often accompanies vendor changes in manufacturer-controlled systems.
BEYOND COST CUTTING: SAFETY AND ENVIRONMENTAL IMPACT
While cost reductions – often 10 percent to 30 percent within three years – drive initial adoption, VMC’s impact extends far beyond savings. In nonstop mining environments, where tyre failures can lead to life-threatening accidents, safety and uptime are equally vital.
“Operating tyres outside pressure or load specs increases blowout risks,” Fernie said, emphasising safety. enTIRE tracks rim certifications and keeps failure histories, supporting safety protocols. “Rim accidents are very dangerous, potentially fatal.”
Environmental benefits have also emerged as an increasingly important value proposition for mining companies under growing pressure to reduce their carbon footprints and waste generation. By extending tyre life and dramatically reducing premature failures, mining operations generate substantially less waste while simultaneously improving fuel efficiency through optimised tyre pressure monitoring systems.
“Optimising pressure with TPMS can extend tyre life by 20–30 percent, reduce rolling resistance and lower fuel consumption by up to three percent – a substantial saving in mining operations,” Fernie explained. In an industry where fuel costs represent significant operational expenses and environmental regulations continue to tighten, these seemingly modest percentage improvements compound into substantial savings and meaningful reductions in environmental impact.
The environmental mathematics are compelling: operators can achieve approximately 30 percent increases in tyre life through proper lifecycle management, directly reducing landfill waste, shipping requirements and manufacturing demands – collectively helping reduce the carbon footprint of tyre procurement and disposal across the mining sector.
THE TECHNOLOGY EVOLUTION
VMC’s technological evolution, from humble beginnings as a basic DOS program to advanced, cloud-based solutions, reflects the broader digitisation revolution in factory operations that began in the early 1990s. The firm’s flagship enTIRE software began as a Windows product with what Fernie recounts with clear pride as a ‘pioneering drag-and-drop interface’ in the early 1990s – a cutting-edge user experience design that was decades ahead of its time.
The platform has progressed steadily through several generations of technology, transitioning from Microsoft Access databases to high-performance SQL Server implementations, which have significantly improved performance and scalability. It introduced full multi-site support features in 2001 and incrementally incorporated tyre pressure monitoring systems (TPMS) from seven sensor vendors starting in 2007. The software industry award was presented in 2005, when the system was named the Financial Review Australian Information Industry Association’s ‘Best Industrial Software Application’.
Recent development efforts focus heavily on artificial intelligence integration for enhanced analytics capabilities and predictive maintenance functionalities. “We’re actively using AI to streamline development and support,” Fernie said, outlining the company’s forward-looking technology strategy. “We expect AI will significantly enhance predictive analytics, client dashboards and user interfaces, improving how data is interpreted and acted upon.”
The integration of multiple TPMS systems represents a particular competitive advantage. “enTIRE PressureNet is sensor brand-agnostic and integrates with multiple sensor types, unlike many manufacturer-locked systems,” Fernie explained. “Our independence allows clients to choose or switch sensor brands without losing backend compatibility.”
FIGHTING FRAUD IN HIGH-STAKES OPERATIONS
In addition to optimising operations and pre-emptive maintenance, enTIRE is an advanced fraud detection and prevention solution in settings where a single tyre costs more than high-end cars. The software’s detailed tracking identifies many forms of theft, tampering and misbehaviour that afflict the high-end tyre market throughout global mining operations.
“Tyre fitters may scrap a near-new tyre (if not tracked) and then this tyre would be picked up from the scrap location and resold,” Fernie explained, detailing one common fraud scheme. “In mining, each tyre can be worth up to USD 50,000. This potential additional income is very significant in developing countries.” The financial incentives for such fraud are substantial, making comprehensive tracking systems essential for asset protection.
Beyond simple theft, the system prevents more sophisticated data manipulation during high-stakes contract negotiations. “If a tyre supply contract is worth USD 100 million, there can be significant pressure placed on operators of any tyre management system to ‘modify’ tyre performance in a supplier’s favour,” Fernie said, highlighting the system’s role in maintaining data integrity. “enTIRE has very strong internal systems to prevent internal tampering.”
