Covestro Completes Modernisation Of Dormagen TDI Plant
- By TT News
- March 21, 2025
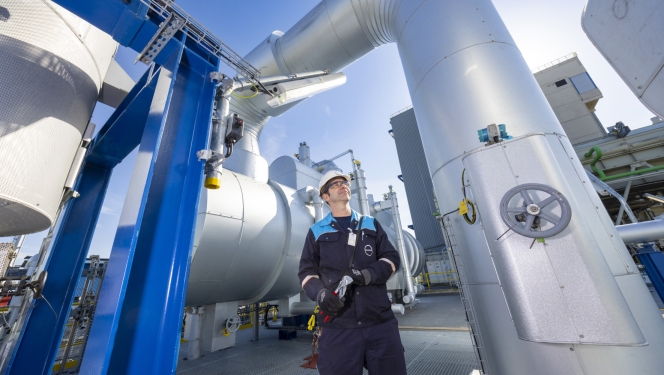
Covestro has successfully completed the modernisation of its TDI (Toluene Diisocyanate) plant in Dormagen, Germany. The facility was formally commissioned by Covestro as it unveiled its new goal of boosting production energy efficiency during an event attended by over 60 visitors from the commercial, political and personnel sectors, including Oliver Krischer, North Rhine-Westphalia Environmental Minister.
By using 80 percent less energy than traditional methods, the modernised plant reduces CO2 emissions by 22,000 tonnes annually. This is made possible by a new reactor that is over 20 metres high and weighs more than 150 tonnes. It produces steam using the reaction energy that is created. Covestro began the modernisation process in the summer of 2023. Over 3.5 kilometres of new pipes, over 14 kilometres of cables and hundreds of new pieces of equipment, valves and monitoring devices were placed throughout the facility. Through its federal subsidy programme for energy and resource efficiency, the Federal Ministry for Economic Affairs and Climate Action (BMWK) has provided assistance for this modernisation.
The company targets a 20 percent reduction in CO2 emissions from energy use per tonne of product by 2030 compared to 2020, underlining energy efficiency as a key component in reaching operational climate neutrality by 2035. With a 300,000-tonne-per-year capacity, the Dormagen TDI facility stands as a shining example of how to successfully convert current manufacturing facilities to be more energy-efficient.
Dr Philip Bahke, Head of the North Rhine-Westphalia Site Network, said, "The successful completion of this project shows that climate protection and competitiveness can go hand in hand. The modernised plant sets new standards in energy efficiency and underlines our path toward climate-neutral production. In light of persistently high energy costs, the project significantly strengthens the competitiveness of TDI production in Europe. My special thanks go to the entire project team, who professionally implemented this complex modernisation during ongoing operations."
Dr Christine Mendoza-Frohn, Head of Sales Performance Materials for the EMEA and LATAM regions, said, "In Dormagen, we operate Europe's largest TDI production plant. With the successful modernisation, we can now offer our customers TDI with an even better carbon footprint. This supports our customers in achieving their own sustainability goals and strengthens our position as a reliable partner for climate-neutral and circular solutions."
Cleaner Pyrolysis
- By Sharad Matade
- July 04, 2025
Pyrolysis has long been associated with pollution and inefficiency, particularly in developing markets where outdated methods dominate. However, technological advancements and a stronger push for circularity are transforming this perception. HF Group, through its subsidiary Farrel Pomini and WF Recycle-Tech, is at the forefront of this shift, introducing a continuous pyrolysis system that promises cleaner and more efficient tyre recycling. Unlike traditional batch processing, its technology ensures consistent output, better resource recovery and reduced emissions.
Pyrolysis has always been considered to be a dirty business. However, with the changes in technology and the increasing hunt for circularity across the tyre industry, businesses are attempting to redefine the age-old tyre recycling process and remove the malice associated with it.
Farrel Pomini is one such entity with the HF Group that is attempting to make pyrolysis cleaner. WF Recycle-Tech, established in 2013, started commercial operations in 2022 with selling its first pyrolysis unit in 2024, slated to be operational in 2026.
