Innovent Renewables Opens New Facility To Tackle ELT Issue In Northern Mexico
- By Gaurav Nandi
- January 13, 2025
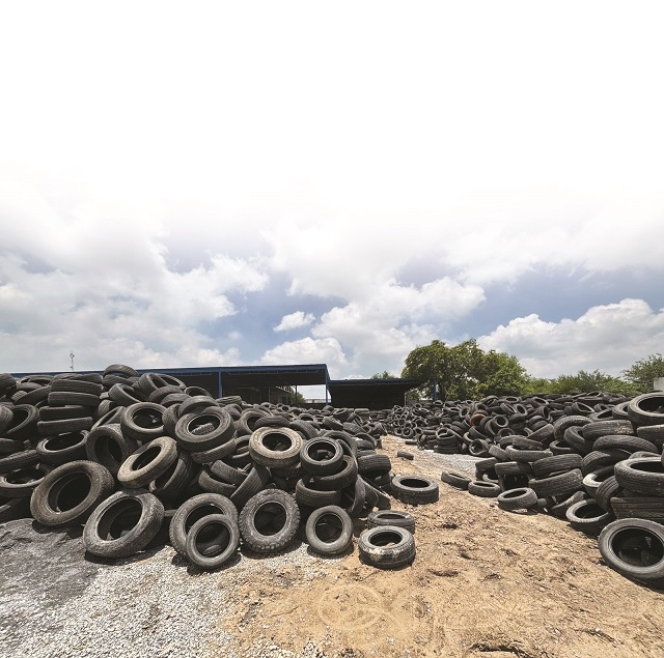
The pilot facility in Monterrey will initially convert 1 million end-of-life passenger tyres to recovered carbon black. Operations are slated to commence by the end of CY2024, while the company also has plans to add a second train in the future to double the capacity.
Northern Mexico has long struggled with the challenge of end-of-life tyre (ELT) disposal. Decades of improper waste management have led to an accumulation of over 20 million waste tyres, many of which are left in municipal dumpsites or landfills. These discarded tyres pose not only an environmental hazard but also a significant public health risk as they can become breeding grounds for mosquitoes and other disease-carrying pests.
Local governments have ramped up efforts to address this crisis, but the scale of the problem requires long-term, systemic solutions. Innovent Renewables’ new facility in Monterrey is poised to play a key role in this effort. The facility will transform waste tyres into valuable resources such as recovered carbon black and will help reduce landfill reliance, cut carbon emissions and provide a sustainable alternative to the traditional methods of carbon black production.
The pilot facility represents a significant milestone for the recycler as it sets out to address the growing environmental challenge of ELTs in the region. Initially slated to process 1 million waste passenger tyres annually, the facility will convert these tyres into high-quality recovered carbon black, oil and steel. With operations scheduled to begin by the end of calendar year 2024, the company is also looking ahead with plans to add a second processing train to double its capacity in the near future. This expansion marks a critical step in tackling the 20 million-plus tyres accumulated in Mexico’s northern areas while offering sustainable solutions for industries seeking to reduce their carbon footprints.
“This facility represents a vital step forward in addressing the enormous environmental burden posed by tyre waste in northern Mexico. We’re not only reducing waste but converting it into materials that industries can use in a circular and sustainable manner,” said Chief Executive Officer Vibhu Sharma.
Extracting value
The tyre recycling process based on pyrolysis begins with the shredding of end-of-life tyres, which are then fed into a main reactor where they undergo pyrolysis, a high-temperature process in the absence of oxygen.
This results in the breakdown of tyre material into pyrolysis gases, oil and recovered carbon black. The gases are recycled within the system for energy recovery or flared off, enhancing energy efficiency.
The pyrolysis oil is condensed and purified, followed by distillation into high-value chemicals for industrial applications. Meanwhile, recovered carbon black, a solid by-product, is processed through milling and polishing for reuse in manufacturing. This design demonstrates an energy-efficient method of converting waste tyres into valuable products such as fuel, chemicals and carbon black.
