THE ANSWER: COLLECTIVE FARMING
- By Dr. Siju T
- October 19, 2020
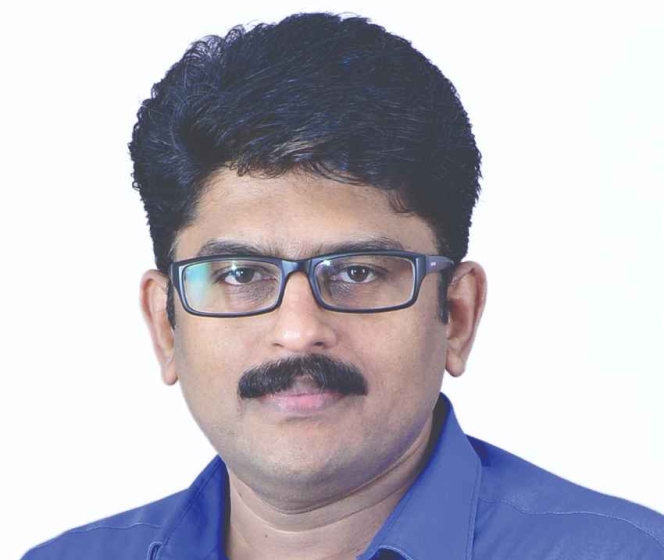
The state of Kerala in southern India still accounts for over 70% of the tappable area and 75% of the national rubber production in India. Given the agro-climatic advantage, quality of human resources cultivating rubber and productivity of rubber, Kerala is expected to retain its prime position in Natural Rubber production in the near future. Though the area under rubber cultivation is increasing in the non- traditional regions, which has got cost advantages over the traditional region, it has inherent climatic disadvantages. A cost-benefit analysis by RRII revealed higher BCR (Benefit-Cost Ratio) for Kerala than in the non-traditional regions due to its higher productivity which offsets the higher cost in the state to some extent. So, maintaining the production sector in Kerala in good health is key to ensuring sufficient domestic production of rubber in the coming decades as envisaged in the National Rubber Policy (NRP) of India.
The NRP envisages sourcing 70% of India’s requirements of natural rubber through domestic production. This also gains importance as India has once again started thinking in the direction of self-sufficiency through its Atma Nirbhar Bharat initiative and the current domestic production of Natural Rubber accounts for just over 50% of the national requirement.
But the days of the smallholding sector of Kerala, which has scripted the success of rubber production in India from the 1980s onwards, seems to be over and running out of steam. The sector is in deep crisis as it is confronted with issues like uneconomic size of holdings, low price of natural rubber and scarcity of tappers. This paper analyses the persisting issue of scarcity of rubber tappers in the sector.
Widening demand-supply gap
The first census of rubber tappers conducted by Rubber Board in 2013 enumerated 77,207 tappers in the smallholdings sector in Kerala. The estimated tappers requirement to tap the existing tappable area of 4,56,000 ha in Kerala in the smallholdings sector under different systems of tapping is presented in Table 1.

The census revealed that 13.7 per cent (10,577) tappers were under S/2 d1, 81.2 per cent (62,692) were under S/2 d2, 4.7 per cent (3629) under S/2 d3 and 0.4% (309) under various other low frequency tapping (LFT) systems in the smallholdings sector. By assuming a stand of 400 trees per tapping block, these tappers could tap only 1,49,011 ha regularly. This shows there exists huge demand-supply gap of tappers in the sector, resulting in large number of holdings either left untapped or tapped irregularly.
Inherent structural bottlenecks
In the general agricultural sector of Kerala, helpers of masons in the rural construction sector are considered to be the most immediate group with whom agricultural labourers identify or that these segments of rural labour markets interact during short-term fluctuations in the supply and demand. Similarly, supply of tappers at a given point of time is determined to a great extent by the wage income of tappers and the wage rates prevailing in the sectors closely interacted by the tappers in the smallholdings sector. Lower wage income of tappers in relation to wage of agricultural labour and semi-skilled workers was reported as the main reason for aversion of younger generation to tapping job. Trends in the wage rate of tappers in the smallholdings sector of Kerala are presented in Table 2.