Other fraud prevention features involve detecting unauthorised tyre replacement in off-site fleet operations, where drivers may sell new tyres and substitute them with less expensive ones, and preventing early scrapping of tyres that can otherwise be retreaded or reallocated for a longer service life.
ORGANIC GROWTH STRATEGY AND MARKET POSITION
VMC has achieved its market-leading position without relying on venture capital investment or large corporate sponsorship; instead, it has relied on diligent organic growth fuelled by strong customer relationships, word-of-mouth referrals and relentless reinvestment in product development. The firm purposefully reinvested earnings in automation technologies and enhanced software capabilities, rather than engaging in fervent hiring or costly promotional campaigns, while maintaining lean operations and establishing increasingly refined development capabilities.
“When large manufacturers’ systems failed with over-engineered projects, clients often came to us for reliable replacements,” Fernie said, describing a pattern that has accelerated during recent supply chain disruptions when tyre shortages made lifecycle extension critical for maintaining operational continuity.
The company’s fundamental growth strategy centres on systematic data accumulation and market share expansion. “Our strategy, early on, has always been to increase market share as we realised that the more tyre performance data our systems controlled, the more valuable we would become,” Fernie explained, articulating a network effect strategy that becomes more powerful with scale.
This field-tested software, combined with deep industry connections and vast databases, now creates major entry barriers that would require competitors years and millions to overcome.
DIVERSE APPLICATIONS AND INDUSTRY DIFFERENCES
VMC software supports significantly disparate operating models in mining and transport industries, each with dissimilar tracking demands and cost-justification criteria. Mining applications typically involve high-cost, low-volume tyres that are closely monitored by operating hours. In contrast, transport fleets manage high-volume, lower-cost tyres, which are tracked by kilometres and frequently shared across interchanging trailers pulled by various prime movers.
“Mining justifies the cost of extensive data entry based on the large cost savings, while the transport industry is more careful regarding tracking cost,” Fernie explained, highlighting how economic incentives drive different implementation approaches across industries.
Its flexibility in covering these differing operational needs while ensuring consistent data quality and analytical functionality across both industries is possible with the software.
GLOBAL EXPANSION AND CULTURAL ADAPTATION
VMC continues to expand its global presence, with a specific emphasis on high-growth regions such as Africa, Indonesia, India, Eastern Europe and Latin America, where a large demand for advanced asset management solutions arises from growing mining activities and infrastructure projects.
The firm has local teams offering multilingual support capabilities. However, cultural adjustment remains a continuing challenge in emerging markets as they transition from legacy manual systems to online platforms.
“We adapt training and user interfaces to local literacy and workflow styles,” Fernie said. “Regional teams help bridge gaps in communication, training and change management, ensuring smoother adoption.”
Main entry barriers in emerging markets include the absence of sound local technical support, the scarcity of internet infrastructure in geographically remote mining sites, the reluctance to change due to entrenched manual systems and administrative hurdles involving payment reliability and bureaucratic delays.
FUTURE TECHNOLOGY AND INDUSTRY TRENDS
Future software updates mirror industry-wide trends towards greater automation and the integration of artificial intelligence. On the horizon are planned improvements, including richer analytical dashboards, enhanced cloud analytics capabilities, mobile inspection tools with integrated image capture capabilities and AI-driven notification systems for predictive maintenance notifications.
As autonomous and electric cars increasingly penetrate mining fleets, VMC’s strategic emphasis on tyre and rim information, rather than vehicle powertrains, places the company well-positioned to meet emerging transportation technologies without necessitating drastic system architecture adjustments.
“enTIRE tracks data independently of vehicle type, so electric vehicles are managed the same as diesel fleets,” Fernie explained. “Our focus is on tyre and rim data accuracy – not the powertrain.”