“Firstly, we have a proprietary continuous pyrolysis process that ramps up and cooks the tyres to decompose them in a particular way. We also use specially designed agitator to ensure uniform decomposition to oil and carbon black. This ensures higher surface area and quality of the RCB. We designed a proprietary polishing unit that crushes that RCB coming out of the reactor and then polishes it to remove metal oxides and silica. We have several equipment in place to capture steel particles in the RCB. The final product still has some amount of silica and metal oxides, but the purity and uniformity of the RCB is much higher,” said Sharma.
Addressing demand
As industries worldwide strive to meet decarbonisation goals, the demand for sustainable alternatives to carbon-intensive materials have surged. Recovered carbon black fits squarely into this trend, offering a viable option for companies looking to reduce environmental impact while maintaining performance characteristics.
Innovent Renewables’ order book reflects this growing interest. The company has secured letters-of-intent from several major tyre manufacturers as well as companies in the printing ink, rubber and paint sectors.
“Increasingly, companies are looking for sustainable solutions that allow them to reduce their carbon footprints without sacrificing the quality of the products. Our RCB gives them that opportunity. It’s a win-win for both industry and the environment,” said Sharma.
He added, “We see the Monterrey facility as just the beginning. As we prove the viability of our process and stabilise operations, we’ll be able to scale up production not just here in Mexico but potentially in other regions around the world that are dealing with tyre waste issues. There’s a huge global need for solutions like this.”
Sustainable vision
According to Sharma, the company’s goal is to provide a circular solution for industries that are serious about sustainability. “It’s not just about the recovered carbon black; we’re also helping companies reduce their reliance on virgin oil and steel by offering them high-quality, recycled alternatives. This allows them to achieve carbon credits and decarbonisation targets while contributing to a cleaner environment,” noted Sharma.
While tyres remain the primary focus, the company is already working to expand its applications into other industries by targeting sectors such as rubber gaskets, printing inks and paints to tap into new growth markets.
It is also finding ways to repurpose the other by-products of its pyrolysis process. The oil extracted from the tyres can be used as fuel or as a raw material for various industrial applications, while the recovered steel can be sold back to manufacturers, creating a fully circular model that maximises resource recovery and minimises waste.
“We’re proud to be part of the solution to one of Mexico’s most pressing environmental issues. But this is just the start. Our vision is to become a global leader in the circular economy, providing industries around the world with the materials they need to build a sustainable future,” Sharma concluded.
Apollo Tyres Hungary Plant Gets ISCC+ Certification
- By TT News
- July 01, 2025
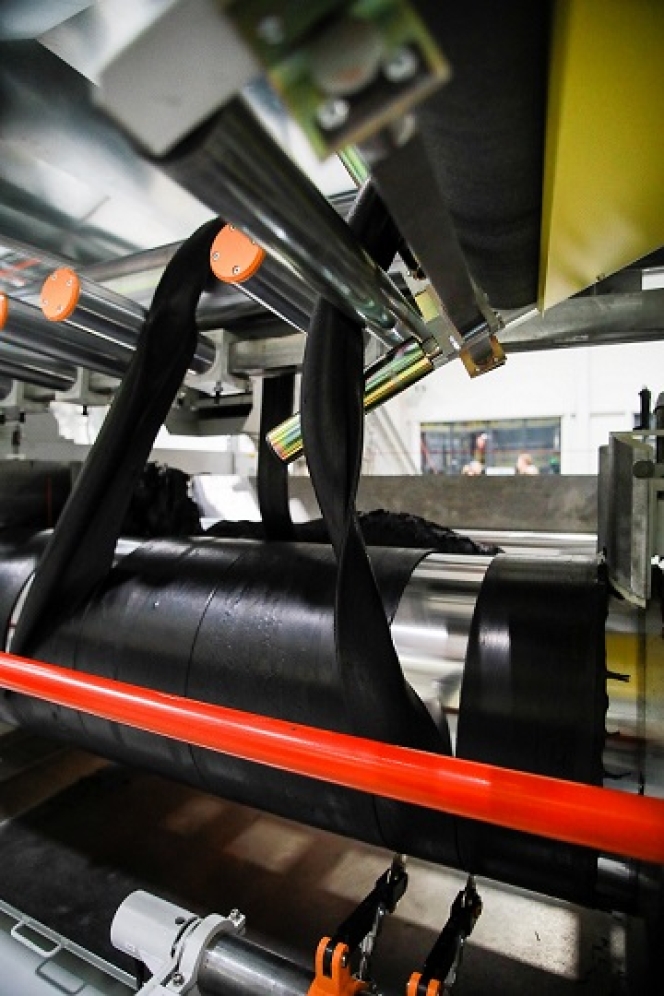
Apollo Tyres, one of the leading tyre manufacturers in the world, has added another feather to its cap, with its Hungary production plant bagging the International Sustainability and Carbon Certification Plus (ISCC+) certification.