Based on the structural breaks observed in the wage rate of rubber tappers since 1980, the entire period was sub-divided into five. During the entire time period, except for the period 2014 to 17, the wage rate of tappers has been increasing in real terms. The highest growth rate in nominal and real wages was observed during 2005 to 2013. A plateau in the growth of nominal wage rate was observed after 2013 and hence the real wage rate showed a decline (Fig 1).

Though wage rate of tappers has been showing growth in nominal and real terms till 2013, the sector has been facing severe scarcity of tappers. This shows that increasing wage rate has not succeeded in attracting sufficient tappers into the sector. Hence, wage share, which is a measure of distribution of income between the capital and labour, was computed to know the distribution of income between the farmers and tappers in the sector. Trends in wage share of rubber tappers in nominal and real terms are presented in Table 3.

The wage share of tappers has increased in the last one decade both in nominal and real terms. Though wage rate of tappers has declined in real terms in the last few years under analysis (Fig 1), wage share has been increasing in the smallholdings sector. Increasing wage share in the sector indicated better distribution of income among the capital and labour.
Nevertheless, the wage rate of tappers, both in nominal and real terms, has been increasing (except for the past a few years) and the sector exhibited an increasing wage share in real terms, the sector failed to attract sufficient tappers, leading to severe scarcity. This warrants for deeper analysis to understand the issue. Hence, a comparison of estimated wage incomes of rubber tappers with agricultural labourers and helpers of masons in the construction sector was done and presented in Table 4.

The estimated annual wage income of rubber tappers in the smallholdings sector of Kerala was found to be 44 per cent and 59 per cent less than their counterparts in the general agriculture and construction sectors respectively. This makes the sector less attractive for the potential new entrants, which is ultimately reflected in tappers supply. Due to division and fragmentation of rubber holdings, the average size of holdings has come down and number of trees available for tapping was only 286 trees per tapping day under single grower dependence system and 75 per cent of tappers in the sector were engaged in the single grower dependence system.
In piece rate-based wage payment system, number of trees tapped per day and number of tapping days per year determines the annual wage income of tappers. Thus, in the present scenario, the smallholdings are incapable of giving more tapping task to the tappers to enhance their wage income. Hence, prevalence of single grower dependence, small size of holdings, lesser number of trees available for tapping per tapping day and the piece rate-based wage payment are the bottlenecks in enhancing wage income of tappers. But, in their effort to retain experienced tappers in the milieu of tappers scarcity, the farmers were forced to follow the labour intensive high frequency tapping systems with more tapping days, though it has implications on net farm income.
Even though the tapping wage rate and wage share has been increasing in real terms, the tappers are expected to demand a hike in the wage rate as the wage income earned by them is substantially lower than their counterparts in other rural employment sectors. In the present scenario, to make wage income of tappers on par with that of agricultural labourers and helpers in the construction sector, a hike of 79 per cent and 143 per cent respectively is required in tapping wage rate (Table 5).

But, an increase of this magnitude in the wage rate is not feasible as further hike in the wage rate would seriously affect sustainability of rubber cultivation as with the present cost of cultivation and price of rubber, the farm income is declining in real terms (Fig. 2) and wage share is increasing (Table 3).

Limited options
Since labour is becoming costlier and farm income has been declining in real terms due to uncertain prices, the options available with smallholdings are either to shift to other profitable crops or adopt cost saving technologies including mechanization as tapping accounts for more than 80 per cent of the labour requirement in mature rubber plantations. Generally, mechanisation is done as a labour saving process that occurs due to the increasing scarcity of labour most often reflected in a rising wage rate. But, since the scope for mechanisation in rubber tapping is limited and adoption of cost saving low frequency tapping (LFT) is constrained by the small size of holdings, farmers may either prefer to keep their plantations untapped or shift to other profitable crops. At present, as per Rubber Board data, around 30 per cent of the mature plantations are left untapped in the smallholdings. This will have serious implications on the rubber smallholdings sector as majority of the farmers are small and marginal with average size of holdings of less than 0.5 ha. A study conducted by the Centre for Development Studies, Thiruvananthapuram, found that the net operating income from an acre of rubber cultivation is only Rs. 16,732 in Kottayam and Rs. 19,681 in Thiruvananthapuram, which is not adequate to induce the rubber growers to continue with rubber cultivation. It was also observed that the recorded net income of those with holding size below 2 ha and depending only on rubber cultivation for their livelihood will be below the poverty line.
