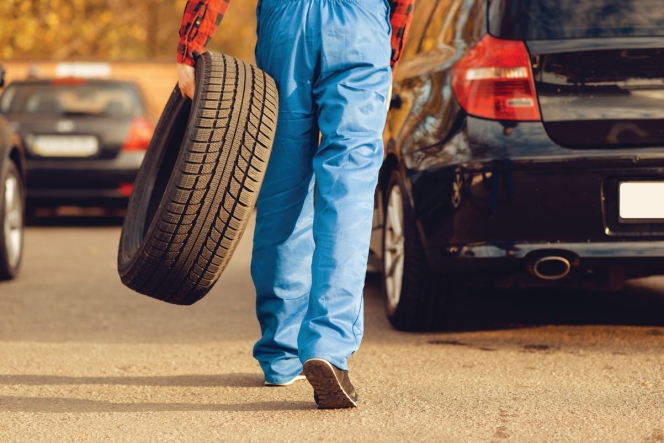
Telling it as it is (Part 2)
In the second part of a two-part series that highlights the importance of claim analysis and the role that this activity plays in the tyre sales continuum, the writer will be tackling and reliving issues to bring to the fore hurdles that are sometimes faced in the African tyre Industry. To the rescue and emerging technology trends in this field, there are thankfully speedy resolutions of the sticky claims processes. Noteworthy however is that even though we may not be close to European counterparts owing to various factors such as technical expertise and supporting institutions, African tyre end-users are increasingly becoming aware of their rights in demanding higher safety standards and better quality products. This article does not deal with the forensic analysis of tyre damages and must not be construed as an attack on any brand of tyres.
Parts per million
If you are somewhat familiar with Six Sigma, you would have heard of terms such as Defects per Unit ( DPU), Defects per Opportunity (DPO)and Defects per Million Opportunities (DPMO). Another important term to learn if you want to understand the concept of quality in the Six Sigma approach is Parts per Million Defectives (PPM).
It refers to the expected number of parts out of one million that you can expect to be defective.
The marketing environment in the motor engineering industry considers PPM as one of the most critical indicators of evaluating their processes and products. Mainly a dimensionless value, PPM is mostly the customer’s value from the supplier. Often misunderstanding arises incorrectly interpreting and using the PPM indicator concerning the customer/Supplier. The biggest problem comes when the customer expects a zero PPM, and the process can only give a PPM of CpK > / = 1.33. In the automotive industry, a PPM of CpK to be> / = 1.67 is acceptable and that too only in the short term horizon.
However small they may be, it is essential to analyse production process failures to carry out the appropriate improvement. Using proven processes such as the FMECA, engineers can focus on the critical sources of the problems and recommend countermeasures for process improvement.
Comments (0)
ADD COMMENT