Speaking to Tyre Trends, President Paul Lloyd said, “Farrel Pomini’s core business lies in supplying processing equipment for the plastics and petrochemical industries. While its continuous mixer can be used for rubber applications, it is primarily designed for plastic masterbatches and compounds. The company operates across multiple divisions with its plastics compounding equipment focusing on niche applications for highly filled and temperature-sensitive materials. Although the plastics market is significantly larger than the rubber sector, Farrel Pomini targets specialised segments within it. Expanding its footprint in sustainability, the company has developed recycling systems for both plastics and rubber. The end-of-life tyre recycling solution was developed in collaboration with its group company, WF Recycle-Tech.”
Tyre pyrolysis has long been regarded as a polluting industry, particularly in developing countries where unregulated plants often operate at night to evade environmental scrutiny. In markets like India, many such facilities shut down due to non-compliance, reinforcing the industry’s reputation as a ‘dirty business’.
Lloyd further explained, “In Europe, the focus is shifting towards sustainability, driving innovation in pyrolysis technology. Traditional methods relied on large kilns, where tyres were burned with external heat over extended periods. The process was inefficient, labour-intensive and environmentally damaging, requiring extensive manual cleanup.
HF Group has taken a different approach, developing a continuous pyrolysis system that eliminates these challenges.”
Instead of batch processing, the system ensures a constant flow of material, allowing for the controlled capture of gases, liquids and solid outputs. The process begins with pre-grinding tyres into metal-free rubber crumb (6–20 mm), which is then fed into the machine via a hopper. Operating at a capacity of 1,500 kilogrammes per hour, the system requires only continuous material input while automatically managing output streams including recovered oil and gas.
Apropos to the pain points that the company wanted to address, he noted, “Over the past decade of developing this solution, several key learnings and priorities emerged. First and foremost, the goal was to create an efficient pyrolysis system that could consistently process tyre waste at an industrial scale. Second, the decision to develop a continuous rather than batch-based system was fundamental as continuous pyrolysis offers greater consistency, scalability and efficiency. Third, integrating a continuous mixer in the pre-processing stage became a major focus as it significantly improved the homogeneity and quality of the output materials. Finally, optimising the recovered output, particularly recovered carbon black, became the primary objective. Initially, the project was focused on tyre-derived oil (TDO), but as the market evolved, the emphasis shifted to producing the highest-quality rCB, aligning with upcoming ASTM standards and stringent industry requirements.”
By integrating advanced processing controls, the solution ensures cleaner, more efficient pyrolysis, positioning itself at the forefront of sustainable and cleaner tyre recycling.
THE OUTPUT
HF Group’s expertise in mixing technology creates a natural synergy between its traditional business and its expansion into tyre recycling. While the company is known for its tyre curing and rubber mixing solutions, it also has a plastics mixing division; this same mixing technology plays a crucial role in its pyrolysis process.
The recycling system starts with tyre crumb, which is fed into a high-shear Farrel Continuous Mixer originally designed for plastics processing. The mechanical shear heating raises the temperature of the material to 330 degrees Celsius. This ensures uniform heating before the material enters the pyrolysis chamber, where temperatures increase to between 520 degrees Celsius and 580 degrees Celsius. The continuous system eliminates inefficiencies seen in traditional batch pyrolysis, where prolonged heating cycles lead to higher energy consumption and inconsistent output.
Material recovery is a key advantage of the system. For every tonne of tyre crumb processed, approximately 50 percent is converted into pyrolysis oil, yielding 550–570 litres. Around 40 percent becomes recovered carbon black (rCB), a critical raw material that can replace virgin carbon black in industrial applications. The remaining 10 percent is gas, which can be used to power the system, further improving energy efficiency.
Beyond throughput, the system’s design significantly reduces overall energy demand. Mechanical shear heating minimises reliance on external thermal energy, while the continuous process prevents heat loss and optimises fuel efficiency.
Additionally, rCB from the pyrolysis process requires 60–70 percent less energy to refine, further enhancing sustainability.
“Pyrolysis fundamentally relies on heat and time in the absence of oxygen. Under these conditions, tyres thermally degrade, breaking down into vapour, which is condensed into oil and a solid residue, which is now widely used as recovered carbon black (rCB). This output can be further refined for industrial applications, creating a circular economy within the rubber industry,” explained Lloyd.
CHALLENGING INTEGRATION
The primary challenge for tyre manufacturers in adopting rCB is achieving performance characteristics comparable to virgin carbon black. Similarly, tyre pyrolysis oil must meet stringent quality standards to serve as a feedstock for high-value applications beyond just fuel. The company’s continuous pyrolysis system addresses these concerns by enhancing the quality and usability of both outputs.