Thus, declining profitability is expected to dissuade small growers in Kerala from rubber cultivation and encourage them to explore alternatives. This will have far reaching consequences in the sector as the share of part time farmers are already high and a recent survey by the Economics Division, RRII revealed that for 69 per cent of farmers in Central Kerala, income from rubber accounted for less than 50 per cent of the total household income.
Collapse of the smallholder’s rubber sector in Kerala will have serious impact on natural rubber production in India as the state contributes nearly 78 per cent of total natural rubber produced in the country and the smallholdings sector accounts for nearly 90 per cent of area and production in Kerala.
Collectivism to circumvent the structural bottlenecks
Earlier studies have suggested methods like crop sharing and production incentives with annual compensatory allowances as alternatives to overcome the hurdles inflicted by the piece rate-based wage payment system and low tapping task in enhancing wage income of tappers to attract more tappers into the sector. But, large scale adoptions of these propositions were not reported in Kerala. Crop sharing is not sustainable in the long run as the return to capital is marginal and hence would deter large scale adoption by the small and marginal farmers. Production incentives to match the wage income of tappers to that of labourers in the general agricultural sector and helpers in the construction sector (Table 4 and 5) would render rubber cultivation uneconomical due to high cost of production in the smallholdings, which has long lost its economies of scale.
Prevalence of single grower dependence, small size of holdings and lesser number of trees available for tapping per tapping day being the critical bottlenecks in enhancing wage income of tappers and attract new tappers into the sector, any new system adopted should be capable of negotiating these bottlenecks efficiently to ensure tappers flow into the sector. Division and fragmentation of holdings aggravates these bottlenecks and render rubber cultivation uneconomical. Thus, as a measure to overcome these bottlenecks, collectivism/co-operative farming is suggested as an alternative. Collectivism would help to circumvent these structural bottlenecks of the smallholdings viz., small size of holdings, lesser number of trees available for tapping and prevalence of single grower dependence of tappers, as in collective farming the factors of production are pooled and the farm is managed as a single unit on co-operative basis. Hence under collectivism tapping task and wage income of tappers could be enhanced considerably. Willing farmers in the smallholdings sector can be bought under different farmer’s co-operatives and the farm can be managed as a single unit by professional managers under the supervision of the elected members.

Collective management of small rubber holdings under co-operative/collective farming would facilitate large scale adoption of cost saving technologies like LFT, as the holding size barrier for its adoption could be overcome by collectivism. Since the farm management decisions are implemented uniformly across the units managed under collectivism, it will have the advantage of economies of scale. Though LFT is recommended as a cost saving strategy in mature plantations to make rubber cultivation profitable, its large-scale adoption is constrained by the small size of holdings in the smallholdings sector.
The first census of rubber tappers by Rubber Board in 2013 recorded its adoption as below 5 per cent in Kerala. By following the LFT (S/2 d7) under collective farming, the tapping task and employment of tappers could be enhanced further (Table 6) and the wage income of tappers could be equated with their counterparts in the rural labour market. Table 6 reveals that with the present tapping wage rate itself, the wage income of tappers could be equated with the income earned by their counterparts in the rural economy under collectivism. In addition to higher wage income, the tappers attached to farmer’s co-operatives would have better access to welfare schemes extended for the tappers by the Rubber Board as the first tappers census observed poor percolation of the welfare schemes among the tappers, since the tappers in the smallholdings were unorganized.

The proposed collective farming is different from the activities performed by the Rubber Producers Societies (RPS). The present day RPSs are basically involved in technology dissemination, provide different services like subsidized input distribution, collective processing and marketing of NR. A few RPSs and Rubber Board promoted trading companies are organizing tappers under tappers banks to tap holdings which are either untapped or abandoned due to absentee farmers, non-availability of tappers and declining profitability due to price crash. Though tappers attached to the tappers bank under the present system get higher remuneration than their counterparts in the smallholdings (Table 7), this will not ameliorate tappers scarcity and encourage large scale adoption of LFT in the sector, as the bottlenecks discussed earlier remains.