The globally recognised ISCC certification is a voluntary programme that recognises companies for their sustainability and carbon reduction initiatives. Apollo Tyres, by achieving ISCC+ certification, has been recognised for not only meeting the stringent sustainability standards but also for its responsible production in the industry.
Apollo Tyres Secures Gold Medal In 2025 EcoVadis Sustainability Rating
As part of its commitment, the tyre maker continues to focus on monitoring and verifying sustainability practices across its processes and supply chain.
Rajeev Kumar Sinha, Chief Manufacturing Officer, Apollo Tyres, said, “This certification is an important step forward as we continue to integrate sustainability deeply into our operations. It aligns perfectly with our ambitious goal of incorporating 40 percent sustainable raw materials – including renewable and recycled input materials – into our products by 2030.”
- Kraton Corporation
- Kraton Sustainability Report
- Sustainability
- EcoVadis Platinum
- 2024 Nitto Supplier Sustainability Award
Kraton Corporation Publishes 2024 Sustainability Report
- By TT News
- July 01, 2025
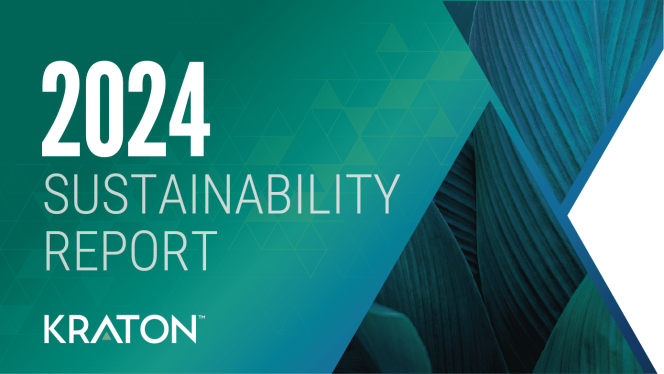
Kraton Corporation, a global leader in speciality polymers and biobased solutions derived from pine wood pulping co-products, has published its 2024 Sustainability Report, ‘Innovating with Purpose’. The report showcases the company’s advancements in climate action, circular product innovation and value chain partnerships, reinforcing its commitment to sustainable solutions.
Key achievements include a 41 percent reduction in Scope 1 & 2 greenhouse gas emissions since 2014 and a 35 percent decline in emissions intensity. Kraton also maintained its EcoVadis Platinum rating for the fourth consecutive year and received the 2024 Nitto Supplier Sustainability Award. Strategic initiatives such as a Double Materiality Assessment and a USD 35 million investment in biorefinery upgrades at its Panama City facility further demonstrate Kraton’s sustainability leadership.
The company enhanced transparency by expanding life cycle assessment (LCA) data to cover nearly 90 percent of its product portfolio, helping customers evaluate environmental impacts. Additionally, Kraton launched a data excellence program to streamline ESG reporting and refine decarbonisation goals.
Aligned with GRI, SASB, UN Global Compact and TCFD frameworks, the report reflects Kraton’s sustainability pillars: Being Reliable Partners, Preserving Planet and Empowering People. These efforts underscore Kraton’s dedication to driving meaningful progress across its operations and industries.