“In the case of tyre pyrolysis oil, if used as a fuel, the calorific value may vary slightly, but it remains a viable option. However, its greater potential lies in serving as a feedstock for sustainable carbon black or even virgin carbon black production. The consistency of the oil’s composition determines its suitability for high-end applications, making process control a critical factor,” noted Lloyd.
He added, “For rCB, higher quality directly translates into increased usability across different applications. While rCB will never completely replicate virgin carbon black, superior grades enable a higher substitution rate. In some cases, a high-quality rCB can replace up to 30 percent of virgin carbon black, whereas lower-quality alternatives may only allow a 15 percent substitution. This increased usability not only enhances sustainability but also raises the material’s commercial value.”
HF Group’s rCB, produced through its WF Recycle-Tech process, has been extensively tested across multiple industries. It has demonstrated strong performance in plastics masterbatch applications, technical rubber goods and even tyre manufacturing. One major tyre producer has already validated its suitability for substitution in new tyres, underscoring its industry acceptance.
A key differentiator of the process lies in its patented two-stage pyrolysis system. While continuous pyrolysis itself is well established, HF Group’s innovation stems from its integration of a high-shear Farrel Continuous Mixer in the first stage.
This approach ensures uniform heating, eliminates direct heat exposure and optimises the pyrolysis reaction in the second stage. The result is a more efficient process that yields higher-quality recovered carbon black and cleaner tyre pyrolysis oil.
PERSEVERING THROUGH LIMITATIONS
The primary limitations of the system, Lloyd noted, revolve around scalability, operational efficiency and material consistency. The current processing capacity of 1,500 kilogrammes per hour is relatively low. Scaling up production rates while maintaining efficiency and reliability is an ongoing challenge. The key challenge is ensuring long-term operational stability and optimising run times.
Another significant factor is feedstock variability, particularly in markets like India, where used tyres from different sources such as passenger cars, trucks and buses are often mixed without segregation. The ideal scenario would involve processing a uniform type of tyre with a consistent rubber composition, but in reality, recycling operations must work with what is available.
“There are two main approaches to addressing this viz-a-viz meticulous sorting, which ensures consistency but is time-consuming and costly, or strategic blending, which creates a stable output by balancing material variations. The current system has been designed to handle diverse feedstocks without sorting, using a consistent blend of tyres to produce a predictable output,” said Lloyd.
In the long term, technological advancements such as artificial intelligence or tracking mechanisms for tyres could enhance sorting processes, making recycling operations more efficient. However, for now, the focus remains on refining the system to handle real-world feedstock conditions while delivering high-quality outputs. The continuous processing system also provides flexibility to adjust parameters and optimise results, making it a robust solution even in environments where feedstock quality is unpredictable.
MARKET TALK
The return on investment for pyrolysis systems is quite favourable, but it carries risks, especially in the early stages. A well-managed system operating efficiently for 6,000–7,000 hours per year, with a stable feedstock supply and consistent product quality, can generate strong financial returns, explained the executive.
However, challenges arise if there are interruptions in material supply, equipment downtime or fluctuations in product quality. These factors introduce uncertainty, which can make securing financing more difficult. That said, the market for TDO and rCB is growing, providing ample opportunities for revenue. Companies that can differentiate its output and meet quality standards can command premium prices, further improving ROI.
The market focus for HF Group’s advanced pyrolysis solutions primarily includes recyclers looking to add more value to their processes, material users such as tyre manufacturers and technical rubber companies seeking sustainable raw materials and new businesses emerging in response to industry needs.
“In the US and Europe, there is a growing entrepreneurial push to bridge the gap between traditional recycling and the sustainability requirements of the tyre industry. However, in markets like India and other parts of Asia, the challenge lies in shifting perceptions. Many existing pyrolysis operations use older-generation systems. The transition to modern, cleaner and more efficient systems requires education, proof of performance and financial support. Despite these challenges, India remains a strong market for HF, as the industry values high-quality technology and is willing to invest in the best solutions once the benefits are clearly demonstrated,” informed Lloyd.
Over the next five years, the company’s primary goal is to establish a proven track record with the first full-scale pyrolysis system, demonstrating its performance, reliability and efficiency. Once this is achieved, the focus will shift to helping potential customers secure financing by reducing perceived risks, making it easier for them to invest in the technology.