In the proposed collective farming, farmer’s co-operatives are expected to play a major and direct role in rubber production by pooling the factors of production (plantations). The authority to make farm decisions would be vested with the co-operatives rather than individual farmers and the profit shall be shared among the members.
Conclusion
Though wage rate and wage share has been increasing in real terms in the small holdings sector, the wage income of tappers were substantially lower than the wage income of labourers in the general agricultural sector and helpers in the construction sector with whom tappers in the smallholdings relate in the rural labour market. Due to presence of structural bottlenecks as such as smaller size of holdings, lesser number of tress available for tapping, piece rate wage payment system and prevalence of single grower dependence, the sector was incapacitated to augment wage income of the tappers to equate it with that of labourers in other rural sectors. To attract more tappers into the sector by increasing the wage income of tappers by circumventing the structural bottlenecks, collective farming under farmer’s co-operatives following the principles of collectivism is proposed. Collective management of plantations will not only help the tappers to get regular employment, sufficient tapping task and remunerative wage income, it would also have the added advantage of bring down the cost of production of NR and increasing profitability of NR cultivation as it would also facilitate large scale adoption of labour and cost saving technologies for rubber production.
Zeon Board Approves Higher Budget For Cyclo Olefin Polymer Facility
- By TT News
- September 03, 2025
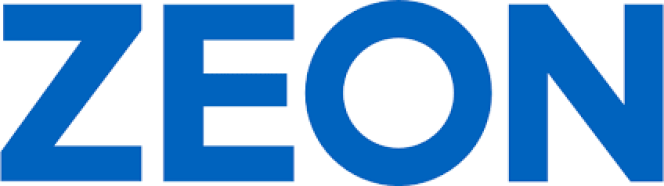
Following a resolution by its Board of Directors on 29 August 2025, Zeon Corporation has formally revised the total investment for its upcoming cyclo olefin polymer (COP) production plant. The new total investment is now projected to be approximately JPY 78.0 billion (approximately USD 525.70 million), a significant increase from the initial estimate of approximately YEN 70.0 billion (approximately USD 471.77 million) announced in June 2024.
This upward revision is attributed to anticipated increases across key construction areas, including rising costs for labour, raw materials and equipment. The updated financial framework incorporates both confirmed and projected cost escalations to ensure accurate budgeting. Zeon Corporation intends to fund the entire investment through a combination of internally generated capital and loans from financial institutions.
The new facility remains on schedule for completion in the first half of fiscal year 2028. Due to this timeline, the substantial investment is not expected to materially affect the company's consolidated financial results for the fiscal year ending 31 March 2026. The project is a central pillar of the company’s medium-term business strategy, identified as a major future growth driver.
The decision to proceed with the plant underscores the strong market outlook for Zeon’s cyclo olefin polymers. These advanced materials are prized for their superior optical clarity, extremely low water absorption and high purity. While already established in applications like optical films and lenses, demand is growing rapidly from the medical and semiconductor industries. By expanding its production capacity, Zeon aims to capitalise on this robust and expanding demand, thereby strengthening its market position and enhancing its corporate value over the medium to long term.
Kraton And International Paper Finalise Agreements For Operational Continuity In Savannah
- By TT News
- September 02, 2025
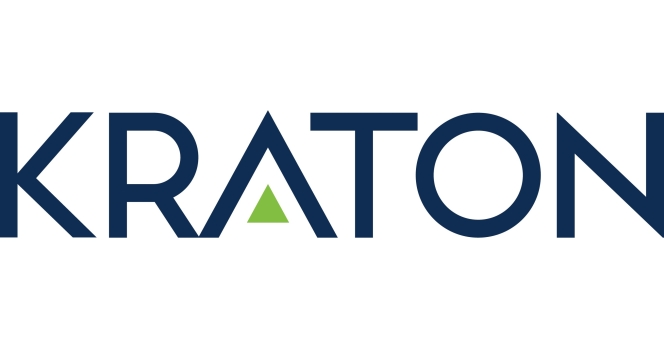
In a move to ensure operational continuity, Kraton Corporation has finalised service agreements with International Paper for its Savannah, Georgia facility. As a leading global producer of specialty polymers and biobased pine chemical products, Kraton will continue to receive essential site services from International Paper, a leader in sustainable packaging. This arrangement guarantees an uninterrupted production and supply of critical pine chemicals for the global market.