INDUSTRY CHALLENGES AND MARKET OUTLOOK
The tyre management industry faces ongoing challenges related to data accuracy and actionable insights. “The industry’s main challenge is accurate and actionable data,” Fernie observed. “Successful tyre management operations start with accurate data collection, management and transparent reporting.”
Supply chain disruptions have strengthened demand for VMC’s services as tyre shortages heighten the importance of lifecycle extension and predictive maintenance. “Our strongest growth has been when there have been tyre shortages and clients want to extend their current tyre life as much as possible,” Fernie noted.
For Fernie, who brings over 30 years of experience in tyre management software development to the industry, VMC’s continued success validates the strategic decision to remain independent in an increasingly consolidated market. “Just ‘being there’ and remaining independent will always attract customers from non-independent tyre management systems over time,” he said, expressing confidence in the company’s long-term competitive position.
In an industry where margins of operation are crucial and safety must not be compromised, VMC has established a highly profitable niche by addressing complex problems that most individuals never even consider – until a USD 50,000 tyre blows on a distant mining operation thousands of miles from the nearest replacement. For mining operators globally with billions of dollars in mobile equipment, that specialised expertise and uncompromising independence have been worth their weight in gold.
Comerio Ercole Participates In Oerlikon Nonwoven Event
- By TT News
- August 12, 2025
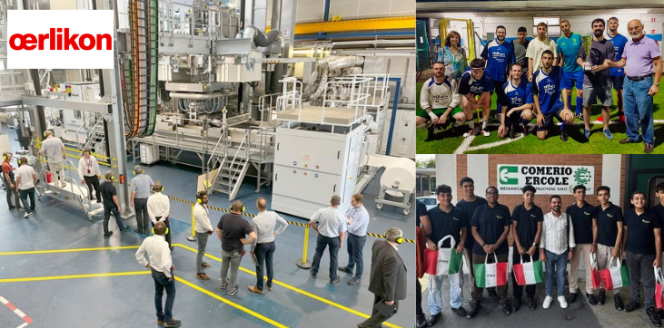
Comerio Ercole participated in Oerlikon Nonwoven's exclusive Technology Centre Open House in Neumünster, Germany, on 2-3 July 2025. The event attracted over 50 industry professionals for interactive demonstrations and technical discussions on nonwoven manufacturing innovations.
As a key partner, Comerio Ercole presented its latest calendering solutions, highlighting their role in enhancing finishing processes through precision engineering and energy-efficient designs. The company emphasised its collaborative approach in developing customised systems tailored to industry needs.
Attendees observed live demonstrations of Oerlikon Neumag's hydro-charging technology for meltblown media and spunbond production lines for specialty materials. Partner companies contributed additional insights across the production chain, from fibre treatment to final winding solutions.
The event showcased how strategic partnerships drive progress in nonwoven manufacturing, with Comerio Ercole demonstrating its commitment to integrated, innovative production technologies.
The Comerio Ercole team said, “We believe that delivering value to our customers means not only providing advanced machines but also being part of a well-coordinated and forward-thinking network.”