Alluding to the next phase of development, Lloyd informed, “The next phase of development focuses on three main areas. The first priority is industrialising the system to ensure it operates efficiently, consistently and reliably over long production cycles. This transition from pilot-scale to full-scale manufacturing is where HF Group’s expertise in engineering advanced processing equipment comes into play. Secondly, efforts are underway to further refine the pyrolysis reaction to enhance output quality and efficiency. Lastly, ongoing research and development is focused on post-processing improvements, particularly the removal of ash from recovered carbon black to increase its usability in high-performance applications.” n
Rubber Tappers: Renew Group Insurance By July
- By TT News
- July 04, 2025
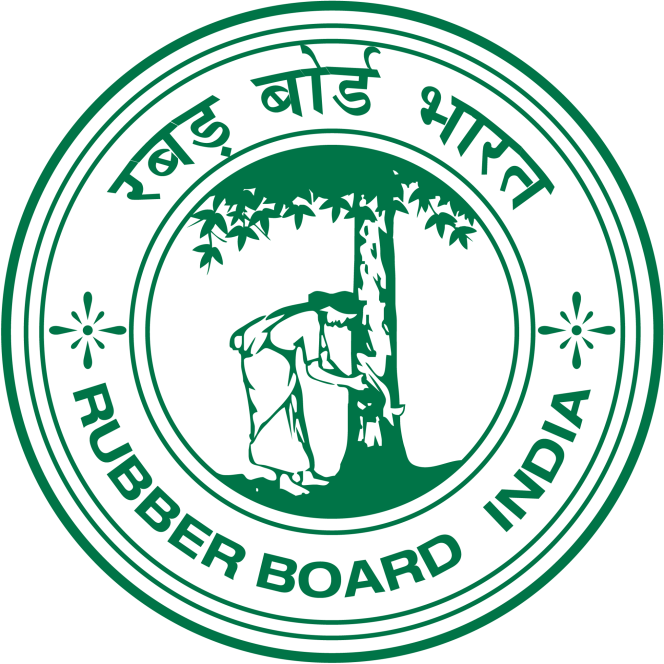
The Rubber Board has announced that rubber tappers enrolled in the Group Insurance Cum Terminal Benefit Scheme, introduced in 2011-12, can renew their policies until 15 July 2025.
Policyholders are required to submit their current year’s contribution at their respective Rubber Board Regional Office. The scheme provides a coverage of INR 100,000 for natural death and up to INR 500,000 in the event of accidental death. A renewal notice has been dispatched to all members, but those who have not received the communication may treat this announcement as an official reminder.
Such individuals should promptly contact their nearest Rubber Board Regional Office to complete the payment process and ensure uninterrupted coverage. The Assistant Director (Publicity) has urged all eligible members to adhere to the deadline to avoid discontinuation of benefits.
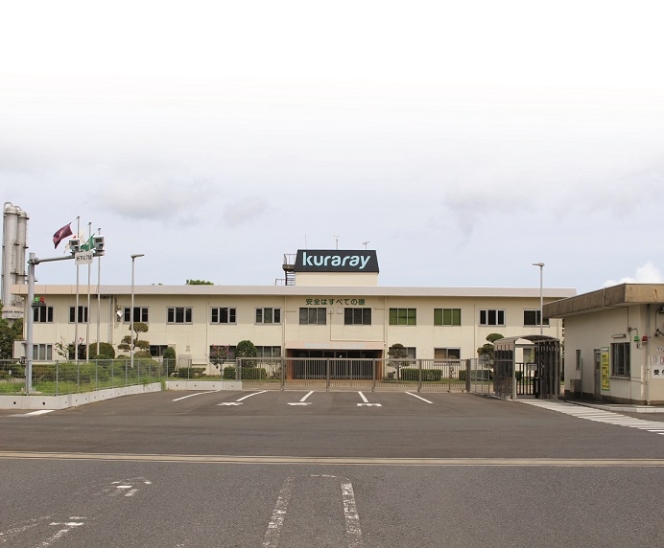
The most basic difference between an electric vehicle (EV) and internal combustion engine (ICE) tyre is that the former demands lower rolling resistance, quieter tread patterns and higher load bearing capacity. While there have been innovations within the tyre industry to meet the current demand for EV tyres, at the molecular level, research and development continues to achieve enhanced compound efficiency as tyre mixtures are complex.