The agreements solidify both companies' shared commitment to reinforcing the pine chemicals value chain and providing reliable service to their customers. For Kraton, this partnership provides stability as it makes strategic infrastructure investments at the Savannah plant. These planned upgrades are designed to facilitate the site's long-term independent operations, supporting Kraton’s broader focus on business resilience and future growth. This initiative reinforces Kraton's position as a global leader in delivering high-performance, sustainable, bio-based solutions.
Minco van Breevoort, President, Kraton Pine Chemicals, said, “Securing this agreement reinforces our unwavering commitment to our customers and the pine chemicals industry. It’s business as usual. Our teams are fully aligned to ensure reliable operations, and this agreement provides continuity of supply to pine chemical markets as we invest in our long-term capabilities.”
Chris Roeder, Vice President and General Manager, Pine Chemicals and Low Carbon Solutions, International Paper, said, “We are pleased to renew and extend our partnership with Kraton. This arrangement confirms our long-standing relationship with Kraton and our commitment to being a reliable, long-term partner to Kraton and participant in the pine chemicals markets for years to come.”
Retreading’s Stubborn Struggle
- By Gaurav Nandi
- August 29, 2025
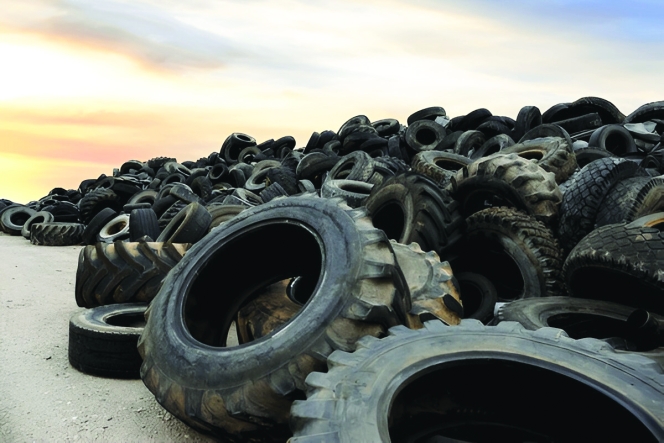
Despite decades of presence and proven sustainability benefits, the global truck tyre retreading industry remains mired in perception problems and systemic inertia. As raw material costs rise and environmental pressures mount, retreading should be a no-brainer. Yet, it continues to be sidelined by outdated mindsets, customer ignorance and a lack of cohesive industry messaging. Tirecore CEO Garry Drisdelle, in a candid interview with Tyre Trends, paints a picture of a sector at risk – not because it lacks value, but because it has failed to communicate it. The stakes, he warns, are too high for complacency.
Despite decades of existence, the retreading industry still wrestles with fundamental challenges across the world – not least the stubborn perception among customers and stakeholders about the true value of retreaded truck tyres. Tirecore Chief Executive Officer Garry Drisdelle pulls no punches in diagnosing the sector’s issues and outlining the uphill battle ahead.
Speaking to Tyre Trends, he said, “Tirecore is primarily a supplier of quality truck tyre casings to the retread industry. But while retreading should logically form the cornerstone of sustainable tyre use, the industry remains far from mainstream acceptance.”
“Educating the customers really as to how much upcycling, how much can we save – it’s beyond the pennies or pounds you save on the initial purchase,” Drisdelle said. Yet, frustratingly, many customers remain fixated on upfront costs instead of the total lifecycle value of a tyre.
This fixation, he implies, represents a systemic failure within the industry. “The industry has to do a better job towards educating the consumers, which primarily are fleet owners, beyond the initial purchase,” said Drisdelle. The inability to shift consumer mindset threatens to leave retreading as a niche rather than a necessity.