Marcello Boldrini, Kraton Chief Executive Officer, said, “2024 marked a pivotal year in Kraton’s sustainability journey. We turned ambition into action, significantly reducing our Scope 1 and 2 emissions by 41 percent from our 2014 baseline and earned an EcoVadis Platinum rating for the fourth consecutive year. We accelerated our decarbonisation strategy, advanced biobased innovation and partnered with customers such as WJ Group and Henkel to help address global sustainability challenges. As demand for sustainable chemicals grows, our focus remains on developing the right solutions, fostering strong partnerships and cultivating the culture necessary to lead this transformation responsibly and competitively.”
Rogier Roelen, Kraton Chief Sustainability Officer, said, “We have established new processes to scale credible, data-driven sustainability across our business. In 2024, we enhanced our ESG reporting through a data harmonisation programme and completed a Double Materiality Assessment to better align with the Corporate Sustainability Reporting Directive (CSRD). We also expanded our Life Cycle Assessment (LCA) data to cover almost 90 percent of our product portfolio, providing customers with greater transparency into the environmental impact of our products. These efforts reinforce our ability to identify where we can make the most impact and support more informed, strategic decision-making.”
Michelin Collaborates With Murfitts For Tyre Pyrolysis Plant
- By TT News
- July 01, 2025
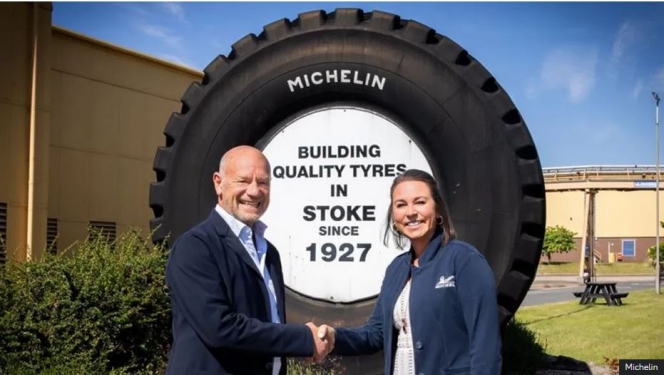
Murfitts Industries, the UK’s largest tyre recycling company, has unveiled plans for a state-of-the-art materials recovery facility at Michelin’s Stoke-on-Trent tyre plant. This groundbreaking initiative will transform end-of-life tyres into valuable resources while significantly reducing the site’s environmental footprint. The advanced recycling process will recover energy to power Michelin’s manufacturing operations, cutting annual CO₂ emissions by 1,500 tonnes. Additionally, the facility will produce high-quality recovered carbon black (rCB) and tyre pyrolysis oil (TPO), supporting sustainable material production.
Under the agreement, Michelin will supply Murfitts with 12,500 tonnes of discarded tyres annually – equivalent to 1.35 million car tyres. This capacity far exceeds local demand, with the plant able to process the equivalent of two tyres from every car registered in Stoke-on-Trent and Staffordshire. Slated for completion by late 2026, the facility will apply Murfitts’ proprietary pyrolysis technology at commercial scale, extracting reusable raw materials from tyres. The rCB will serve as a sustainable alternative in tyre manufacturing and other industrial applications, while TPO will be used in material production and alternative fuels, displacing virgin petroleum feedstocks.
Beyond material recovery, the process generates steam that will directly supply Michelin’s tyre-curing operations, replacing natural gas and further reducing fossil fuel reliance. Murfitts, which already recycles 20 million tyres yearly for applications like sports surfaces and road asphalt, continues to pioneer circular economy solutions – ensuring tyre-derived materials re-enter production cycles, closing the loop on waste. This collaboration marks a major step toward greener tyre manufacturing and resource-efficient industrial practices.
Mark Murfitt, Founder, Murfitts Industries, said, “We believe this plant could be a breakthrough in the life cycle of a tyre. It moves tyre recycling on from recovering energy and material for other uses to being able to feed it directly back into factories for new tyre production. Our core ethos at Murfitts has always been that end-of-life tyres are a valuable resource and we need to do all we can to maximise the use of the energy and materials within them. We have been developing our pyrolysis process for a number of years and our results now show we can produce material from end-of-life tyres which can perform better than the virgin equivalent for some applications. This plant will be a win-win for the tyre industry, the local and national economy and the environment.”