As electric vehicles redefine performance benchmarks, tyre technology is undergoing a molecular-level overhaul. While the industry has focused on rolling resistance, noise reduction and load capacity, Japan’s Kuraray is pushing the boundaries deeper into the chemistry of rubber itself. By integrating silane-functionalised liquid rubbers into natural rubber-silica systems, the company aims to resolve longstanding formulation challenges. These innovations not only offer measurable improvements in abrasion resistance and wet grip but also open the door to broader adoption of sustainable materials in EV tyres. Kuraray’s work signals a strategic shift towards more efficient, adaptable and environmentally aligned tyre compounds.
Japan-based chemicals manufacturer Kuraray has dismissed all odds to achieve a more efficient molecular chemistry in tyres with its silane-functionalised liquid rubbers. In an earlier issue, Tyre Trends had reported how the company’s silane-modified rubber marked a major leap in tyre technology as it enhanced polymer interaction within the tyre, especially in natural rubber and silica-based formulations.
Coming to the present, its silane-functionalised liquid rubbers offer the reduction of rolling resistance (RR) and the resulting compound shows excellent balance of low RR, abrasion resistance and wet grip performance.
Speaking to Tyre Trends exclusively on the development, Technical Service Engineer for Quality and Product Development Department, Elastomer Division, Kuraray Co., Naoto Takahashi, divulged, “We propose to incorporate natural rubber (NR) for silica-based PCR treads. NR is preferable for its high strength and from the viewpoint of sustainability. However, the combination of NR and silica has typically been considered unusual as compounds for PCR treads. One of the reasons is that NR and silica have poor interaction, which causes decrease of physical properties.”
“Our silane-functionalised liquid rubbers can react with silica in the mixing stage and with NR in the vulcanisation stage. Using this technology, NR or silica-based compounds have been proven to have an excellent balance of lower RR and competitive abrasion resistance and wet grip compared to typical styrene-butadiene rubber, butadiene rubber and silica compounds. So we believe it has the potential for EV tyres, which require these properties,” he added.
Furthermore, using silane-functionalised liquid rubber in tyre manufacturing offers several advantages. Firstly, it provides a plasticising effect during the mixing stage, leading to lower torque and electricity consumption.
Secondly, the improved rolling resistance itself contributes to the sustainability goals by extending the driving range of EVs. Long-range EVs significantly reduce carbon dioxide emissions compared to fossil fuel-powered vehicles. This helps mitigate global warming and other climate changes. In addition, EVs with extended range reduce the burden on charging infrastructure and promote efficient energy use. Less frequent charging means reduced strain on the power grid.
Additionally, the improved performance of NR and silica compounds sheds light on the utilisation of NR, which is a kind of sustainable material. “We believe this technology could expand the potential of NR. If you are considering using more NR in your products, then this type of liquid rubber could be useful,” added Takahashi.
MIXING THE MIXTURE
Typically, it has been said that conventional silane coupling agents have poor reactivity with NR. This is not the case for silane-functionalised liquid rubbers. The liquid rubbers react with silica at the mixing stage by hydrolysis and condensation, in the same manner as silane coupling agents. As a result, the silica would be surrounded by hydrophobic liquid rubber chains. This helps silica to disperse well in the rubber matrix.
In the subsequent stage of vulcanisation, the reaction of liquid rubber chains and NR occurs. This forms bonds between two types of rubbers, effectively resulting in reinforcement of silica-NR interaction.
“We believe that these mechanisms contribute to maximising the potential of NR and silica combination,” said Takahashi.
The molecular weight of rubber is another key factor in determining the characteristics of liquid rubbers, alongside the glass transition temperature and monomer components.
Explaining how the molecular weight range of Kuraray’s liquid rubbers affect its compatibility and performance in tyre applications, the executive said, “Our liquid rubbers’ molecular weight range is strategically positioned between typical plasticisers and solid rubbers, ensuring an optimal balance of enhanced processing and physical properties.”
“Each grade’s molecular weight is precisely controlled and tailored to specific purposes and applications. Generally, liquid rubbers with lower molecular weights offer superior compatibility with other ingredients, while those with higher molecular weights provide better physical properties. Interestingly, the viscosity of liquid rubber alone does not determine the processability of compounds. We are glad to support you in selecting the ideal grade of liquid rubber to achieve your objectives,” he added.