Tirecore positions itself primarily as a global supplier of high-quality truck tyre casings to the retread industry, operating across markets that include the United States, Canada and India. Rather than manufacturing or retreading tyres directly, the company serves as a critical node in the circular economy of commercial tyres, ensuring that valuable casings find extended life through retreading.
“We are in the business of preserving 85 percent of the tyre components existing material’s value saving valuable resources,” said Drisdelle.
The company’s operational model is rooted in the principle of upcycling over replacement, focusing on longevity and material reuse rather than disposability. While Tirecore’s precise logistical affiliations remain unspecified, its strategic direction is clearly aimed at aligning with sustainability mandates and evolving global market demands.
DISPOSABLE TREATMENT
Drisdelle highlights a critical contradiction. Tyres are one of the most safety-critical components on the road, yet they are taken for granted at a staggering scale. “Picture a truck is rolling down the highway at 100km/h pulling 20,000 kilogrammes of freight, riding on just 6-8-10 rolling rubber contact points. Tyres are one of the most critical transportation components, yet we treat them like disposable goods. How taken for granted is that product?”
Even as raw material prices surge and truck tyre costs climb, the entrenched perception treats tyres as disposable consumables. “We need to reframe the conversation – a tyre should be seen as an asset and not a consumable,” Drisdelle emphasises.
This disconnect reveals deeper issues prevalent within the industry. Retreading has not been effectively communicated as a financial and environmental beneficial in the long tome. Moreover, legislative inconsistency and lack of incentives for the industry as a whole is a deterrent that needs to be addressed immediately.
Drisdelle insists that retreading should be the environmental rallying point for the sector. “We have 85 percent of the material in the original product that is quite capable of being reprocessed and upcycled many times,” he said.
He contrasts upcycling favourably with recycling, which he argues requires more energy and effort than the original production process, especially in plastics and other materials: “By the time you just recycle something, the energy to recycle it is more than the process.”
Yet these arguments come with an implicit critique that the industry has failed to effectively translate this environmental rationale into a compelling value proposition for customers and regulators alike.
LEGISLATIVE MOMENTUM
Drisdelle points to potential legislation requiring truck tyres to be recyclable or retreadable as a possible catalyst for change. “Picture if legislation comes out that you’re not allowed to sell truck tyres unless they’re recyclable from their ingredients unless they’re retreadable,” he noted.
However, he quickly tempers this with realism stating, “We can never get to zero. That’s a cool little marketing thing but it’s an impossibility in the world of physics and science.”
This admission highlights the gap between aspirational sustainability goals and practical realities, a gap that leaves retreading vulnerable to accusations of greenwashing or insufficient progress.
ADAPT OR STAGNATE
Looking to the future, Drisdelle’s plan is pragmatic but cautious. “Our future plans are to keep up with the market demand, to evolve as the market evolves. Pivot and prosper,” he said.
Such a measured approach reflects the uncertainty and fragmentation within the industry. The promise of retreading remains strong, but without decisive action on education, regulation and innovation, the sector risks losing ground to cheaper, new tyres or alternative technologies.
The recurring theme throughout Drisdelle’s commentary is education, or rather, the lack of it. “The education of the fleet owners is primary to everything. The education of the industry to build a better tyre is somewhat secondary,” he stated.
This stark admission speaks volumes. Despite retreading’s environmental and economic advantages, a fundamental communication failure continues to hobble the industry.
Drisdelle points out the irony stating, “Without a widespread cultural shift in perception, retreading will struggle to move beyond a cost-saving niche for price-sensitive fleets to a mainstream standard.”
Drisdelle’s blunt assessment of the retread industry reveals a sector caught between its potential and its persistent shortcomings. Tirecore’s role as a global supplier to retreaders is clear but the wider challenge remains.
Without significant progress on education and regulatory backing, the retread industry risks remaining on the margins, overshadowed by the convenience of new tyres and the pressures of market inertia.