BendPak Launches Ranger RB30T Hybrid Wheel Balancer For Truck And Bus Wheels
- By TT News
- August 07, 2025
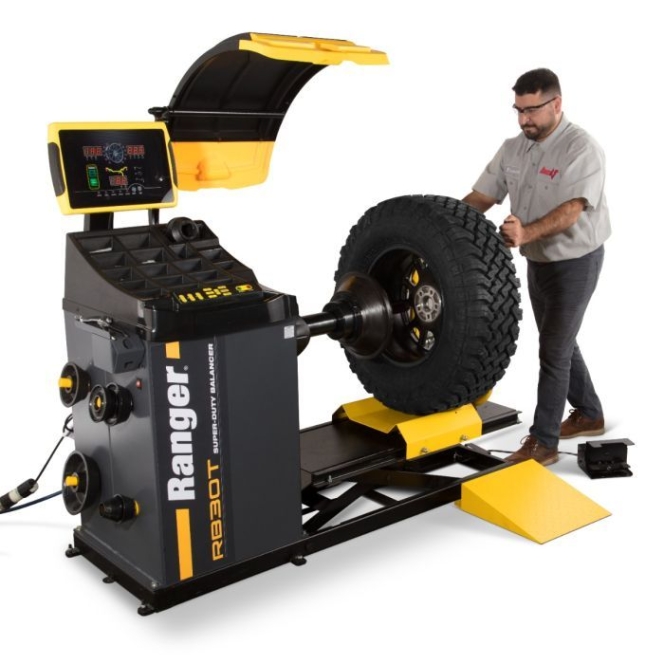
Designed to tackle the largest truck and bus wheels while maintaining precision for passenger vehicles, the RB30T Hybrid Wheel Balancer from Ranger (a BendPak division) delivers power and versatility. Switching between heavy-duty and light-duty applications is effortless, requiring just a button press. Its integrated pneumatic wheel lift enhances safety and ergonomics by minimising manual handling and reducing injury risks.
Capable of balancing wheels for buses, semi-trucks, OTR vehicles, light trucks and cars, the RB30T ensures fast, accurate results without recalibration. Its re-engineered platform supports wheels up to 330 lbs (approx. 150 kg), 49.25 inches in diameter and 20 inches wide, with rapid cycle times – seven seconds for car wheels and around 20 seconds for full truck assemblies. At its core, the Ranger Drive-Check system uses advanced 64-bit processing and quartz piezoelectric sensors to detect even the slightest imbalances across multiple axes. This smart technology simulates real-world driving conditions, identifying vibrations before they become road issues and automatically recommending optimal corrections.
Built for durability, the RB30T features a ribbed nylon-fibre drive belt, counter-weighted flywheel system and a three-phase motor with solid-state phase conversion for smooth, high-torque operation under heavy loads. The balancer comes ready to use with a commercial mounting kit, including cones and adapters, while its spacious top tray and side shelves keep wheel weights and tools organised for efficient workflow.
Available as a standalone unit or with the Ranger Select package – which includes professional installation and training – the RB30T is a robust solution for shops handling diverse wheel balancing needs.
Sean Price, Director of Product Development, said, “The new RB30T wheel balancer can do it all. Its versatility makes the RB30T a great choice not just for heavy-duty fleets and repair garages but also for high-volume tyre shops and mixed fleets.”
Bridgestone Launches First Aircraft Tyre Tracking System With Cebu Pacific
- By TT News
- August 04, 2025

Bridgestone has officially rolled out its proprietary aircraft tyre management system “easytrack” in collaboration with Cebu Pacific Air, marking the first deployment of the solution by a commercial airline.
The system, launched in April 2025, uses QR codes and a smartphone app to track aircraft tyres across the supply chain—replacing Cebu Pacific’s manual, paper-based process.
“As Cebu Pacific continues to expand its operations, it's essential that we invest in smart solutions that enhance efficiency and reduce manual workload,” said Shevantha Weerasekera, Vice President, Engineering & Fleet Management at Cebu Pacific. “Partnering with Bridgestone to implement the ‘easytrack’ system has enabled us to significantly improve our tyre management processes significantly, ensuring greater accuracy, safety, and productivity across our operations.”
Bridgestone said the system has halved labour time for inventory management and achieved full tyre tracking accuracy after verification trials at Cebu Pacific’s warehouses, MROs, and maintenance bases.
“As a value co-creation partner, we have proposed solutions tailored to on-site operations based on learnings and insights gained from Cebu Pacific Air’s frontline operations,” said Arata Tomita, Director, Global Aviation Tire Solutions Business Division at Bridgestone. “We are very pleased that the official implementation of ‘easytrack’ has contributed to the improvement of operational accuracy, safety, and productivity.”
Bridgestone said the move aligns with its “Bridgestone E8 Commitment,” with a focus on enhancing efficiency and ecology by supporting sustainable tyre practices and operational productivity.
Comments (0)
ADD COMMENT