He also noted that liquid rubbers have a low tendency to bleed out as a plasticiser because of their higher molecular weight and ability to be vulcanised. The low migration property directly affects the life span of the tyres.
Additionally, the improved abrasion resistance compared to traditional plasticisers also offers the long-term liability of tyres. “Wear particle is one of the biggest issues in today’s tyre industry because it has been recognised that it has a severe impact on the environment. The new regulation to handle this matter has been under discussion for a long time. Our silane-functionalised liquid rubbers would offer the solution to these challenges,” noted Takahashi.
COMPETITIVE EDGE
One of the characteristics of the material is its narrow molecular weight distribution. This provides the benefit of suppressing reduced physical properties due to the low molecular weight fraction. Another is that it has functional groups grafted onto the polymer chain. These functional groups seem to have different reactivity compared to other types of modification.
These features have a positive effect on the storage stability and other performances as tyres. The company highlighted that it has already found that the material would not deteriorate so much for 1-2 years in a bulk container under air.
Besides, the silane-functionalised liquid rubber technology is applicable to various types of tyres including winter and all-season tyres, and high-performance tyres. It is particularly beneficial in improving the dispersion of silica fillers, reducing compound viscosity and enhancing overall tyre performance. This technology helps achieve a balance between grip, low RR and abrasion resistance, making it suitable for a wide range of tyre applications.
Considering the characteristics of the material, another application of this type of material is TBR. Most TBR tyres use NR and carbon black (CB) compounds with less or no oils. However, using silica in place of CB in TBRs is getting more and more attention to achieve the high level of rolling resistance and wet grip performance. Here emerges the problem of NR and silica combination. As mentioned above, the silane-functionalised liquid rubbers would act as the effective additive for these kinds of compounds.
Commenting on the role of the liquid rubbers in enhancing wet or ice grip performance on winter tyres, Takahashi explained, “We have two types of silane-functionalised liquid polybutadiene with relatively higher glass transition temperature (Tg) and lower Tg. Initially,
we only commercialised the former one. However, in response to customer demand, we have developed another grade with lower Tg and are now fully equipped to mass-produce.”
“Liquid rubbers with lower Tg provide flexibility to the compounds even at low temperatures, which is particularly beneficial for the ice-grip performance of winter tyres. This flexibility ensures that the rubber remains pliable and maintains good contact with icy surfaces, enhancing traction and safety. Since the compound Tg is also highly affected by other components such as solid rubbers, plasticisers and resins, we think that our product lineup with different Tg offers freedom of choice for users’ compound formulation,” he added.
MEETING DEMANDS
The company continuously spoke with tyre manufacturers during the development of its liquid rubber. “We have instruments in our laboratory for measuring not only compound properties but also tyre performances such as wet grip and abrasion resistance. This allows us to have close and detailed technical communication with our customers,” said Takahashi.
He added, “The wet grip performance is usually expressed by the value of tanδ at 0 deg.C as an index from the viscoelasticity measurement. But the actual compound’s grip performance often shows a different result from the viscoelasticity. We have equipment to measure the friction coefficient of compounds on wet and icy surfaces, allowing us to minimise the discrepancy between viscoelasticity and grip performance.”
Alluding to how the use of silane-functionalised liquid rubber in EV tyres aligns with current trends and future directions in tyre technology, he said, “We recognise the growing trend towards sustainability as well as the importance of reducing rolling resistance and wear particles. Here, we recommend using NR more to address these issues. While the combination of NR and silica may not be the conventional choice for PCR tread compounds, we believe that our innovative approach demonstrates the potential of this formulation. The use of silane-functionalised liquid rubber offers the excellent dispersion and reinforcement of NR and silica compounds, paving the way for the solution to address future challenges in tyre technology.”
Takahashi indicated that the silane-functionalised liquid rubber can play a role in reducing the carbon footprint of tyre production. The key driver, he explained, is a measurable drop in rolling resistance, which translates into lower fuel consumption for internal combustion vehicles and reduced electricity use in EVs.
The firm also highlighted its broader sustainability efforts, noting that its liquid rubber plant is ISCC Plus-certified. From this year, Kuraray has started producing sustainable materials under a mass-balance approach – an initiative that includes its latest silane-functionalised grades, though the product range is still expanding.