Retreading’s promise is substantial. But, as Drisdelle’s comments underscore, fulfilling that promise demands a candid reckoning with the industry’s educational failures and a relentless push for change or face stagnation in a rapidly evolving tyre market. n
India’s Tyre Recycling Industry Enters New Era With Gujarat’s Green Light To Continuous Pyrolysis
- By Gaurav Nandi
- August 28, 2025
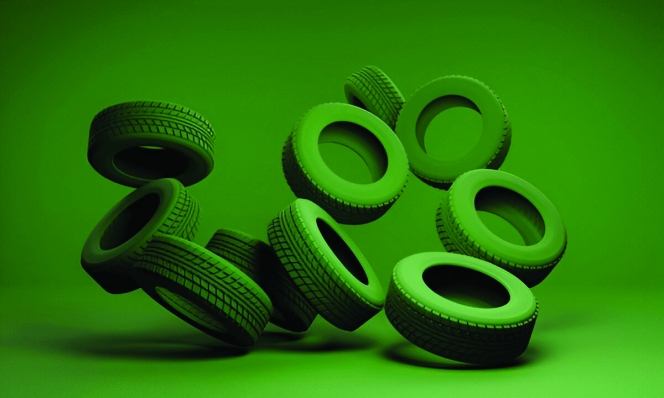
India’s tyre recycling sector, long plagued by fragmented operations and lax compliance, is undergoing a critical overhaul. With Gujarat’s recent approval for continuous pyrolysis plants, the industry is moving decisively towards cleaner, scalable and regulation-driven solutions. This shift signals more than a technological upgrade and it’s a rebuke of outdated batch systems and a call for formalisation, traceability and environmental accountability. As global demand for sustainable materials rises, India’s pivot positions it as a potential leader in circular economy practices. In conversation with TRRAI President Chetan Joshi, we explore how this development could redefine the future of tyre waste management at home and abroad.
India’s tyre recycling sector is on the cusp of a transformational shift with the Gujarat Pollution Control Board (GPCB) approving the establishment of continuous pyrolysis plants in the state. The move marks a significant departure from traditional batch-based tyre processing systems, promising to boost efficiency, environmental compliance and resource recovery at an industrial scale.
“This shift is nothing short of revolutionary,” said President of the Tyre and Rubber Recyclers Association of India (TRRAI) Chetan Joshi. “We’re moving from outdated, fragmented batch operations to streamlined, automated continuous pyrolysis systems. This is going to uplift the entire industry, from cleaner emissions to higher resource recovery, better traceability and serious investor interest. It sets a new national standard and will accelerate formalisation, industrial-scale operations and a far more sustainable approach across India.”
The approval has been met with optimism by recyclers and environmental advocates alike as it signifies a structural change in how end-of-life tyres will be handled in India, which is home to more than 1.8 million tonnes of tyre waste annually.
The Gujarat model mandates stringent adherence to environmental standards, particularly concerning air quality and emissions. Continuous pyrolysis plants approved under the new framework are required to incorporate top-tier pollution control mechanisms.
“We see compliance not as an obligation but as a core design principle. Our plants are being built with advanced air pollution control devices (APCDs), real-time emissions monitoring and automation that ensures consistent performance. We’re aligning with both GPCB and CPCB regulations through pro-active design, third-party audits and integrating global best practices. It’s not just about meeting today’s standards but staying ahead of tomorrow’s,” said Joshi.
The approach reflects a broader shift in the recycling sector, where regulatory compliance is no longer viewed as a hurdle but as a strategic advantage and market differentiator.
Industrial scale
Under the new directive, each continuous pyrolysis facility must operate at a minimum capacity of 60 tonnes per day (TPD). This scale reflects the government’s push to industrialise tyre recycling and eliminate inefficient, informal practices.
“Scaling to 60 TPD is a serious industrial commitment and it means heavy investment in automation, utilities, safety systems and logistics. But it’s also the only way forward. India generates over 1.8 million tonnes of end-of-life tyres annually. This scale allows us to handle the problem responsibly while creating traceable and economically viable recycling ecosystems,” Joshi said.
With India’s growing automotive base, the urgency to develop sustainable, high-capacity recycling infrastructure has never been higher.
One of the key advantages of continuous pyrolysis lies in its outputs that include valuable petrochemical byproducts like pyrolysis oil, sustainable fuels and recovered carbon black (rCB). These materials are increasingly in demand across a range of industries, from rubber manufacturing to renewable energy.