Christina Peloquin, Site Director, Michelin UK, said, “This is a really exciting project which reduces our environmental impact at the same time as helping us stay competitive by lowering our energy costs. The team has worked exceptionally hard on this project, and we’re looking forward to welcoming Murfitts to our Stoke-on-Trent site.”
Maria Röttger, CEO and President, Michelin Europe North, said, “At Michelin, we see every challenge as a chance to lead positive change – and end-of-life tyres are no exception. As shapers, innovators and pioneers of sustainable mobility, Michelin is committed to transforming the way tyres are handled at every stage of their life cycle. Through our deep expertise and forward-thinking approach, we are co-building a robust recycling ecosystem that redefines what has previously been possible. This project with Murfitts Industries is a powerful reflection of Michelin’s enduring commitment to sustainability and responsible leadership in the tyre and rubber industry.”
Evonik to Boost Asia Supply Chain with Shanghai Production Expansion
- By TT News
- June 30, 2025
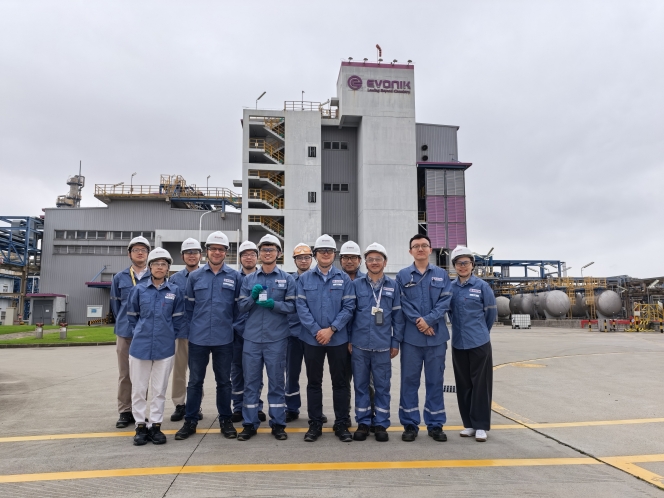
Evonik Industries will localise production of a key tyre additive in Shanghai, marking a strategic shift to enhance supply security across Asia amid growing regional demand.
The Essen-based company announced plans to establish the final production step of its POLYVEST ST-E 60 product at its Shanghai facility, with operations expected to commence by the third quarter of 2025. The expansion will significantly increase the global production capacity of silane-functionalised polybutadienes.
The move represents Evonik’s latest effort to strengthen supply chains and reduce dependency on European manufacturing for Asian markets. POLYVEST serves as a reactive plasticiser in tyre formulations and is also used in rubber compounds, adhesives, tyres, coatings, and sealants.
“This strategic investment will enhance our production capabilities and ensure that our customers in Asia benefit from improved supply security and shorter lead times,” said Dr Anna Maria Ickert, Head of Evonik Coating & Adhesive Resins. “In today’s environment, fostering independent supply chains and bringing our products closer to our customers is essential, enabling us to respond more effectively to their needs.”
The Shanghai expansion comes as global chemical companies reassess manufacturing footprints following supply chain disruptions experienced during the pandemic and ongoing geopolitical tensions. China remains a crucial market for speciality chemicals, particularly in the automotive and construction sectors.
Evonik’s decision reflects broader industry trends towards regionalisation of production, with companies seeking to reduce logistics costs whilst improving responsiveness to local market demands. The tyre industry, a key end-market for POLYVEST, has experienced robust growth in Asia driven by expanding automotive production.
Dr Jürgen Herwig, Head of Evonik’s polybutadienes and speciality acrylics business, emphasised the expansion’s strategic importance. “This expansion aligns with our long-term strategy to strengthen our global footprint while maintaining a strong focus on sustainability and operational excellence,” he said. “The new capacity will enable Evonik’s customers to achieve their business goals while participating in the region’s growth.”
POLYVEST products utilise rubber-based chemistry to ensure compatibility with tyre tread compounds, thereby addressing performance requirements in an increasingly demanding automotive market. The localisation strategy aims to reduce lead times whilst maintaining product quality standards.
Comments (0)
ADD COMMENT