On managing cost-performance trade-offs, he acknowledged that liquid rubber typically commands a higher price than traditional plasticisers. However, the benefits tend to supplement the cost.
The company pointed to challenges like dispersing high-surface-area silica in tread compounds – an area where its liquid rubber grades can provide a processing advantage. It also emphasised the potential of NR and silica combinations, made feasible with its silane-modified products, as an example of how formulation innovation can justify the premium.
Kuraray’s silane-functionalised liquid rubber represents a critical inflection point for tyre formulation – technically and environmentally. By enabling stable silica dispersion in natural rubber and forming durable crosslinks during vulcanisation, it addresses both performance and sustainability imperatives.
While the cost remains a consideration compared to traditional plasticisers, the material’s added value, such as reduced energy use, lower rolling resistance and extended tyre life, could redefine return on investments calculations for manufacturers. Its compatibility with evolving regulations on wear particles and carbon footprint reduction positions it not just as an additive but as a strategic material. The challenge ahead lies in scaling adoption without compromising economic efficiency.
Apollo Tyres Hungary Plant Gets ISCC+ Certification
- By TT News
- July 01, 2025
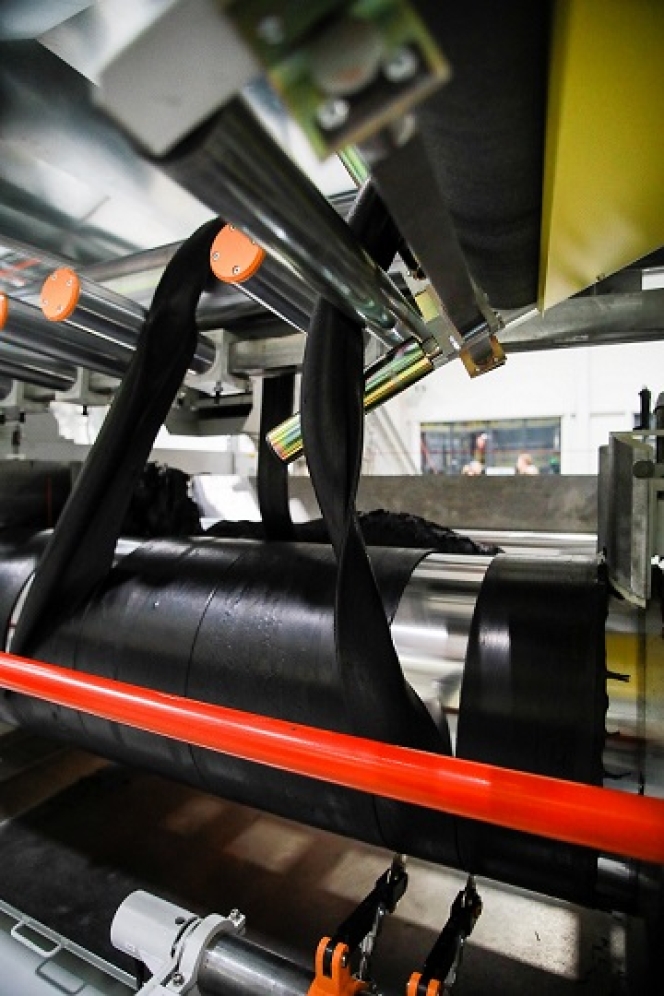
Apollo Tyres, one of the leading tyre manufacturers in the world, has added another feather to its cap, with its Hungary production plant bagging the International Sustainability and Carbon Certification Plus (ISCC+) certification.
The globally recognised ISCC certification is a voluntary programme that recognises companies for their sustainability and carbon reduction initiatives. Apollo Tyres, by achieving ISCC+ certification, has been recognised for not only meeting the stringent sustainability standards but also for its responsible production in the industry.
Apollo Tyres Secures Gold Medal In 2025 EcoVadis Sustainability Rating
As part of its commitment, the tyre maker continues to focus on monitoring and verifying sustainability practices across its processes and supply chain.
Rajeev Kumar Sinha, Chief Manufacturing Officer, Apollo Tyres, said, “This certification is an important step forward as we continue to integrate sustainability deeply into our operations. It aligns perfectly with our ambitious goal of incorporating 40 percent sustainable raw materials – including renewable and recycled input materials – into our products by 2030.”
Comments (0)
ADD COMMENT