“These by-products are entering a new phase of global relevance. Recovered carbon black is being adopted in rubber, plastics and even pigments. Pyro oil, when upgraded, is a viable alternative fuel. We’re actively engaging with global buyers and certifiers to standardise and integrate these outputs into international supply chains. The world is ready for sustainable alternatives and it’s up to us to deliver with consistency and quality,” averred Joshi.
India’s entry into this global supply chain positions it not just as a recycler of waste but as a producer of sustainable industrial materials.
Circular economy
TRRAI views this milestone as more than an environmental success. It’s a step towards realising India’s vision of a circular economy, where tyre waste is fully reintegrated into the production cycle.
“We aim to be more than recyclers. We want to be circular economy enablers. That means building systems where tyre waste is traceable from collection to output, where value is recovered and re-injected into the economy. We’re developing collection infrastructure, digital traceability and offtake agreements with industries globally. This is not just about waste; it’s about resource optimisation and environmental stewardship,” Joshi explained.
Such a shift could significantly reduce the country’s carbon footprint while fostering job creation and industrial growth.
Despite the enthusiasm, industry leaders acknowledge that challenges remain, particularly in terms of adoption among legacy operators and infrastructure gaps.
“The biggest challenge is inertia as many operators are still working in the unorganised sector with outdated setups. Then there’s infrastructure as a hurdle as tyre collection networks are underdeveloped in many parts of India. To overcome this, we’re advocating policy changes, investing in reverse logistics and training the workforce. Regulatory clarity and enforcement will be key and we’re working closely with industry associations and government bodies to drive this,” said Joshi.
Stakeholders believe that education, investment and enforcement will be pivotal to ensuring widespread transition to continuous pyrolysis systems.
Global trends
Globally, countries like those in Europe and North America have already adopted advanced tyre recycling technologies. But Joshi believes India has a unique opportunity to leapfrog older systems and build world-class facilities from scratch.
“Europe and North America have a head start, especially in policy frameworks and end-use applications. But India’s opportunity lies in scale and adaptability. We can leapfrog legacy systems and build efficient, tech-driven plants from the ground up. If we get the ecosystem right – collection, compliance and capital – we can set new benchmarks, not just catch up. India could become a global hub for tyre recycling technology,” he said.
The industry’s fast pace of development combined with India’s manufacturing and engineering capabilities could make the country a case study in sustainable industrial transformation.
Innovations in emission reduction
In line with global best practices, TRRAI and its partners are integrating innovations to ensure safety and minimal environmental impact.
“We’re integrating closed-loop systems, AI-driven control logic and multi-stage gas cleaning technology. Real-time emissions data will be available both internally and to regulators. Safety protocols are built into every operational layer, from material feeding to shutdown procedures. We’ve also prioritised workforce training and regular third-party safety audits. The goal is to operate with zero compromise on health or the environment,” Joshi explained.
Such innovations are crucial not only to maintaining regulatory compliance but also to building public and investor confidence.
The entry of advanced technologies is expected to catalyse foreign investment and technical collaboration.
“Our approach is partnership-driven. We’re already working with European and Australian technology providers and are in discussions with institutional investors. We see India as a platform for co-creation, where global IP meets local scale and agility. Through industry associations like TRRAI, we’re building collaborative networks to ensure knowledge sharing, investment facilitation and joint innovation,” Joshi noted.
This strategy could help India become a global innovation hub for recycling technologies applicable across other emerging markets.
The vision
Looking to the long term, the industry’s goals extend far beyond domestic waste management. TRRAI envisions exporting its model to developing nations facing similar challenges.
“Our vision is bold but simple. It is to create a fully circular, scalable and replicable tyre recycling ecosystem. India should not only solve its own tyre waste crisis but become a global model for how emerging markets can tackle resource recovery. We see this model being exported to Southeast Asia, Africa and Latin America. With continuous pyrolysis, India can move from reactive recycling to proactive resource management on a global stage,” Joshi concluded.
As Gujarat lights the way with its approval of continuous pyrolysis plants, India’s tyre recycling sector is poised to become a beacon of innovation and sustainability – one that could shape the future of global recycling practices. n
Comments (0)
ADD COMMENT